Right from 1853 when the Franz Saurer foundry was set up, Saurer has made vast strides and passed through various developmental phases and introduced to the world the very first manual and automatic embroidery machines.
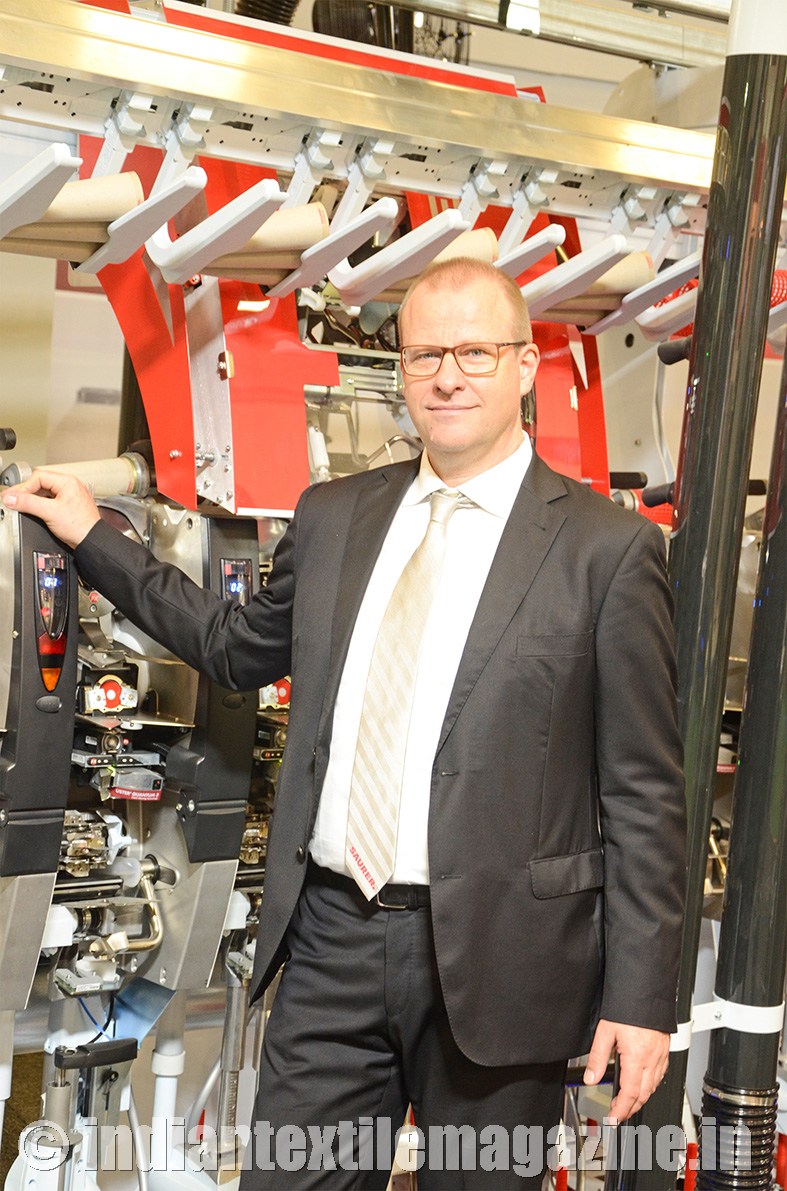
Rich with history and tradition, Saurer today is a leading technology group that functions across the globe, mainly focusing on machinery and components for yarn processing. For even more synergies for customers, the group has been segmented into Saurer Spinning Solutions which offers high quality, technologically advanced and customer-specific automation solutions for processing staple fiber, from bale to yarn. Saurer Technologies specializes in twisting and embroidery as well as engineered and polymer solutions.
The Saurer Group also holds to its credit annual sales revenues of 1.1 billion Euros, 4300 employees, and settlements in Switzerland, Germany, Turkey, Brazil, Mexico, the US, China, India and Singapore, Saurer also happens to be listed on the Shanghai Stock Exchange.
