Known for its quality and innovative products, the company has a total of 14 plants across India in which four factories manufacture nonwoven fabrics and the other 10 manufacture automotive interior trim components
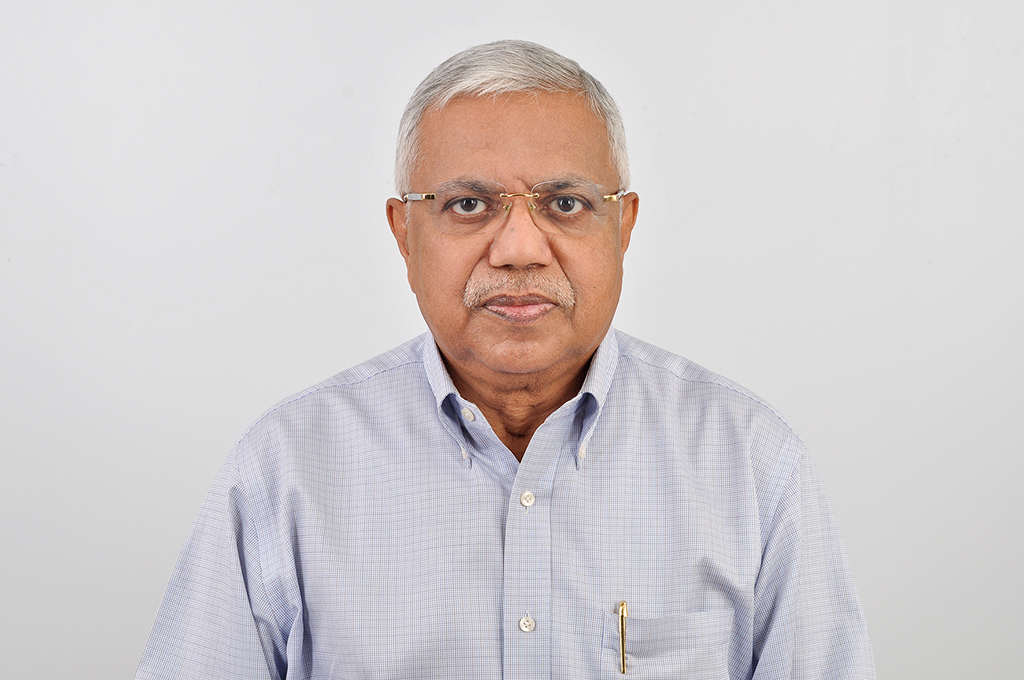
The next time you get into your car, spare a minute to observe the interiors. There is a marked improvement in the quality and finish of automotive interiors in the last couple of decades, more particularly the noise, vibration and harshness (NVH) levels. Automobiles are much more sophisticated and quieter in the inside. This generation shift in technology is thanks to the extensive use of nonwoven material. Thinking of nonwovens fabrics and automobile interiors trims, the first name that one would recollect is Supreme Nonwoven Industries and Supreme Treon.
Just like the tagline ‘Intel Inside Every Computer’, there is a ‘Supreme Inside Every Automobile’. And automobile is one of the many industries in which the company operates. Supreme Nonwoven Industries was started in 1986-87 by Mohan Kavrie, a graduate from IIT Mumbai. The company, a part of the Supreme Group, is considered the largest and most diversified nonwovens’ producer in India. Supreme Treon (P) Limited is a group company, which manufactures automotive interiors and NVH components.
