Taiwan’s textile industry is attracting more and more international attention. Global brands such as Nike, Adidas, Uniqlo, etc. use functional fabrics from Taiwan, 70% of the international market, which makes the country one of the best textile manufacture suppliers in the world. With the talent, experience and the healthy relationship with big global manufacturers, there’s a big effort in Taiwan’s textile machinery supply chain. According to statistics from Taiwan Association of Machinery Industry (TAMI), the export value of textile machinery from January to December 2018 was 1.02 billion US dollars, which was up nearly 1% from last year.
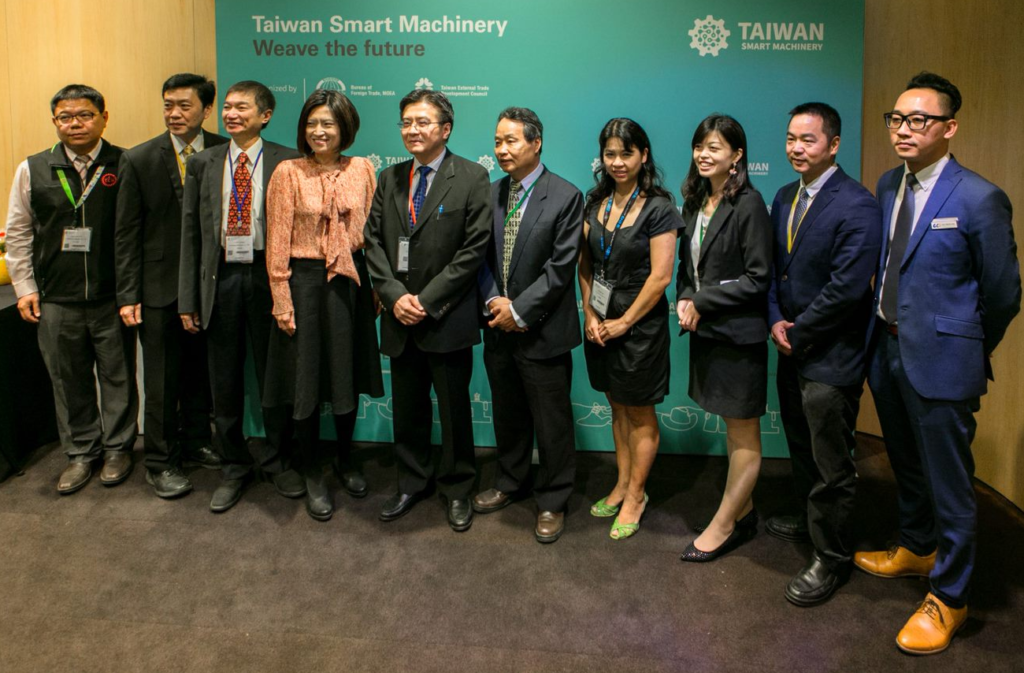
In this context, seven Taiwanese textile companies with TAITRA (Taiwan External Trade Development Council), have showcased their intelligent/smart textile machinery and innovative solutions at ITMA 2019, in a press conference attended by numerous medias, both technological and economic. Companies such as Pai Lung, Logic Art, AK Dyeing, ACME, CCI Tech, Tai Ho Shing and Taiwan Giu Chun have presented their state-of-the-art innovations and technological advances related to smart machinery solutions for the world textile industry.
As Jenny Tsai, Director of TAITRA Barcelona office, says: “In Taiwan’s textile industry, the upper, middle and downstream of the industry chain is working hard to transform itself, actively pursuing a refined and differentiated layout, and gradually paving new roads. Industry 4.0 flipped the manufacturing industry, allowing small enterprises to rely on smart machines’ software and hardware integration to build their brand features”.
Here are some of the Taiwanese innovations that are presented at ITMA 2019.
Pai Lung
Based on industry 4.0, Pai Lung presented the MES solution to achieve cost-reduction and become smart factory. With POMS, which is a command center that can give orders to all machines to achieve production target, and KFMS (Knitting Fabric Management System), a complete database to help customer to realize Datamation, Pai Lung provides perfect repetition on fabrics with error rate less than 1%. Brian Lan, Pai Lung Assistant Vice President, explains that “MES is a system designed to assist corporations to collect and monitor production data during the manufacturing process from order placing, production inception, and process control to product output”.
