In this interview, Jay Shah, Managing Director, Lakshmi Enterprises, exudes confidence about the growth and prospects of his company while elaborating on how modern technology has helped it keep ahead of the curve
VMS Fabrics Private Ltd. is a part of the well-known Lakshmi Enterprises, Ahmedabad, one of India’s leading trading houses for the supply of quality grey and dyed fabrics, which has been serving the Indian textile industry for more than four decades. The company had been sourcing fabrics since 1985 from 75 of the best corporate vendors in India. To meet their bulk requirement of quality fabrics, they ventured into manufacturing under a new company, VMS Fabrics (P) Ltd., which was set up in 2016. VMS Fabrics recently installed the new, cutting-edge KARL MAYER Prosize® sizing machines to complement their Toyota high-speed air jet weaving machines.
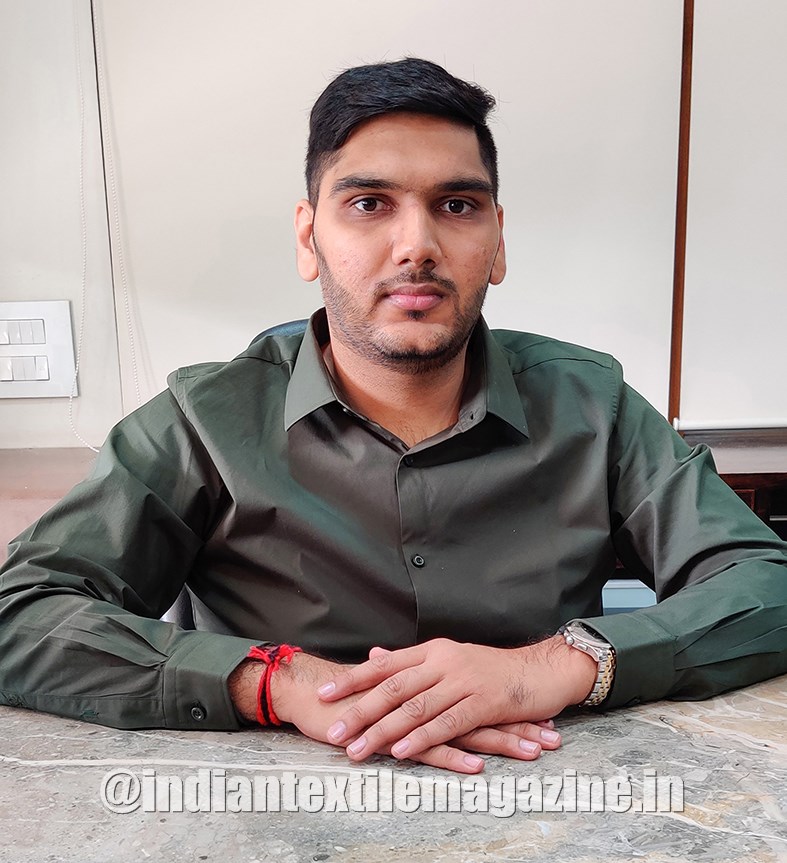
Excerpts from the interview:
What are the key strengths of VMS Fabrics that will ensure the success of this new venture?
We have been sourcing the bulk of the fabrics we require only from leading manufacturers of India. The new manufacturing setup will definitely boost our confidence and prosperity in the coming years as we will be able to serve both domestic and export-related needs through our in-house produced quality fabrics. We use only the best quality yarns from the Indian spinners as per our buyer protocol, which gives us the best output in terms of fabric quality and loom efficiency. We have the best technical team in marketing and manufacturing, which helps us meet the common goals of the group.
We also have the best machines and working culture which assures the best output from each of the resources we have. All these strengths help us produce the best quality and competitive products, which ensures buyer satisfaction. We are committed to provide quality fabrics to our customers. We have repeated orders from our exporters and have well-established clients outside India. We produce 1.5 million metres per month and are targeting 3 million metres by 2022. The growing demand and having our own setup with state-of-the-art machines will surely help us to grow faster in this competitive market.
Ahmedabad has always been a hub for fabrics trading in India. Do you see this continuing?
Yes, surely. There are many modern process houses in Ahmedabad that offer quality fabrics in shirting, dress material, denim, bottom weights, lycra, etc. The requirement of fabrics by the process houses will increase day by day and hence we foresee an overall growth in the weaving sector, as well as other areas in textile.
You have been in the trading business for decades. Could you tell us how the idea of the sizing project came up?
As I mentioned, we have been sourcing the fabrics from almost all the leading weaving mills. Looking at the increasing demand from the process houses, as well as global challenges for fabrics such as rising prices, we thought that having our own manufacturing setup, in addition to our trading business, would not only help us meet our commitments to our customers, irrespective of the market situation, but also make our products more competitive globally. We set up the sizing unit to ensure backward integration and good quality warp beams for our weaving unit.
What made you opt for KARL MAYER’s Prosize® sizing machine?
We had been sourcing grey fabrics from South India and other weaving centres where all our suppliers have installed KARL MAYER Prosize sizing machines. All our suppliers are very happy with the performance of this machine in terms of high productivity, high-quality warp beams, lowest wastage of yarn, and optimum stretch control. With reduced consumption of size chemical and other utilities, the Prosize is cost-effective as well. The warp beams produced on the Prosize run smoothly on our high-speed air jet weaving machines, and achieve the highest weaving efficiency compared to the beams produced with conventional sizing technology. Keeping sustainability and growth in mind, we prefer to go with new technologies and machines. If we want to cater to the global fabric demand, we must have the best machinery that can produce the best quality products at competitive prices to help us tap the international markets in future.
What is the production you are able to achieve with Prosize sizing machine?
We have selected the machine configuration to achieve maximum production speed. With a specified speed of 150 metres per minute for the KARL MAYER Prosize – and looking at the highest production speed achieved at all other installations of this machine – we are hopeful of achieving a production speed of 140 to 150 metres per minute for all warp qualities. We commissioned the Prosize machine along with the KARL MAYER high-speed direct warper in March 2019. With this combination, we are running high-speed weaving machines with the best installed efficiency in weaving units and can produce more than 12-13 tons per day of sized warp. The good quality of warp beams has helped improve the weaving speed. Our target is to produce 450 tons of sized warp per month with this machine.
Could you share your experience of working with A.T.E. as a business partner?
We have known the A.T.E. team for a long time. We have met them at our suppliers’ places from where we source the fabrics and yarns. It was in one such meeting that the A.T.E. team convinced us to set up our own manufacturing unit. A.T.E. helped us not only to decide the right specifications of the warp preparation machines based on a wide range of weaving qualities, but also the layout and the finalisation of the utilities and other important requisites for the project as well. We highly appreciate the timely support provided by A.T.E. and KARL MAYER.