By Arun Rao
Water Next Solutions, headquartered in Italy with over 30 years of industry expertise and team experience, is pioneering sustainable and cost-effective wastewater treatment solutions tailored for the textile sector. By emphasizing on biological processes, the company’s innovative systems significantly reduce both the operational costs and environmental footprint of effluent treatment plants (ETPs).
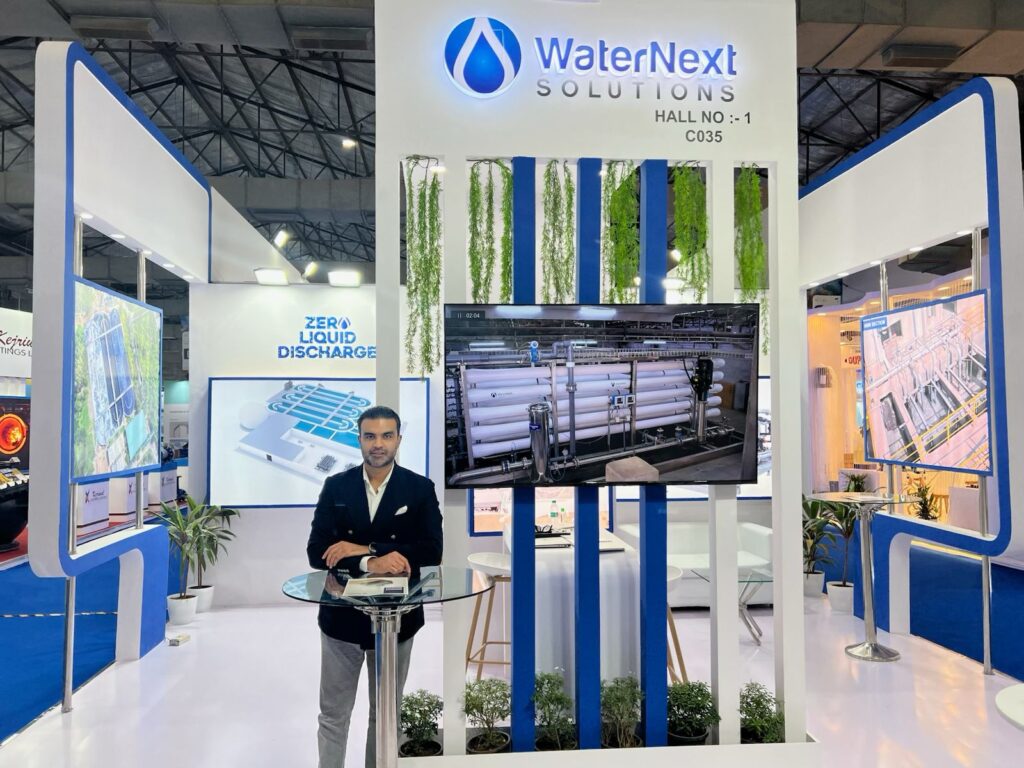
Mr. Pranay Behl, Co-Founder & CEO of Water Next Group, highlights the company’s groundbreaking biological treatment technologies and membrane based solutions, detailing their advantages over traditional chemical-based systems and their transformative impact on the textile industry in an interview with The Textile Magazine.
Revolutionizing Wastewater Treatment with Biological Solutions
Water Next has led the introduction of biological treatment technologies for wastewater management, focusing primarily on ETPs. Unlike conventional chemical treatments that rely on toxic substances, the company harnesses bacteria’s natural capabilities to break down wastewater pollutants.
“In conventional ETPs, effluents first undergo chemical treatment before biological processing. In contrast, our approach is entirely biological, making it more sustainable and significantly reducing operational costs,” Mr. Behl explains.
Key Advantages of Biological Treatment Systems
One of the standout benefits of Water Next’s biological treatment solutions is their remarkable cost efficiency. According to Mr. Behl, their systems can be up to five times cheaper to operate compared to traditional ETPs. “Electricity is our primary operational cost, with all other elements optimized for maximum efficiency,” he notes.
