The trend towards automation significantly determines investments of the textile industry, both in new installations and in the replacement sector. The Autoconer with RFID material flow technology offers various automation solutions that can be individually and intelligent adapted to customer requirements. With MultiLink, it is now possible to design the spinning mill layouts more flexible, cost-effective and space-saving.
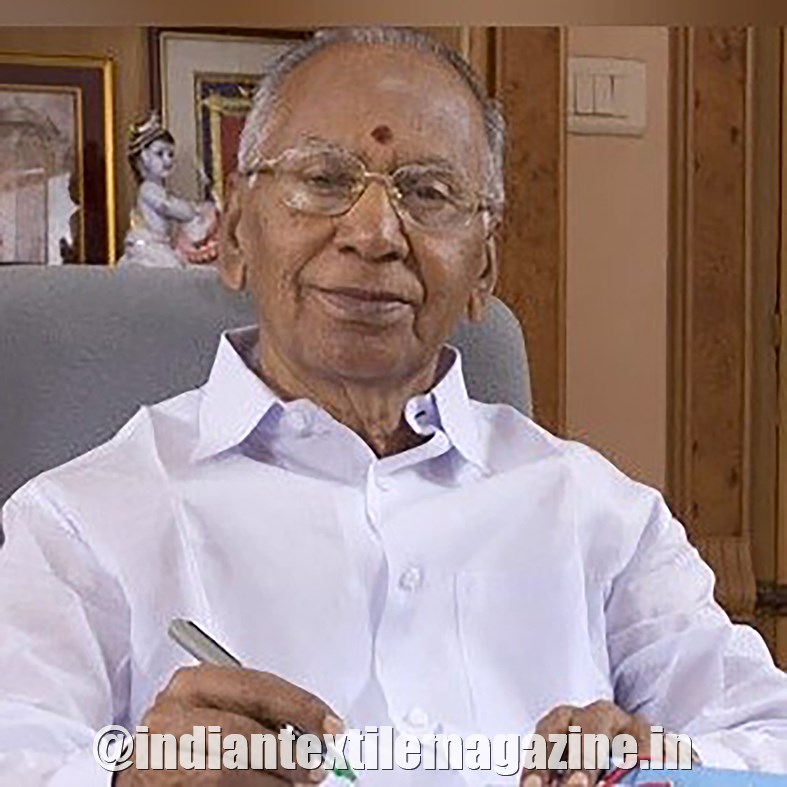
Flexible, space-saving spinning mill layouts
Up to four ring-spinning machines can be linked to one Autoconer via MultiLink. This makes automation possible in situations where it was previously not economical. This applies, for example, to conditions where space is cramped or limited, typical of the replacement segment. Mill layouts for linked installations with relatively narrow spacing between the machine, e.g. already from 1.80 m distance centre to centre of the ring-spinning machines, are possible. Thanks to MultiLink, spinning mills that still work manually today can now go into economical automation. This is because assigning up to four ring-spinning machines also enables a profitable link with shorter spinning machines, which is typical for the manually operated sector. MultiLink is implementable as a direct or underfloor link. Since the interface and the positioning of the machines are variable, there is a high degree of flexibility in the design of the spinning mill layout. Parallel positioning or in row – this is done optimally according to the space available in the spinning mill.
Investment costs are reduced by up to 15% – energy costs are reduced by up to 20%, highest throughput rates with the Autoconer
The flexibility and the optimal space utilisation also open up economic perspectives in the construction of new spinning mills. The maximum possible throughput rates are decisive for the design and capacity calculation of such MultiLink systems, both for the interface and the material flow. Here the Autoconer has a unique advantage: the patented optical infrared tube inspector. It allows material flow rates of up to 100 tubes per minute, so that the interface capacity can be used to the maximum. Therefore, more ring-spinning positions can be assigned to an Autoconer than to other winding machines.
