Despite the global pandemic, exports of textile goods from China increased by almost 30% in 2020, to over $150 billion. There is now a pent-up demand from the country’s textile manufacturers for the latest advanced technologies that can further their progress in a highly competitive market, according to TMAS – the Swedish textile machinery association.
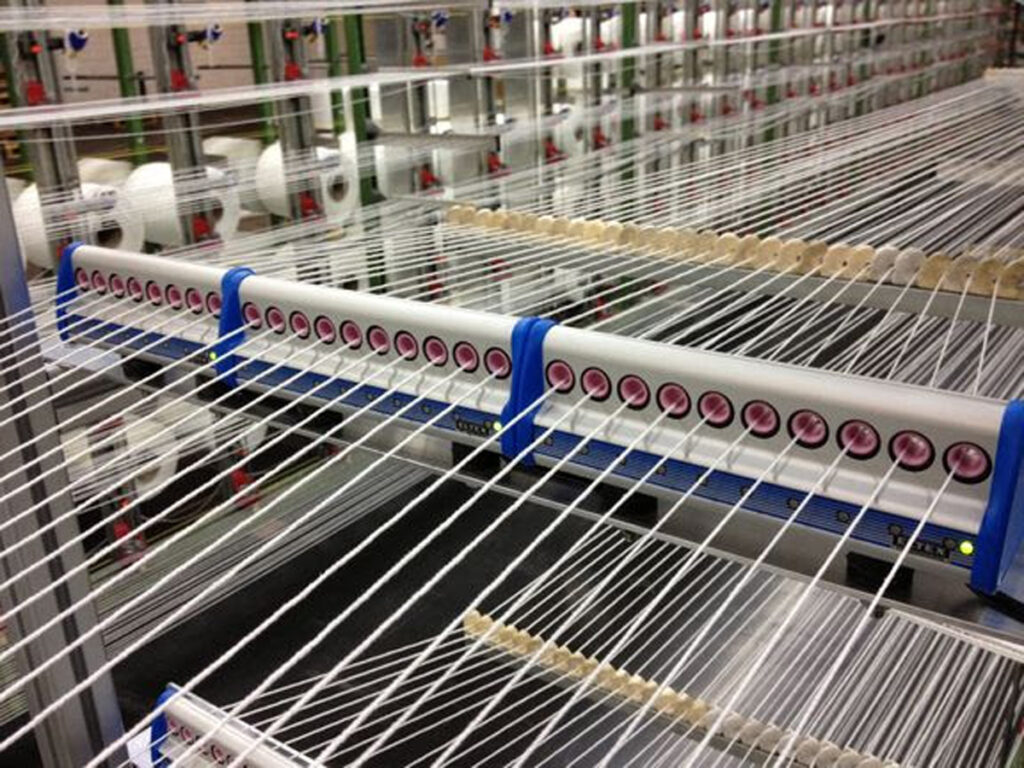
The astonishing success of China’s economy in recent years has also seen wages soaring and made it difficult for textile manufacturers to find and retain trained machine operators. This is where bespoke automation concepts can help.
“Our member companies have been forced into testing new working methods, looking at what it’s possible to do remotely and how to exploit automation to the full during the Covid-19 pandemic, in order to become more flexible,” says Premler-Andersson. “The situation has not only resulted in further transparency and openness, but more than ever before, a need for both speed and simplicity.”
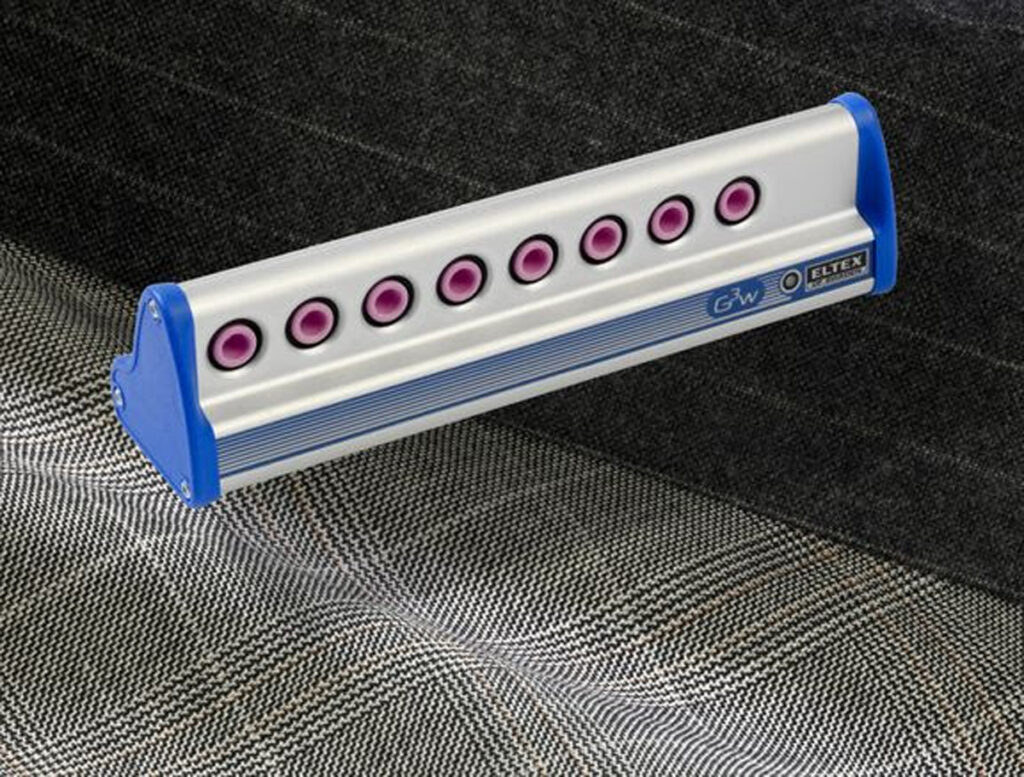
Bespoke solutions
A specialist in automated concepts is ES Automatex, the provider of bespoke cutting, sewing and folding equipment solutions for the production of bedding, towels, curtains and table linen.