Beyond cost savings, Water Next’s systems are also environmentally friendly. Unlike chemical-based plants that produce hazardous sludge, Water Next’s biological systems generate non-toxic sludge that can be repurposed as organic manure.
Sustainable and Chemical-Free Solutions
Water Next’s innovative biological systems employ beneficial bacteria to consume pollutants in wastewater, eliminating the need for harmful chemicals. “Sustainable practices are becoming essential for the textile industry,” Mr. Behl emphasizes. “Our goal is to eliminate chemical treatment stages in ETPs, providing fully sustainable solutions.”
Cutting-Edge Membrane base Technologies/ Systems for Maximum Efficiency and Recovery
Leveraging membrane bio-reactor (MBR) technology, the backbone of its biological treatment process, Water Next ensures a simple and effective path to achieving Zero Liquid Discharge (ZLD). “Our water recovery process involves just three steps, with high automation levels,” says Mr. Behl. “Unlike conventional plants requiring a minimum of 10-15 operators, our systems are managed by just one skilled operator.”
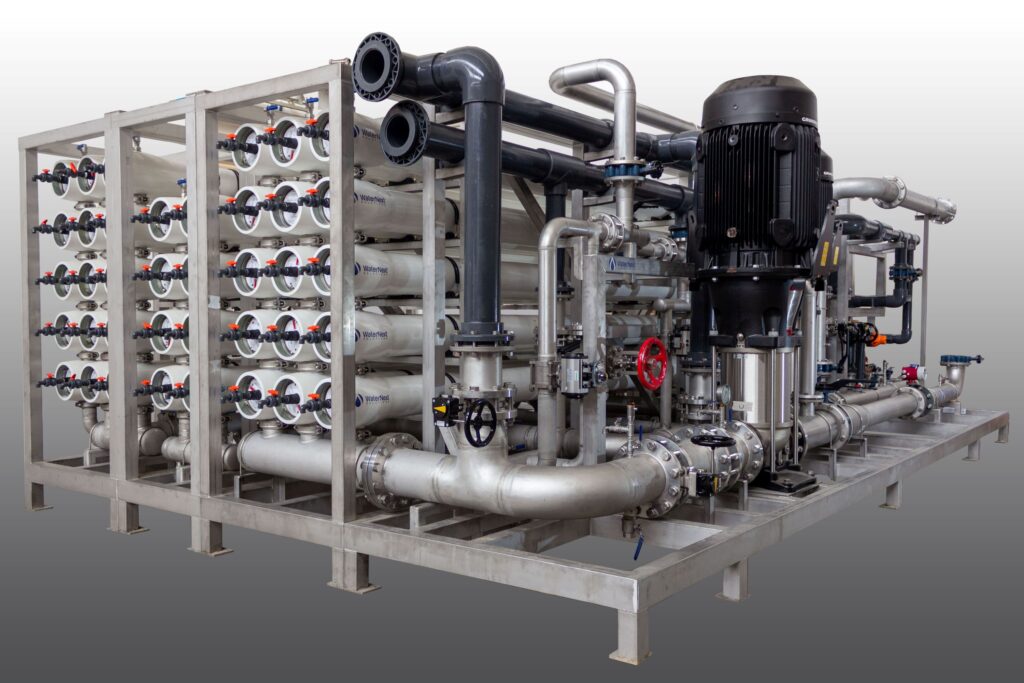
The company’s expertise in biological treatment, membrane filtration, and reverse osmosis enables them to design highly integrated and reliable systems. “Few companies possess in-house expertise in these technologies like we do, enabling highly automated and efficient solutions,” Mr. Behl asserts.
The complete system facilitates up to 95-97% reuse of textile wastewater with low operational costs and continuous 24/7 water feed to dye mills.
Global Reach and Impact
Team Water Next has executed over 500 effluent treatment plants globally, with more than 100 focused on wastewater recovery. Their systems are especially popular within the textile sector, where efficient and sustainable wastewater management is critical.
“In India, we have served leading textile companies and set up green field projects in the recent past,” Mr. Behl notes. Internationally, Water Next has a strong presence through offices in Italy, Mexico, and Colombia, executing projects across Bangladesh, Sri Lanka, China, Indonesia, Colombia, Africa, and more.
