In today’s competitive nonwovens industry, the pursuit of manufacturing excellence has never been more critical. Rising energy and raw material costs, coupled with increasing customer demands for quality and sustainability, are squeezing producers from both sides. While investing in cutting-edge machinery is often seen as the primary solution, true production excellence requires a more holistic approach.
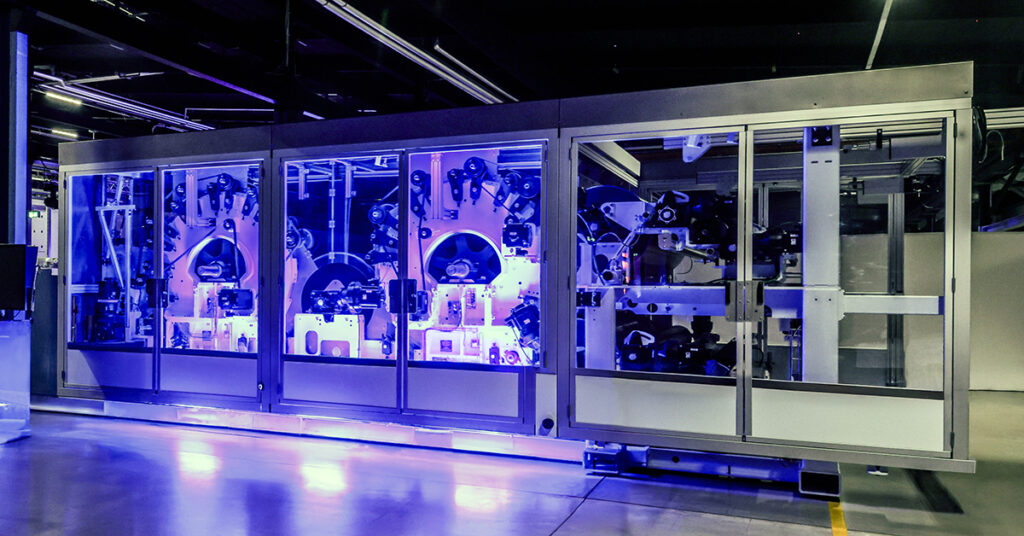
NCT-X at T-SUPREMA customer days in April 20204; NCTC Technical Center Egelsbach
Trützschler’s X-Series: engineering excellence in nonwoven cards
At the heart of any needle-punched, hydroentangled and air-bonded nonwoven production facility is undoubtedly the carding machine. Our new X-Series nonwoven cards—the NC-X and NCT-X—represent the pinnacle of engineering excellence, designed specifically to enhance product quality, machine availability, and raw material efficiency.
Three key innovations stand out in these next-generation cards:
- Rail-mounted card modules
Perhaps the most visible innovation is the modular design with all card components mounted on linear rails. Each module can be easily moved apart by up to 1,600 mm, providing unprecedented access for cleaning and maintenance. This feature reduces daily cleaning times by approximately 20 minutes, creating up to 100 additional production hours per year—a substantial boost to overall equipment effectiveness (OEE).
- Good fiber recycling
The X-Series features a separate suction system that captures good fibers from the web edges at both doffers. Unlike conventional systems that just suck off these fibers with the standard aspiration system, the X-Series allows these valuable fibers to be reintroduced into the production process. This innovation alone can save up to 2.5% of primary fibers annually – translating to significant cost savings and improved sustainability.
- Additional Worker/Stripper Pair
The NC-X variant features an innovative 5+5 worker/stripper configuration, adding an extra carding point on the pre-cylinder. This enhancement significantly improves fiber singling, parallelization, and blending quality, resulting in superior web formation and ultimately better end products.
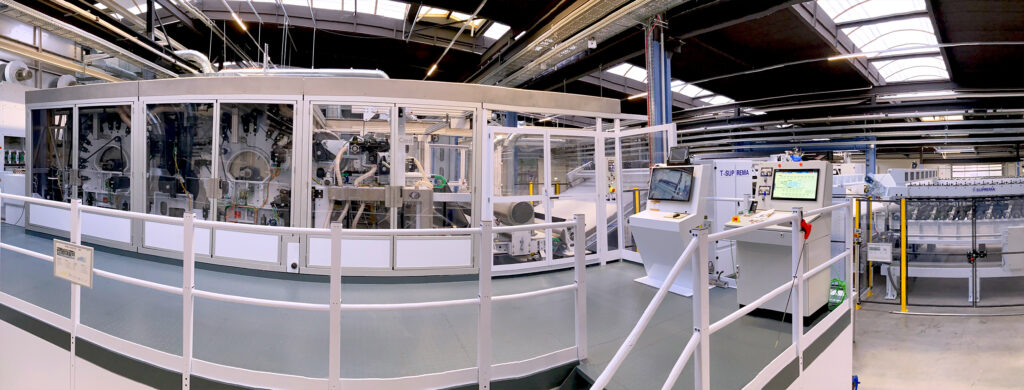
Application excellence: the right card for every need
T-SUPREMA needle-punching lines
In needle-punching applications, the NC-X delivers exceptional value through reduced downtime and fiber savings. T-SUPREMA lines equipped with these cards offer an impressive working range from under 35 to more than 1,500 g/m². For demanding applications like visible automotive textiles, the high-performance NCT-X provides maximum carding and blending capabilities, ensuring flawless appearance of the final end product.
Hydroentangling lines
For spunlaced nonwovens producers, the X-Series cards deliver three critical benefits: reduced cleaning time, lower fiber consumption, and maximum web width. Compared to other cards on the market, Trützschler Nonwoven cards provide up to 4% more usable web width at the same nominal working width—directly increasing sellable product. The flexible doffing section with swivel upper condensing rollers, easily removable lower condensing rollers, and stepless adjustable take-off rollers allows quick adaptation to different product requirements.
