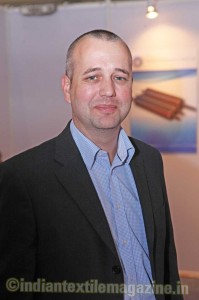
Stewart Pinned Products Ltd. of the UK, a global leader in the manufacture of components for textile machinery, has recently set up a manufacturing plant in Bangalore to cater to the Indian market. Started in 2013, the Indian entity, Stewart Pinned Products Private Ltd., is a full production facility owned and operated by Stewart Pinned Products in Scotland.
The new Indian plant, located at Bommassandra, Bangalore, is dedicated to the supply of the full range of pinned products to all Indian customers.
Stewart has been manufacturing textile-pinned products for over 140 years and is a world leader in the textile industry. Founded in 1874 to manufacture and repair hackles and staves for the Jute Hemp and Flax industry, its present production emphasis is on pinned products whose base material is light aluminium alloy instead of the more traditional beechwood or brass. This not only reduces weight but also gives significant advantages in terms of strength and product life.
With over 140 years of experience in design innovation in many different industries, Stewart remains a preferred supplier to all major machinery manufacturers and exports to over 50 countries. The company is focussed on providing the highest quality pinned products direct to the Indian market.
Mr. Michael White, Director, Stewart Pinned Products, says: “We have established the Indian plant mainly to cater to the demand from customers in the domestic market. In India, many of our customers have been requesting for refurbishment services which we have not been able to offer so far. Now with the local presence, we will be able to offer refurbishment services and component which would be manufactured locally”.
The company manufactures pinned products for the blowroom and carding machines and supplies as an OE to most of the leading global machinery manufacturers. In India, Stewart has been working with LMW since last 20 years and has been catering to most of its requirement.
“We want to expand our business in India as earlier, with high import duties and freight cost, we were not very competitive. Now, with local manufacturing, we can offer the customer our products and service at a much more competitive cost”, says Mr. White.
With the setting up of the Indian plant, the complete product design, development and production can now be undertaken locally. Stewart is also ideally located to offer full refurbishment and repair service to local customers.
Stewart designs and manufactures most models and variants of pinned components within textile machinery and has improved the life span and the production process of those pinned components.
Pinned products are more reliable and a better alternative to wired products. Pinned products cause less damage to fibres. They have a longer life span than wired products.
Mr. White says: “We have launched a product which is quite new to the Indian market. As an alternative to the traditional wired product, we have launched the pinned stationary carding flats. This has better life, 3 times that of wired products, and enhances the overall design, quality, accuracy and alignment of the product. We are just promoting this in the Indian market and it will be available in the full range and in the full densities”.
Although Stewart caters to many industries globally, the Bangalore plant will focus mainly on products for the textile industry. “We do the complete manufacturing of our products here through a fully equipped machine shop. At the moment we are importing most of the raw materials, but we are actively looking to source them locally”, he reveals.
Stewart is also a major supplier of pinned products to global brands like Rieter, Marzoli, Crosrol and others. The company has a manufacturing facility in Scotland and China and supplies to all major manufacturers globally.
For Stewart, the aftermarket is or the refurbishment market is equally important. “As we now have a local presence we can take the customer’s old rollers, refurbish and repair them, fit the new pins and supply it in a form which are as good as the new rollers”, adds Mr. White.
Stewart is clearly the global leader in this segment when it comes to high quality, high performance pinned products. It is considered the Rolls Royce standard in the textile industry.
Stewart has capacity to produce 500 rollers per month. The focus is to cater to the requirement in the domestic market and look at export later.