InspirOn Engineering, a reputed name in the Indian textile fraternity, is engaged in manufacturing stenter machines for many years. The company has manufactured and sold a sizable number of machines in the Indian market under its flagship brand ‘Motex’. With the success of Motex machines within India, the company has decided to take on the Asian market with the launch of its very own technology, SprinOn Stenter.
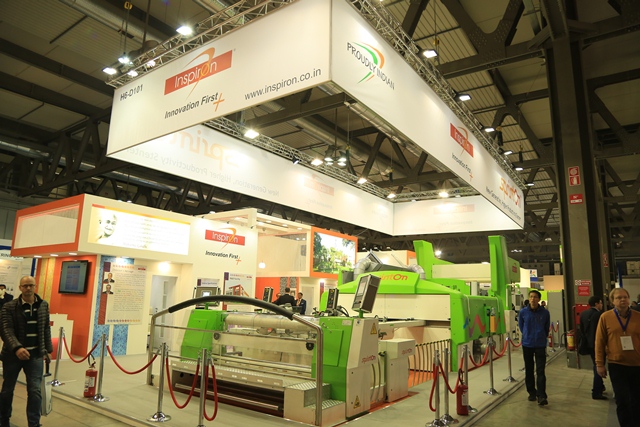
InspirOn presented its all-new SprintOn Stenter for the first time to the international audience at ITMA.
Inspiron Engineering has modern manufacturing facilities equipped with ultra-modern CNC machines and state-of-the-art production set up in Ahmedabad. The machines from the company conform to global environmental standards.
Mr. Prakash Bhagwati, InspirOn Chairman, said: “We want to consolidate and extend our position in the market by achieving sustainable satisfaction of our customers. We distinguish ourselves from our competitors by offering our customers the best technical solution for optimum cost-effectiveness. Our machines are technically and in all other aspects comparable to those manufactured the world over.”
The entire group is very efficiently and professionally managed by highly qualified engineers. Manufacturing facilities are efficiently run by qualified technical personnel and a highly skilled workforce.
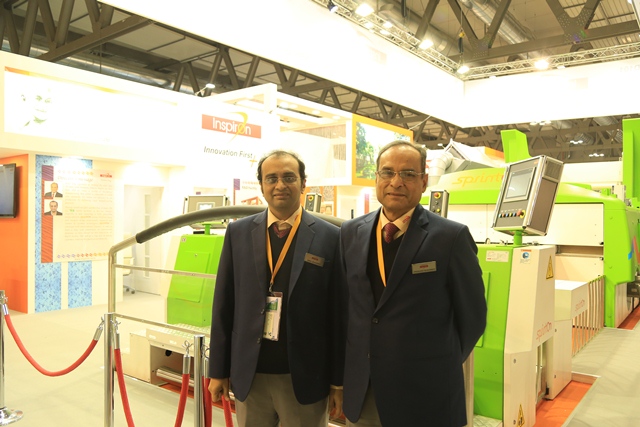
A dedicated R&D team of technocrats is continuously involved in improving and updating technologies in the product range and development of new product lines. This highly experienced team provides excellent support, from supervising, installing, erecting & commissioning of the machines supplied as well as prompt after-sales service.
Headquartered in Ahmedabad, the company has been involved in engineering activities for decades. InspirOn has exclusively developed technology that enables new SprintOn Stenter to achieve upto 15 per cent higher drying efficiency than Motex. Additionally, it has developed a new transport mechanism within the machine which consumes much less energy.
SprintOn nozzles are better designed compared to Motex nozzles, ensuring that more hot air is blown onto the fabric without consuming any extra energy. The nozzle design is unique, and InspirOn has applied for its patent.
SprintOn has further developed a new set of tracks wherein the chains move with much less friction. They are redesigned to make them lighter in weight and yet stronger to withstand the tension. Hence, electrical energy to move the chains is less due to lower friction. The graphic user interface (GUI) with regard to machine controls is redesigned to make it more user-friendly.
The R&D work applied to all line components, starting with material savings, less energy consumption, increased production, higher efficiency and availability, improved ease of operation, reduction of downtime for maintenance, service and cleaning and remote access.
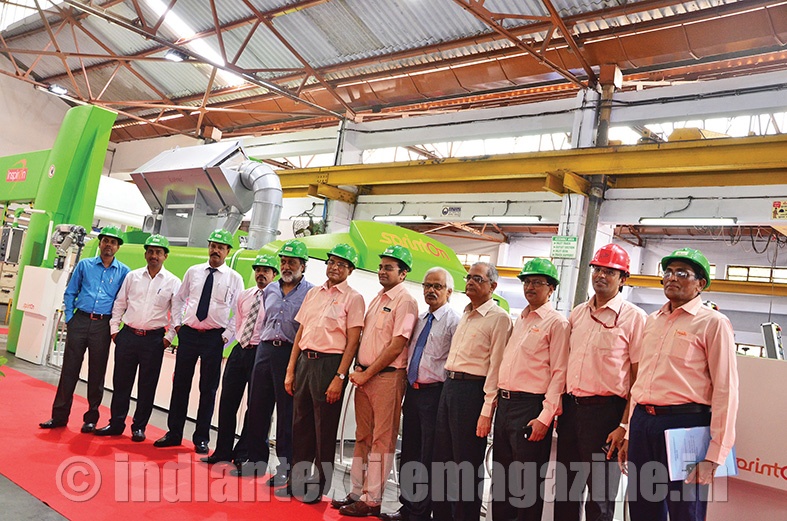
Visitors to the trade fair can witness the impressive performance of the SprintOn machine, which was developed in-house through dedicated engineers using the best design softwares. All relevant standards were revised in collaboration with research centers to adapt the machine’s construction, its ergonomics and its functionality to the special textile finishing requirements.