Extremely simple to operate and control, the company’s latest FT0-6880-D pillow manufacturing system achieves an impressive 60% in fabric savings from standard length fabrics in converting.
“The FT0-6880-D is unique in working length-to-length with the fabric to fully construct the pillows, incorporating the folding of the flap and turnover, prior to automatic stitching,” explains ES Automatex managing director Stefan Persson. “This is made possible by a proprietary two-sided folding section, whereas the industry standard is for fabrics to be folded and stitched length-to-width, resulting in tremendous wastage. It sounds simple, but it took some intensive development work to perfect. We have a number of similar concepts we will be happy to discuss with visitors to ITMA Asian in Shanghai.”
Full monitoring
Eltex is meanwhile achieving considerable success with its yarn fault detection and tension monitoring systems across a range of sectors, including the creeling of woven materials and advanced systems for the sewn products sector.
The company’s UPG-Stitch thread break sensor is based on the piezoelectric principle and is suitable for all types of yarns while being insensitive to dust, dirt, and humidity variations.
The Eltex thread sensor is designed to monitor up to six intermittent running threads on automatic sewing machines. The eyelets are electronically scanned, and both broken and continuously moving threads are identified, allowing yarn movement to be precisely monitored even at low yarn tension.
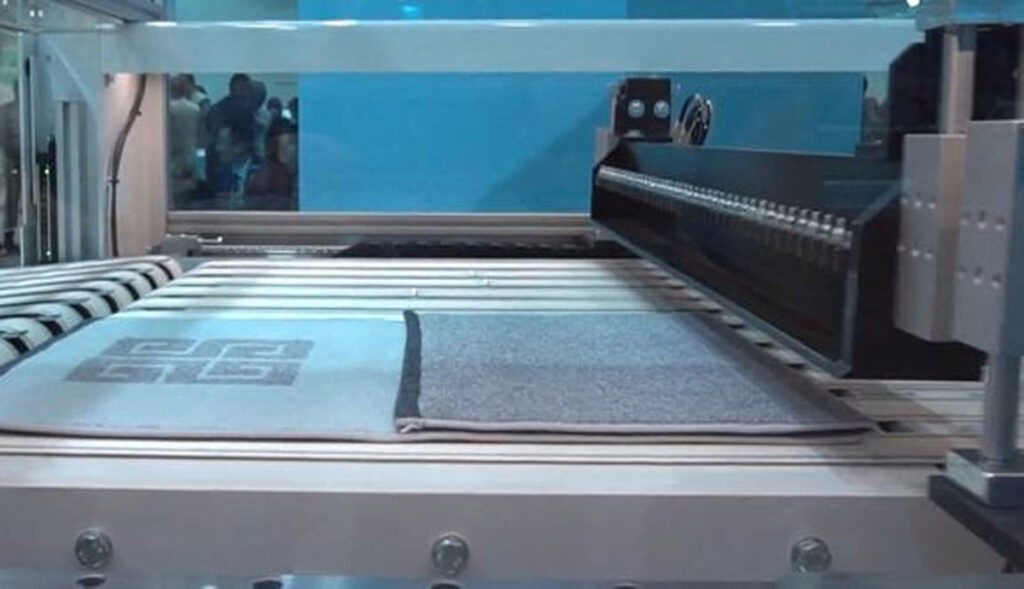
Weaving advances
As a trusted market leader in the field of weft yarn feeding and tension control units for weaving looms for many decades, Vandewiele SwedenAB today benefits from being a member of the Vandewiele Group, now one of the leading names in textile machinery worldwide.
