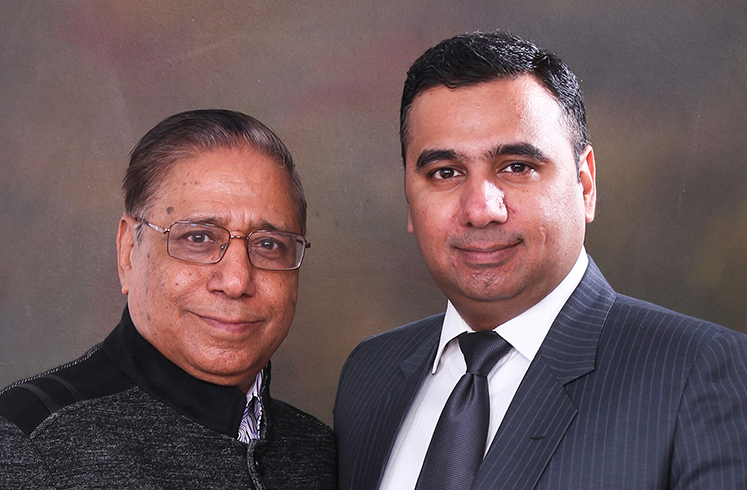
Excerpts from an interview with M S Gaur and Anubhav Gaur of THE GAURS
THE GAURS was established in 2010 with an aim to bring to India and surrounding regions innovative European machinery for dye houses. Since the beginning, the focus has been to provide next-generation machinery, technology and solutions which promote sustainability, have lower energy and utilities consumptions, are green for the environment and promote circularity in textiles. The machines are designed to bring a visible difference in the customer’s life in terms of lower energy and low utilities consumptions and giving back faster ROI when compared with the traditional dyeing and finishing machinery available in the market.
THE GAURS started out initially promoting calendar rolls, rubber rolls and special nonwoven-based squeeze rolls. Today, the company has grown to be able to provide a comprehensive set of machineries required by any dye house. The core focus, however, still remains the same – wet processing and dry finishing. THE GAURS today caters to customers located in India, Sri Lanka, Bangladesh, Thailand and Indonesia markets.
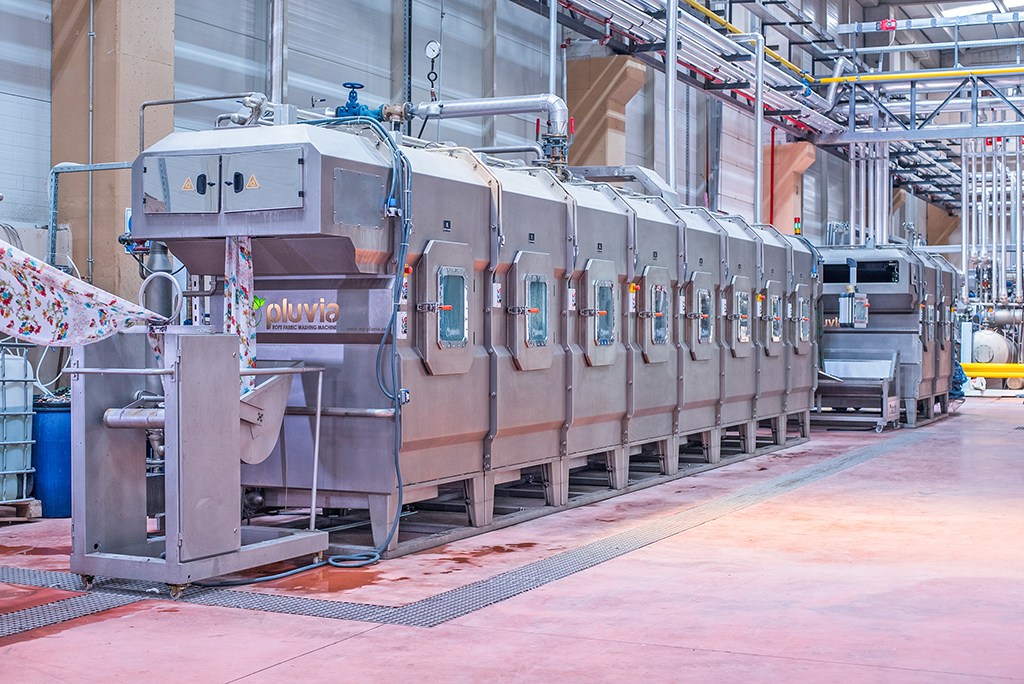
Global Principals Represented by the Company
THE GAURS represents machinery manufacturers from Germany, Italy, Sweden, United Kingdom, Turkey and Switzerland and are able to offer a wide range of machinery across the dyeing and finishing process such as:
• Singeing (for wovens, knits, technical textiles and nonwovens) – Parex Mather
• Scouvering and bleaching ranges – Pluvia and Revozona
• Jiggers – Memnun Makina
• Exhaust dyeing – Beneks Makina
• Waterless dyeing – Imogo and Alchemie
• Cold pad batch dyeing – Polteks
• Washing ranges after dyeing and print washers – Pluvia
• Rope opener and slitters, tubular padders and pre-drying cylinders – Beneks
• Stenter and stenter accessories, loop ager and relax dryer – EFFE
• Sanforizer (for knits, denims and wovens) and denim finishing lines – Cibitex
• Calendar machines and calendar rolls – Polteks and KWF
• Brushing, raising, shearing and combing machines – Memnun
• Inspection and packing machines – GCM Group
• Nip width and pressure measuring equipments – Nip Control
• Rubber rolls – Regal Rubber and Polteks
• Textile waste recycling – Dell’Orco and Villani
• Nonwoven airlay machinery and end of line solutions – Technoplants
• Dyeing kitchen, printing kitchen, screen engraving machinery – Beneks and Memnun.
