The finishing sector is undoubtedly the most significant stage in the value chain – contributing to a wide range of properties in the textile end-use. Bringing an ideal look, touch and functionality to many different applications is a real challenge for machine manufacturers. Smart innovations are needed. And customers also demand solutions that respect both valuable resources and the environment. The Sperotto Rimar portfolio combines both ingenuity and sustainability, to meet these goals – and customer needs which can be discussed with the real experts at upcoming India ITME.
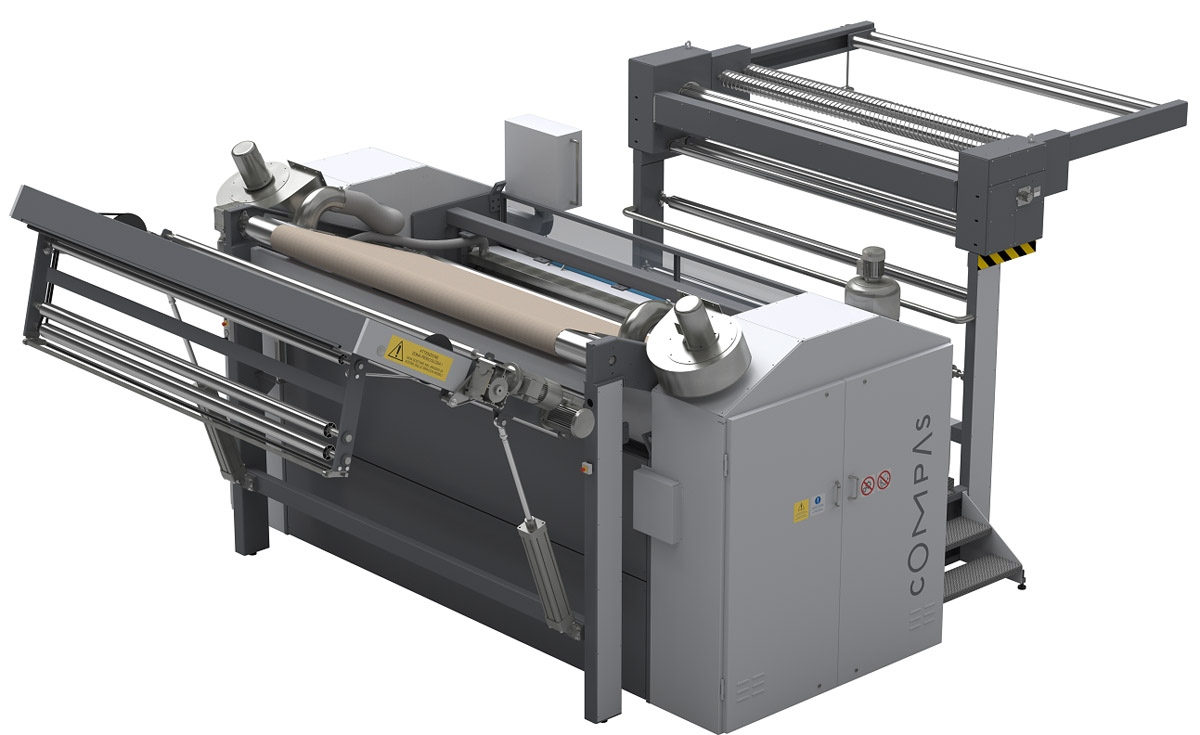
Sperotto Rimar follows two energy-saving strategies in machine development for fabric finishing. The first aims at technology which skips one or more production steps, to shorten the finishing process. Equally important is the use of innovative components such as motors, electrical and electronic controls, which can significantly reduce energy consumption.
Optimizing finishing processes is another way to save energy. The highest potential for energy saving today would come from reducing the use of steam, water or electricity in processing, and adopting technical solutions to limit, or partially recover, the energy consumed.
Short process, big impact
The Decofast decatising machine offers significant energy savings with the substitution of a discontinuous process. On certain fabric types, it allows users to skip one pass of direct steaming with pressure. This shortened process results in lower energy consumption and requires less labour. The technology enabling more sustainable decatising was actually introduced at the beginning of 2000 – long before finishing customers demanded machinery with reduced environmental footprints or urgent solutions for energy-saving needs.
Less steam, less energy
The Universa fabric relaxing machine can be used wherever relaxing, shrinking and bulking effects are required. It has wide application in different finishing fields – from wool to synthetic fabrics. Universa was designed to drastically reduce steam consumption. Tests prove that 30% less steam is needed compared to traditional technology. Conclusively, the machine needs 30% less energy – while achieving the expected quality results.
