
The revolving flat card is called the heart of the spinning mill. This illustrates the immense significance of carding to the end result and the quality of the yarn. All carding products developed and made by Groz-Beckert feature the details which also show advantages beyond quality parameters.
Spinners have high expectations towards card clothing manufacturers. They expect yarn quality to be maintained at a constant level or even improved while achieving high production output. Furthermore, they ask for low production costs and minimum expenses for maintenance. These requirements are met to the full extent with the C20-40-95-CMF cylinder wire from Groz-Beckert. This card clothing is established in the market, and it has proven itself many times, achieving satisfying results for a wide range of customers.
Ingenious tooth geometry
The C20-40-95-CMF cylinder wire is characterized in particular by its special tooth shape and shows its potential when processing cotton for combed and carded ring yarns. Due to its special and patented tooth geometry, the card clothing doesn’t need to be re-sharpened subsequently. There’s no need for complex grinding processes and conclusively no need for production stops. For revolving flat cards with an automatic grinding system, no activation of the system is required – and also no replacement of the grinding stone. This results in minimized maintenance costs for the card clothing and savings due to reduced downtime of the revolving flat card.
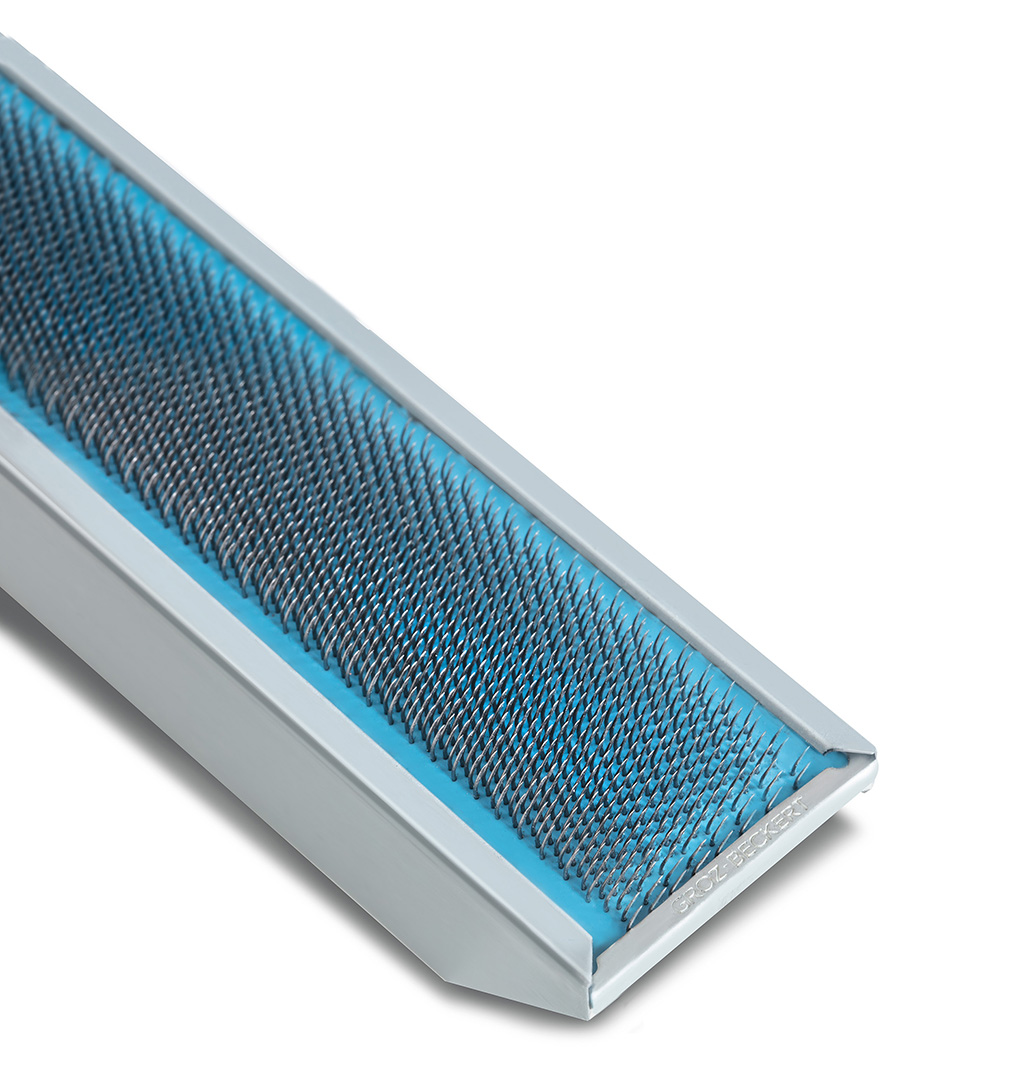
The card clothing is currently available in Duratech and Ultra steel grades. Duratech is a micro-alloyed steel grade and Ultra offers the longest lifetime. Ultra is recommended for all modern revolving flat cards and highest production outputs.
