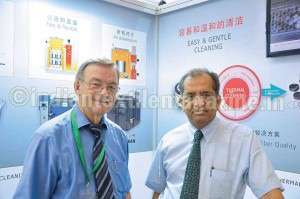
SCHWING demonstrated at ITMA Asia its latest thermal cleaning technology for filament, fibers, and recycling processes. The equipment has been designed with the latest in pollution control. It operates with low energy consumption as mandated in most markets.
SCHWING is the only manufacturer worldwide offering the advanced thermal cleaning technology for removal of polymers and organic contamination from metal components and machine parts of any type and size. This includes spinnerets, pack body components, screens, filter components, extruder screws, etc.
For synthetic fiber production, proper cleaning of spinnerets and the pack body during pack changes is critical for faster start-ups, tenacity, denier, dyeing and operation cost.
Further, SCHWING offered its latest VACUCLEAN system based on vacuum pyrolysis operating principle with a unique 3-step operation that ensures spinnerets are completely cleaned before returning them onto the line. It is very well accepted by customers who experience the difference over traditional burnout ovens or TEG cleaning by having much better cleaning results with lower energy usage and without pollution by use of a special catalytic converter.
SCHWING also offers its INNOVACLEAN cleaning system, which typically needs three to six hours to complete the cleaning process at temperatures between 450°C and 480°C. INNOVACLEAN can be used with most nozzle geometries and even with critical capillary sizes.
SCHWING has mastered all methods to clean components without any residues – cleaned perfectly without carbon residues, gentle on the components to be cleaned and the environment, economical in terms of energy consumption and operation, and safe through operation with intelligent controls.
SCHWING is an international industry leader with customers from the international fiber and plastics industry having trusted the application experience of the company for over 20 years.