BY Mr. Pawan Gupta, Co-Founder and CEO of Fashinza
Sustainability is a major challenge within the textile and apparel industry, and while we have observed growing awareness over the recent years, there is still a long way to go. The textile and apparel industry has multiple impacts on the environment – there is huge dependency on water and energy resources, harmful chemicals are involved in the manufacturing process, and then there’s the issue of proper disposal. Fast fashion has further added to the concerns with millions of tons of clothes being discarded every year.
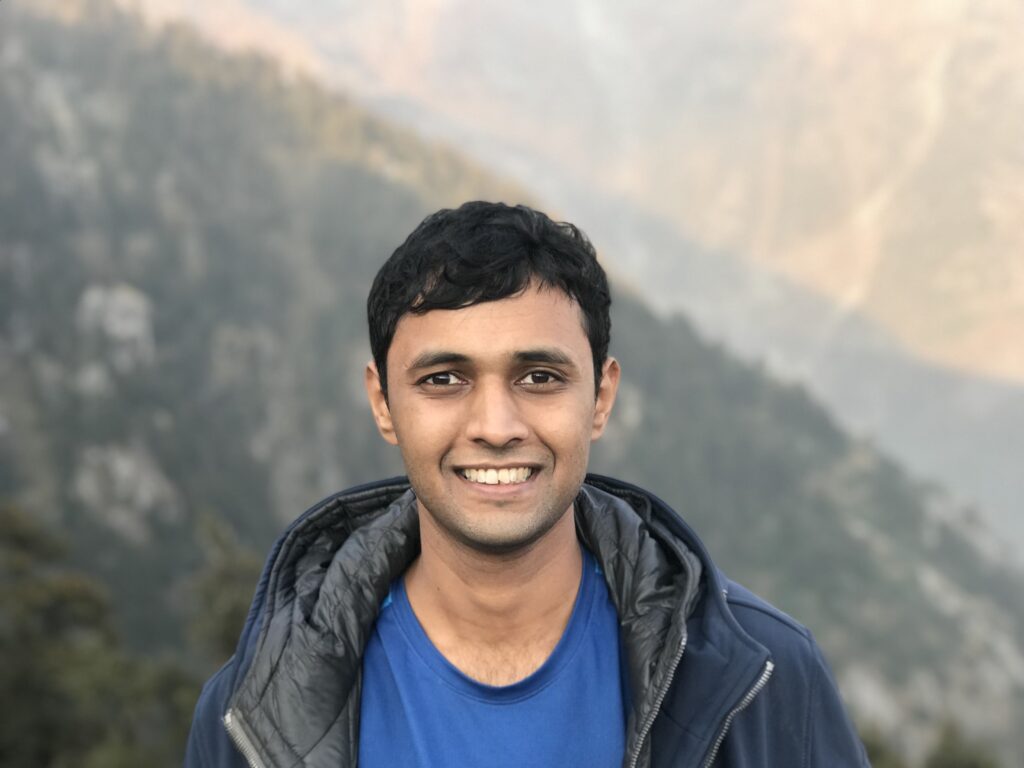
The textile and apparel supply chain, as we know it today, is not optimized to prioritize sustainability. There are multiple barriers embedded within the supply chain which makes it difficult for the industry to adopt more environment friendly practices, the first and foremost among them being financial and technological barriers. The cost of raw materials is a massive burden for apparel manufacturers, especially in countries where they have to import the raw materials. The high costs combined with problems like inflation make it difficult for them to afford sustainable practices. Here, lack of adequate infrastructure and skill also add to problems. In developing countries, most SMEs do not have access to advanced technology that aids sustainable production. For instance, to convert plastic bottles to fibre for clothes, you’d need certain infrastructures to be in place. To reduce the use of non-renewable energy, you’d have to switch to solar or wind power, which again demands the infrastructure. The same holds true when it comes to processing toxic chemicals. Add to this the lack of skilled labor needed to adopt new technologies to local conditions, and you can see why most SMEs shy away from adopting sustainable practices. The challenges are multifaceted, and while some problems receive a degree of attention – such as proper treatment of chemicals – others demand greater financial investment, which SMEs cannot afford.