Through-air bonding lines
In through-air bonding applications, the NC-X variant excels with its 5+5 worker/stripper pairs, good fiber recycling, and shortened cleaning times. This makes it particularly suitable for producing lightweight hygiene nonwovens, including ultra-soft topsheets for diapers with weights significantly under 20 g/m², where precise blending of expensive melt fibers with more economical base fibers is essential.
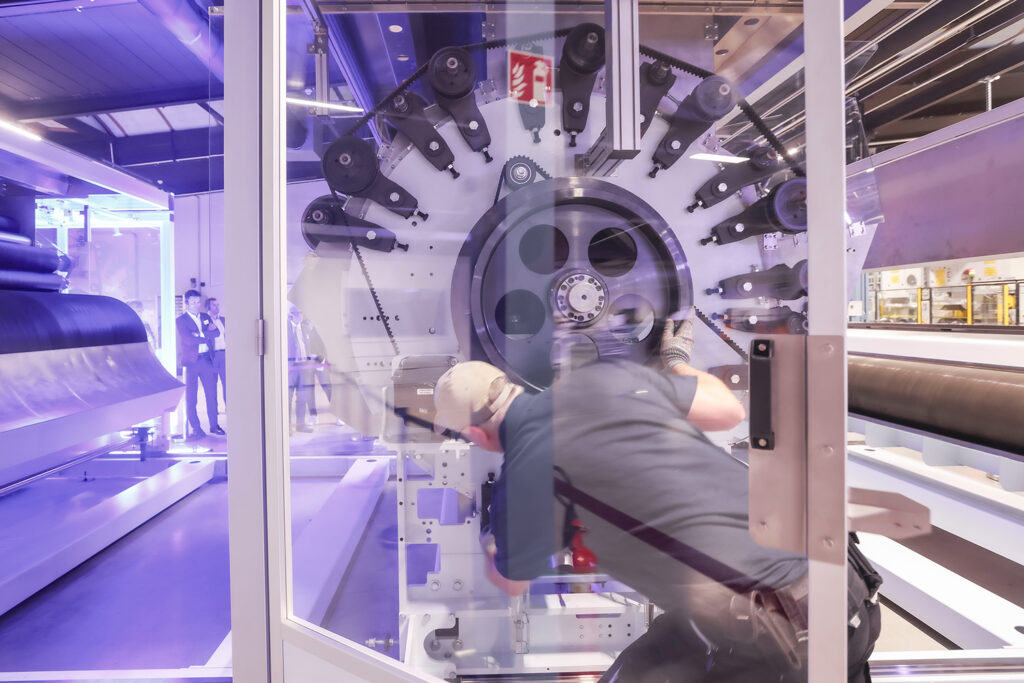
Beyond machinery: the continuous adjustment mindset
Operating a nonwoven production line is much like driving a car. Even on a straight highway, a driver must make continuous small steering adjustments, brake or accelerate as needed, and maintain awareness of surrounding conditions. Similarly, nonwoven production requires constant fine-tuning and adjustments to maintain optimal quality and efficiency.
No matter how advanced the machinery, today it is both human expertise and digital tools that are essential for translating mechanical capabilities into consistent, high-quality output. This is where Trützschler Nonwovens’ T-ONE digital platform becomes the perfect complement not only to the X-Series cards.
T-ONE : the digital partner for continuous improvement
Our software package is more than just a machine monitoring system—it’s a comprehensive digital environment that implements best practices, collects and analyzes production data, and supports continuous improvement across the entire manufacturing ecosystem.
Key capabilities of T-ONE include:
- Centralized data hub
T-ONE creates a single source of truth for all production-related information, from product specifications and quality data to machine parameters, consumption metrics, and custom KPIs. This comprehensive data repository enables informed decision-making and provides the foundation for the integrated, ai-based optimization algorithms.
- Digitalized workflows
By digitalizing critical processes like quality control, recipe management, and line monitoring, T-ONE eliminates paper-based workflows, reduces human error, and ensures consistent application of best practices across shifts and production runs.
- Systematic problem-solving
When quality issues arise, T-ONE supports structured root cause analysis, helping teams identify and address the underlying causes rather than merely treating symptoms. An easy-to-use project management tool helps keep track of and resolve any issues.
- AI-powered optimization
Advanced algorithms simulate and optimize production settings to achieve multiple objectives simultaneously, such as maximizing throughput while minimizing energy consumption and waste.

Real-world success stories
A manufacturer of nonwoven cleaning wipes implemented T-ONE’s recipe management and process documentation modules, resulting in line speed increases of up to 40% depending on the product. The system’s ability to capture and standardize optimal settings for each product type eliminated the variability between shifts and operators.
In another case, a technical nonwovens producer reduced waste by 30% and doubled production speed by implementing the same T-ONE modules. By digitalizing their process knowledge and implementing systematic quality monitoring, they transformed tribal knowledge into standardized excellence.
The future of nonwoven excellence
True production excellence in nonwovens manufacturing is not just about machinery alone. The X-Series cards – as many other of our solutions – provide the mechanical foundation, while T-ONE delivers the digital infrastructure needed to maximize their potential.
Looking ahead, we can expect even greater integration between machinery and digital systems, with real-time optimization becoming the norm rather than the exception. Manufacturers who embrace this holistic approach to excellence will be best positioned to thrive in an increasingly competitive and demanding market.
The path to excellence isn’t found in machinery alone—it’s discovered through the powerful combination of innovative technology, digitalized workflows, and a relentless commitment to improvement.