By Arun Rao
Spray Engineering Devices Ltd, based in Chandigarh, has emerged as a pioneer in sustainable thermal sciences. The company has made significant strides in reducing utility costs for its customers, particularly in the textile industry, by focusing on energy-efficient, eco-friendly alternatives to traditional processes. Their efforts to eliminate or reduce fossil fuel consumption are helping businesses move towards more sustainable practices, which is critical in today’s environmentally conscious industrial landscape.
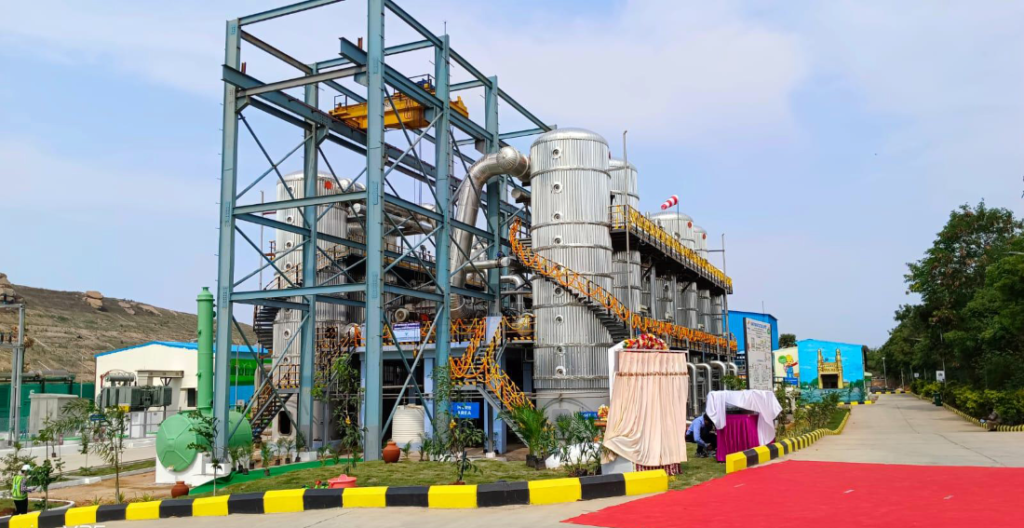
Mr. Vimarsh Verma, the Head of Water Division at Spray Engineering, elaborated on the company’s approach: “Our goal is to cut down on fossil fuel consumption and offer solutions that are both economically and environmentally sound. We are transforming the way textile mills handle their effluent treatment processes.”
Boiler-Free Technology Cuts Operating Costs and Reduces Fossil Fuel Dependency
One of the company’s most notable innovations is the introduction of its low temperature evaporator based on Mechanical Vapour Recompression (MVR) Evaporators, which have eliminated the need for boilers. Traditionally, textile mills rely on large boilers to generate steam for various wastewater treatment processes, often resulting in high fuel consumption and operational costs. Spray Engineering’s MVR evaporators run on electricity, significantly lowering the overall energy consumption.
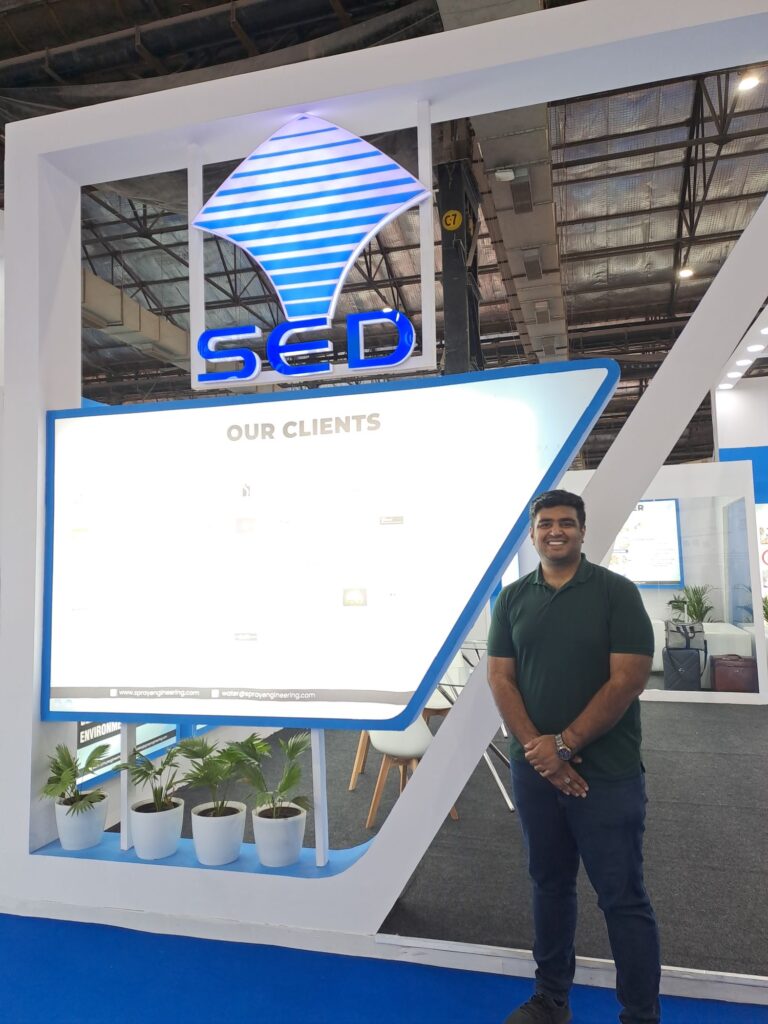
Mr. Verma explained, “We’ve found that by removing the boiler entirely, our systems operate at an incredibly low cost, sometimes as low as Rs 0.12 to 0.15 per liter of effluent treated water. This change is revolutionary for textile mills, as it not only reduces fossil fuel dependency but also leads to significant savings in both operational costs and energy consumption.”
