Drawing-in 4.0 – innovation in weaving preparation
The WarpMasterPlus combines all properties offered by the established WarpMaster concept to date: modular design consisting of needle, reed, healds, drop wires and yarn module, low space requirements for the machine and drawn-in harness. This machine offers maximum flexibility with minimal setup requirements and problem-free drawing-in of critical warp yarns, as the drawing-in takes place via a bobbin.
Groz-Beckert is the world’s leading provider of industrial machine needles, precision parts and fine tools as well as systems and services for the production and joining of textile fabrics. The products and services support the fields of knitting, weaving, felting, tufting, carding and sewing. Everything comes together at the headquarters in Albstadt, Germany. The family-owned company, founded in 1852, also operates with agencies, production and distribution subsidiaries in more than 150 countries around the world.
Recently, Groz-Beckert expanded its product portfolio for Weaving preparation with a new drawing-in machine: the WarpMasterPlus.
Developed for the future
The WarpMasterPlus is the latest generation of fully automatic drawing-in machines from Groz-Beckert and was presented for the first time at ITMA 2019 in Barcelona.
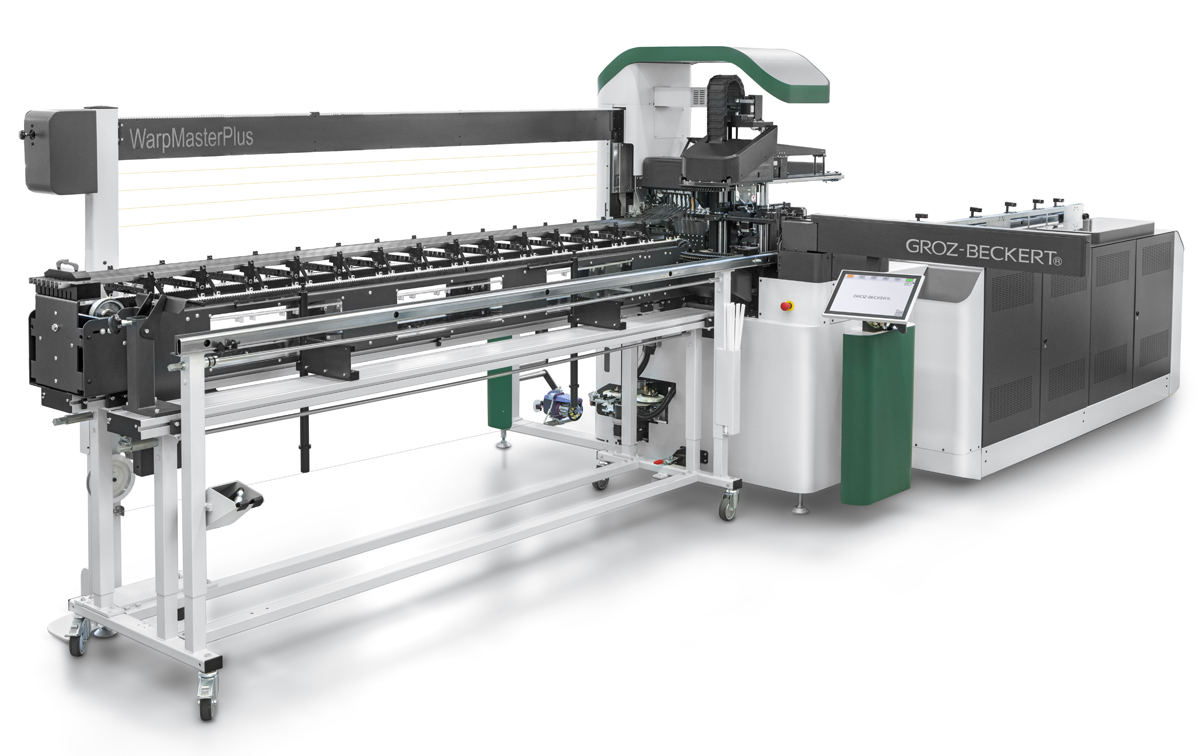
In this machine generation, Groz-Beckert continues to rely on the globally proven drawing-in concept, where the drawing-in takes place via a single yarn package. Nevertheless, WarpMasterPlus is not merely a further development of the WarpMaster: The system has been newly developed from the ground up. The latest technologies were consistently used to bring a machine to the market that is already equipped today for future requirements with regard to increased automation in the course of Industry 4.0.
