Auro Spinning Mills, Baddi, a part of the Vardhman Group, is one of the mills in India where quality matters the most. Vardhman is famous for its quality, and thus Auro serves some of the most demanding customers in the world.
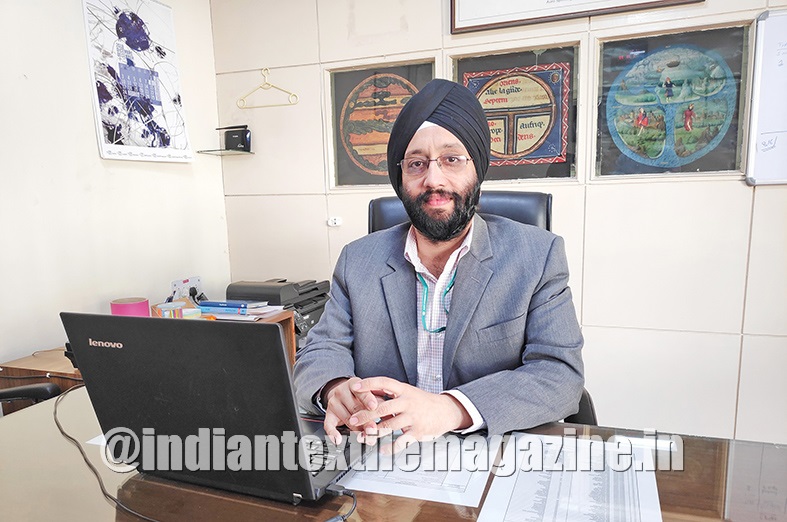
Set up in 1991, Auro Spinning Mills has now six internal units having 80,000 spindles and 1,500 rotors. Mr. Gurpreet Singh, who is responsible for Auro Spinning, heads a team consisting of around 800 employees who have expertise in running coarse, medium fine and superfine yarn counts. The average count is Ne 38’s and the finest yarn spun here is compact Ne 200’s with Suvin cotton. Along with cotton yarn, Auro also produces yarn from special blends of linen, wool and silk. Total production is upto 44 metric tons per day.
Auro Spinning Mills is also the centre for all Vardhman units in the Baddi area. A new product development and R&D centre is located here to takes up challenging assignments to produce special core spun yarn blends of Lycra and other complex products. It is here that Savio winders have been living up to the exacting standards of Vardhman’s customers. This mill has 300 Savio automatic winder drums running mostly on Lycra.
Mr. Gurpreet Singh explains why Savio automatic winders are preferred: “Filament visibility, especially in the dark shades of the core spun Lycra yarns, is not at all desired, and Savio’s twin splicer gives us the best results. At Vardhman, our prime responsibility is to deliver value-added products to our customers”.
He added: “In a few articles, appearance of splice is very critical and we agree that moist splicer is an innovative solution as it is comparable with the same as the parent yarn. The twin splicer for core yarns ensures minimum fibre loss and maximum coverage to filament”.
Savio’s moist air splicer is an innovative one that also uses a very small quantity of water alongwith air in the form of a spray. This creates a moist atmosphere in the splicing zone in a controlled manner with a centralized setting arrangement. “Next to splicers, ‘Flexible cycle’ is one among the best features that avoids unnecessary operation of moving parts. With online tension monitoring in sync with the drum speed and package speed sensors, the output package density, especially the unwinding tension, make a huge difference in downstream process efficiencies.”
Mr. Gurpreet Singh was all praise for the technology supplier partner A.T.E. when he said: “With A.T.E. we have a long and comfortable relationship. They address our issues in a professional manner and come up with the desired solutions instantly. We are happy to continue our relationship with A.T.E. in the expansion of the Vardhman Group’s core spun yarn capabilities at Vardhman Fabrics, Bhopal, with 720 additional drums from Savio.”