New technology helps adhere to stringent quality standards and improve productivity
Spinning mills in Tamil Nadu have built a reputation for themselves based on innovation, use of latest technologies and consistent raising of the bar when it comes to quality standards. Gomuki Spinning Mills (P) Ltd., located in Vijayamangalam in Erode district, a good example of top management believing in investing in the latest technology and upgradation of infrastructure to stay ahead of the competition.
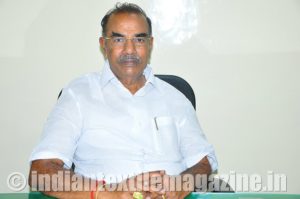
Helping Gomuki Spinning Mills to maintain top notch quality and improved productivity is the Sheltronics Group of Companies ISO 9001: 2015 Certified Company, headquartered in Coimbatore, which is a leading manufacturer, exporter and supplier of textile machinery accessories and components. Sheltronics’ pathbreaking, SEDAC-16 Electronic Draft Autoleveller Controller for Drawframe is playing a key role in Gomuki Spinning Mills’ success story.
Giving a brief overview of Gomuki Spinning Mills, Mr. S. Subramaniam, Managing Director, said: “We started operations in 1990, with about 6,000 spindle capacity. With consistent growth year-on-year we have now 30,000 spindle capacity. We have around 350 staff working in our unit.”
The company’s key focus area is the manufacture of 100% compact yarn and its major market is neighboring Tirupur. It exports its products mainly to South-East Asian countries, apart from South America and Turkey.
As mentioned earlier, Gomuki top management is a strong believer in investing in the latest technology, which is reflected in infrastructure where one can find machinery and testing equipment of global brands such as LMW, Reiter, Schlafhorst, Uster, Premier, etc.
Going into details about the quality assurance process followed at the mill, Mr. Subramaniam said: “Our strength lies in product quality. We source cotton only from a select few suppliers. We make sure that we have enough stock to last 6-7 months. With us you can be assured of consistency in quality. Remember, we are catering to some of the most discerning customers such as exporters in Tirupur who in turn have to satisfy quality conscious customers in Europe, the US, etc. Partnering us in our endeavor to maintain high quality standards is the SEDAC-16, autoleveller technology without gear box.”
Pointing to another major advantage with the use of the SEDAC-16, Mr. Subramaniam added: “The SEDAC-16 technology can be adapted in the 15-year-old existing drawframe machines like RSB851 and D35 models. The upgrade makes these machines superior to the latest drawframe machines available in the market. There is no need to go for new model drawframe machines which are expensive”. ,thus enabling huge savings of money spent in the purchase of capital equipment.”
The SEDAC-16 enables consistent sliver quality and optimized yarn realization because of continuous monitoring. Any kind of variation and the machine would automatically stop. This ensures that there is no chance of inferior quality.
“Since the entire process is being constantly monitored, the chances of machine downtime are also reduced significantly. Moreover, the display and interface are also very user-friendly. Even typical, semi-literate floor level staff can understand and operate the device,” Mr. Subramaniam said pointing out to the other advantages of the technology.
According to Mr. Subramaniam, the technical support provided by Sheltronics is indeed excellent. Gomuki Spinning Mills had earlier installed a Combo-T model from Sheltronics for about one year and was extremely satisfied with its performance. Later it was decided to go in for the SEDAC-16 model, which had created quite a buzz when it was officially introduced after exhaustive trials at ITME 2016 in Mumbai.
In the case of Gomuki Spinning Mills, the upgradation has been done on RSB 851 to D35 drawframes.
Some of the salient features of the autoleveller without gear box, which is a result of Sheltronics’ indigenous R&D effort are:
- India’s No.1 and first auto leveller with 35 per cent infeed variation correction.
- SEDAC-16 Technology incorporated in the old drawframe machine will ensure higher productivity with better quality standards of sliver in the existing machine.
- The more reliable and cost-effective electronic draft system eliminates the diffrential gear box and draft change wheels, thus enabling a layman to change the draft with one touch without the help of the mechanical team for changing the gear wheels and thus reducing the production loss.
- First of its kind to incorporate remote monitoring and control with the Internet of Things (IOT) in Auto Leveller.
- The technology is adpated and implemented by world leaders in drawframe machines.
- Auto levelling action for every 3mm of infeed sliver from start to end.
- Thick place measurement of each can and 24 hours datalog and stop control
- 1mm scanning and 0.5 millisec Auto leveller corection response
- Excellent sliver evenness achive at higher delivery speed by the high dynamic servo motor
- 1200 mtr/min delivery speed operation.
- Recording of thick place > 2cm.
- Online quality monitoring system for quick assesment and decision making with data storage for 31 days.
- Trend graph and stop contol for infeed ,delivery, A%,U% & CV%.
- Unique user friendly integrated operator console for monitoring and control.
- Cost effective automation technology