Terrot is known worldwide for its production of electronic and mechanic controlled circular knitting machines of top standard. Innovations have a long tradition at Terrot. The year 2017 was very successful and eventful for the company. Terrot was able to demonstrate its strength in major markets and continue growth in sales. The year also marked the 155th anniversary of Terrot.
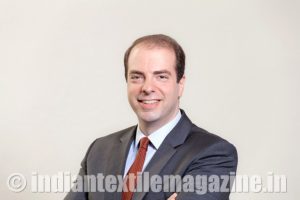
It was against this backdrop that The Textile Magazine had an interview with Mr. Von Bismarck, Managing Partner, Terrot GmbH.
Highlighting the company’s achievements in 2017, Mr. Bismarck said: “2017 was the 155th anniversary of Terrot. We celebrated this special occasion with a significant number of new machine developments which we believe that along our customers will mutually benefit in the future partnerships. A very special present was the first sale and installation of our Corizon technology in Japan which has shown some very good results already and follow up orders are expected in 2018.”
The German circular knitting machine builder has recently opened its new Technology Center in December 2017. The opening of the new centre underlined Terrot’s recent developments and provides its Advisory Department more space for creative ideas.
The Technology Centre is also important for sales events and customer visits, and in the future customers can experience new machine and technology developments before purchase. With a strong demand for machine and product presentations, the centre has a specific showroom for Terrot and Pilotelli machines. “We will use the Technology Center for external and internal sales and training events and give our customers an opportunity to get to know our products in detail. We invite all our customers to also make knitting trials and developments here together”, said Mr. Bismarck.
Commenting on Terrot’s major innovations and product launches in 2017, Mr. Bismarck said it was a year of significant innovations in its product portfolio. The most important innovation in the electronic portfolio was the UCC 572 ME3, which is the world’s most productive mattress machine with double electronics in cylinder and dial. This machine has 100 feeders and a speed factor of 720. No machine in the world comes even close to the flexibility and productivity of this one. Furthermore the company started development of the UCC 572 TRE3 which could be the most productive machine for shoe upper material. This machine has 2.4 feeds per inch and can produce transfer and relief technology structures with double electronic selection. Last but not the least in the jacquard portfolio, the company has developed the world’s finest transfer machine UCC 572-T with 24E gauge in cylinder and dial.
In its standard machine program, Terrot modernized its 8-lock portfolio with the two models I3P 196 and I3P 584. Based on the world’s best knowledge in double jersey these machines have a very wide range of possible structures and, for example, the possibility to have elastic fabrics with long delay timing. In the single jersey segment of Pilotelli brand, Terrot has developed the J-4.0-V model, with a speed factor of 1750 and 4 feeders per inch.
With the manufacturing sector moving towards Industry 4.0, Terrot’s strategy is not only to integrate automation features into the products but to expand digitalization to all its business processes in the whole group.
Indian market
Answering a question on his company’s performance in the Indian market and its growth potential, Mr. Bismarck said: “We performed well in the Indian market last year and could defend our market position. Over the past years we were able to introduce successfully our sinkerless single jersey machine from our Pilotelli brand into the Indian market. This model has its specific strength by decreasing maintenance cost, cleaning significantly and avoiding vertical lines caused by sinkers. We intend to increase our footprint in India with this machine model. We also see future potential for increasing our business not only in the cotton-based applications, but also with good solutions with the upcoming demand in knit synthetic fibers.”
As for its major global markets, Terrot has been performing very well in Turkey, India and Bangladesh which occupy the top 3 positions in 2017. This year the company has plans to increase its market presence in these areas as well as others with the help of its high performance machines.
Energy efficiency
Terrot contributes significantly towards global green footprint by increasing productivity without using high energy consumption components in the machines which have very low power consumption. Care is taken to select machine components that consume least energy. For instance, lighting on all Terrot machines has been changed to LED.
Lack of skilled manpower is one of the major issues faced by textile industries which lead to machinery manufacturers increasing the level of automation in machines. Terrot has been continuously working on its mechanical and electronical components. In terms of automation the company has already integrated a weighing device for the fabrics rolls into its machines as an option on request.