The Pallava Group, established in 1971, has consistently prioritized quality in the textile industry, particularly in Vortex and Ring spinning. With over 80% of its products exported globally, the group has recently enhanced its operational capabilities through advanced technologies from Indo Texnology. Mr. Muthu Lakshmanan, President of Pallava Group, discusses the significant benefits of these innovations: the **Automatic Cone Packing System** and the **KNIT I – Online Fabric Inspection System**.
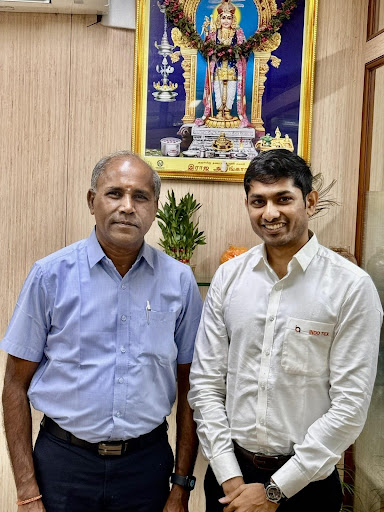
Automatic Cone Packing System
The integration of the Automatic Cone Packing System in Pallava’s Vortex unit, which has a production capacity of 26 tons, has brought remarkable improvements. Mr. Lakshmanan notes that this system has reduced the workforce dedicated to packing by more than 50%. He emphasizes the advantages:
“Now, we also have an edge on the realization. More precise accountability ensures that labels are generated automatically, eliminating manual errors.”
This precision in packing not only enhances efficiency but also improves accountability. The automatic generation of packing lists and invoices has streamlined operations, reducing duplicative tasks and disputes related to packing quality.
In comparing manual packing to the automated process, Mr. Lakshmanan highlights the consistency and quality of finished bags:
“The finished bags are too good, consistent, and neatly done. The shape and method of packing are really good.”
The Auto Cone Pack System effectively prevents cone de-shaping and damage, ensuring that products reach customers in optimal condition.
Innovating Fabric Inspection with KNIT I
Indo Texnology’s KNIT I system represents a significant advancement in fabric inspection technology that surpasses any traditional fabric scanners with its advanced capabilities to see even the minute spandex defects (Lycra jumps or misplating). Used in Pallava’s knitting plant for viscose and modal fabrics, this system captures faults during the knitting process and provides detailed reports on defects. It halts production upon detecting a fault, which minimizes fabric wastage and ensures that only high-quality products proceed to packing.
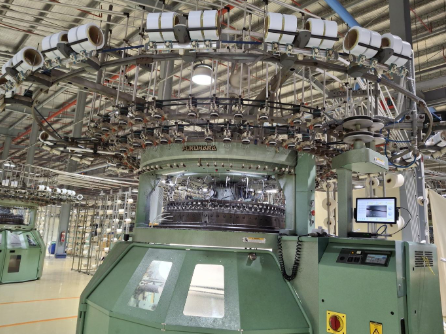
Mr. Lakshmanan appreciates this innovation for its efficiency:
“If we install KNIT i on all the knitting machines, there will be no need for fabric inspection on the inspection table.”
By eliminating the requirement for additional inspections, KNIT I allows for direct packing and selling of fabric, reducing handling time significantly.
After-Sales Support:
Pallava Group has also benefited from Indo Texnology’s robust after-sales support. Mr. Lakshmanan describes the responsiveness of their engineers:
“The after-sales support is too good. Within a call away, the engineer comes and attends.”
This level of support ensures that any issues can be resolved quickly, either through direct assistance or remote troubleshooting.
