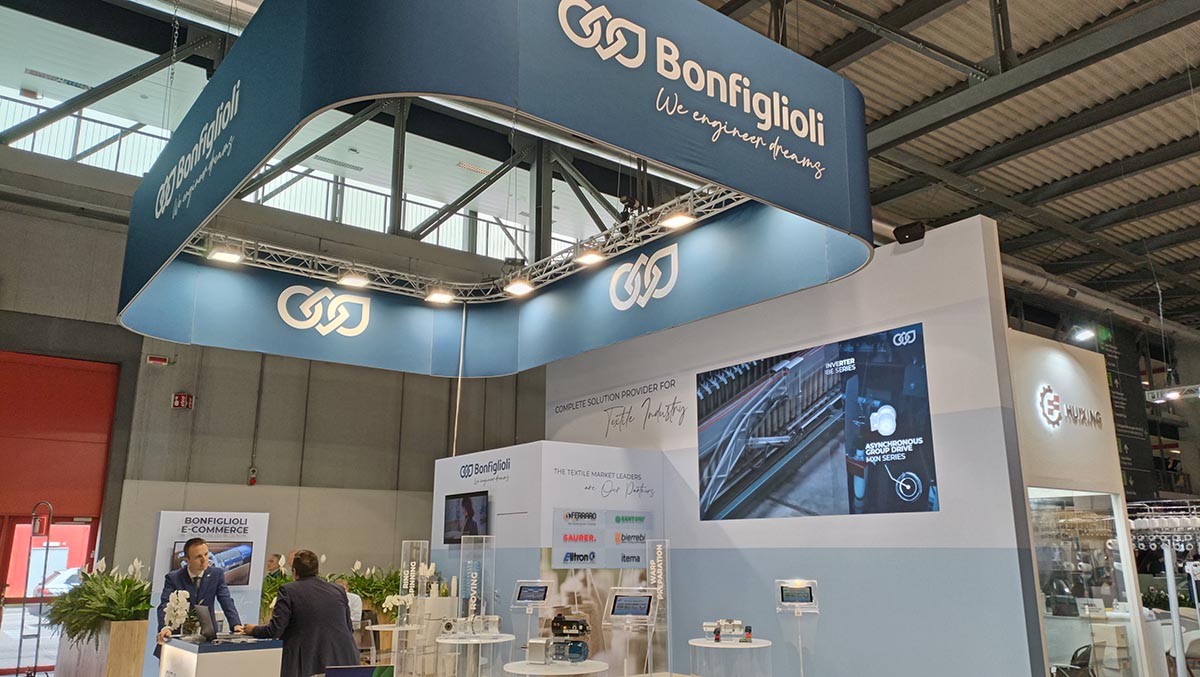
The textile industry is a sector in which fabrics and yarns are manufactured and processed using different techniques and materials. The sub-sectors include spinning, weaving, knitting, dyeing, printing, and finishing. Each sector requires specific equipment and techniques to produce the desired fabric or textile product. A wide range of natural and synthetic fibers such as cotton, wool, silk, polyester, and nylon are used to produce fabrics and yarns, which in turn are processed into products. The industry is constantly evolving its technologies and techniques to improve efficiency, sustainability, and product quality. Advanced manufacturing processes are also used to develop environmentally friendly materials and production methods in compliance with local and international regulations. This constant evolution fosters a culture of continuous improvement by investing in research and development and by adopting technologies and processes to emerging trends.
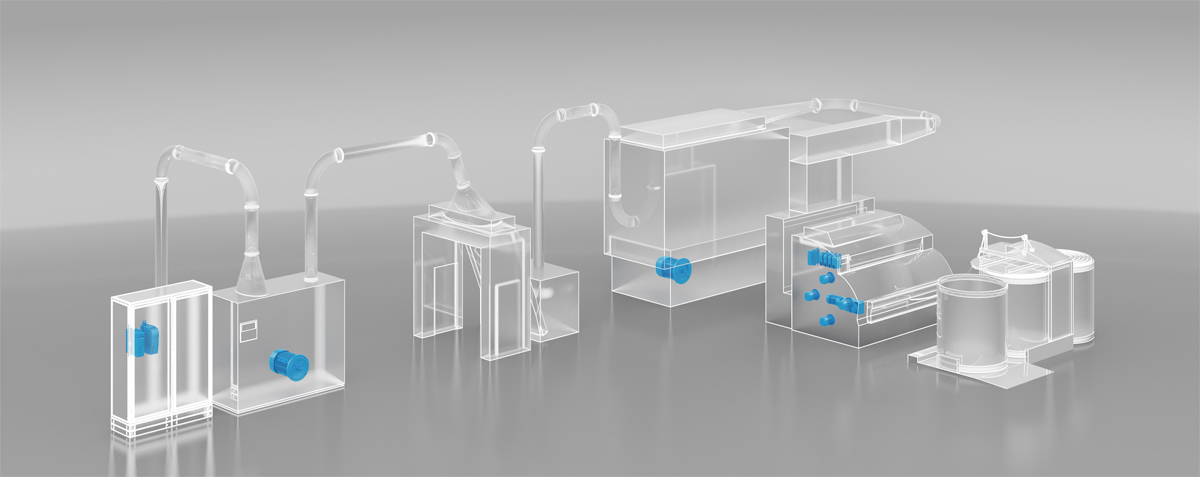
“Energy efficiency, cost saving and sustainability have been the roots of the design for Textile Drive Solutions,” says Christofer König – Sales Manager at Bonfiglioli, and adds: “Thanks to our wide experience in controlling machines through electronic drives, we have improved the functionality and monitoring of controllers, motors and gearboxes to ensure long-term and stable operations of textile machines. As a result, we are able to offer complete product packages (inverter + gearbox + motor) of highly dynamic drive systems for increasing production efficiency.”