Furthermore, Spray Engineering’s low temperature evaporators help recover water at temperatures around 60-65°C, which is beneficial for textile mills that require hot water for dyeing or finishing processes. This recovered water is of exceptional quality, with a total dissolved solids (TDS) count of just 50-100, making it even better than potable water. This reduces the need for mills to invest in expensive pre-heating systems, further improving cost-efficiency.
Maximizing Water Recycling and Resource Recovery
In terms of water recycling, Spray Engineering’s solutions excel in achieving Zero Liquid Discharge (ZLD) with minimal pre-treatment. Traditional ETPs involve multiple stages like collection, filtration, biological treatment, reverse osmosis, and evaporation, which can be costly and energy-intensive. Spray Engineering simplifies this process by removing suspended salts and adjusting the pH in a single step before directly passing the water into the evaporator.
“Spray Engineering’s evaporators offer a highly efficient solution that not only recovers reusable water but also recovers salts like sodium chloride, Glauber’s Salt, etc which can be reused. This makes the capital investment in a ZLD plant recoverable at an accelerated rate,” Mr. Verma added. The ability to recover 95% of salts further enhances the sustainability of textile mill operations, providing both environmental and economic benefits.
Comprehensive Support and Training for Sustainable Operations
Spray Engineering’s commitment to sustainability extends beyond providing cutting-edge technology. The company actively partners with its customers to ensure the long-term success of their effluent treatment processes. The company offers extensive support, including training programs for operators and technical teams.
“We invite our customers’ technical teams to our facilities for regular training sessions. This not only empowers them to resolve common mechanical issues on their own but also reduces the dependency on our service engineers,” Mr. Verma noted.
Additionally, all of Spray Engineering’s installations are remotely monitored, allowing the company’s service engineers to resolve most issues without needing to visit the site. This further streamlines operations, saving both time and resources.
Challenges in Treating Complex Effluents and Tailored Solutions
Mr. Verma pointed out that the effluents from textile dyestuff and intermediate industries can be particularly tricky to treat. However, treating effluents from other industries, such as Active Pharmaceutical Ingredient (API) manufacturers or even Common Effluent Treatment Plants (CETP’s) is even more challenging, In spite of these challenges Spray Engineering has provided working solutions to these industries as well.
A Robust R&D Ecosystem Driving Innovation and Patented Technologies
Spray Engineering’s commitment to continuous innovation is driven by its robust research and development (R&D) team, which plays a crucial role in the company’s success. The company invests around 5% of its annual revenue into R&D, ensuring that it remains at the forefront of technological advancements in wastewater treatment.
The company operates two R&D facilities—one in Chandigarh and another in Karnataka—and boasts a team of 50 employees, many of whom hold PhDs. Spray Engineering files at least 10 patents annually, underscoring its focus on developing unique, market-leading solutions and has a portfolio of over 100 patents to its name across all its business areas.
Cost-Effective Caustic Recovery Systems for Textile Mills
Spray Engineering also manufactures advanced caustic recovery plants that help textile mills recover clean caustic. These recovery systems are highly efficient, capable of recovering caustic concentrated up to 35-40%, which is on par with the raw caustic used in the industry.
The operating cost for Spray Engineering’s caustic recovery plants is estimated at just Rs 5 to 6 per liter, compared to the much higher cost of raw caustic, which can be priced at Rs 35 to 40 per liter. This substantial cost savings makes the caustic recovery system an attractive option for textile mills looking to reduce operational expenses while promoting sustainability.
Future Vision: Decarbonizing the Textile Industry by 2030
Looking ahead, Spray Engineering has set ambitious goals to drive sustainability in the textile industry. Mr. Verma shared the company’s long-term vision: “Our goal is to completely decarbonize the industrial sector by 2030, starting with the textile industry. We’ve already implemented our boiler-free technology in distilleries and sugar plants, and now we are focusing on textiles.”
“Wherever very high temperatures are needed, the mill can have a very small boiler, which can also run on electricity. It is also possible to reuse the heat generated by air conditioners. The idea is to use just one technology to serve two different and divergent needs. This will also lead to lower operational costs, which is the only tangible to survive in any competitive industry,” Mr. Verma informed.
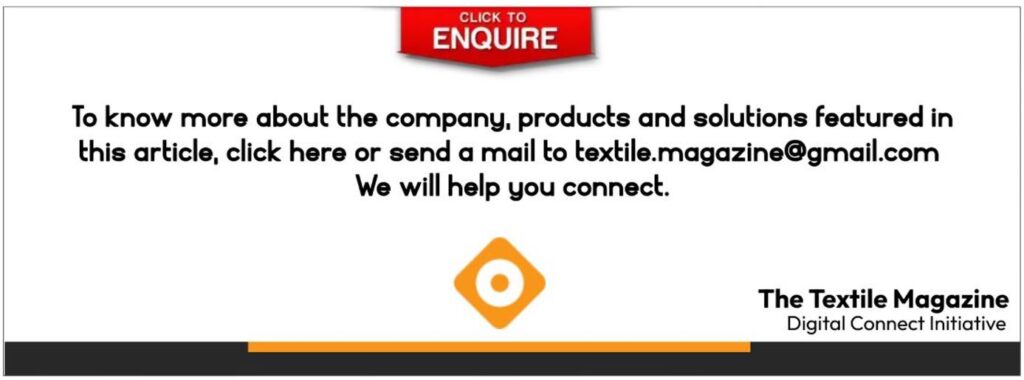