The textile industry today is facing several major challenges: cost and availability of labor, utilization of resources and the increasing pace of fashion. Saurer approaches solutions for these challenges in creating ground-breaking innovations to foster customer profitability. The passion for customers, innovation and quality gave birth to E³, the striple added value (energy, economics, ergonomics), which has since been the guideline for Saurer’s innovation process.
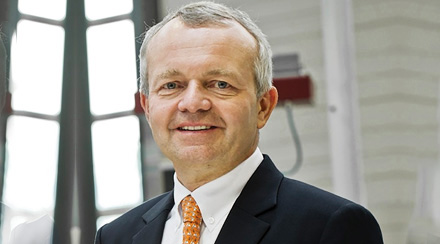
The name Saurer already carries a long tradition in setting new standards. At ITMA 2015 the Saurer Group will reveal all new E³ labelled machinery with the triple-added value for customers. It will be showcasing new standards in energy savings, production flexibility, highest productivity and the most complete automation processes.
Saurer is also bringing customer service to the next level with SUN – SERVICE UNLIMITED to ensure maximum efficiency during the whole product life cycle. It has the latest innovations in components for both filament and staple yarn processing for optimum yarn quality and production efficiency.
Introduced as part of its philosophy of innovation and sustainability, Saurer’s E3 Label ensures that all the innovations take the essential customer demands into consideration; energy saving, efficient and waste-minimizing production, maximized productivity per m² used in mill and improved handling and ergonomics on all levels along with optimized material flow.
In order to ensure highest efficiency of the installed capacities throughout the machines lifetime, Saurer has also set out to establish new service standards for the entire textile value chain. At ITMA 2015 Saurer will be introducing SUN – SERVICE UNLIMITED – a bundle of differentiated services setting the benchmark in Consulting, Installations, Know-How Transfer, Original Parts, Maintenance and Repair as well as Updates and Upgrades. The SUN team at the machinery booth will explain the latest innovations in service.
Rotor spinning machines from Schlafhorst, setting new benchmarks
Schlafhorst will be presenting new rotor spinning machines that have been awarded the E3 label. They offer spinning mills a triple added value in the areas of energy, economics and ergonomics.
The revolution in rotor spinning continues. Schlafhorst will be presenting the next generation of the revolutionary Autocoro at ITMA 2015. The innovative single spinning position technology proves its technological superiority once again. Compared to the previous model, the new Autocoro uses much less energy. The savings are in a two-digit percentage range. Longer machines, higher rotor speeds, intelligent automated processes and minimized maintenance costs quickly increase efficiency, productivity and profitability. The next generation of Autocoro leaves the competition far behind and is defining a new benchmark for rotor spinning.
The BD 6 is in a class of its own. Equipped with patented high speed technologies from the Autocoro, it surpasses the qualitative and economic standards of semi-automatic rotor spinning machines which the market has known up until now. At ITMA 2015, Schlafhorst will be presenting a new, even more productive, energy-efficient and user-friendly generation of the BD 6. Take-up speeds of up to 230 m/min, two-digit energy savings, an LED signal system for fast checking and an ergonomic machine operation are some of the pioneering improvements. Schlafhorst is defining the new performance standard of the future in the semi-automatic area as well.
Schlafhorst will be unveiling the new Autoconer 6 to a large audience at ITMA 2015. The innovative winding machine has been available for delivery since the beginning of the year. The initial customers are positively impressed by its performance.
Schlafhorst will be presenting an updated generation of the new Autoconer which is even more energy efficient, economical and user-friendly. This is why the new generation was awarded the E³ label for triple added value in the areas of energy, economics and ergonomics.
Visitors to the exhibition will be able to experience virtually all of the conventional machine configurations and the entire textile technological application range of the Autoconer 6 in action. With a fully automatic link to the latest Zinser ring spinning machines and the currently most advanced automation solution, the Autoconer impressively proves its claim to leadership in the sector. The unlimited possibilities for process-oriented package optimisation, bobbin processing and rewinding will be demonstrated on a second machine.
