Uster Technologies brought textile industry leaders together to discuss the current issues in using recycled raw material. A delegation of spinners from India met experts from Rieter, Säntis-Textiles, Otto Yarns, Gherzi Textile Organization and TVU at Uster headquarters in Switzerland. This article summarizes the challenges and opportunities of recycled yarns from both sustainability and business aspects.
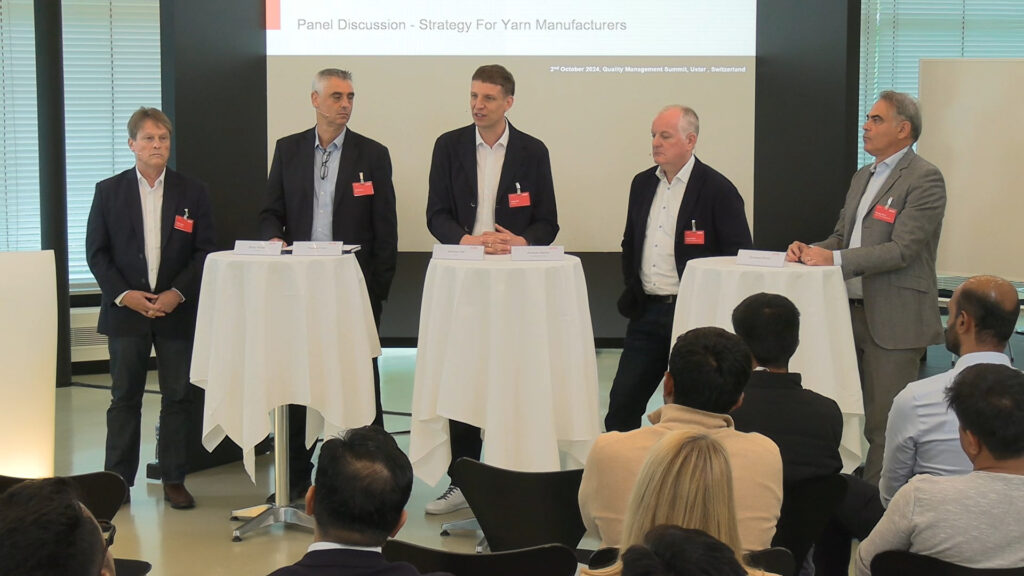
The ideas and solutions of the panelists diverge on the subject how to be successful with recycled yarns. They see different approaches to achieve the goal. The quality of recycled yarn could be improved with an additional step between mechanical opening and the spinning process, according to Michael Will (Head Textile Technology & Process Analytics) from Rieter. The pre-opening or carding does not necessarily have to be in the responsibility of the spinners. It could also be done by the fiber suppliers. Andreas Merkel (CEO) from Otto Yarns anticipates better results with pre-consumer fibers. Post-consumer waste remains a difficult raw material – although readily available in large quantities. He forecasts great future opportunities, but it will take some time.
Stefan Hutter, Owner of Säntis-Textiles, also believes in the recycling business, and that recycled material will become a standard. He expects two segments growing: one based on industrial and the other on post-consumer waste. A lot of groundwork has been done, but it’s still a good time to jump in on this business.
Looked at from a trading and dyeing perspective, the quality and sourcing of recycled yarns are challenges. Thomas Franz (Sales and Purchasing Manager) at TVU states that yarn properties are not comparable with virgin fibers – and more difficult with cotton than polyester – and so neither dyeing results nor process efficiency are the same.
Who pays for sustainable yarns?
Producers agree that there will always be a disadvantageous difference compared to virgin fibers. The question is, could consumer expectations be corrected in terms of quality and price regarding garments made from recycled raw material?
Giuseppe Gherzi, Managing Partner at Gherzi Textile Organization, makes clear that the problem is not the consumer expectations, but that retails and fashion brands are not ready to pay more for recycled garments. The power for change lies in legislation. But there’s a lot of uncertainty. In the end, regulations generate costs as they need a control system.
How to prove recycled yarn?
Technology to secure, that recycled products are genuine are available and also Uster Research & Development team is working on this subject. It is possible to verify the lifecycle of recycled items, such as denim, from their first to third use. However, the cost and whether brands are willing to pay for traceability remain concerns.
Can traceability be addressed in spinning? Michael Will says: “With innovative technology in combing a 50/50 blend could become a 40/60 but is it necessary to declare this change?” The result of the further discussion of spinning practices was that using a certain percentage of less expensive recycled fibers should be a common standard in the future as long as quality requirements are met – without the need for information or proof.
Of course, the certification also adds to the cost for yarn producers. Plants, as well as raw material shipments and shipments to the customer, need to be certified. Only when the complete chain is certified can, for example, a GRS (Global Recycled Standard) logo be applied. With a required minimum of recycled content in the product a certification system is a must. Merkel could imagine two markets in future: a mass market for cost-effective yarn production with recycled cotton fiber but no certification; and a smaller market with certificates required. There’s a crucial fact that lower prices are expected for recycled, but that’s not the case in reality.
How to make it profitable?
Making good money with recycled yarn will be possible by optimizing and shortening the processes in yarn production. Hutter believes that the costs will come down as soon the market picks up and grows and there’s more material in the market. This happened with polyester and will also follow with cotton. The market wants recycled products.
Spinners are advised to start at some point – meaning with a certain blend of recycled material – to develop recycled yarn further. It’s crucial to learn by testing and analyzing over some years finally to achieve the required product at a much better quality.
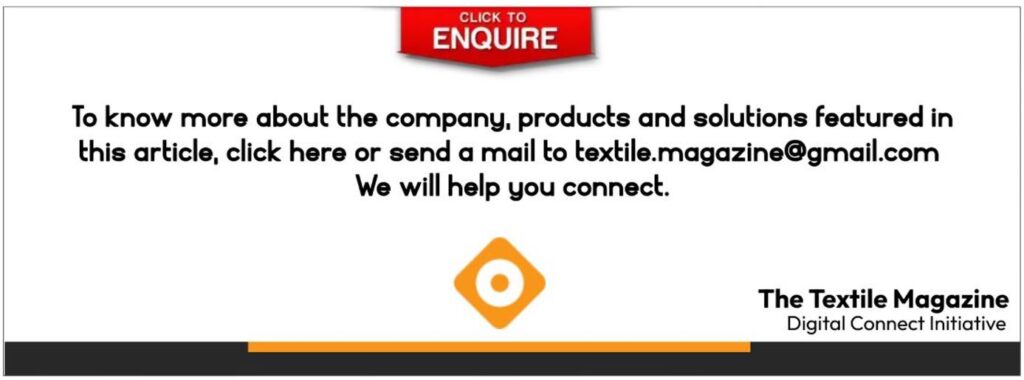