Excerpts from an interview with S Rajendran, Senior Vice President, A.T.E. Enterprises, in which he highlights the company’s foray into new products and technologies and how the textile industry in India will shape up in the coming years
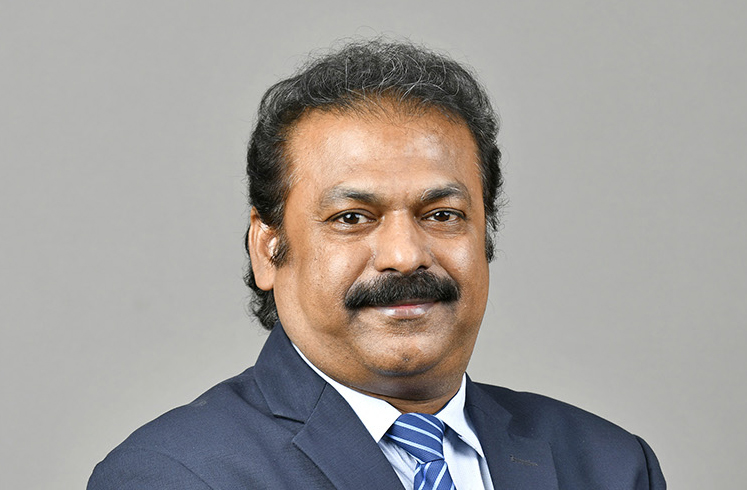
The Indian textile and apparel industry is expected to touch USD 190 billion by 2026. What are the major factors that could drive the market’s growth?
Looking at the bigger picture, on the one hand, there are a lot of expectations about India becoming one of the world’s largest and fastest growing economies in the world. However, on the other hand, India’s exports have contracted as much as 16.7%, which is a bit of a dampener. This is, however, not unexpected, as the global trend seems to be recessionary that is due, in large part, to the war in Ukraine. China’s pandemic-related policy also seems to have had a negative impact on the world’s economies. Apart from this, the global chip shortage and other supply chain issues have slowed down the demand that surged after the pandemic.
Given that background, we are still bullish about the Indian textile market. For one reason, India has a huge population that drives a lot of domestic demand for apparels and other textile products. Leading fashion brands are seeing a big leap in online apparel purchasing, which is turning the conventional wisdom that buyers look for ‘touch and feel’ on its head. Indians are buying casual wear like denim and shoes online – and fashion purchasing is beginning to rival online electronic purchasing. I feel that e-commerce will emerge as a major driver in the fashion industry.
The agile manner in which India stepped up production to answer the shortages of face masks and other PPE items during the peak of the pandemic alerted many to the vast potential of the Indian textile industry. Subsequently, there has been renewed interest in the technical textile, manmade fibre (MMF) and nonwovens sectors. I strongly feel that these sectors, in addition to garments, will be the growth engines for the Indian textile industry. Moreover, the rapidly changing trends in fashion and the willingness to try out new designs and styles is also a contributing factor to the growth of the industry.
You mentioned technical textiles and MMF will provide the required impetus for growth in Indian textiles. What are your thoughts on the policy front?
The government has pushed a number of policies forward that will invigorate the textile industry. For example, the push towards MMF and technical textiles through the PLI scheme is laudable. PLI 2.0 is already on the cards, as are plans for SITP and MITRA parks, which will help boost manufacturing in the textile sector. Up to 100% foreign direct investment (FDI) in the textile sector will increase the comfort level of investors in India and. A number of free trade agreements (FTAs) have been signed, which is another silver lining.
