At the VDMA special press conference at Techtextil, speakers from member-companies like Trützschler, August Herzog Maschinenfabrik and Oerlikon Manmade Fibers Segment added content to the sometimes loosely used watch word ‘sustainability’. The perspectives ranged from sustainability as corporate culture to textile machines as enablers for textile products for recovering energy.
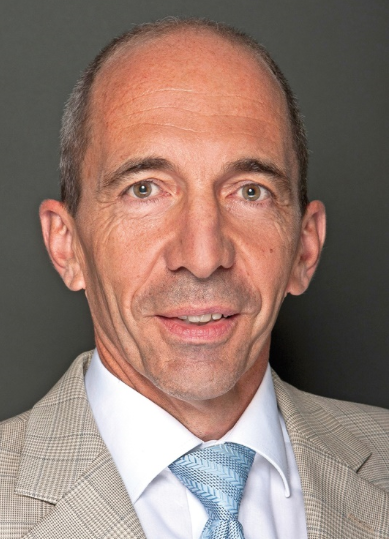
With regard to sustainability, Dr. Dirk Burger, CEO / Managing Director of Trützschler, stated that the company makes a distinction between resource optimisation and environmental protection. In the context of resource optimisation, Trützschler addresses matters such as lower energy consumption, optimised use of raw materials, low maintenance costs and investment protection. “All these points combined optimise ‚total cost of ownership‘ for the customer, which make them extremely important selling points”, said Burger.
Examples of Trützschler functions in this field include energy measuring devices that display energy consumption, and sensors for minimising waste in the machines. “We are literally fighting for each fibre, to ensure that the causes of added value and sustainability are advanced continuously”, added Burger.
Trützschler has been actively committed for a long time to environmental protection objectives. The company’s noise emission profile is significantly below all worldwide standards. “At Trützschler we began addressing dust emissions very early. In this case, the requirements of the Western world were raised to match the global Trützschler standard. This is now respected and duly recognised in Asia as well”, concluded Burger.
Braiding technology for energy recovery
Dr. Janpeter Horn, Managing Director of August Herzog Maschinenfabrik, an Oldenburg company whose history began 154 years ago, showed how braiding technology is making contribution to energy recovery. Offshore extraction of oil and gas is a field of activity not just for oil companies but also for August Herzog. “In work on open sea, conventional steel cables are being replaced increasingly with lightweight, synthetic fibre ropes that float on the water”, explained Horn.
According to him, these braids are endowed with significantly better properties and can be used at much greater depths than steel, for lifting loads, lowering parts, or mooring rigs and ships. “We provide the technology for this. The braided synthetic ropes that are produced in this way are self-supporting in the water. This enables great strength at much greater depth”, Horn added.
The energy recovery effect is obvious: Every kilogram of weight that can be saved with these much lighter textile ropes in the transportation process means that they can support correspondingly heavier loads.
Another field of action for August Herzog is lightweight construction. According to Horn, automated braiding technology from Oldenburg is not only used by BMW. Wherever loadbearing structural components made from carbon fibres are fitted, in aircraft, cars or bicycles, technology from Herzog is in demand.
Economy, ecology and social activities
André Wissenberg, Vice President, Oerlikon Manmade Fibers Segment, explained that sustainability has always been playing a significant role in the company’s strategy. The so-called e-save program already started in 2004. “Sustainability is covering economy, ecology and social activities, that’s why our efforts are addressing customers as well as our employees”, said Wissenberg, and continued: “Our latest WINGS technology (Winder Integrated Godet Solution) reduces the average energy consumption per tonne of POY (Pre-oriented Yarn) by 40% and that of FDY (Fully-drawn Yarn) by as much as 55% compared to the machines produced in the mid-1990s.”
But also in regard to the production of their machines, Oerlikon is a good example of what is possible. “In Remscheid, the recently developed one-piece flow concept was used both for a new assembly line, and for the production of the change bars, which resulted in an increase of 15% in production capacity and ergonomic benefits for the assembly personnel. At the same time, energy consumption was reduced.”
According to Wissenberg, the company has imposed strict energy management regulations, which must ensure that energy consumption is reduced by 1.5% per year. The recovery of drilled oils from machined metal by centrifuging or reconditioning lubricants, waste recycling and energy recovery with heat exchangers are other examples of how Oerlikon handles resources for sustainable results.
Thomas Waldmann, Managing Director of the VDMA Textile Machinery Association, summarised: “Today’s presentations are just a few examples showing that sustainability is an integral part in the business of our member-companies. With regard to the economic and ecological aspects of sustainability, VDMA member-companies will provide profound technological answers on how to adjust to volatile energy and commodity prices as well as ecological requirements from governments, brands, retailers, and consumers at ITMA 2015 in November in Milan.”
In the run-up to this event VDMA will publish a series of best practice examples that show how member-companies are addressing the ITMA motto “Master the art of sustainable innovation” with their technologies and concepts.