We will be setting new standards for packages in the future, as the Autoconer 6 has redefined the performance criteria for quality packages. Autoconer 6 – the best original ever.
Zinser ring spinning machines, for cost-effective automation
Zinser will be presenting itself at ITMA 2015 as a pioneer of new cost-effective automation solutions for ring spinning. Its latest machines have the E³ label, the guarantee for triple added value in the areas of energy, economics and ergonomics.
Schlafhorst and Zinser will be exhibiting a fully-automatic linked system solution, from the roving frame to the winding machine. It is the perfect interplay of a highly integrated automation solution for the greatest possible energy savings, maximum economic efficiency and optimum user-friendliness.
With the Zinser CoWeMat and CoWeFeed doffing automation systems, the world’s most economic self-cleaning compact spinning technology Impact FX, and the proven cutting-edge technology for reliable and precise processes, Zinser is setting new standards with every machine length for yarn quality and profitability in ring spinning.
Schlafhorst is presenting the new service concept “SUN – SERVICE UNLIMITED” at ITMA 2015, and is setting a new standard in the sector with innovative service products.
The German textile machine manufacturer supports its customers in their day-to-day business like no other. Over 500 Service employees in 20 Service centers and 3 technology centers advise customers all over the world on questions relating to the increase of productivity, quality and energy savings. With their unique know-how, the service representatives help customers to overcome textile-technological challenges and ensure highest production quality. For the delivery of original spare parts, the Secos e-commerce platform guarantees the fastest response times.
Yet SUN does not only stand for the best service, but also for limitless innovation. Schlafhorst creates technical innovations that can be retrofitted in existing machinery. With improved original parts, modernisation kits, technology kits and service kits, Schlafhorst is taking on the responsibility of innovation for the entire product life cycle, and is ensuring that Schlafhorst and Zinser customers with older machine generations will always be able to benefit from technological advances.
Allma Volkmann competence in twisting
Allma and Volkmann will attract the attention of industry professionals with numerous technological innovations at ITMA in Milan. Technologies that generate even more customer benefits and set performance directions in the market: the guarantors for success are called the CompactTwister, CarpetTwister, CarpetCabler, Heat-Set and TechnoCorder TC2.
The CompactTwister, the high performance twisting machine for staple fibre yarns, was awarded the E³ label for triple added value in the areas of energy, economics and ergonomics. Energy savings of up to 40 per cent can be achieved with the eco-drive concept and the eco-spindle technology with adapted spindle combinations. The systematically integrated HD feeds are setting new standards for further efficient processing in the areas of energy savings and optimised feed weights.
The productivity of the CompactTwisters is 30 per cent higher, thanks to the high delivery speeds of up to 120 m/min. Operating costs drop due to the low energy, space and maintenance costs. The ergonomic benefits include greater ease of use due to the improved take-up geometry, central settings and handling aids, which result in an up to 10 per cent reduction in operating time.
The CompactTwister covers all yarn materials as well as count ranges, and with its high yarn and package quality offers the best conditions for optimal added value – today and tomorrow.
Volkmann is winning over customers with the new CarpetTwister and CarpetCabler product generation. The outstanding characteristics are the energy-saving spindle family and the maximum quality with optimum economic efficiency. Spindle and spindle pot versions as well as drive and storage technology enable very high energy savings of up to 40 per cent. With delivery speeds of up to 120 m/min during uptwisting, reduced space requirements due to smaller spindle gauge and the adaptation of the spindle speed, productivity can be increased by up to 45 per cent. Operating time can be reduced by up to 8 per cent, thanks to the pneumatic creel, threading aids, new pneumatic centrally adjustable creel yarn brakes and ball yarn brakes.
A new feature is the computer controlled drive system that enables a quick changeover to new yarn lots and the change of production parameters. This enhances the machine availability and simplifies operation.