Logic Art
Logic Art presented at ITMA 2019 the LA-210 machine, an innovation for dye house intelligent integration, allowing automated production centered in product development, brand creation and facilities improvement. This production starts with an intelligent system with signal control, then continues with the data process until the production integration, including big data analysis and the intelligent automation, doing operative control. LA-210 gives dye houses unparalleled accuracy and reliability for dye stuff weighing, especially when it’s combined with Logic Art automatic dye dissolving and distribution, automatic chemical distribution and dye house supervisory software. Steven Shen, Logic Art Managing Director, says: “LA-210, the automatic dyestuff weighing system is a fast and convenient method of dyestuff refill that can eliminate human weighing errors, providing a total solution essential for the modern dye house”.
AK Dyeing
AK Dyeing presented AK-DSL 2018 machine, which has washing-smart wash system and hybrid technology to reduce 30-40% wastewater discharge. Sensor (steam, water, electric consumption, machine run speed, chemical injection rate, Fabric run speed) are all embedded in the machine to provide digital operation data. All the operational data collected through the sensors can be stored in the Industrial PC provided and connect to the Dyehouse’s Central Management System. The machine’s smart wash system is able to monitor and control the fabric washing function in real-time. This will provide the ability to avoid the problem of over-washing the fabric and waste unnecessary water.
Steven Lin, AK Dyeing, General Manager adds “The machine retains the ability for wide range application of synthetic fabric. It is able to satisfy the stringent quality requirement of branded company need for light weight, high quality, highly functional fabric.”
ACME
During the press conference, ACME exhibited AM-ICD, a smart machine that reduces the necessary evil of the conventional dyeing machine with 65% water reduced, 65% pollution reduced, and 65% chemical, energy and power saved. It works with a conveyer drive system and it only needs water for pipe circulation and fabric pick up with and extreme low and uni-liquor ratio: 1:2.5~3.5. “Reducing the liquor ratio of dyeing machines has become the highest target for manufactures, because the textile dyeing industry is not only one of the biggest consumers of water and energy but also the biggest producer of pollution”, said Ms. Ya-Chen Chang, Marketing Manager.
CCI Tech
CCI Tech is the only one that is fully committed to sampling solutions for varied weaving application. CCI’s automated sampling solution only requires as minimum as 1 bobbin to complete the whole process from sizing, warping to weaving. And the lead time for making a sample fabric, can be easily shortened from few weeks to just a few hours. According to the different customers, CCI presented two major solutions: “IN THE STUDIO” and “ON THE LOOM”. The first one is specially designed for small factories and research centers. In this solution, customers are able to produce a width of 500mm or 900mm, and a length from 3.6m to 30m sample fabric in a very short time. “ON THE LOOM” is focusing on preparation process of sizing and warping, to manage your full-width sample and small volume order effortlessly with advantages of extreme space efficiency and lowest operation cost. “We believe that through our complete automated sampling solutions, customers can create more new business opportunities and a faster market response to different sorts of sample development, and enhance their competitiveness in the market.”, said Andy Yueh, CCI Tech sales manager.
Tai Ho Shing (THS)
Tai Ho Shing (THS) exhibited Rosso Method, an automatic linker machine that essentially joins the two open ends of the open sock together. This method reduces the traditional three steps hand linking into only one step. In addition, reduces 30-50% of the total production time and it has high productivity in socks manufacturing because it can produce wide variety of socks with the same machine. Sensors are installed throughout the machine to collect digital data and to provide safety during operation. Fernanda Lin, THS, Marketing Manager explains that “We provide real time information collection on every machine that feeds back to the plant central PC or company network. Data includes daily or shift machine productivity collection, stop times, alarms, error messages, yarn breakage”.
Taiwan Giu Chun (T.C.H)
Taiwan Giu Chun (T.C.H) presented two exhibition machines to develop crochet knitting: double bed warp knitting and cord knitting. The first one produces lateral contraction garment flexible tapes, with high production, saving space and less maintenance. Instead, the cord knitting machine produces shoelace, ropes, glassed string and decorative cords with flat, round, triangle or quadrilateral shape. Vincent Tsai, T.C.H, Managing Director said that: “The technology that T.C.H provides saves space and improves production. We are specialized in crochet develop, and we know that the style, time production and quality products are really important for our sector”.