Indian operations to play an important role in future growth
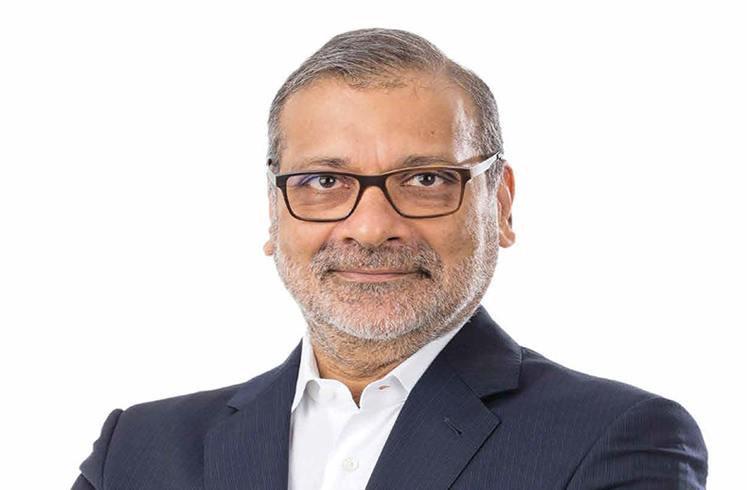
The Teejay Group is one of the largest knit fabric mills in South Asia specializing in weft knit manufacturing. The company has facilities located in Sri Lanka and India and a state-of-the-art printing facility in Sri Lanka. Teejay Group crossed the USD 250 Million in FY 22 for the first time in its history which reflects its visionary leadership and operational excellence.
Teejay is accepted as the sole multinational mill to originate in Sri Lanka. The Group gained popularity due to its wide range of products and services offered in relation to weft knit manufacturing that includes dying, finishing, and printing – recently expanded to accommodate lace dying, yarn dying, and synthetic fabric production.
Teejay’s fabric portfolio is inclusive of; Single Jersey, Interlock, Rib and Pique ranges where leading global brands use the fabrics to manufacture intimates, sleepwear, lingerie, and active wear, and so on. However, Teejay aspires to branch out from traditional means to discover new sophisticated approaches to manufacture fabrics more attuned to the emerging trends and global perceptions.
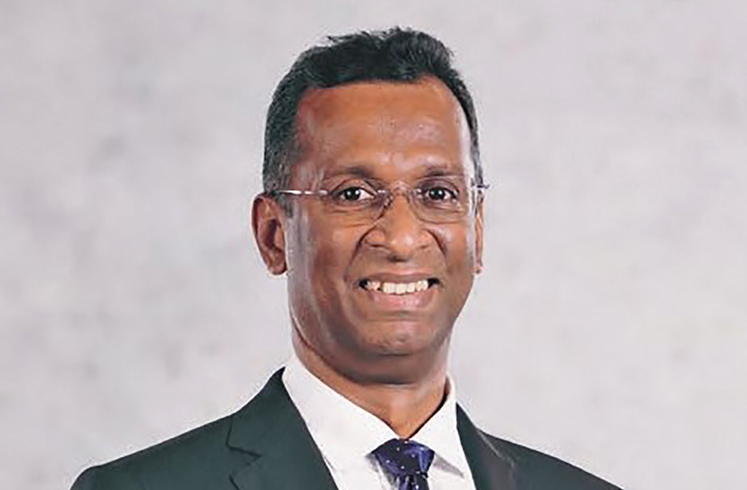
Understanding the vitality of transforming and reinventing business practices, the company assigned Sustainability, Innovation, and Synthetic as key pillars of growth for the upcoming years. Progress has been made in these aspects – indicated by the recent inclusion of digital printing, lace, and technical synthetic production into the Group’s portfolio.
Teejay’s progressive attitude enabled the brand to grow amongst European, American, and Asian markets whilst positioning it as a preferred fabric provider for leading retail brands such as PVH, Calzedonia, L Brands, Decathlon, Marks & Spencer, Nike, Uniqlo, and LIDL among others.
Focus on Synthetics
Teejay Group is making a determined bid to attract a major portion of the synthetic business currently dominated by Taiwan, Thailand, Vietnam and China. The global market forecasted for synthetic fabrics is over USD 85 Billion by 2025. The synthetic manufacturing capacities in Teejay India and Teejay Sri Lanka combined will deliver benefits going ahead with full capacity utilization.