Participation at INDIA ITME
India ITME exhibition is important for us, more so specially because an exhibition like this is being held in India after a very long time. It is a good opportunity for us to showcase the new and innovative solutions we have in our portfolio. Basically, we will have at our stand:
• Singeing solution that is capable of replacing bio wash in knit fabrics at 60% reduced cost
• The world’s most energy efficient stenter
• Waterless dyeing solutions
• Continuous ranges that consume up to 40% less water, 35% less space, up to 45% less steam and up to 60% less energy
• Innovative calendaring solutions
• Digital equipment and devices to correctly align every nip including CPB
• Latest bleaching technology which can save up to 92% water and up to 45% steam.
Expectation on Future Growth of Indian Textile Industry
We can confidently say that the India growth story, specifically textiles, is, in fact and is at a tipping point. The current situation in China, Bangladesh, Pakistan and Sri Lanka all point in one direction – when it comes to textiles, India has a chance right now to outgrow and expand exponentially. I think the pandemic period lockdown in 2020 helped traditional dye houses to take a pause, re-evaluate their market strategy and how they would like to lay out the future of their existing and new investments. This thought process combined with a stable government which is inclined to promote growth is opening up opportunities across the entire value chain of textiles and technical textiles.
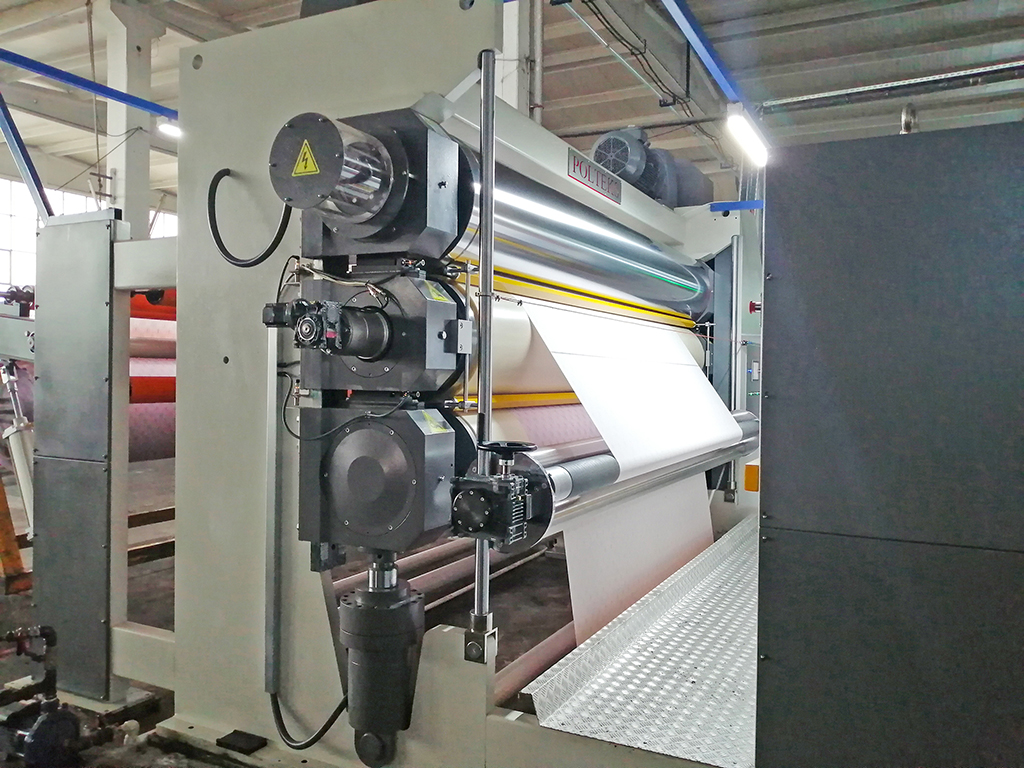
At the same time, fashion brands are becoming more environment conscious and are starting to push manufacturers to adopt a more eco-friendly and sustainable methodology in manufacturing textiles. Those who are going to start today to adopt sustainable technology that promotes lower CO2 emissions and low utilities, are the ones who are going to win and come out stronger. They are the ones who have a chance to earn good margins from their products compared to those who still carry on with traditional methods and machinery. The traditional dye house is now gradually changing and transforming into an agile process with a flexibility to do more with less.
