The Indian textile industry is one of the largest in the world, accounting for 4% of the global textile and apparel trade. Textile manufacturing process is an important aspect for today’s fashions. There are numerous steps involved in making of textiles and which needs variety of tools and machines to ensure best quality production. An important aspect for regular production of contemporary textile firms is the use of air compressors in the textile industry. Air is often referred to as the fourth utility after electricity, water and natural gas that power the textile industry. The use of air compressors in this sector has a direct impact on the quality of the finished goods which is why choosing the best industrial air compressor manufacturer is crucial.
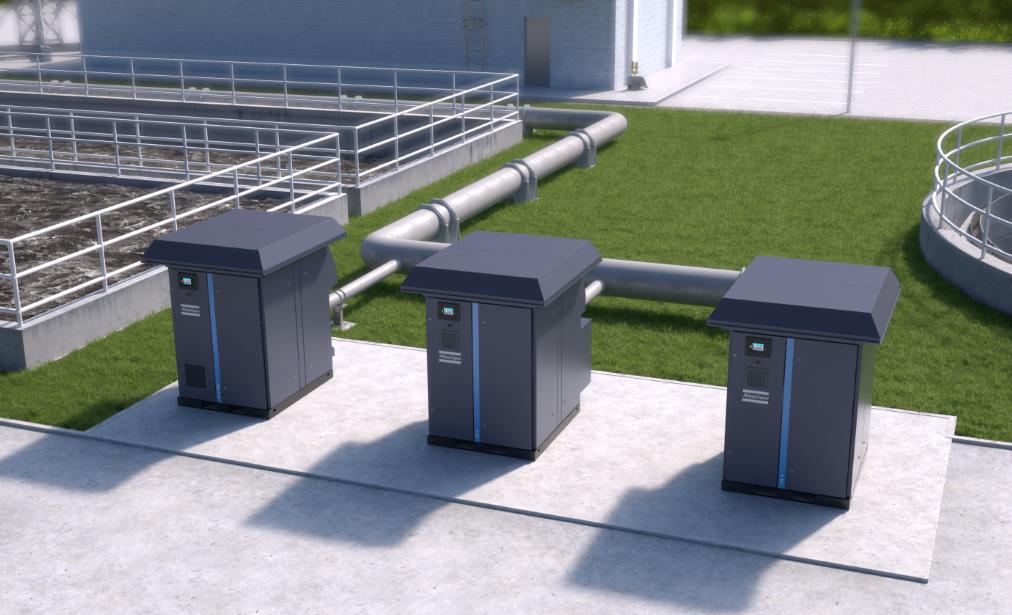
Applications of compressed air in textile manufacturing
In textile manufacturing facilities, compressed air systems are widely used for a number of purposes that are critical to preserving both quality and productivity. Mentioned below are few applications of compressed air in textile manufacturing:
- Spinning: To clean and operate the machinery, compressed air is utilized during the spinning process. In order to guarantee the spinning frames run smoothly and continuously, high-pressure air jets assist in clearing the fibers of contaminants and lint.
- Weaving: The weft yarn is driven through the warp shed by compressed air on air jet looms. Compared to traditional shuttle looms, this technique is quicker and more effective, increasing productivity and enabling the creation of finer, more intricate fabrics.
- Textile finishing: Fabrics are dried and texturized using compressed air during the finishing process. It aids in producing particular textures and finishes for fabrics, such as a smooth, wrinkle-free finishes or a soft feel.
- Pneumatic conveying: Raw materials and completed goods can be transported pneumatically with the help of compressed air systems. This mode of transportation lowers the chance of contamination and is efficient and clean.
- Garmenting: The process of making garments includes a number of organized steps, including marking, cutting, sewing, and laying. For many of these operations, compressed air for pneumatic tools is required.
- Intermingling: It is a process in the textile industry where continuous filament yarns are entangled or intertwined using high-pressure air jets. This operation produces interlaced yarns that are more cohesive and stable, improving their handling and processing properties. Low-pressure compressors provide a steady and reliable supply of compressed air, which is crucial for maintaining the consistency of the intermingling process.
- Maintenance and cleaning: For textile machinery to operate efficiently, regular maintenance and cleaning are essential. To keep machinery in top operating condition, compressed air is used to remove lint, dust, and other debris from it.
Benefits of compressed air in textile manufacturing
Textile industries across the world have been using air compressors as an energy source lately. Compressed air systems increase overall efficiency and decrease downtime in a variety of manufacturing processes. A wide range of applications can benefit from the consistent operation and high-quality output that is ensured by the precise control and flexibility of air pressure and flow.
Furthermore, it reduces the requirement for mechanical interventions and manual handling, improving workplace safety. For every application there is a right solution available with respect to pressure & flow requirement. The right selection of compressor will help to operate efficiently, and will consume less energy compared to high-pressure systems. This leads to lower operational costs and energy savings and also intangible benefits such as a reduced carbon footprint.