The Group’s thrust into synthetics with the USD 26 Mn investment in enhancing capacity at Teejay India will add 20 additional tons of daily capacity and will prove to be another critical factor in its future success. Teejay has committed to invest on transforming existing business operations and duly added 5 tons of daily capacity in synthetic Teejay Lanka whilst further entering into an outsourcing partnership. The aim is to enhance the synthetic production capacity for the Group overall from 5% to 20% in the medium term. The Teejay India expansion project will come on stream in September 2022 and further strengthen its transformation journey.
Furthermore, the capability of Teejay Prints too was further expanded by investing in a dispersed printing, jacquard printing, fleece technology and a lacer engraving machine which will yield results in the next financial year.
The aim to move up the value chain with high-end products is being driven by Teejay’s Inscope initiative through product transformation strategy. Modernisation will be an ongoing effort to improve productivity by investing in state-of-the-art machinery which uses fewer resources. The future is undoubtedly digital and Teejay will continue to improve IT infrastructure to align with digital transformation, becoming the first company in Sri Lanka to implement SAP S4 Hana on Google Cloud. Eventually, the Group intends to integrate all companies onto an ERP system with a significant number of processes automated.
The Group’s ambition is to reach net zero global emission by 2050 and also to contribute to the industrial drive to limit global warming by 1.5°C by 2030. We are proud of the fact that Teejay Lanka has achieved 81% reduction in greenhouse gas emissions by investing in a LKR 90 million, worth steam powered paddle dryer which is largest in the country.
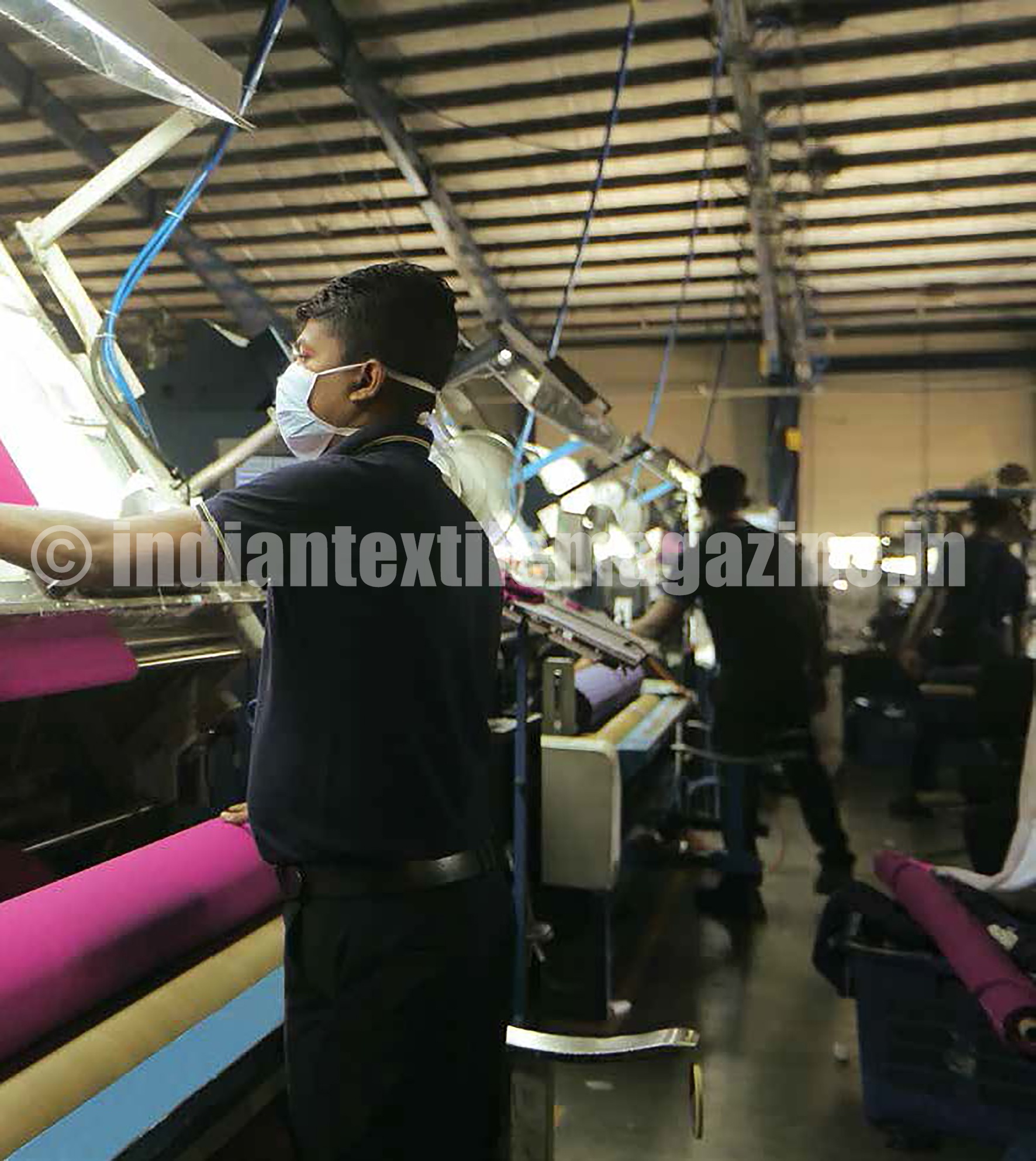
Teejay Prints
Modernization efforts were made on behalf of Teejay Prints to uplift its capabilities by acquiring new machinery with low energy and water consumption potential while deriving a considerable level of output. Prints were able to increase its capacity and its product portfolio this financial year. The capability to perform reactive printing was a new introduction to the Teejay Group during the period under consideration.
