The new generation of the Thread King winder is living up to expectations. It offers the perfect combination of efficiency and sustainability, with a shorter production cycle, easier thread-up of the yarn, reduced machine footprint and lower power consumption.
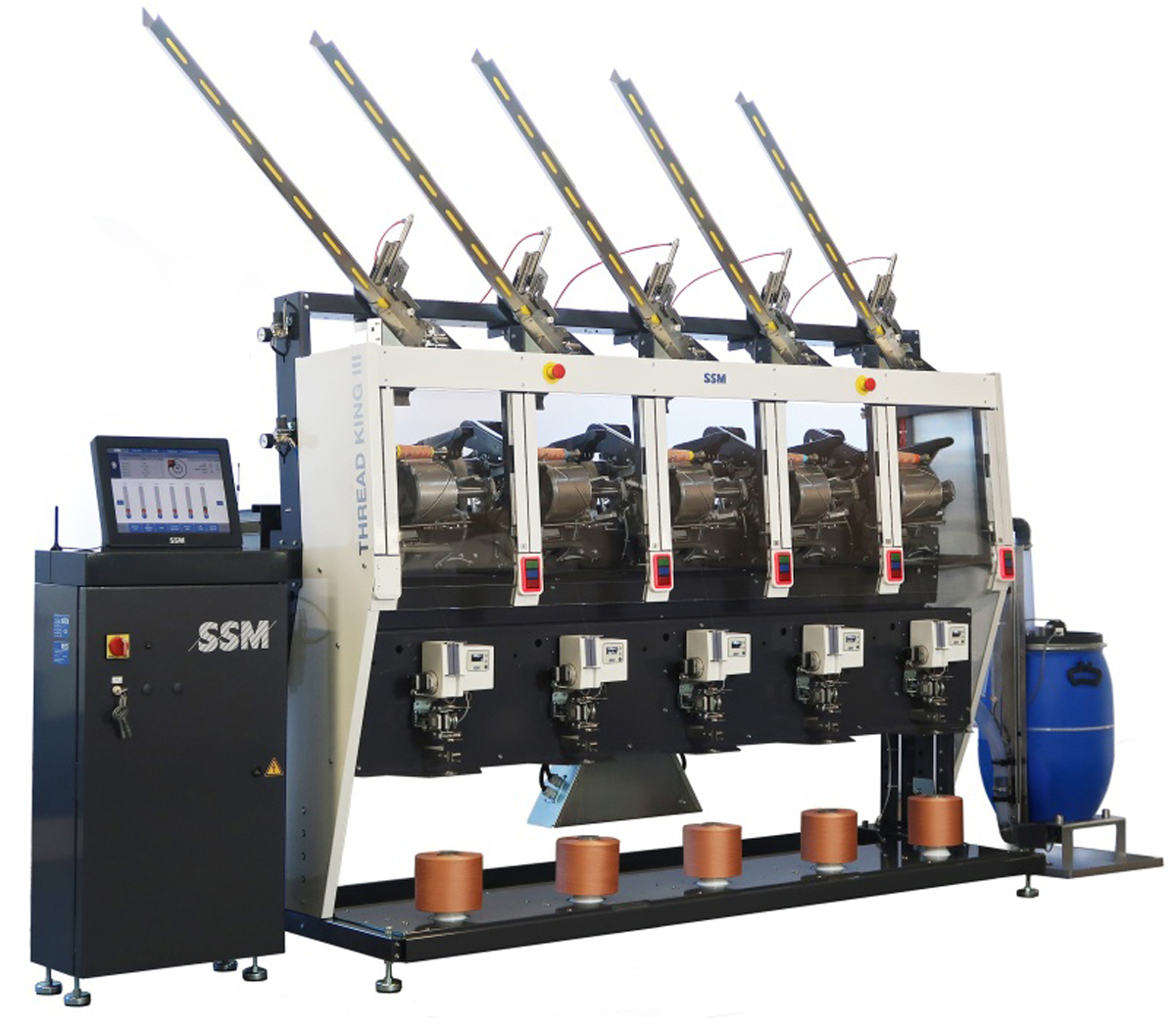
The reputation of the Thread King is second to none. Over the years, it has continuously been loaded with advanced technology to always stay ahead of competition. This new generation, the Thread King III (TK3), is more efficient than ever with an increased supply tube capacity, a shorter doffing cycle of up to 40% and a raw material saving of about 1%. The machine is also IoT ready and can be equipped, as an option, with Nema, SSM digital suite.