Mr. Peter Goelden, Vice President – Director Business Line Ring Spinning Solutions from the Saurer Group helped shed some more light on the recent activities of his organization in his exclusive interaction with The Textile Magazine.
The year gone by
The year 2017 has a lot of success and accomplishments. If 2016 was a good year for business, its successor has proven to be the best so far. Significant growth was achieved and many innovations were launched in various fields.
After a successful market launch of the Zinser 71 and Zinser 72 series, Saurer launched the innovative Zinser 72XL ring spinning machine in the market. Zinser 72XL is the longest ring spinning machine in the world with a maximum of 2,016 spindles – its precursor possessed only 1,680. Cost efficiency is important to ring spinning and Zinser 72XL maximizes that as the average length of ring spinning machines in the industry happens to be only 1,200 which is almost 50% less than that of Saurer Group’s latest innovation.
Owing to its flexibility, low energy costs, maximum productivity, highest number of spindles and optimal machine length the Zinser 72XL has been well received by the customers. What further sets Saurer apart from its competitors is its compact spinning system with its precise adjustability and reliable compacting based on self-cleaning technology provisions which are futuristic and efficient.
The Autoflow System from Saurer is also proving to be ground-breaking as it links the processes of roving, ring spinning and winding. This complete package favours Saurer as a partner of spinning mills worldwide.
Another technology highlight of Saurer is the Texparts spindle bearing unit CS1S, making an impact on the working conditions in mills due to its silent running and relatively cooler nature when compared to its noisy and immense heat generating counterparts.
Anchoring in India
Many automation systems, including the linkage system, have been installed in India. The reason for a prosperous trade relation with India is not only the customizations available to Indian needs but also the manufacturing and customization of these automation systems on the Indian soil. Saurer Group has set up its manufacturing plant in Vadodara in 2015 which manufactures systems for the Indian customers as well as for export. The availability of Indian footprints for the machinery is a highlight for the buyers but that of European and Chinese footprints is a cherry on the top!
Saurer expects to maximize its market share in India and the presence of other big automation manufacturers only toughens the competition which is why Saurer is already taking steps like tailoring machinery and systems according to Indian taste and bringing the processes closer with their linkage system. The Customer Road Show last March recorded great reception of these technologies in the Indian market.
Owing to its Chinese roots, complete automation systems are easily available in China. Even Europe has had encounters with these systems since the past years and now finally this experience is brought to India. To develop the business in India, a new Head of Indian Operations, Mr. Vikas Sharan, has been appointed by the Saurer Group. With his expertise in business, he is expected to devise a dynamic manufacturing and sales structure in India to offer new business opportunities.
The Saurer Group has been setting industry standards for more than a century and a half now and doesn’t seem to want to stop the good work anytime soon. Having evolved from a small foundry to a multi-million dollar company, Saurer has always made headlines with its pioneering spirit and inventions. With the introduction of innovative technologies for expanding its Indian operations, the company is keen on setting new standards of production technology.
Schlafhorst’s new innovative VTC for Autocoro 9
The new vacuum trash cleaner (VTC) from Schlafhorst is an innovative unit for the Autocoro 9. It improves automated cleaning of the rotor spinning machine and thus increases its profitability. The VTC increases the raw material tolerance of the Autocoro 9, further reducing spinning costs. Spinning of recycled or coarse yarns generates a lot of fibre waste due to the high material throughput. The E3-optimised innovation counteracts this. It significantly reduces the manpower required to keep the machines clean in these applications.
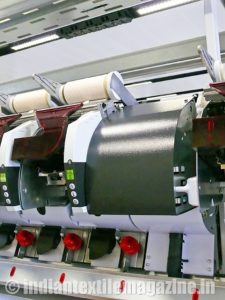
Efficient machine cleaning with minimum personnel costs The VTC is located in the middle of the machine where it vacuums the dirt removal conveyor belt halfway. As a result, less fibre material accumulates on the belt, so that it does not pile up even with larger quantities of waste. The fibre dust can no longer fall down, get swirled up or contaminate the machine from the inside. The machine remains clean even at high material throughput rates.
