Draw frames are key in every spinning process because they play a lead role in determining the quality of the yarn that is manufactured. So regular maintenance and care are required to ensure top performance. Rieter’s new maintenance concept features a range of essential upgrades that help draw frames reach new heights. The SERVOdrive for auto-leveler draw frames is a shining example of how the quality of the sliver can be improved while overall costs are reduced over the long term.
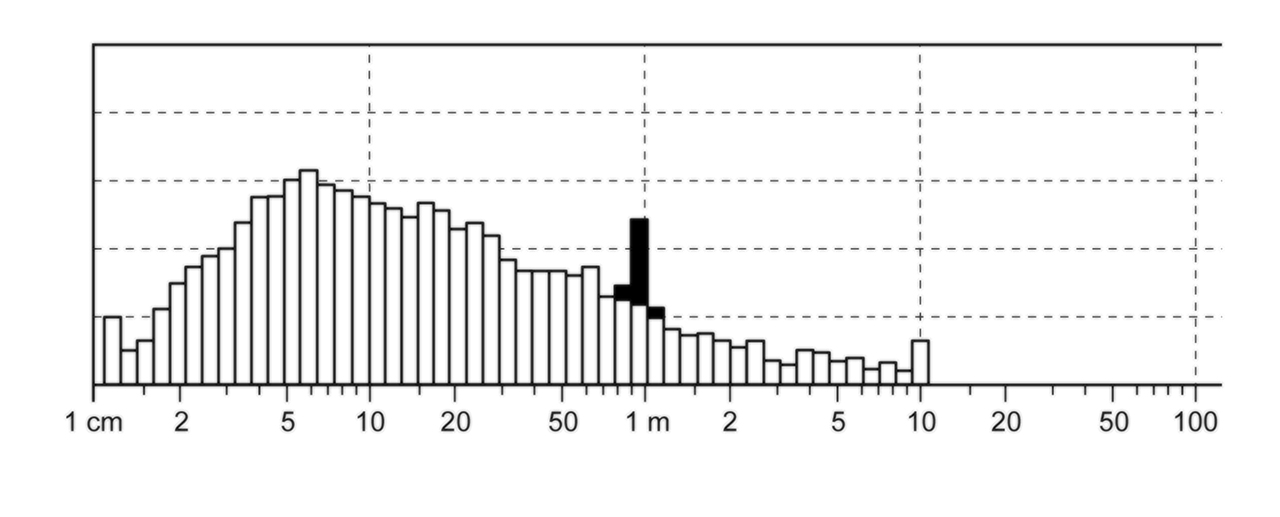
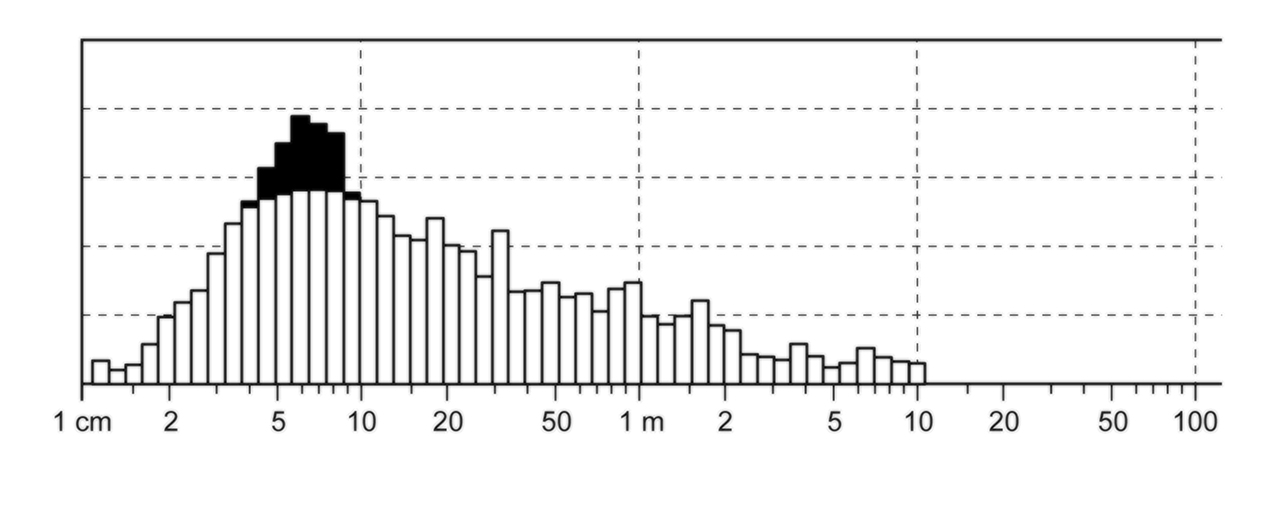
Rieter’s new draw frame maintenance concept takes a comprehensive approach. It defines the machine as a system of components that need to work together as a team so they can deliver the best results. One of the key components is the levelling system. Replacing it with a new SERVOdrive not only improves the quality of the sliver. It also reduces overall maintenance costs as high-maintenance components such as the gearbox are eliminated.