Pushing sewing thread production beyond limits
The Thread King III (Fig. 1) is all about efficiency. Thanks to a patented tuck-in system (Fig. 2), the TK3 has the shortest doffing cycle on the market, up to 40% shorter than its previous version. It is the first in its category to feature an automatic slit-drum opening (Fig. 3). This allows a quick thread-up of the yarn with one hand, easy maintenance and clean-up – all save a considerable amount of time. The encapsulated locked winding heads provide full safety for operators.
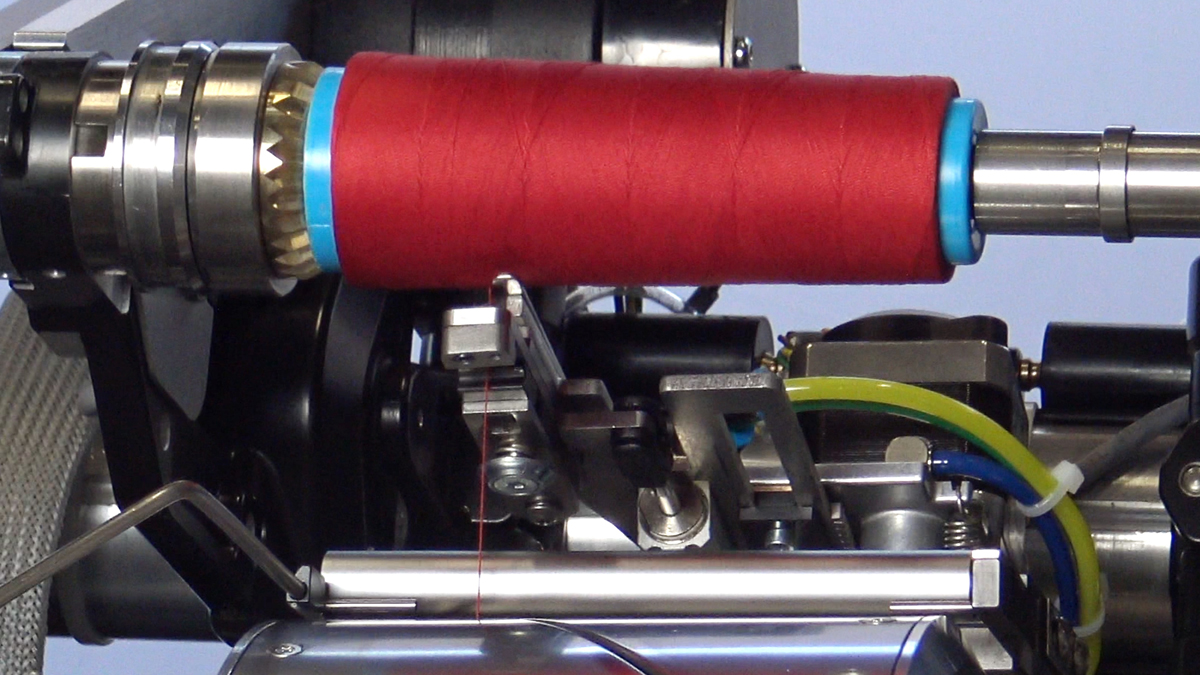
In terms of sustainability, the TK3 certainly checks the box. The design of the TK3 has been optimized to reduce machine footprint. With speeds up to 15 000 rpm, the Thread King III offers a short production cycle: fewer machines are required for the same production capacity, resulting in less energy consumption, less waste, and thus more sustainability.
Cost saving drive
The new winder benefits from improved length measuring accuracy. This ultra-precise capability results in 50% reduction of the safety margin on wound packages, thereby saving 1% raw material. To go even further, the Thread King III is equipped with SSM innovation preciforce, the first system to allow regulation of the backpressure force for a precise package build-up without any density or diameter deviation.
This third generation of Thread King also comes with the new lubetex high precision lubrication system. lubetex delivers the exact right quantity of lubricant needed – not less, not more – for a positive impact on the environment and costs.

From king spools to cones
Like its predecessor, the TK3 is available in two versions: TK3-CT for cones handling and TK3-KT for king spools. Compared to the previous model, the supply tube capacity of the TK3 is doubled with the king spool version, and even quadrupled with the cone version, depending on tube size. Both machines offer the highest possible bobbin and yarn quality. Two other versions with different executions are planned.
With the Thread King III, SSM confirms its position of leader in the winding machine market. This state-of-the-art machine improves customers’ profitability while delivering outstanding quality and contributing to significant cost savings.