Saheb Fibre Pvt Ltd took an unconventional route by venturing into the recycling of post-consumer PET bottles into recycled polyester staple fibres, diverging from the traditional path taken by cotton ginners in the Saurashtra region of Gujarat, who typically forward integrate by setting up spinning mills.
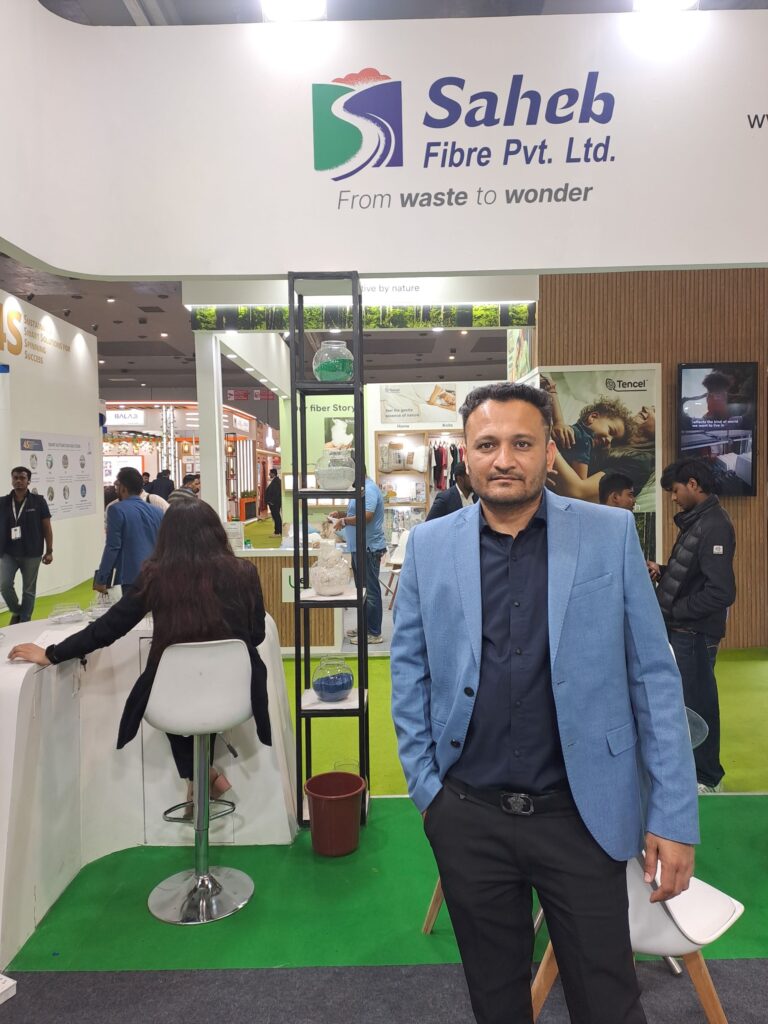
Mr. Sandip Patel’s family first entered the cotton trade in 2010 at the Rajkot Marketing Yard, marking their initial exposure to the cotton industry. After several years of trading, they decided to set up a cotton ginning unit in 2013.
Shifting Focus: From Cotton to Recycled Polyester
“With the establishment of the gin, our understanding of the textile industry grew. However, we soon realized that the cotton business might not be sustainable in the long run, so we explored other options, like setting up a spinning mill, as many cotton ginners in our region had already ventured into this area,” Mr. Sandip Patel, Director of Saheb Fibre Pvt Ltd said in an interview with The Textile Magazine.
“But with increasing environmental consciousness and consumers demanding more sustainable textiles and garments, we decided to foray into production of recycled polyester staple fibre. It did not require high capital investment and was in line with the growing trend of sustainability,” he added.
The Recycling Process: From PET Bottles to Polyester Fibres
The company sources post-consumer PET bottles through agents and brokers across various cities. Once the bottles reach the factory, they undergo a thorough cleaning process to remove any contaminants. The cleaned bottles are then converted into flakes, which are subsequently transformed into fibres of varying lengths.
Production Growth and Fibre Specifications
Saheb Fibre is an ISO-certified company and holds various compliance certificates, including BIS and Global Recycled Standard (GRS) and began its recycled polyester staple fibre production journey in 2024 with an initial capacity of 60 tons per day, which was expanded to 80 tons per day, employing around 550 staff members working in two shifts.