Recognizing Signs of Fatigue
Draw frames improve the evenness of the sliver for the downstream spinning process. After years of operation and heavy use, the quality of the sliver shows minute variations. As parts slightly wear out over time, the machines can no longer run at high speeds which is why some operators choose to reduce the machine speed to achieve the same quality. In practice the quality monitor or control settings are often enlarged or bypassed to increase speed, resulting in lower quality. In these cases, maintenance restores the machine performance and reduces the number of warnings and standstills.
Engineered Parts as an Ideal Solution
Condition-based maintenance can be done for machines up to an age of six or seven years. After ten or more years, multiple components run out. This is when Rieter recommends its customers to integrate new technology components to enhance machine performance. Instead of replacing the old part one-to-one, a new, engineered part is the ideal solution. The levelling system of an auto-leveler draw frame is subject to a high workload. The new SERVOdrive upgrade is a state-of-the-art replacement for the levelling system. A cost-effective and highly dynamic drive concept, it is used in the latest draw frame generation (RSB-D 50). SERVOdrive replaces four maintenance-intensive parts – motor, brake, coupling, gearbox – with just one that is maintenance-free. On top of the technological advantages, there is also an economical argument for a SERVOdrive upgrade: A collective single part replacement is more expensive over the long run than new technology. Hence, a SERVOdrive upgrade saves maintenance costs in the long term. The exchange of the levelling system is all about the right timing.
When to Exchange Motor and Gearbox
The existing levelling system consists of motor, gearbox, coupling and amplifier (controller). Rieter uses high performance quality motors that have an internal temperature sensor that acts as a safety mechanism: Gearing sluggishness causes the motor to overheat, which is when the sensor stops the drive, preventing consequential damage to the motor winding. But the most common failure occurs because of worn out ball bearings of the motor shaft. The bearings are lubricated at the factory. The grease is used up after a while so that the bearings run dry and become firm. If they are not replaced, quality losses arise due to the lower drive dynamic.
Another focus area is the gearbox. When it becomes stiff due to defective bearings or oil leaks, it runs hot, which negatively affects the levelling performance. Besides operational limitations, there is a mechanical limitation of the bearing exchange. The motor and gearbox casings have a press fit for the bearings, which are worn out after two to three bearing exchanges. For such cases, an elaborate overhaul strategy should be considered.
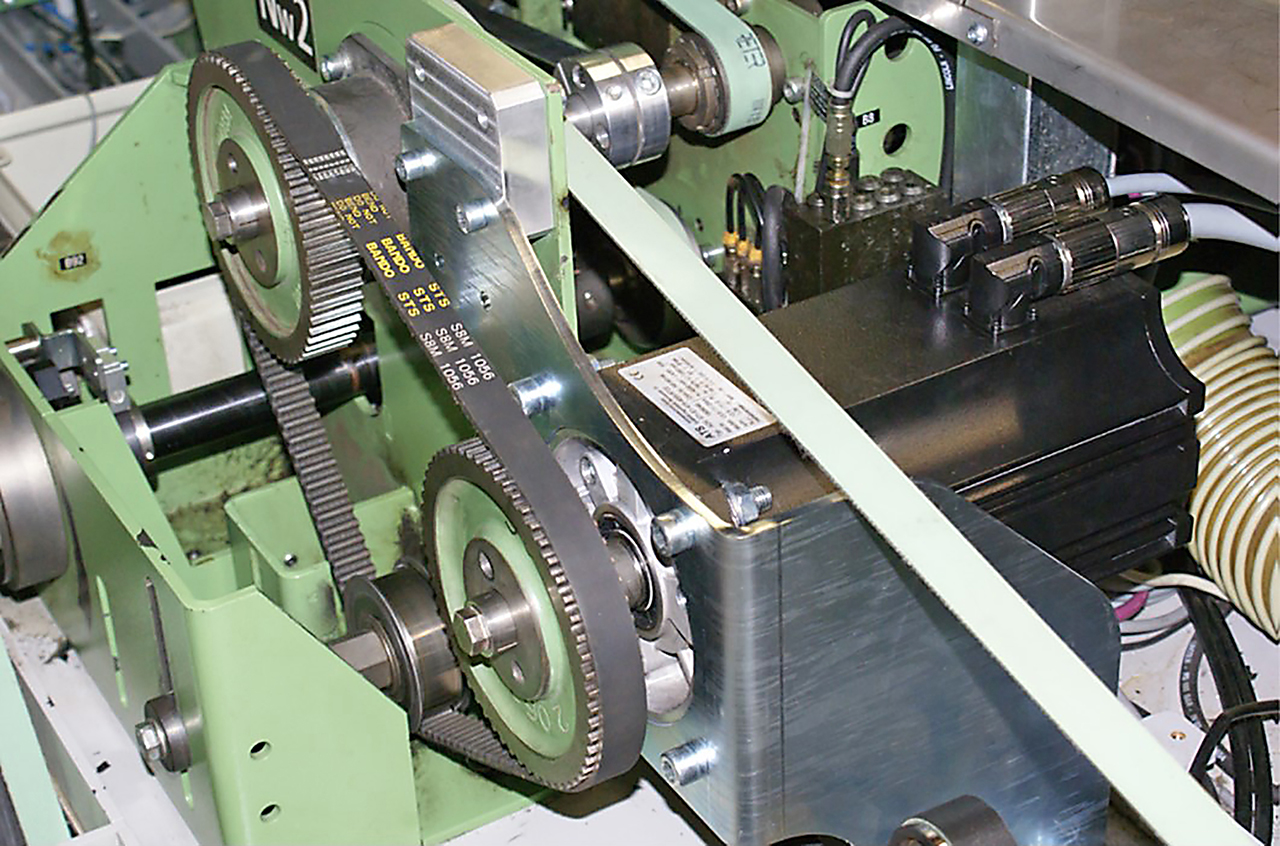
Error Analysis and Search
