Truetzschler, a leading textile machinery manufacturer, presented its intelligent machine technologies, digital solutions and installations for sustainable nonwovens at the ITMA exhibition in Barcelona.
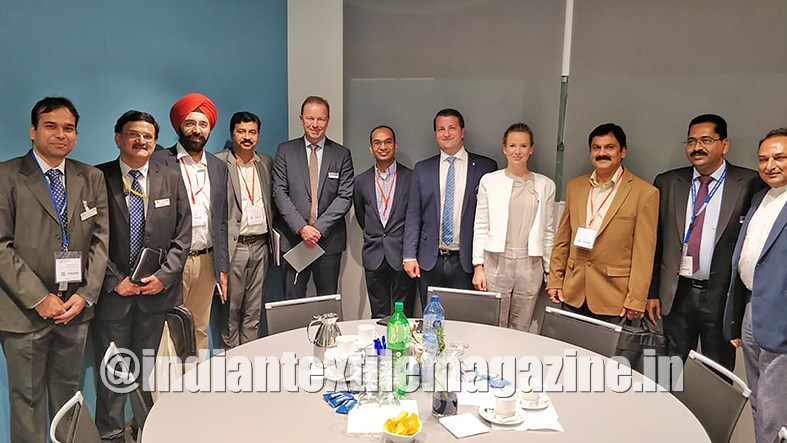
In order to meet the intelligent spinning preparation requirements, Truetzschler counts on state-of-the-art sensor technology and digital integration. The new intelligent card TC 19i is designed to automatically and continuously optimise the carding gap, whose setting has a critical influence on quality and performance. With a precision not achievable by humans, the intelligent card permanently realises even the narrowest carding gap setting of 3/1000 inch.
“This allows us to measurably improve our customers’ raw material utilization and productivity while achieving consistently high quality,” said Dr. Dirk Burger, CEO of the Truetzschler Group. In addition, new cloud-based digital monitoring and management systems provide yarn manufacturers with transparency over all processes in the spinning mill.
The My Wires app, for example, provides information on the status of clothings and service intervals and helps with the planning of reorders. Competent service for re-clothing can be provided immediately by Truetzschler Card Clothing (TCC). “With the smart networking of machines as well as production and maintenance, we support customers in simplifying their entire spinning process,” explained Dr. Christof Soest, CTO of the Truetzschler Group. “This is why our digital platforms work not only for Truetzschler technology.”
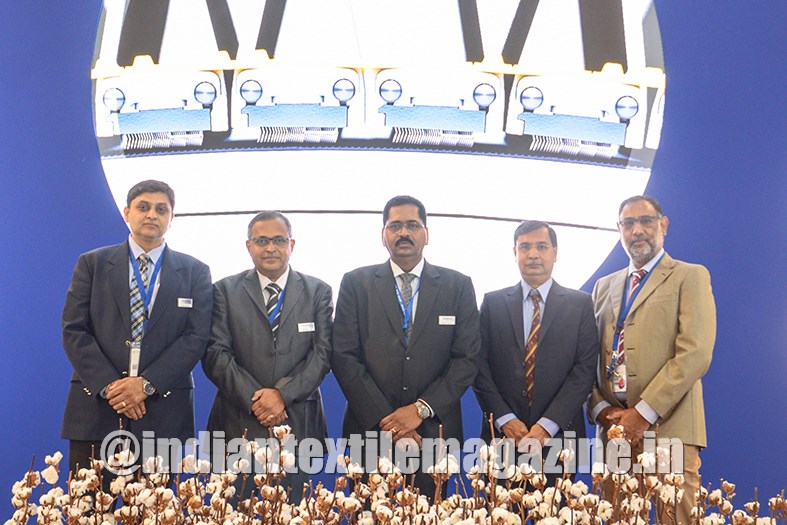
Economy and quality
The latest innovation in the blowroom offers more economy and quality as well. The portal bale opener BO-P, with widths of 2,900 mm or 3,500 mm, is said to allow significantly more bales to be placed side by side and processes them in parallel using two opening rolls. Thus, it results in significantly better blending and higher production of up to 3,000 kg/h.
As a complete supplier for spinning preparation, Truetzschler is also breaking new ground in draw frames, the quality filters in the spinning mill. The autoleveller draw frame TD 10 automatically adjusts the perfect break draft for optimum sliver quality and realizes significant cost savings due to its compact design and energy-efficient suction system. Like the TC 19i and the BO-P, the TD 10 provides the operator-friendly T-LED remote display which visualizes important machine and production information in a simple way.
Individual and sustainable
Truetzschler Nonwovens presented sustainable concepts tailored to individual customer needs. The focus is on technologies for production of biodegradable light-weight webs from renewable raw materials.
In addition to proven solutions for carded, spunlaced nonwovens made of 100% cotton or 100% viscose, Truetzschler Nonwovens has developed an alternative technology in co-operation with Voith: In a wet-on-wet process, the web is formed from cellulose-based short fibres suspended in water and then bonded by means of hydroentanglement. The sustainable, high-quality wipes and cleaning cloths that result from this process can be completely degraded by micro-organisms in the environment after usage by the consumer, the company reports.
The Man-Made Fibers division presented the new four-end BCF machine MO40, which is based on the M40 concept. The symmetrical design in combination with the lamellaless HPc texturing results in top yarn and bobbin qualities. As each spinning position produces four BCF ends simultaneously, the machine achieves high productivity at moderate speeds, ensuring a stable process. “Higher, faster, further is not always the solution, as with the entire Truetzschler Group, individual customer requirements always have priority for us. We support our customers with complete installation concepts, services and know-how – from the product idea to new business models,” emphasised Dr. Lassad Nasri, CTO at Truetzschler Man-Made-Fibers.
Tailor-made clothings
In addition to the highlights from the Spinning, Nonwovens and Man-Made Fibers business units, the Truetzschler Group presented its comprehensive services and high-performance clothings for cards and roller cards from TCC on 1400 m².
TCC completed its portfolio of special flat clothings with the MT 52, which demonstrates outstanding stability, particularly at high card productions in ring and rotor spinning. In addition, the company has developed the new Precisetop flat clothing, which is essential for the intelligent self-optimisation of the carding gap in the TC 19i.