Teejay Prints – Digital printing unit
Reactive printing was commenced and that has improved the position of Teejay Prints and expanded its product portfolio. This new capability offers more value addition in the area of pigment printing and has reported positive customer feedback since its introduction. It can be taken as a key performance indicator, and a crucial component in the company’s success story as its expertise in reactive and digital printing continue to improve with each passing year.
Teejay India
Teejay India is located in the Brandix India Apparel City, a Special Economic Zone with 100 per cent export-oriented units involved in the integrated apparel supply chain at Visakhapatnam, Andhra Pradesh. As an apparel hub in nature, India can leverage on its advantage gleaned by its close proximity to other booming apparel hubs such as Indonesia, Bangladesh, and Vietnam to source raw materials. The recently concluded expansion of Teejay India placed it in a prime position to achieve the group’s target of earning $300Mn and has positioned it as a leader in the global textile manufacturing market.
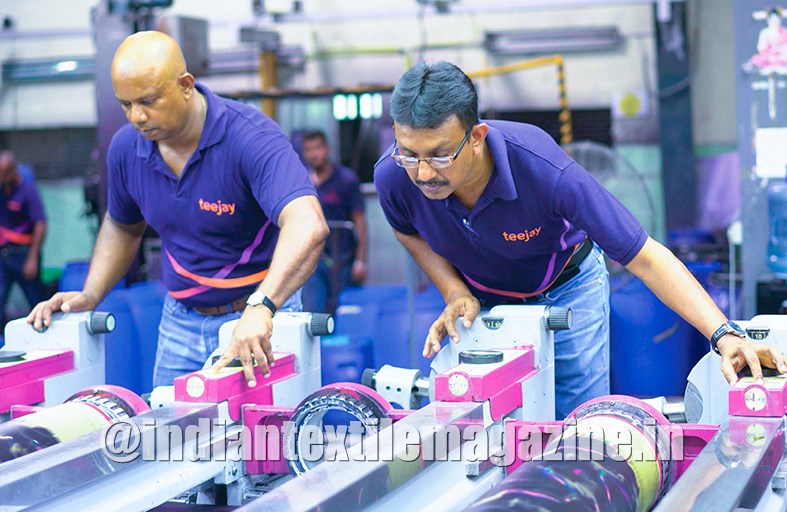
Digitization
The factory expansion and modernization of machinery is a vital pillar in Teejay’s operational excellence journey. A massive information gathering exercise was conducted to examine the causes for downtime and automate the monitoring of data using a real-time digital assessment tool to coincide with this endeavour. A control room was set up to monitor the digital data of individual operation units – enabling individuals to mitigate or resolve any grievance on the spot. It is an exercise that enabled the group to witness a 15% increase in efficiency over two years.
The team will be granted greater visibility to view functions in real-time with a direct link to a SAP system once the digitalisation process of all shop floors are completed. Moreover, it can contribute towards the streamlining of operations. Other benefits include; improvement in efficiency, optimal consumption of raw materials, and the reduction of wastage. The inspection and storage units were expanded to accommodate more capacity.