Recycling and closed loops
Nova has been a success for the past 50 years and is still the most eco-friendly solvent scouring machine – and the ideal alternative to traditional water scouring for the washing of synthetic fabrics. The technology has been continuously improved and therefore it facilitates excellent cleaning performance on various materials. Most of all, Nova convinces ecologically-sensitive finishers by its mastery of recycling. The machine recycles more than 99% of the chemicals used in the process.
Traditional scouring machines need a critical amount of water and detergents, which then must be treated as effluent. They also effect a relatively low level of oil elimination from the fabric. Nova solvent-based scouring is eco-friendly, as it works with a closed loop system in which air and solvent are properly treated and recycled. The fact that it takes 10 times less energy to dry solvent than to dry the same amount of water is an additional environmental plus for Nova. Furthermore, it almost totally removes the oil contained in the fabric, so that no polluted fumes are released in the subsequent thermic processes (heat-setting).
Compas – sustainable prime example
Sperotto Rimar’s Compas open-width compacting and finishing machine for knitted and woven fabrics uses an indirect water-cooling system to reduce the compacting belt temperature. With this system, the water is recovered by passing it through a chiller to keep its temperature at the right level. This technology can save about three cubic meters per hour. This water, totally unpolluted, can be continuously recovered and re-used in the machine. Traditional technology uses nozzles to spray water on the belt surface. The disadvantage of this is that the water is then discharged into the drain, contaminated with fluff and other products contained in the treated fabric.
Another feature enables a minimal environmental footprint through technology-based process optimization. Chemicals used before the dry finishing process are typically softeners or resins to enhance the final appearance and touch of the fabric. These are then transferred to the final garment. It is possible to reduce significantly the level of such chemicals, since the machine partially compensates for the effect of these chemicals. Thanks to its unique compacting method, Compas imparts a silky touch, only partly attributable to the softeners used, while mainly deriving from the special materials in the machine design.
Natural stretch is usually obtained by inserting elastane (a synthetic elastic yarn) during the weaving phase. The elastane itself, however, is difficult to deteriorate. Compas ensures the same degree of elasticity but with a final product that is 100% `natural´. Thanks to technology, saving the environment no longer means end-users have to compromise on the touch and feel of fabrics.
Sperotto Rimar inside
Know-how and experience – with a creative and successful development team – can make a big difference to finishing machinery design. Underpinning this, Sperotto Rimar always chooses machine components from latest-generation technology, aiming to save as much energy as possible. For example, the motors installed are of the IE 3 type.
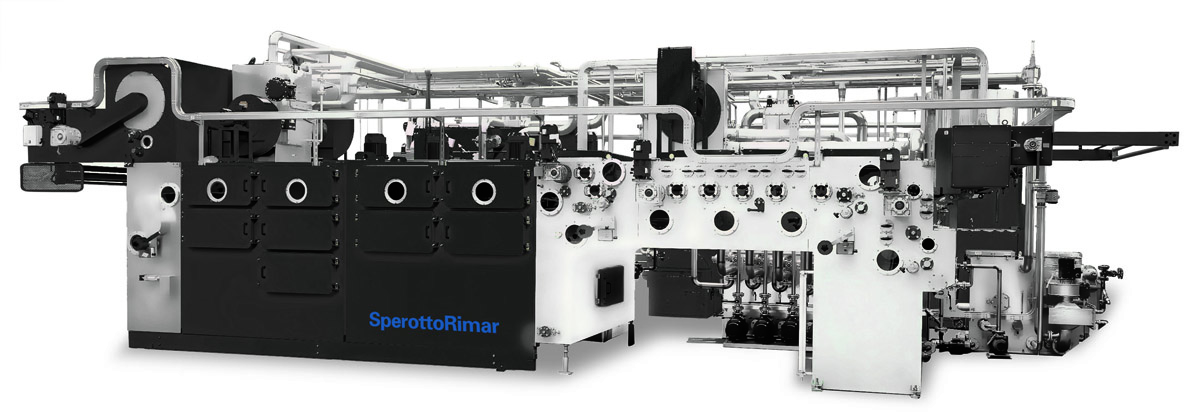
The focus of Sperotto Rimar is to develop a range of effective solutions, which make the most of textiles, in a sustainable way. Continuous technological innovations result in a smaller environmental footprint without compromising final fabric quality.
Sperotto Rimar on-site! Experts offer first-hand information about sustainable solutions for finishers at upcoming India ITME. Sperotto Rimar (member of Santex Rimar Group) welcomes visitors at the Group’s Booth H5F5 in Hall 5 at IEML in Greater Noida, Uttar Pradesh.