Maximum flexibility with minimal setup time
Further focal points in the development were maximizing machine efficiency and simultaneously reducing the set-up and dismantling time. For this purpose, the number of cycles has been increased and sophisticated functions such as pre-setting drop wire magazines and CNC axes for adjusting the heald length have been added. Conversion times can be reduced to a minimum with different accessories.
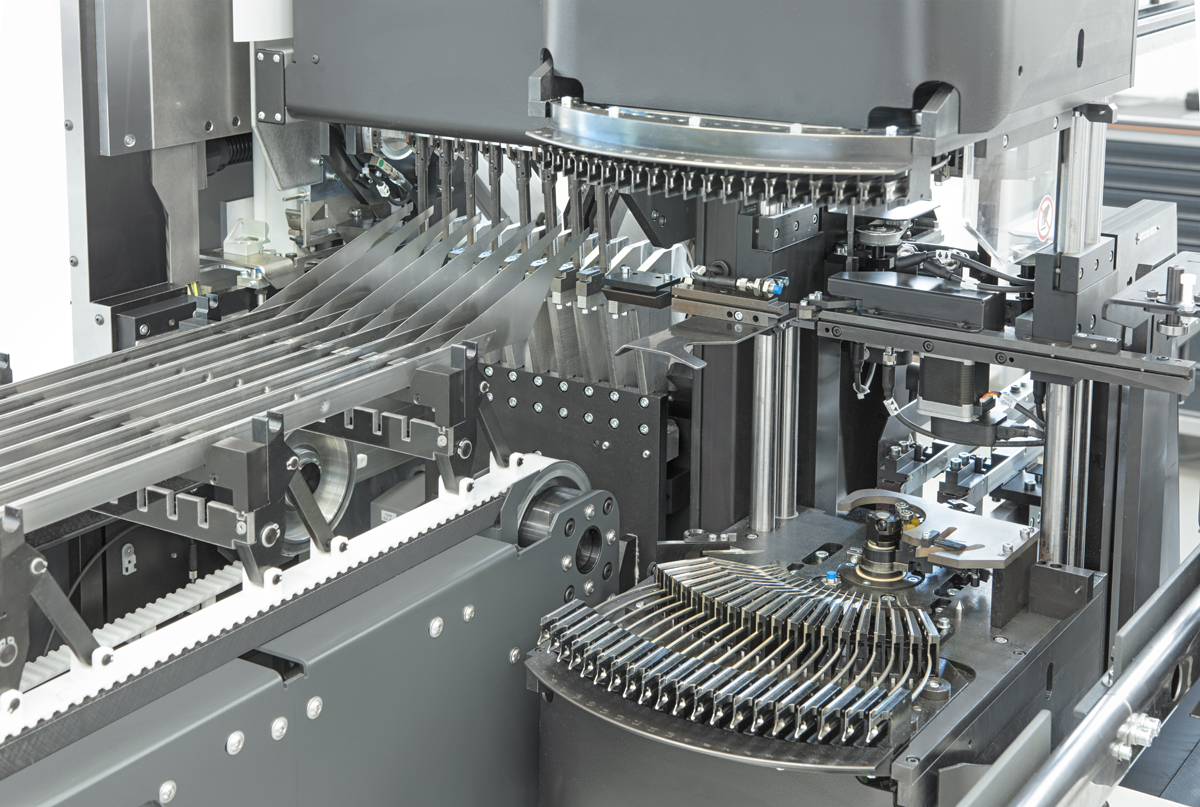
Dividing the machine into four modules further increases the ease of maintenance and service. Another advantage of the modular concept is that customer-specific machine lengths can also be realized. The WarpMasterPlus is built in two lengths as standard: 2.40 m and 4.00 m.
In addition to the completely new developments, tried-and-tested features such as video support for the operating personnel, which customers already know and appreciate from WarpMaster, were also incorporated into the new WarpMasterPlus. This makes it possible to operate the machine quickly and reliably even for persons without prior knowledge of drawing-in. Groz-Beckert is therefore also addressing the increased shortage of skilled workers in the industry.
Hands-on training
Groz-Beckert would also like to demonstrate the advantages and operation of WarpMasterPlus directly on the machine. That’s why they plan to expand their services and set up further training options in addition to the training programs that already exist at the headquarters in Albstadt. For this purpose, they will set up new showrooms this year – initially in China, Turkey and India – where, in addition to the WarpMasterPlus, other machines from their weaving preparation portfolio will be available for training, tests and demonstrations.