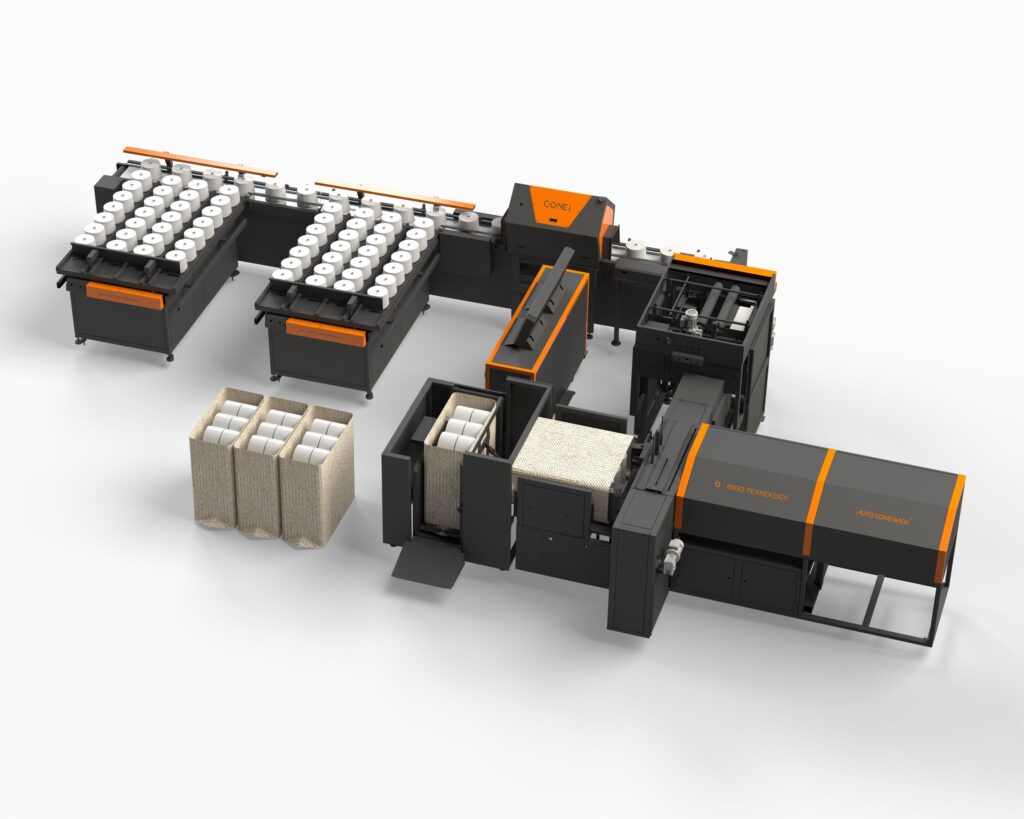
In conclusion, the collaboration between Pallava Group and Indo Texnology highlights how innovative technologies can enhance efficiency and quality in textile manufacturing. The Automatic Cone Packing System and KNIT I Online Fabric Inspection System are not just improvements; they represent a strategic shift towards greater reliability and productivity in the industry.
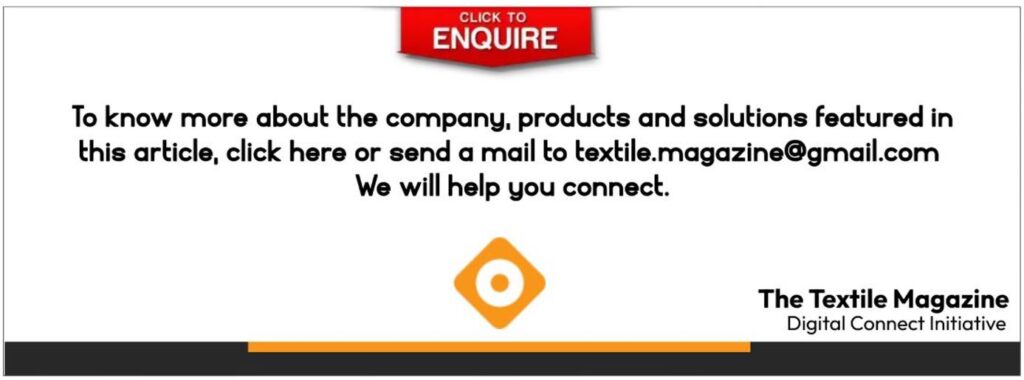