Growth of Manmade and Technical Textiles
I think most of these segments are going to see a considerable growth. But I feel it will be driven mainly by manmade fibres and technical textiles because India is still at a very nascent stage in these two areas. THE GAURS as a solution provider is well positioned to be able to offer the customer more value for his investment if he is ready to discuss with us. We see a lot of traction and trust from our customers in these areas. We have an exhaustive set of solutions and machinery available which offer “something different” than the usual. It is definitely a very interesting and a very exciting space for us. We continue to make a difference to our customer’s life for whoever walks this journey with us.
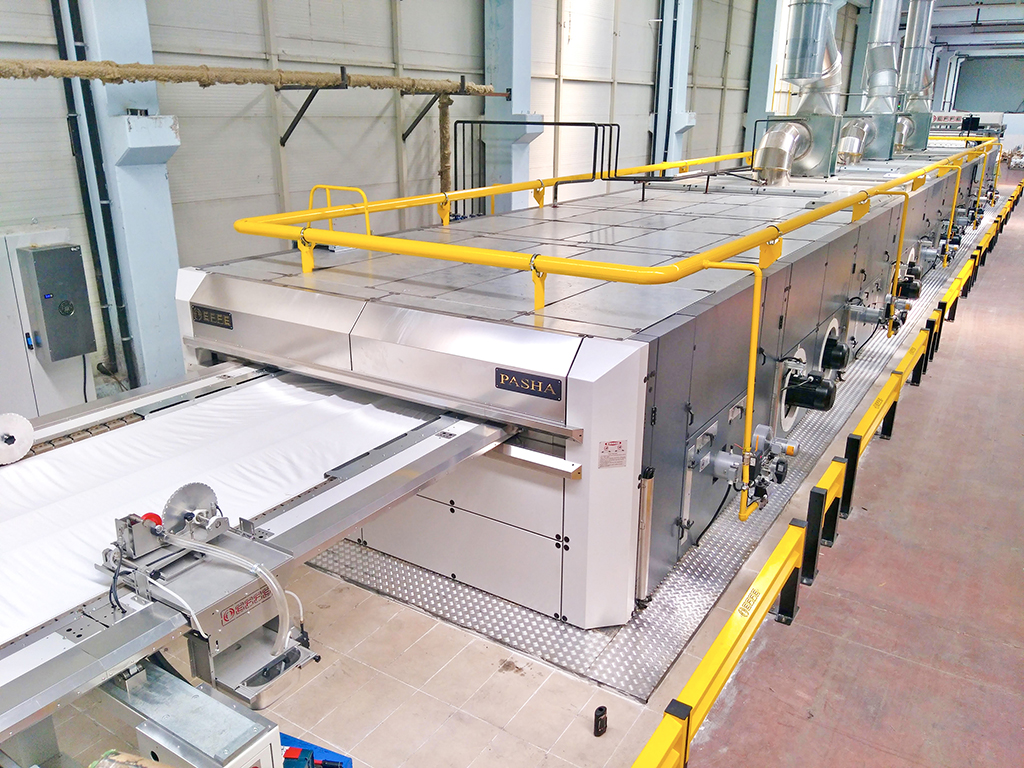
Sustainable Manufacturing Solutions
Most of our solutions are pragmatic, sustainable and futuristic. It can create a significant difference. Some examples:
• Our singe machines eliminate use of bio wash process at fraction of cost. For knit fabric processing it generates a saving 3.5% of weight loss for every kg of fabric.
• Our washing ranges after dyeing help to reduce water consumption by up to 40%, energy consumption by more than 50% and chemical consumptions y up to 40% compared to other traditional washing ranges.
• Our stenter machines use IE4 energy efficient motors (IE4 is the highest energy efficiency rating available worldwide). Most others use IE2 or IE3.
