Vardhman Textiles Ltd. has recently forayed into printed fabrics by commissioning the first phase of its printed line and is now stabilising its operations. It commissioned a printed fabric facility with an annual capacity of 9 millon metres at Baddi in Himachal Pradesh. It has installed machinery with state-of-the-art technology suitable for woven, knitted and non-woven fabrics.
Vardhman has also installed laser engraving machines to get quality printing registration on fabrics. Other than cotton, the company is printing on various bases like modal, tencel, viscose, CVC and cotton poly bases, among others.
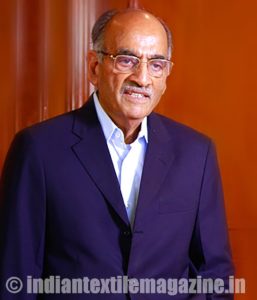
Incorporated in 1973, Vardhman Textiles is the flagship company of the Vardhman Group, one of India’s largest textile conglomerates with presence across the textile value chain, viz., yarn, sewing thread, fabric, fibre and garments. Vardhman’s humble beginning dates back to 1962 when it started its manufacturing at Ludhiana with 6,000 spindles. Today it is one of the largest textile companies in India manufacturing cotton yarns & fabrics with a capacity of over 1.00 million spindles, constituting about 2% of the country’s yarn production, 1,320 looms for weaving of fabrics and 110 million meters per annum of fabrics processing capacity.
Vardhman registered turnover of Rs. 5,728.28 crores as compared to Rs. 5,613.95 crores in the previous year.
The company incurred a capital expenditure of around Rs. 2,000 crores in the last five years. Currently it operates at near 100% utilisation levels in the yarn business, catering to diverse customer requirements. It manufactures a wide range of textile products across yarn, fabrics and fibre (acrylic) and has the operational flexibility to strengthen it further. Besides cotton yarn and blends, it is looking at more synthetic and blended yarns and is also taking steps to expand its existing fabric processing capabilities.
Vardhman enjoys a strong presence in markets like the EU, Canada, China, Japan, South Korea, Mexico, Brazil, Mauritius and the Middle East. The company has also emerged as a preferred supplier to global garment makers like Tommy Hilfiger, Esprit, Gap (including brands such as Old Navy), Zara, H&M, Mango, Benetton and Arrow.
In line with its strategy of focussing more on its core business (yarn and fabric), Vardhman sold 40% stake (of 51%) in its subsidiary Vardhman Yarns & Threads Ltd. (VYTL) for Rs. 413 crores. It is also consolidating its fabric business and focusing on expanding capacity in this space.
Going forward, the company has a planned capital expenditure of Rs. 2,500 crores over three-four years towards the ongoing schemes at Baddi, as well as the proposed expansion at Satlapur and Budhni in Madhya Pradesh and modernisation in other units.
The proposed capex would be partially towards the ongoing expansion schemes for enhancing yarn dyed and printed fabric capacity as well as increasing the looms capacity. Further, it has been proposed to increase the fabric processing capacity at Budhni, along with the installation of additional spindles at Satlapur.
Vardhman continues to invest in infrastructure, systems and certifications. Moreover, the company has its focus on ‘greener operations’ by further reducing water consumption, minimising wastage and using renewable energy resources over conventional ones.
Vardhman has realigned standard operating protocols (manufacturing and non-manufacturing processes) in line with the best global practices. It has also institutionalised periodic operational audits in line with the Standard Operating Procedures (SOPs) and invested in real-time monitoring of operations for faster corrective action. It has also put in place a systematic asset review to trace and arrest technology obsolescence and invested in top-of-the-line equipment to provide unique fabric finishes.
Vardhman has improved its technology platform, so that its process automation, product quality and monitoring processes can be upgraded to deliver higher and better output. The company’s technological capabilities have accelerated data-driven analytics and decision-making, enabling it to capitalise on opportunities at a faster rate.