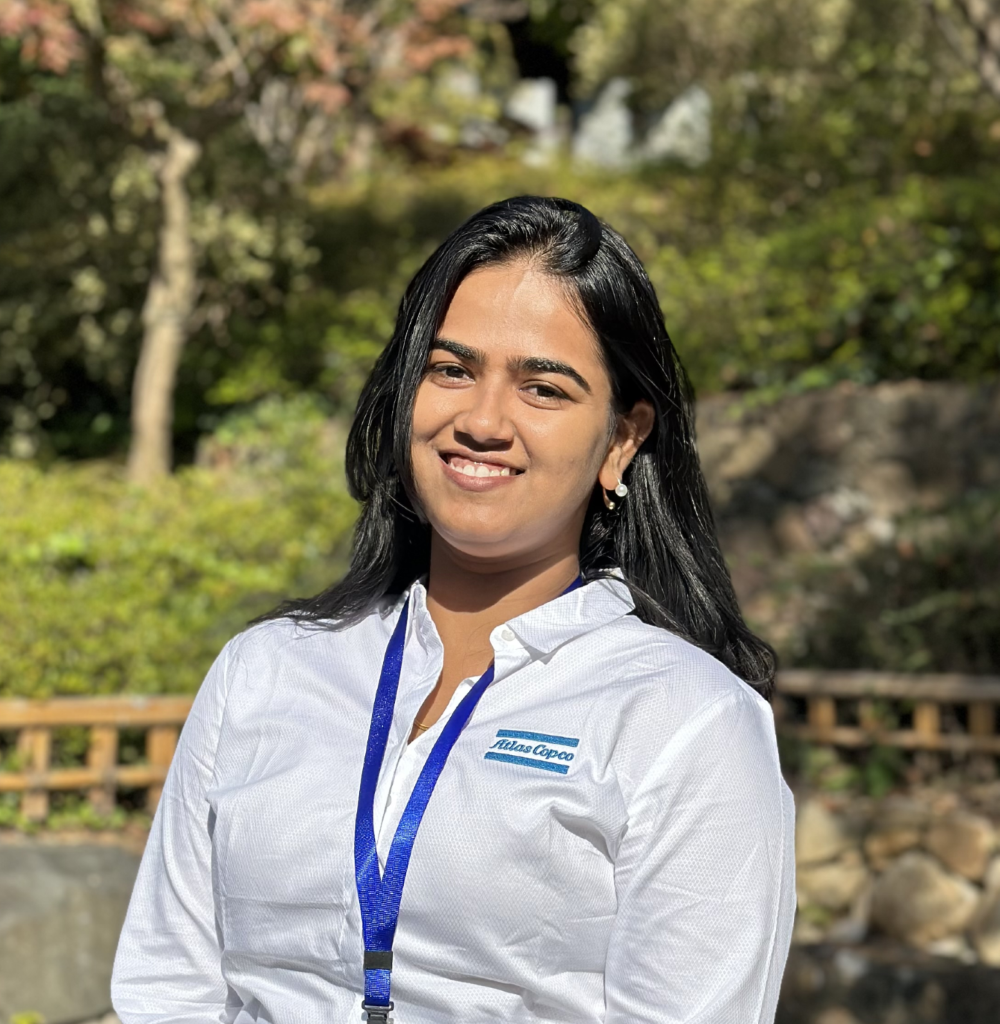
In the textile manufacturing industry, compressed air systems are essential for improving operational effectiveness, guaranteeing product quality, and fostering sustainability. The significance of these systems will only increase as the industry develops, propelled by continuous technological breakthroughs and a heightened awareness of environmental responsibility and energy efficiency. Textile producers can boost their bottom line and help ensure a more sustainable future for the sector by investing in contemporary, effective compressed air systems.
The importance of blowers in textile manufacturing
Water is used for different purpose like dyeing, finishing, bleaching, etc. Water that contains high levels of TSS (total suspended solids), dyes, chemicals & auxiliaries, metal toxicants and BOD (biochemical oxygen demand) must be treated before being discharged into the environment. Chemical impression and dirt is common in the textile industry. To treat this water, effluent plants must be set up in every manufacturing unit. As per environmental compliance, ETPs (effluent treatment plants) and TPs are essential for treating wastewater generated during textile manufacturing. They help in ensuring that your facility complies with environmental regulations and standards. Implementing ETPs aligns with sustainable manufacturing practices, enhancing the company’s reputation and commitment to environmental stewardship.
Application of blowers in ETPs
Aeration/ activated sludge stage: In this process air is included in water that needs to be treated. providing necessary biological micro-organisms growth & development that can take place. Generally, this process required 24*7 continuous supply of air leading to highest consumption of power utilisation in the entire ETP set up. Using the right blower technology can substantially decrease power usage and is a more sustainable approach.
Benefits of the right blower
- Energy Efficiency: Blowers provide the necessary air for various processes in textile manufacturing, such as drying, air jet weaving, and pneumatic conveying. Advanced blower technology can significantly reduce energy consumption, leading to cost savings.
- Process Efficiency: Blowers ensure a consistent and reliable supply of air, which is crucial for maintaining the quality and efficiency of textile production processes.
- Product Quality: In applications like drying, the use of efficient blowers can directly impact the quality of the final product by ensuring uniform drying and reducing the risk of defects.
- Operational Reliability: High-quality blowers contribute to the overall reliability and uptime of the textile manufacturing process, reducing the likelihood of breakdowns and maintenance issues.
- Noise Reduction: Modern blowers are designed to operate quietly, minimizing noise pollution in the manufacturing environment, and contributing to a better workplace for employees.
Both Effluent Treatment Plants and blowers play a critical role in enhancing the environmental sustainability, efficiency, and overall operational effectiveness of textile manufacturing.