The advantages of this innovation in automation are evident. The manual effort for cleaning the spinning boxes and winding devices as well as the underside of the machine is reduced substantially. The fibre waste is taken to where it belongs: the dirt collection chamber. In addition, the brush housing stays clean for much longer, meaning that brush cleaning can be reduced by up to 80%. With a cleaning cycle of 10 minutes per machine, this measure alone quickly saves the expenses of an operator.
With its extremely high piecing capacity thanks to SynchroPiecing, the Autocoro 9 gives spinning mills more flexibility in the selection of raw materials. The VTC now significantly boosts the raw material tolerance of the Autocoro 9 further. It prevents fibre build-ups in the spinning box area underneath the machine and thus reduces contamination of the yarn with dirt particles. The spinning stability increases, reducing yarn breakage. The greater cleanliness ensures better IPI values and an overall higher yarn quality. This ultimately also increases productivity, as the Corolab has to intervene much less frequently with cleaning cuts.
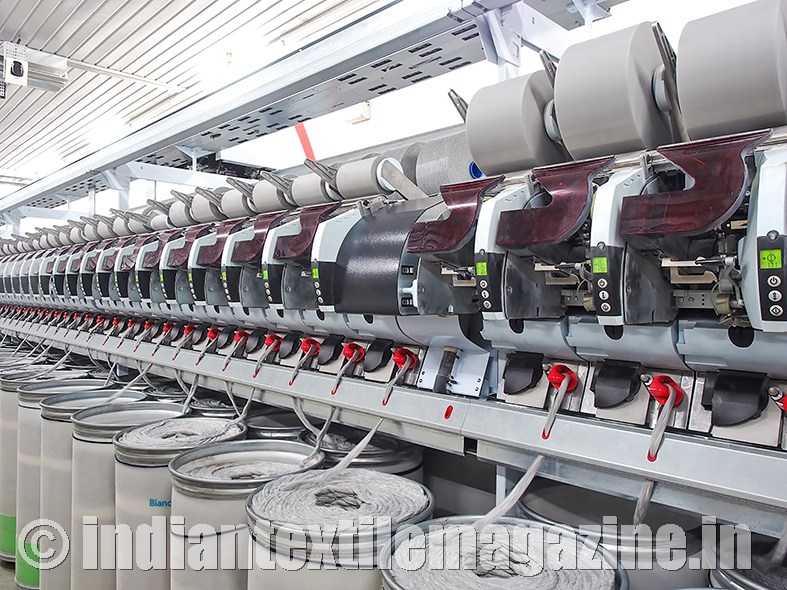
Maximum added value for recycling applications true to the E3 philosophy, the Autocoro 9 delivers triple added value to spinning mills in terms of energy. This also makes it the benchmark for recycling. Even at extremely high rotor speeds, the Autocoro 9 achieves efficiency levels of more than 99%, thanks to SynchroPiecing. With spinning components that have been specially optimised for recycling applications, the Autocoro 9 also spins yarns with higher strength from critical raw materials. A special opening roller protects the stressed fibres.
The VTC improves this already considerable added value of the Autocoro 9, especially in long machines. This opens up new savings opportunities for spinning mills. Raw material accounts for a large part of the spinning costs. A cost saving of 1 ct/kg weaving yarn (Ne 10) with a production capacity of just under 10,000 kg per day, which is what an Autocoro 9 with 720 spinning positions can achieve, adds up to annual savings of more than €35,000 for each machine. Against this backdrop, the Autocoro 9, equipped with the innovative VTC, is likely to rapidly expand its undisputed market leadership in the price-sensitive recycling market.