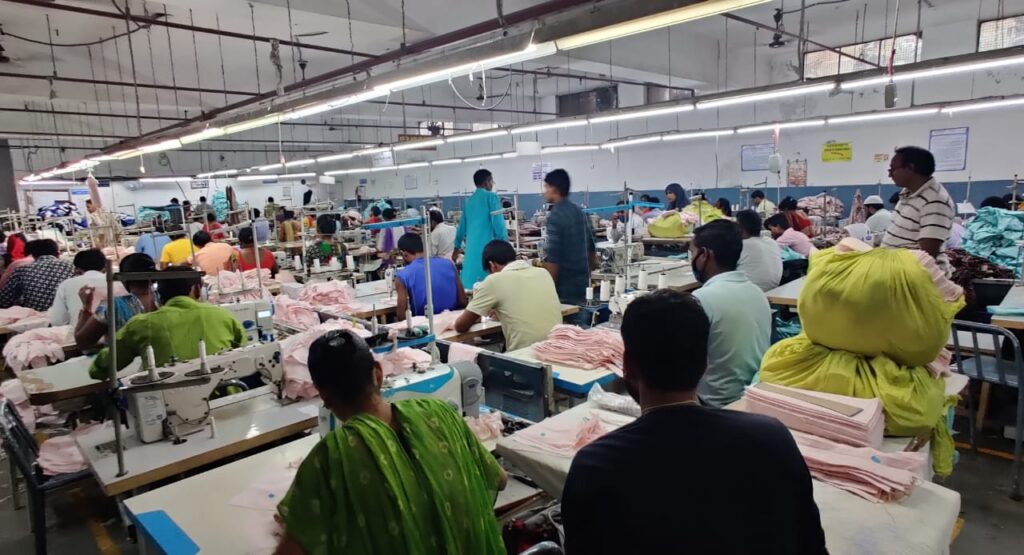
While cost and infrastructure are tangible problems, other challenges involve the values of the management and lack of demand in the market. While in the West, eco-consciousness has assumed a center stage, in developing countries like India and Bangladesh the awareness is still limited. When the suppliers and manufacturers in question are themselves invested in the idea of sustainable production, it becomes easier to deal with the tangible challenges by shifting focus to long-term benefits. The lack of awareness, on the other hand, becomes a barrier in itself. At the same time, the demand for sustainable products is limited at the moment in our domestic markets, and understandably the demand influences the supply.
A conversation about sustainability challenges within the textile and apparel industry remains incomplete unless we mention the opaque nature of the supply chain. The supply chain here is extremely complicated with multiple steps involved in the production and distribution, from sourcing raw materials to placing a finished product in the store. Multiple stakeholders are involved in the process and it is not an easy task to trace the practices undertaken at every stage of the supply chain. At present, most brands have no clue where their raw materials come from or how they are treated. But this does not mean it’s impossible to introduce transparency within the supply chain. Brands that do care about end-to-end sustainability rely on transaction certificates and sustainability certifications (like GOTS, BCI, and others) for the same. The sourcing process in such a case might involve additional costs but it is definitely worth it because the environmental cost goes down.
How to build resilience in the Textile Supply Chain?
The textile industry is an old and traditional industry, and to be more resilient, it needs to become more agile. The textile supply chain needs to adapt to the changing circumstances, and one way to do that would be to embrace digitization like most industries have. When we started our journey with Fashinza, our biggest priority was to bring agility within the supply chain by reducing lead times, introducing digitization, and improving inventory management. The apparel industry is going through multiple changes at the same time. The environment has become super dynamic, WFH has changed the demand patterns, online business has become massive, there is a lot of uncertainty in the supply chain, and a lot of cash is stuck in inventory. What the industry has realised during the pandemic is that it was stuck in its age old ways of working for far too long.
Going forward, the supply chain will have to be super agile and adopt technology to react to any change in the demand. They need to be driven by data and not just intuition. Agility has to be built into the industry from the ground up.