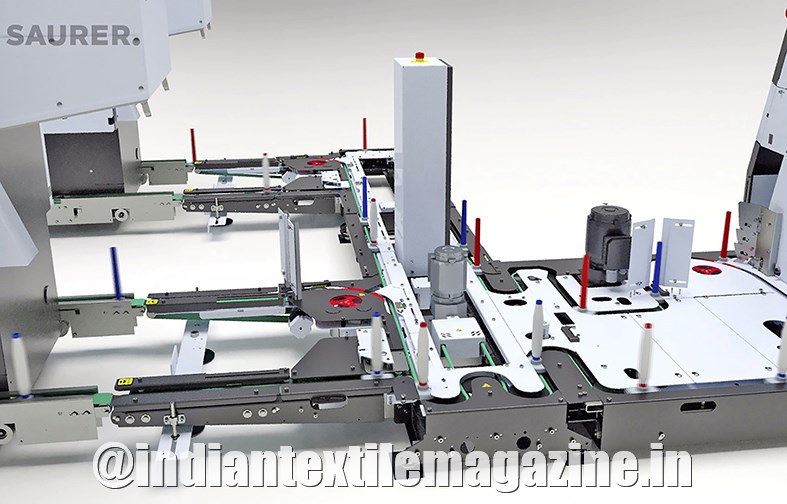
Overall, investment costs are reduced by up to 15%, as the costs for one-off units can be spread over more winding units. Since energy consumption, for example in suction systems or machine cleaning, only occurs once instead of 2-4 times, MultiLink saves up to 20% on energy costs compared to conventionally 1:1 linked solutions depending on the configuration.
Guaranteed quality monitoring with SPID
The guaranteed and patented online quality control offers additional benefits in the Saurer solution thanks to integrated SPID (Spindle Identification System). This allows the yarn quality to be monitored at each individual ring-spinning position, even when an Autoconer is flexibly linked to up to four ring-spinning machines.
Practical experience in the system and automation business
With its extensive automation and system competence Saurer is the ideal engineering partner for customer specific spinning mill layouts. From pre-spinning, to roving frames, ring-spinning machines, winding machines and twisting machines, Saurer can plan and install the entire process in the best possible logistic. A 3:1 MultiLink system (Saurer ring-spinning, winding and twisting machines) is currently being installed in China.
The first Autoconer MultiLink installations in Indian spinning mills have been running to the full satisfaction of the customers, e.g. Sri Matha Spinning Mills Ltd. for about one year. Here 2:1 link solutions were installed, on the one hand as a direct link and on the other hand as an underfloor link. Improvements can be seen in material flow logistics, route optimisation for personnel and capacity utilisation.
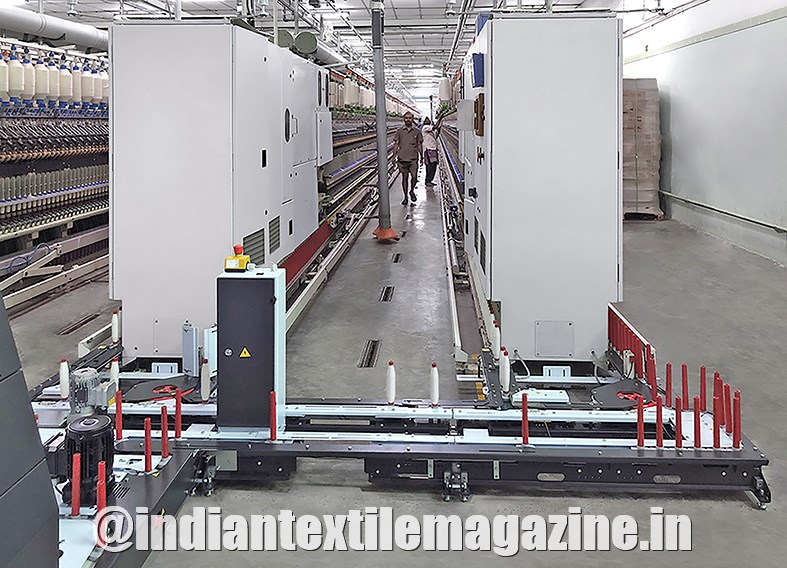
Shri. P. S. Velusamy, Chairman, SSM Group, and Director, Sri Matha Spinning Mills Ltd., said: “When we were interested in the automation of our ring/winding shed, it was not possible to realise this with a standard solution in the existing layout due to the presence of concrete pillars. Thanks to Saurer, who tried very hard to find an intelligent automatic solution for us, we decided on MultiLink Autoconer based on their expertise. It has been working for more than a year and we are extremely satisfied with the machine’s performance. We are very happy that we were able to implement the automation within the existing layout.”
MultiLink: summary of the Autoconer features and customer benefits
• Flexible design of spinning mill layouts
o Link two to four ring-spinning machines with one Autoconer
o Variable positioning of the Autoconer along the interfaces
o Available as direct or underfloor link
• Economical automation
o Space-saving: economical link of short ring-spinning machines and for mills with limited space
o Cost-saving: reduction of investment and energy costs
• Maximum throughput rates
o Decentralised material flow with highest throughput rates
o Unique optic tube inspector with up to 100 cycles/min
• Online quality monitoring with SPID
o Integration of Spindle Identification System (SPID) to monitor the quality of each ring-spinning spindle
• Saurer’s system expertise