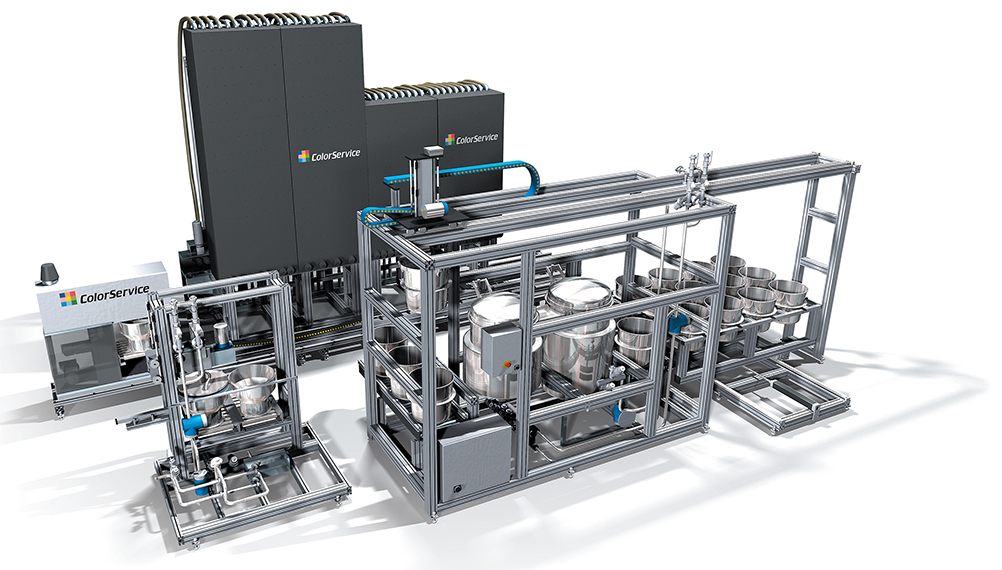
However, for the FTAs to be truly effective, textile exporters must be quick to take advantage of them. Export demand needs to pick up as it is the only way we can achieve an upward growth trajectory for the long term. This is particularly the case in garments and home textiles, where we have lost ground to Vietnam and Bangladesh. However, those countries are facing other issues, while India is seen as a stable democracy – something that foreign investors seek. Policy makers need to find a way to help manufacturers and exporters cut costs and remove roadblocks. At the same time, textile organisations need to work with the government and focus on accelerating the ‘Make in India’ initiative.
What are the major problems that textile processors face? What expectations do they have from machinery manufacturers in this segment? How is A.T.E. strategising to meet these demands?
The pandemic and subsequent lockdown made abundantly clear how labour-intensive industries like textiles needed to automate and reduce operational costs. There are no two ways about it – automation is the key that will unlock value in the textile value chain and take us to the next level. Consider one of the small but vital processes in textile processing – that of dye and chemical preparation. Without automation, there is wastage in chemicals and dyes due to manual transfer or incorrect chemicals being picked. Loss of productivity is an additional issue as the machines are idle while the preparation is done.
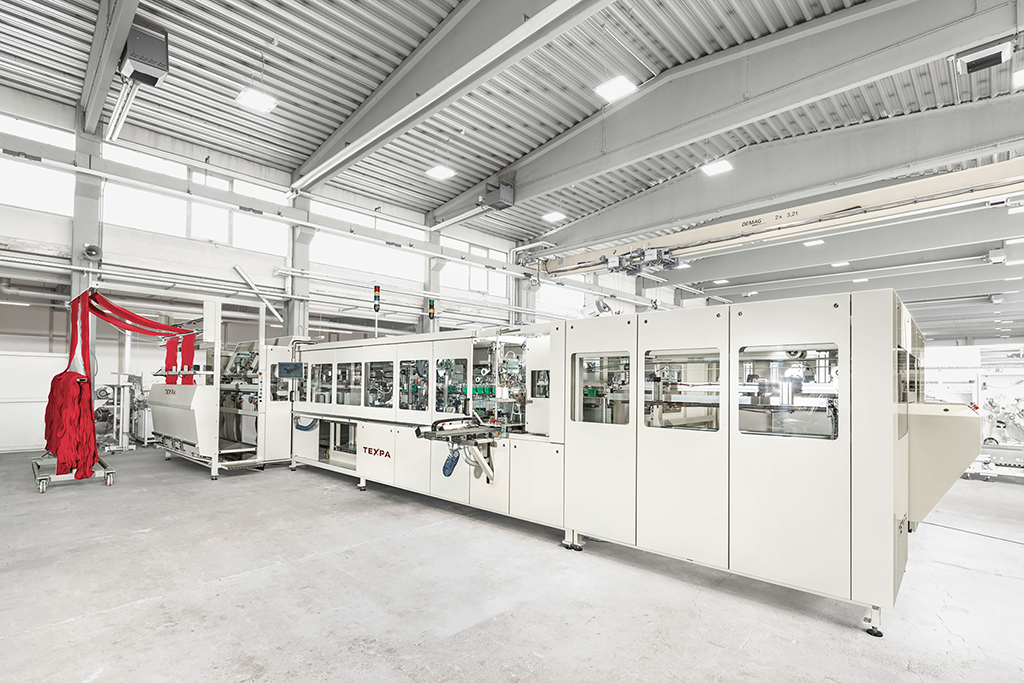
A.T.E. provides Color Service (Italy) automatic dyes and chemical dispensing systems that have helped customers the world over realise considerable improvements in productivity and cost reductions. With automation, operator mistakes are minimised, safety margins that are required to ensure colour pick-up and wastage of chemicals are eliminated, energy is saved and productivity rises. This is just one small example of how automation can result in energy and labour savings. We also provide Texpa (Germany) high productivity automatic cut and sew solutions with precise finishing for home textiles.