Commitment to Innovation and Continuous Improvement
Innovation is central to Water Next’s mission. With R&D teams based in Italy and India, the company consistently enhances its systems’ performance, boosting water recovery and operational efficiency. Initially, reverse osmosis systems achieved 70% water recovery; today, they surpass 95%. “This advancement represents a major leap in water conservation and efficiency,” Mr. Behl remarks.
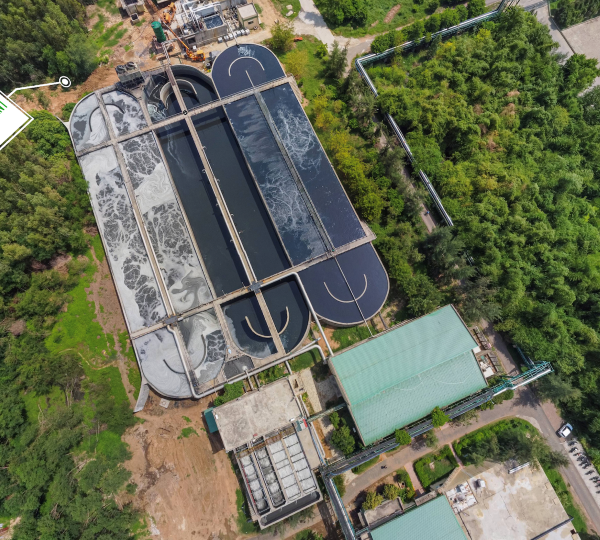
In recent years, the company has developed systems that utilize CO2 from chimney smoke for pH neutralization. The boiler smoke is directed to the effluent treatment plant (ETP), where it helps neutralize the high pH in wastewater. This innovative process offers two key benefits like reducing or eliminating carbon emissions, and also minimizing or eliminating the use of sulphuric acid.
Water Next’s commitment to sustainability extends beyond technology, with many plants installed over a decade ago still operating efficiently with minimal maintenance costs.
Robust After-Sales Support
Dedicated to customer satisfaction, Water Next provides strong after-sales support with a team of engineers who remotely resolve most technical challenges. “Our customers trust us for continuous support,” says Mr. Behl. “We deliver high-quality, automated ETPs that maintain high efficiency while reducing costs and environmental impact.”
Water Next Solutions demonstrates that sustainable, cost-effective wastewater treatment is achievable, transforming effluent management in the textile industry through innovative biological technologies. As demand for sustainability grows, the company is poised to lead with advanced, eco-friendly, and cost-efficient solutions.
“We are dedicated to advancing sustainability in the textile sector by offering solutions that are both environmentally friendly and economically viable and strive for customer delight by ensuring smooth plant operation ,” concludes Mr. Behl.
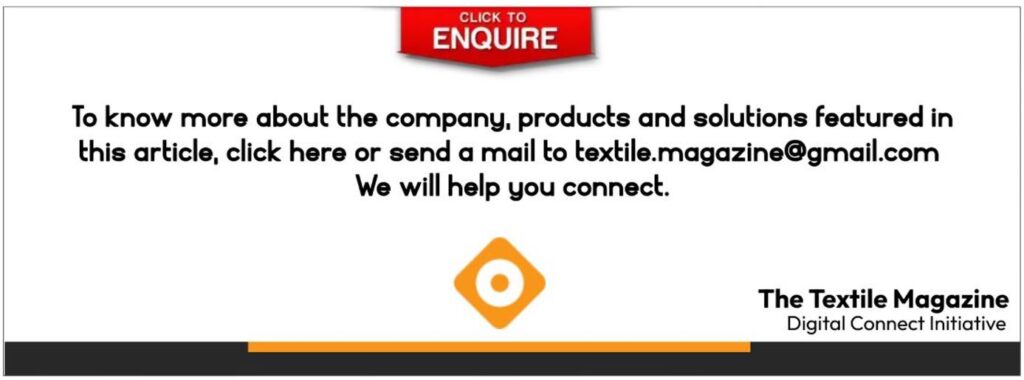