After cabling, BCF carpet yarns are heat set in a second process step to stabilise the shape. Volkmann integrates this process step in the cabling machine – cabling and heat setting in one process run. Interim storage and handling are no longer needed at all, process costs are clearly reduced and a significant contribution to economic efficiency is achieved with the faster order turnaround times, shorter process sequences and greater system utilisation.
TechnoCorder TC2 offers triple-added value
The TechnoCorder TC2 was awarded the E³ label for triple added value in the areas of energy savings, productivity increase and ergonomic improvement. It is winning over customers with its independent spindle technology, 400 m/min delivery speed and the 25 per cent higher package density. And this pays off: productivity is up to 30 per cent higher and energy costs drop by up to 10 per cent.
The TechnoCorder TC2 is distinguished by attractive developments, such as the new FlexiPly equipment for production of hybrid yarns and the new larger 830 mm spindle spacing for processing of coarse yarn counts. Energy-optimised modern drives and a lean yarn balloon, thanks to the optimised balloon geometry and height-adjustable balloon yarn guide, lead to low energy costs.
The independently-driven spindles enable limitless possibilities for the creation of new twist constructions. Two spindle gauges cover a large range of yarn counts, from 235dtex to 33,000dtex. PrimePac quality twist packages can be manufactured according to individual needs. Compact twist packages save up to 30 per cent in transport costs and make further processing more efficient.
Special attention was given to the ergonomics, resulting in the independent spindle unit and new section concept enabling an ergonomically friendly spindle design. The operating elements and the entire spindle area can be easily accessed by the operating personnel. This saves set-up time.
Saurer Embroidery System Epoca 7
The gates for a new future of embroidery are opening at ITMA 2015. The newly developed Epoca 7 is setting standards for productivity, speed, embroidery quality and reliability. This is why the new generation was awarded the E³ label for triple added value in the areas of energy, economics and ergonomics.
In addition to energy savings of up to five per cent, the company customers can benefit from an increase in productivity of up to 20 per cent. The Epoca 7 achieves an embroidery speed of 700 rpm, and is thereby up to 18 per cent faster than the previous generation. Along with the increased production speed, other processes were optimized and improved to achieve the overall performance increase of up to 20 per cent.
Innovative solutions lead to unparalleled adjustment options and top quality production at the push of a button. A guarantor of this are also the new technologies on the needle side, such as the thread guide shut down, the newly developed thread delivery and the flat, wear-resistant yarn path. The new electronic yarn monitors detect yarn breaks quicker and more precisely. The new precise thread cut ensures trouble-free production of high-quality embroidery.
Modular and reliable components that are designed for high speeds with minimal wear are the foundation of the Epoca 7’s long service-life.
Saurer Embroidery is a total solutions provider and supports the embroidery process with qualitatively superior items and equipment, such as sequins, soutache, HeatCut as well as auxiliary machinery, accessories and conversions.
EmStudio – the embroidery software
The EmStudio CAD/CAM system integrates all the procedural steps from drawing, punching and visualization to production optimization, up to the analyses of the operating data and the archiving of designs on a platform. With the new iSed – the intelligent Saurer editor – the production and quality can be easily and efficiently optimized.
Components technology
Saurer Components will be introducing a new technology creating the yarn industry of the future. Accotex AccoSmart is a new sandwich cot based upon a completely new revolutionary technology platform. It has been developed from two individual tailor-made high quality elastomer layers; a softer inner layer and a harder outer layer. The cots feature a larger contact area compared to conventional soft rubber cots that results in an improved and stable yarn quality over the lifetime of the cot. Lifetime is long with less maintenance, less machine breakdowns and reduced costs.
Texparts Spinning Rings and Travellers provide superior performance due to the high-tech coating. During the short staple spinning process the system operates dry, which means that fibre debris from the yarn, along with natural fibre waxes like cotton pectin or spinning oil from manmade fibres, are accumulated on the traveller and ring system.
The ring coating includes a deposit function to support the lubrication effect, and an orange skin function to reduce friction. The traveller has one universal design to optimize the balance between the traveller speed, lifetime and yarn quality. Texparts Travellers are designed for all kind of fibre material with the two different coatings. Sprint or Marathon coatings are available for standard or high speed, special applications enabling reduced running-in time.