• Our bleaching ranges can help save water by up to 90% and energy by up to 40% compared to traditional ranges.
• We can provide low liquor ratio soft flow dyeing machines with 1:3.5 liquor ratio or even waterless dyeing machines which substantially reduce the dyeing costs.
• We can provide spray finishing machinery which reduce dependency on padders and can save drying costs by up to 40%.
There are many more such things which we can do. Many of our customers are achieving such low consumption values on our machines.
After-Sales Service Support
The pandemic taught everyone many things. Even we learnt and our suppliers learnt. Having worked in the IT industry for many years before venturing into textile machinery, I was very clear in adopting processes which are not people dependent to the extent possible. And it played out very well during the pandemic. Since ours is a process driven organization, and our machines are already internet enabled since many years, we were able to offer remote troubleshooting services. Our principals were also available online and we leveraged online collaboration platforms to assist our customers. Yes, spares were sent physically.
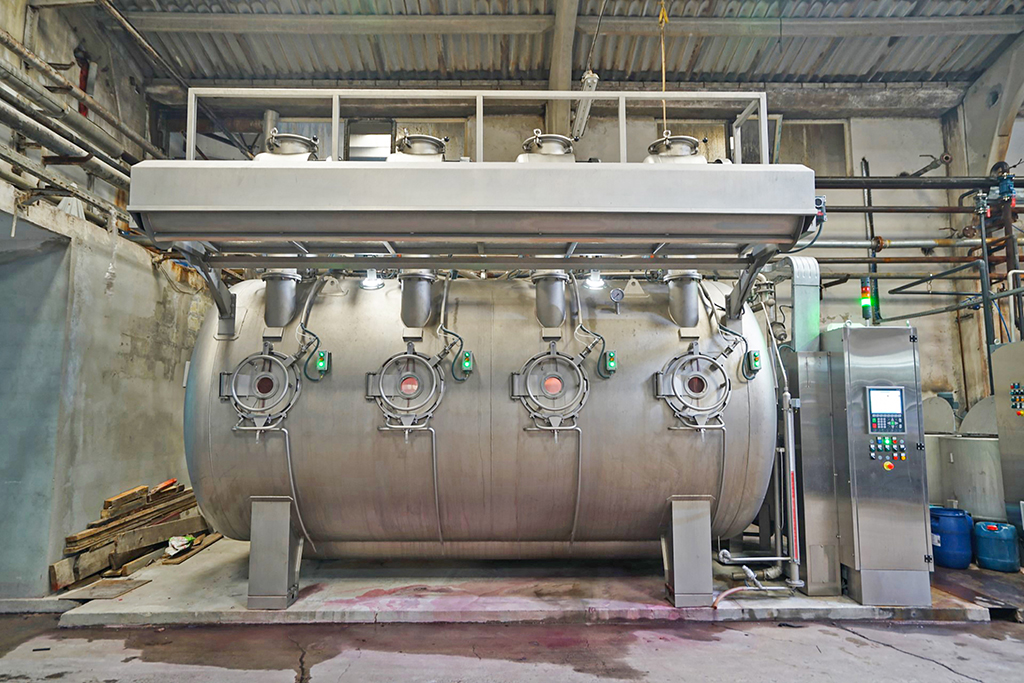
Our customers were very supportive and understanding about the entire situation and that was a major factor that ensured that we could operate smoothly even during the lockdown period.
And that period also taught the customer a very important thing – our machines are designed for low maintenance. Any spare part to be changed is easily accessible. The machine design is not complicated unlike a BMW car engine bay. It is clean, simple, it works without a fuss and delivers great results. So our customers trust in the technology & machinery went up.
Future Growth Plans
THE GAURS is focussed and committed to providing low energy, sustainable and next generation machinery to dye houses. All the principals we represent are technically very strong, have in house research and development centres and are constantly innovating to provide more and more sustainable solutions. We see tremendous potential for the machines we have in our portfolio. With the focus shifting from quantity production to quality production at lower costs, we expect customers to start relooking at their machinery and plant investments and think about how they are going to meet the strict demands of their international fabric buyers. With many of our machines running with customers and showing considerable and measurable results from sustainability perspective, we expect customer interest in such machinery to increase.
Our principals are also equally excited to be a part of the India’s growth story. They see a big potential in this market because they believe that their solutions and technology can really create a positive impact in a country like India. They are investing in disruptive tech and disruptive process methodologies which ultimately is going to benefit a textile machinery buyer immensely. And yes, optimizing the machine’s utilities and energy consumptions is at the core of their thoughts when designing a new product. Globally, the final buyer’s preferences are changing and our principals are aware of this and are innovating at the back end to deliver the results.