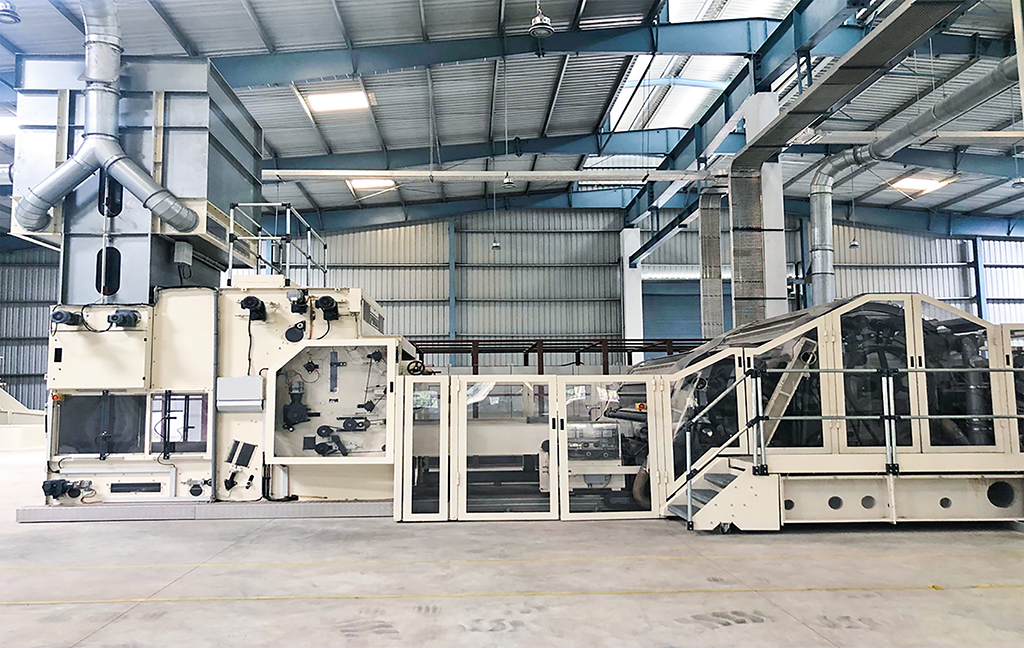
Focus on Innovation
Supreme Nonwoven Industries has always been known for its focus on innovation. Elaborates Mohan Kavrie, Chairman, Supreme Nonwoven Industries: “Innovation is the key to development of new products and applications. This has been and is our strength. We are a clear leader in India in both the segments that we operate. All the leading companies in both the automotive and other industries are our customers.” He further informs that the group has a total of 14 plants across India. While four factories manufacture nonwoven fabrics, the other 10 manufacture automotive interior components. The group clocks a turnover of Rs 1,000 crore with steady growth and expansion year-on-year.
Products and Solutions
Getting into the details of products and solutions offered by Supreme Nonwoven Industries, Kavrie states, “We have facilities using all the standard nonwoven technologies that start with staple fibres. Nonwovens essentially have two basic stages: fibre opening and making of a web or batt and the bonding stage where the fibres in the web or batt are bonded to make a nonwoven fabric. We use all web or batt forming processes i.e. direct web, X-laid webs and air-laid webs. The nonwoven fabric bonding technologies are basically mechanical, chemical and thermal. A nonwoven gets its name from the bonding technology used and not the process used for making the web or batt.”
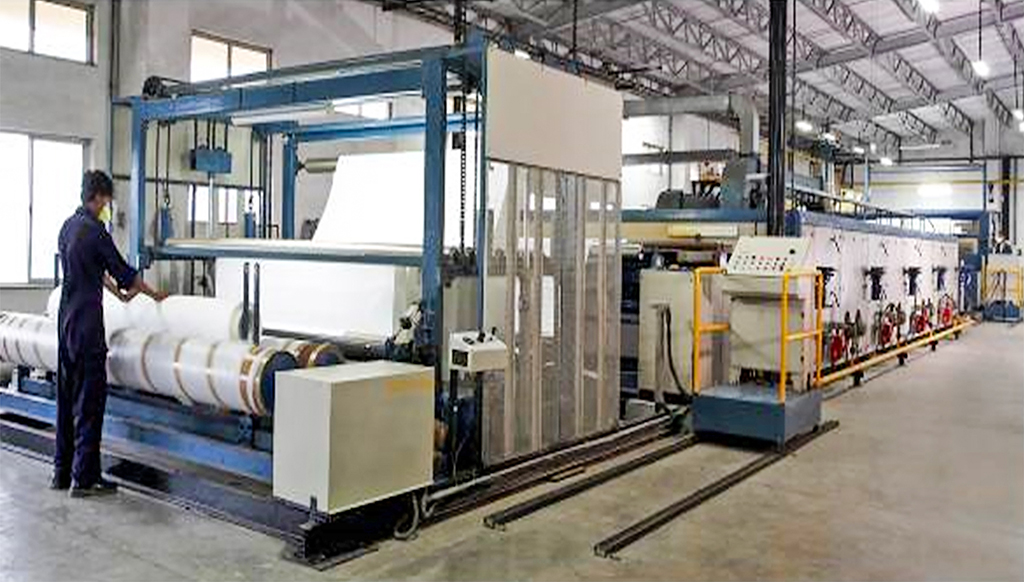
“In addition to the manufacture and marketing of nonwoven fabrics, a significant part of our production is primarily used for manufacturing moulded automotive interior components such as carpets, head-liners, NVH insulations, parcel trays, etc. These are supplied to the automotive OEMs, both passenger and commercial vehicles. This company’s name is Supreme Treon. We are suppliers to nearly all the OEMs in India,” Kavrie states. “At both Supreme Nonwoven Industries and Supreme Treon we are engaged in the continuous improvement of our processes to enhance the quality of our products and ensure cost-competitiveness,” he adds.