If the motor and gearbox function flawlessly, they ensure a consistent sliver quality. Under heavy use, the parts wear out and the levelling system loses its dynamic ability. Levelling related issues can also be associated with sluggish mechanics. They reduce the dynamic of the system and cause delays between the scan and the drafting zone. This negatively affects the levelling performance. The timing is no longer accurate so that the levelling is performed at the wrong segment of the sliver. To identify these errors, the built-in spectrogram-troubleshooting function supports operators (Fig. 1). The spectrogram characteristics accurately point to wrong parts or settings in different zones of the machines. There are two spectrogram errors: peaks (single channel) and draft waves (multiple channels). Peaks arise from errors related to rotating parts. The sliver passes through the machine’s moving parts. If one part quivers, the sliver is disturbed resulting in a peak. Draft waves arise for three reasons. First, because of poor textile technology settings such as a faulty drafting system setting. Second, because of wrong sliver tensions and sliver guiding elements, or thirdly because of the quality of the raw material.
The good news is that there is a simple solution to correct the spectrogram errors which is cleaning and maintenance. The aim is to avoid spectrogram peaks and CV%-values outside the targeted range. The following steps help to locate and correct errors:
1. Get the basics right
Clean and adjust the machine and check the free movement of all rotating parts. Check the mechanics such as the shafts, bearings and gears, belts and pulleys. Don’t forget the scanning discs in particular. If errors in the spectrogram persist, check the functionality of the machine by running it with the auto levelling turned off. If peaks still show up in the spectrogram, this is related to the mechanics. The values of the CV%-diagram provide another error indication. If these deviate from the usual standard values, this usually indicates that the levelling system is not functioning properly.
2. Align with Uster tester
For the quality values, the machine mechanically measures the scanning disc deflection and gives an indication of the error. The Uster tester by contrast uses an exact capacitive measurement method that is used as a guiding value. The laboratory values can be entered into the machine to calibrate the machine CV% with the laboratory CV%. A comparison of the machine’s values, based on the Rieter Quality Monitor (RQM), with the values measured in the laboratory by the Uster tester enables the identification of errors.
3. Verify the electronics with a cross-change
Use electronic parts such as motor or frequency converters of a second machine to either identify or exclude errors based on electronics.
Rieter’s Service Offering
Rieter’s latest motor generation, called SERVOdrive, shifts the drive concept from a mechanical to an electrical gear making it simple and reliable. It includes the M90 SERVOdrive, the G90 servo amplifier, the new soft starter and the new non-contact B92 encoder. Immediately available, this upgrade enables a high dynamic levelling system that is easy to maintain and operate. It is compatible with the RSB-D 30/35 and replaces all existing upgrade solutions. The new drive concept for the RSB-D 40/45 (Fig. 2) is available starting in 2022. More information about the new draw frame maintenance concept can be found in the latest brochure on www.rieter.com.
Rieter’s After Sales organization leverages its vast experience in retrofitting and extending machine lifecycles to help customers get the greatest value from their machines and systems throughout the entire life cycle.