Systems are supplied to the majority of the leading weaving machinery manufacturers for their new looms and the company also develops advanced products for retrofitting to working mills around the world.
Following significant investments in R&D capabilities at its base in, Sweden, Vadewiele has introduced innovations to further automate the weaving process.
“We look forward to discussing methods for enhancing the weaving process with customers old and new in Shanghai,” says Sales and Marketing Manager Pär Hedman. “We are also very aware of the desire in China to further expand the country’s technical textiles base and expect great interest in our latest ZTF Zero Twist Feeder, particularly from companies involved in the growing market of textile reinforcements for composites.
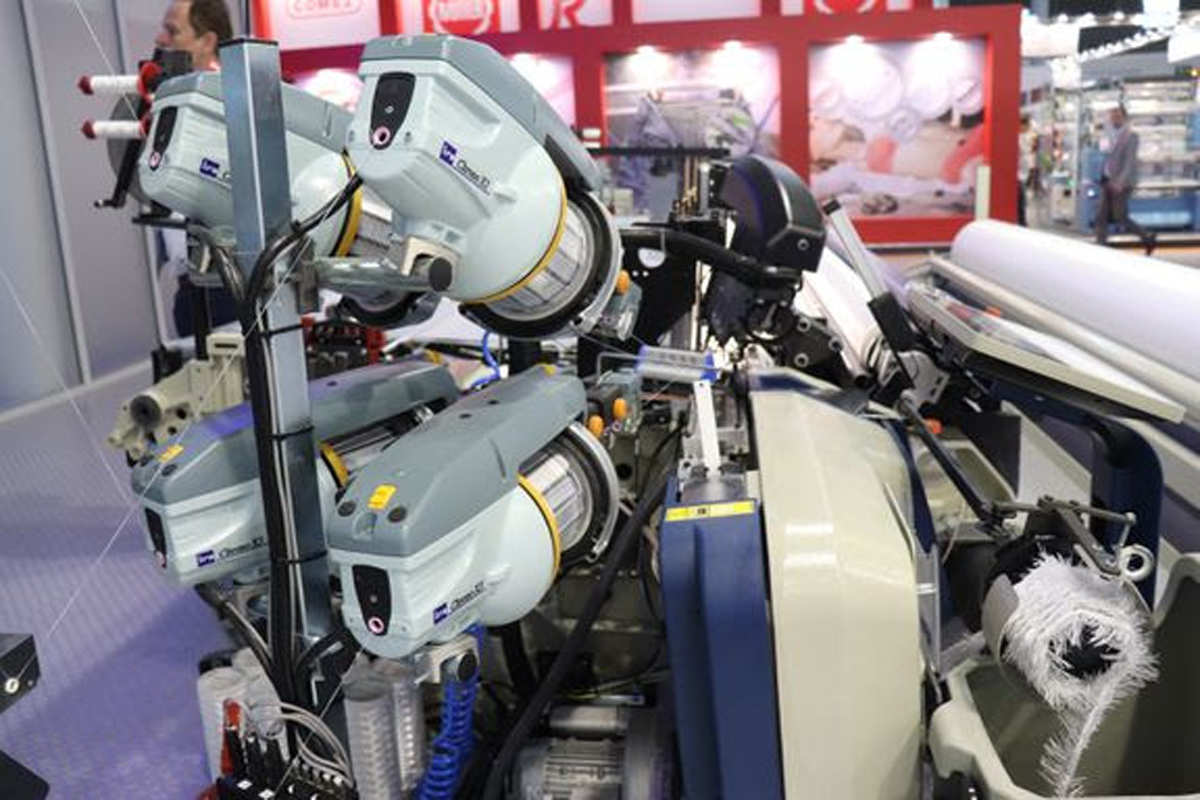
Composites
“In the weaving of fibres such as carbon, glass and aramids, as well as thermoplastic tapes for highly engineered composite fabrics, it is essential that there is no twist in the feed, which this new machine absolutely guarantees.
“It keeps the tape yarns or fibre tows constantly stretched to avoid the risks of any snarls or twisting and is being supplied in bespoke versions specific to the individual needs of each customer and the intended end-use.”
The ZTF Zero Twist Feeder can accommodate tapes in widths up to 10mm and weights up to 7kg, with an insertion length of up to 3.4 metres. It is equipped with a buffer arm synchronised with the rapier movement of the weaving machine to deliver the exact amount of yarn from the bobbin required for the weft insertion. A tension and sensor arm ensures constant yarn tension is maintained during the entire insertion cycle.
Swedish TMAS member look forward to seeing you at ITMA Asia + CITME at the National Exhibition and Convention Center in Shanghai from June 12-16. ES Automatex is at stand H5 F16, Eltex at H3 A01 and Vandewiele SwedenAB can be found at H3 D01.