Have we ever wondered how all the prints on our clothes come about and do not fade away or get wiped off after a wash? This is just like a simple drawing on a paper. Washing it would have caused the print to wither away making our favourite clothes look dull. Thankfully, the textile industry was smart enough to pre-empt this, and the process of textile printing began.
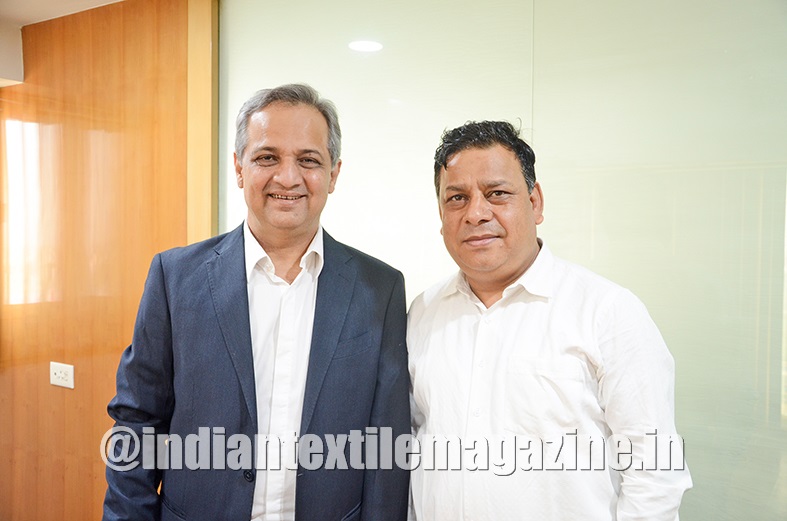
Textile printing is essentially the process of applying colours in definite designs and patterns on to the fabric. In such printed fabrics, the colour(s) bond with the fibre, which ensures that the print does not wash away. To print the fabric in bulk screen printing is the most popular and cost-effective way. It involves using mesh to transfer ink onto the substrate and for that a design is imposed on a Nickel Fine mesh. To serve a similar purpose of giving value to the printing industry and for preserving prints Screen-O-Tex was set up in 2001.
Screen-O-Tex, since its inception in 2001, has been working relentlessly to make the world around us look colourful and for us to look stylish. Sudesh Khanna, Managing Director, and Kuldeep Rawat, Sales – Head of Screen-O-Tex, tell us more about the company’s contribution to the textile industry.
Initially, Screen-O-Tex started as a small company specializing in various types of technical screens for printing on textiles. In 2019 the company become the largest producer of rotary nickel screens in India with a capacity of producing 2.5 lakh units per annum. In fact, the company started off by producing a unique product which ensured that a higher number of repeats were produced, whereas now it produces the complete range of screens which include Altus screens, Nova screens, Tech screens and the newly-introduced finer Mesh Vega screens.
The company also makes sure that it remains technologically updated with systems and processes in place which are also regularly updated with their technical partners since last 16 years. The competitive edge Screen-O-Tex has over other manufacturers is its continuous research and development along with process updates. The company’s main concentration is on the textiles industry where more than 90% of the screens produced go for fabric printing, whereas the remaining 10% is used for non-textile purposes.
While stressing the company role in the current scenario, Mr. Sudesh Khanna cited an ideal instance in Africa. The Africans print a special textile known as the khanga or the kanga, for which they used a special type of screen. At that time, they realised that there was no other alternative available to provide for the unique kind of screen used for the special textile used.
Mr. Sudesh Khanna also mentioned that his company motto as a promoter has always been “providing good quality screens at reasonable prices so as to fill the vacuum created”.
Highlighting the company’s journey, the two executives said how the company started in Europe for the trial of all suitable machinery. After the initial struggle of 2-3 years in establishing the product, the efforts paid off, and it was possible to start a company in 2001. In the beginning, the company only produced for export. Gradually, it started exploring the domestic market in 2005-2006. At present, the dynamics have completely changed. Exports constitute only 35% of the production and the major 65% of production is to cater to the domestic textile industry. Currently, the company exports to 20 countries such as South America, Brazil, Peru, Germany, Spain, Portugal, Pakistan, Sri Lanka and Bangladesh. It has its warehouse in Pakistan.
The progress of the company was so rapid that now it produces the complete range of screens. The company has a separate R&D department managed by a European PhD researcher. Without continuous research and upgradation it would be impossible to offer the full range of textile screens. The only raw material used for screen printing is high-grade pure nickel. There is no alternative since no alloy is as strong, flexible and reactant with the printing chemicals as nickel.
The production plant is located at Changodar, near Moraiya. The capacity utilisation of the plant currently is around 90% of its full potential. Screen-O-Tex is proud of its highly trained human resource. Today there are 100 people in charge of production and administration. They are highly qualified and backed with long experience. The team consists of management and techno professionals, technical (R&D) experts, marketing and finance specialists and support staff.
The company strongly believes in quality and services rather than in quantity and services. There is no warehouse as such in the country. This is because a complete inventory is available at the factory with a range of products.
The company also makes sure that orders are executed within 24 hours. Mr. Rawat believes that it is easy for people to manage and assist all users and customers from one place. This is the only company where every printing solution is available under one roof and where all repeats and mesh sizes are offered.
Screen-O-Tex recently joined hands with A.T.E. for further growth. This was announced on October 5, 2018, at a seminar in Tirupur. The reason why Screen-O-Tex chose A.T.E. was that it was very well aware of the company and its products. A.T.E. also had a strong infrastructural and marketing base.
A.T.E. has the necessary experience and understanding of how the textile screen market functions. This helps A.T.E. to perform better and ensure guaranteed success.
This relationship between the two is now 6 months old and has yielded results. In the past 4-5 months, there are 16 new contracts signed in the South. The company has already generated Rs. 20 million worth of business. On the international front, it has received a handsome order from a leading Bangladesh company.
The relationship with A.T.E. has been growing fast, and the latter has been instrumental in enhancing the company’s performance to a great extent.
Mr. Khanna said: “A.T.E. has showed us a path of a bright future and will definitely be a win-win situation for both parties and the customers. With the help of A.T.E. our company will have 35 new customers by March 2019”.
In the last 8 years, progress has been magnanimous. Production has grown from 35,000 to 250,000 screens per annum.
The vision of the Screen-O-Tex team is to double its capacity in the next five years. The aim is also to set up a warehouse out of the country, in South America and Bangladesh.
The interaction ended on a positive note with major focus on the importance of digital printing which will make prints of better quality.
“We are happy to tie-up with Screen O Tex recently mainly to work for South India and Bangladesh markets. A.T.E is well known in our country for bringing the latest technology and one of the reasons for our success in business is the selection of product. We study in detail the product and technology which should match with the requirements of the end users in India. Also we are strict in selecting the manufacturers who should well align with us on customers satisfaction, the attitude towards customers satisfaction is an important factor for us. We are fully convinced with the products of Screen O Tex in terms of the quality and technology for producing the screens. They use European technology which has been well accepted in the global market. The management of Screen O Tex has an attitude towards customers’ satisfaction by which they are in alignment with us. We have rich experience of handling/establishing rotary screens business, many of our customers are excited with our tie-up with Screen O Tex and we are confident of achieving our goal of increasing our market share”
– Mr. S. Rajendran, Senior Vice President – Processing, Accessories and After Sales Services, A.T.E. Enterprises Pvt. Ltd.