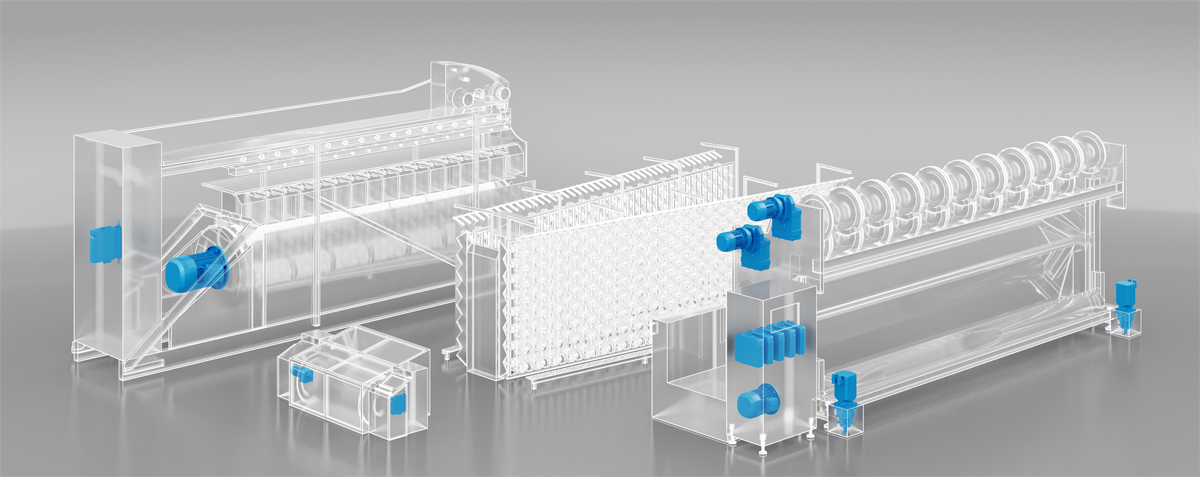
Thanks to the extensive know-how and long-term collaboration with key customers, Bonfiglioli engineering specialists work side-by-side with customers to develop tailored and forward-thinking integrated solutions for the textile industry, covering the entire motion drive train, including the Industry 4.0 approach. Their drive system portfolio has the perfect features to respond to the typical demanding environment of the textile sector, characterized by fiber-polluted air, high ambient temperatures and occasional mains failure management. Bonfiglioli faces the harsh environments of the textile sector in different ways:
- As for DC-Bus & Mains failure, Bonfiglioli takes care that the machine can react during a power failure with a managed ramp down and in this way material damages (i.e. yarn breaks) can be prevented
- Concerning products used in high temperature environments, the company offers the cold plate and feedthrough solutions, so that the heat losses are outside the cabinet, allowing space savings. Device variants without fans and without electrolyte capacitors improve the longevity of the inverters and their robustness to work in harsh environments (high temperature).
- They offer alternative cooling concepts for frequency and servo inverter and coated printed circuit boards
All this, coupled with a comprehensive range of professional services, allows Bonfiglioli to satisfy the customers’ demands with solutions aimed at minimising the total cost of ownership of plants by significantly reducing maintenance activities, energy consumption and downtime.
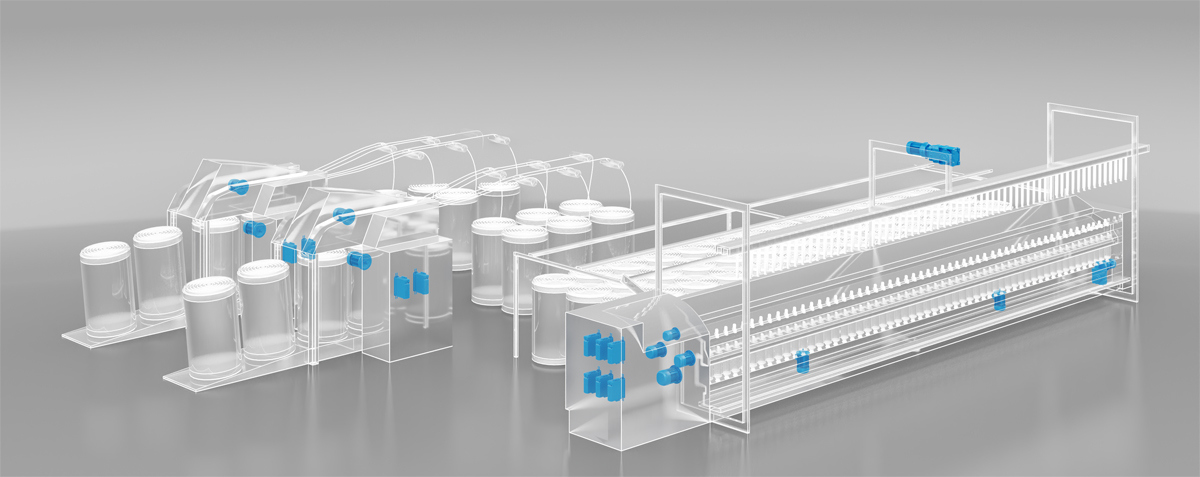
For a responsible resource usage, energy efficiency is a major task today for every production machine to reduce the ecological impact and saving operation costs at the same time. The following approaches help to increase the energy efficiency of the drives and therefore for the whole machine:
- Smart energy usage
- Converting energy with high efficiency
- Using kinetic energy during braking
- Reducing energy consumption through energy saving functions in the frequency inverter