Texparts PK2600 Series meets Compact Compact systems of well-known suppliers found in the market can be retrofitted to the well-established weighting arms PK 2630 SE and PK 2630 SEH. The latter is a complete substitute of weighting arms for ring frames with hexagonal support rod. This means that the front roller load can be set optimally and fully independently from the nip roller load which provides no interference between nip and front top roller. As standard weighting arms are used there is no loss in the lapping reserve. The PK 2600 series can be installed on almost all machine types, so spinners can make use of all features of the well proven weighting arm and consequently improve yarn quality considerably.
More than six million spindles with Texparts Zero Underwinding (ZUW) systems have been installed worldwide consistently preventing excess underwound yarn ends. Air resistance and energy consumption are reduced and maintenance costs eliminated for the removal of excess underwound yarn ends that accumulate on the top parts of conventional spindles. Usually deployed for use with fine to medium yarn counts, there is a coarse count version designed for low speeds. A new yarn cutter has been introduced to provide long service when processing challenging yarn materials – such as Modal yarn. The new yarn cutter generation will be available in future for all yarn count ranges.
Saurer Components has 50 years of experience in the production of the industry’s leading shrinkage belt. Daytex Shrinkage Belts are engineered to produce the best quality for all different shrinkage applications. Daytex uses 100% premium pure natural rubber supplied by selected plantations to ensure constant quality. The belt is crack resistant under heavy loads and has outstanding heat and chemical resistance, which results in exceptional long life for all fabric types. Its unique homogenous belt structure yields constant shrinkage results during the entire lifetime of a belt, and a “Curved Edge” also improves the belt performance minimizing the risk of edge cracking.
Heberlein WarpJet provides time saving threading and energy efficient customized interlacing. The new updated WarpJet boasts performance improvements of between 10 per cent and 50 per cent, thanks to higher operating speeds, lower air consumption, and higher nip numbers. Its modular design allows a choice between a cost optimization or high-end performance solution. The full range of Heberlein jets will operate on the WarpJet in line with yarn size and performance requirements and the jet package insert of 32 ends is easy to mount and unmount for easy maintenance.
Heberlein KF Jet Insert provides knot-free air interlacing for false-twist texturing
The new updated KF Jet Insert guarantees there are no imperfections in the fabric such as pinholes, teardrops or stripes. It provides a 15% to 30% increased unwinding speed compared to non-interlaced yarn together with improved energy efficiency.
Heberlein PolyJet SP-2 HP provides high-performance air interlacing for filament spinning applications. The latest PolyJet has the full range of jet inserts for producing all yarns including finer denier ( The latest system, Fibrevison Fraytec FV2, boasts increased trigger optics with software selection of fault size. The broken filament faults are measured with fault size options available for 3mm, 4.5mm and 6mm from the yarn. It also has improved noise immunity and connectors, includes central optic for denier variation and interlace measurement, is capable of handling up to 12 end winders and allows integration with Fraycam 2.
Saurer Components will showcase the new Temco Covering Spindle type USU for 5.5” and 6.5” bobbins with a package weight of up to 2.5 kg. This universal spindle with a shaft diameter of 16.65 mm can cover the whole speed range of 0 – 30,000 1/min without restrictions. The new USU spindle is based on the durable and established USL spindle. The USU is feasible with spindle bores of Ø3 to Ø9 mm and also newly allows installation in a spindle rail bore of Ø42 mm.
Saurer Components will introduce the roller-bearing high speed Separator Roller Temco VR50300-00-HS. These separator rollers can be applied for a wide variety of spinning processes, and in the Hotbox with a max. yarn temperature of 190°C and a max. yarn speed of 5,500 m/min. Air bearing separator rollers can be replaced with these separator rollers, and the high compressed air costs can be saved. Thanks to integrated bearings in hybrid technology, the starting torque and frictional torque in operating speed are even lower than those of the air-bearing separator rollers, which are known for low friction.