Proven in practice and comparisons
Customer trials with the CMF design showed improved yarn quality compared to a standard Groz-Beckert cylinder wire over time. As a result, fewer thick and thin places as well as neps in the yarn (IPI) were detected. In addition, a higher Neps Removal Efficiency (NRE) was achieved on the revolving flat card in the course of the trials, which naturally had a positive effect on the yarn quality.
The special tooth geometry of the C20-40-95-CMF shows a further advantage: Customer trials proved a significantly increased service life. The positive results stand out in comparison to standard cylinder card clothing. This makes it particularly well suited for quality-oriented cotton spinning mills producing high quality yarns.
Tests in spinning mills underlined that the C20-40-95-CMF is the perfect solution to achieve high production rates. The unique design matches customer requirements for high output applications, as spinners state. Groz-Beckert plans to develop further CMF cylinder wires with the advantages of the existing C20-40-95-CMF that will become the ideal future fit for many more applications.
Consistent – Revolving top TV56
The TV56 revolving top features a special tooth geometry, too. Most popular with the TV56 revolving top is its unique setting pattern and 560 points per square inch. This setting pattern offers various benefits in production. Spinners observe more consistence in carding performance while tapping the potential of higher production rates.
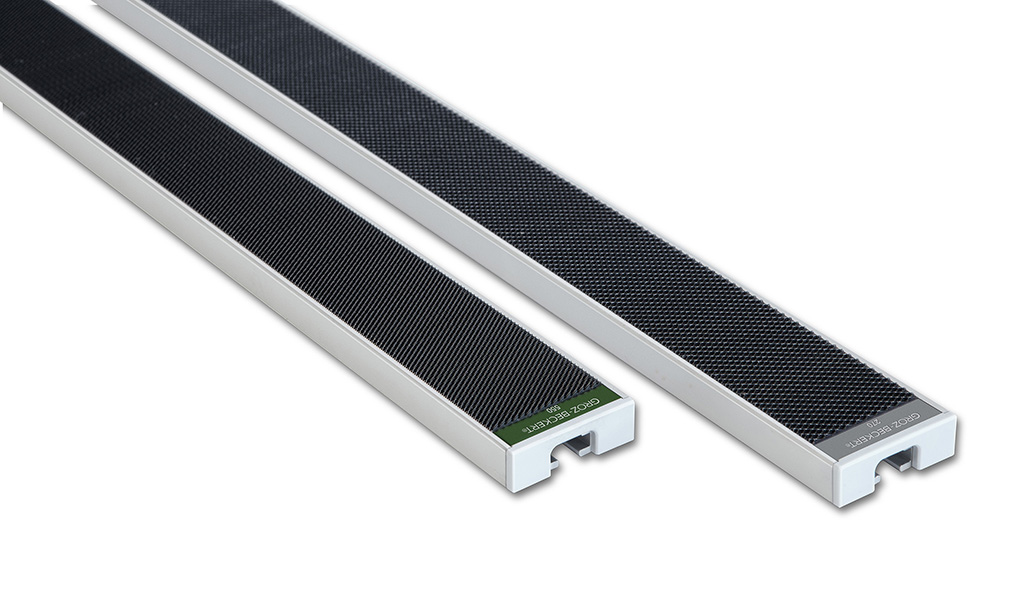
When it comes to performance, the unique setting pattern and 560 points per square inch make it easy to stay clean and guarantee consistent picking up of short fibers and trash. The revolving top TV56 offers high resistance, which increases the already mentioned production output potential of the revolving flat card. The TV56 is particularly well suited for cotton applications and blends with yarn counts between Ne20 and Ne45.
Tough – The new fixed flat series
The third tooth geometry innovation is the stationary flat series. Clever engineered geometry and distribution of the teeth result in improved carding action and increased fiber control. The tooth distribution enables controlled opening of the fiber tufts in the revolving flat card. The controlled fiber opening relieves the stress on the revolving flat and has a positive effect on its service life.
The new stationary flat series also has a more resistant surface, which provides protection from damage caused by incorrect handling. The design of the stationary flat decreases the risk of scratches – and there is also reduced risk of loading. The Groz-Beckert stationary flats are available in a wide range of densities: from 88 and 160 to 270, 330 and 440 up to 550 and 660 PPSI.
Teeth for success
Cylinder wires, revolving tops and stationary flats are the elements for main carding action and fiber separation in the carding zones. In addition to the actual carding, tops are designed to collect trash, dust and short fibers. Tooth geometry plays a major role in all actions of the carding process – and offers benefits beyond quality. Groz-Beckert carding products are developed in the way – or let’s say in the shapes – that spinners relax because well carded is half spun.