A.T.E.’s focus has ever been to support the steady growth of the Indian textile industry. We aim to build collaborations with some of the world’s best textile machinery manufacturers to ensure that Indian textile manufacturers have access to textile technologies on par with the rest of the world. At the same time, our goal is to also develop innovative and sustainable technologies in-house. We also offer substantial saving in services with faster response and issue resolution due to availability of service engineers locally. We offer single point of contact for spares from various manufacturers. Our team of experienced engineers undertake a range of activities from supervision to the final installation and commissioning of the machines supplied by us.
How do you feel A.T.E. is positioned in the Indian textile processing market? What solutions do you offer?
A.T.E. has established itself as a one-stop shop for end-to-end solutions in natural and manmade textile processing. This is due to our long standing tie-ups with leading manufacturers such as Fong’s, Goller, Monforts, Corino, Color Service, Danti Paolo, Zimmer, Mahlo, Osthoff-Senge, and many more. Our machinery is extensively used in leading processing houses around the country for the production of high-quality finished fabric and made-ups. We cover every process from singeing and desizing, scouring and bleaching, mercerising, dyeing, analogue and digital printing, to coating and finishing. We also offer process control systems, automatic dispensing systems for dyes and chemicals and effluent treatment. A.T.E. also covers every fabric type – woven, knit (open width and tubular), terry, denim, and more. Our technologically superior products and solutions have been widely accepted in the industry, which is the biggest reason for our success.
Could you elaborate about A.T.E.’s after-sales service?
Many of our customers who plan to expand or modernise always turn to us for help. Deliverables such as enhanced productivity and end-product quality, savings in raw materials, etc. create lasting impressions in the minds of our customers. This is in large part due to our exemplary after-sales service. We have a dedicated team of around 20 people, based all over the country, who render the best services in machine installation, commissioning, machine relocation, etc. We always endeavour to extend to our customers the best in support – not just in sales, but in service as well.
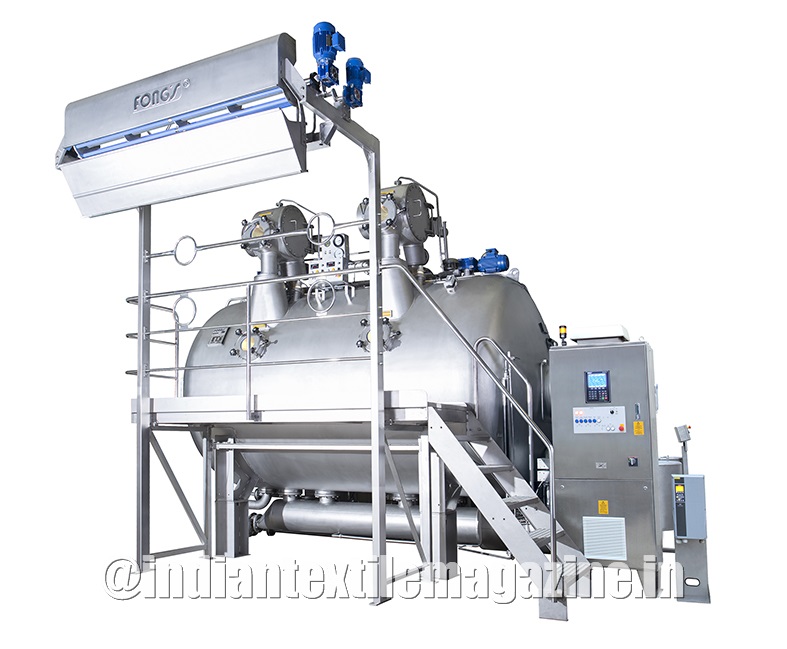
Where do you see this market in the near future? What is the future roadmap for your company?
India is growing in the knit segment and is expected to grow further in the coming years too. Most of the existing knit processors are increasing their production volume and greenfield projects are coming up. Interestingly, the knit segment is switching over from tubular to open width processing. We are very clear about our roadmap: we have a package of machinery for knit processing and one of our principals is in the process of introducing a continuous open width knit dyeing technology which is a breakthrough. We have a package of machinery for technical textiles finishing. Our principals have established their products in Europe and we are planning to bring the latest technology for finishing technical textiles to India. India is looking for a suitable technology for automating the processes. While we have a package solution, we are further looking for new technologies.