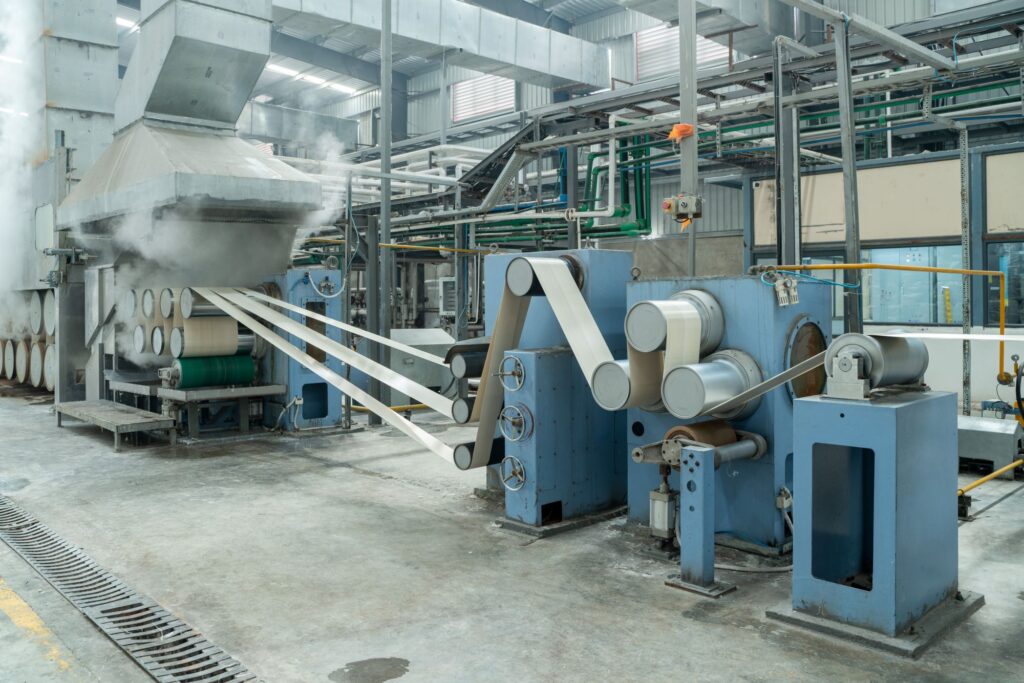
“We produce recycled polyester staple fibres in both gray and dyed forms, available in cut lengths of 28, 32, 38, 44, 51, and 64 mm, as well as deniers of 1, 2, 1.4, 2, 3, 6, 15, and 25. The tenacity of these fibres is below 6.35 grams per denier, and their elongation ranges from 18% to 22%,” Mr. Patel explained.
Environmental Impact and Sustainability
Mr. Patel emphasized the environmental benefits of their initiative, stating, “Producing 80 tons per day of recycled polyester fibres results in a reduction of 130 tons of carbon emissions per day when compared to producing virgin polyester fibres. Additionally, by recycling post-consumer PET bottles, we are preventing plastic waste from polluting the environment.”
Optimistic Future for Recycled Polyester Fibres
“The consumption of recycled fibres is steadily increasing, primarily due to growing consumer awareness of sustainable products. The European Union has also introduced new regulations that require textiles and clothing to be made from a larger percentage of recycled fibres. These factors combined point towards a bright future for the industry,” he concluded.
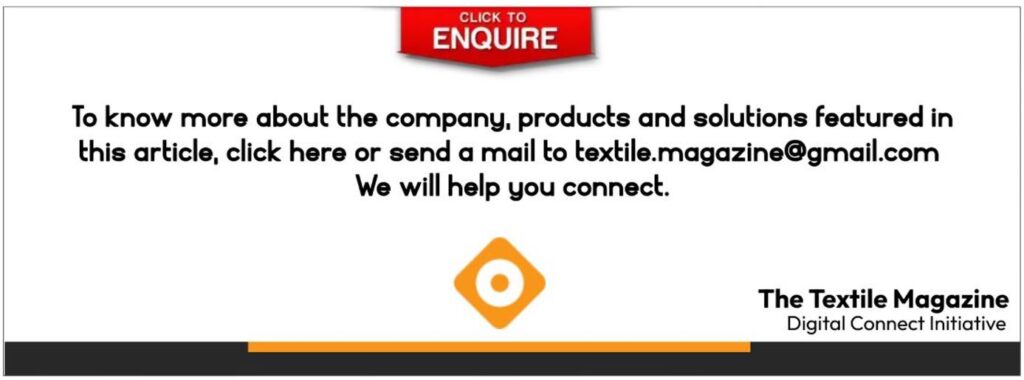