Manufacturing Infrastructure
As mentioned earlier, Supreme Nonwoven Industries has a total of 14 plants across India for nonwoven fabrics and automotive interior components. As regards any new investments by the group in recent times, Kavrie replies: “We have started operations in Thailand in 2020 and have set up two factories for manufacture and supply of automotive interior components near Bangkok. In addition, we have two new greenfield projects. The first one is at Anantpur in Andhra Pradesh which will commence commercial production in January 2022 and the second one is at Jamshedpur that will start in the first quarter of 2022-23. Both are for automotive interior components. The capacities of existing factories keep getting added or upgraded on a regular basis to match increasing demand.”
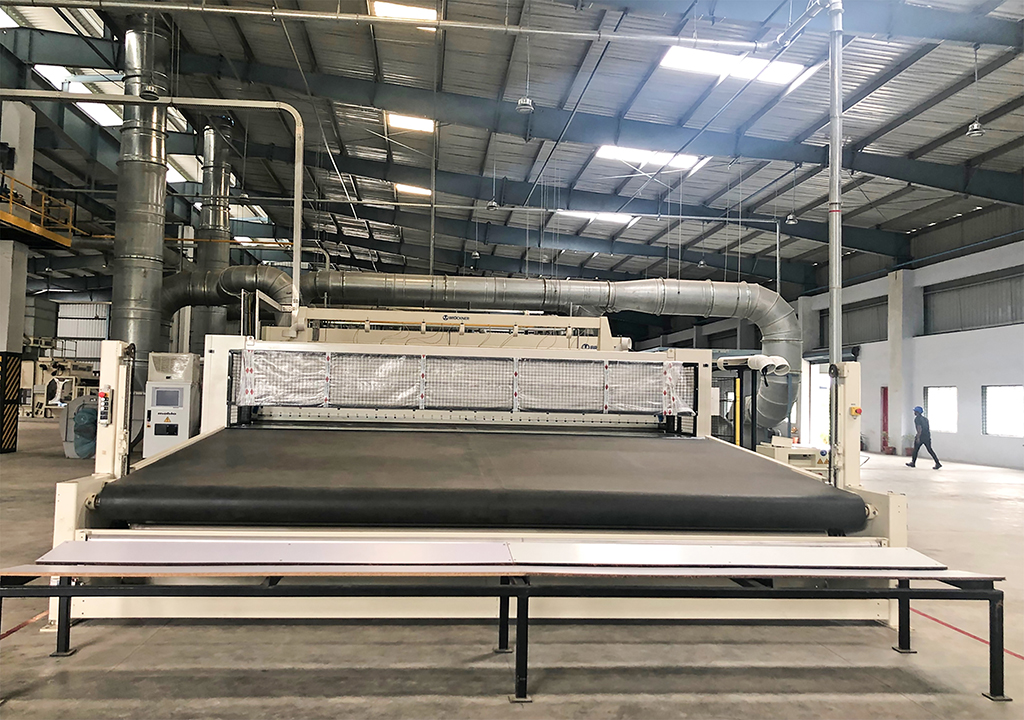
Competitive Edge
Speaking about the advantages offered by Supreme Nonwoven Industries and the key reasons that make it stand apart from the crowd, Kavrie observes: “We consider our customers and suppliers as our partners. We believe in long-term relations and continuously get new business on account of our ability to develop and supply tailor-made products. Our policy is of giving total satisfaction by providing the right product at the right price and the right quantity at the right time. Quality is a given.” In the automotive segment, Supreme Treon is a supplier of choice to practically all the major automotive OEMs and enjoys around 50% market share.
Nearly all the Automobile OEM’s, both Passenger and Commercial vehicle manufacturers are customers of the company. In addition to Nonwovens manufactured for full range of standard applications, the Company is particularly appreciated for its products for all types of Filtration and Garment Interlinings. Finally, sharing the company’s growth plans and vision for 2025 and beyond, Kavrie confidently states: “We are leaders in our business and are committed to remain as leaders. The future belongs to India and we will be part of that story. Modern infrastructure and technologies further augment Supreme Group’s philosophy of creative partnering and this provides all collaborators optimal outcome in managing their functional and portfolio needs.”
—
Nonwoven Fabric Bonding Technologies
1. Mechanical Technologies: Needle punching, hydro-entanglement, stitch bonding and V-lap.
2. Chemical Bonding Technologies: Wet process by application of binder – usually lightweight nonwovens and dry process through the use of bonding resins such as phenolic resin or polyester resin powders – usually high GSM and thickness.
3. Thermal Bonding Technologies: Thermal bonding using a calendaring process – lightweight fabrics. Hot air bonding – usually high GSM and thickness.