The Tirupur-based Spoorthi Technologies has emerged a front-runner in the highly competitive textile printing field. The company represents S.Roque, a leading Portuguese garment printing machinery manufacturer, in the country.
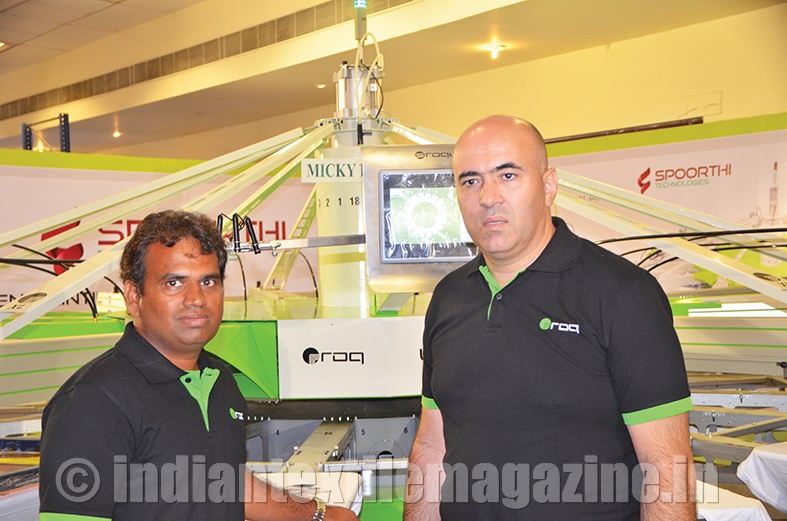
In an exclusive chat at the company’s booth at Knit Show 2015 held recently at Tirupur, Mr. Ramesh Ganduri, Managing Director, Spoorthi Technologies, said: “We are a 6-year -old company. We are distributors for the Portugal-based S.Roque. This is our main business. We have been distributing their automated garment printing machinery for the last five year now. The company is the exclusive distributor of S.Roque machines throughout India and has in the last five years installed around 300 machines, with 285 of these installations being in Tirupur and the rest in places like Ludhiana, Mumbai, Kolkata and Delhi.”
Talking about the huge market potential for automatic textile printing machinery, Mr. Ganduri pointed out: “The market has picked up over the last 2-3 years. For example, last year we sold 95 machines. Gradually the manual machines are being replaced for various reasons such as labour problems, poor productivity, lack of quality, etc. Exporters also want to bring down rejection rates. They have found that these machines help them tackle all these issues successfully. I feel that the market potential of India is 5000 machines per annum.”
Going into details about S.Roque, Mr. Ganduri said: “It is a 33-year-old company, considered an industry leader in automatic textile printing machinery. Ranked No.1 in Brazil, the company also have significant presence in markets such as Vietnam, Cambodia, Pakistan, Bangladesh, Romania, France and the US.”
According to him, high technology and user-friendliness give the company machines a competitive edge over others. There is no need for a skilled operator to run the machines. Even an operator running a manual machine can be easily trained to operate these automatic printing machines. The other advantages that these machines include usage of smaller frames instead of big frames, multi-print options, printing both front and back, etc. Added to this is the 24X7 after-sales support.
Spoorthi Technologies has an 18-member team, 16 of whom are technicians and the rest for marketing. The company has a sub-distributor in Ludhiana, while it directly handles the Mumbai, Delhi and Kolkata regions.
The company also manufactures waste water treatment plants for the printing industry. It has been manufacturing these plants for the last six months and has already completed 12 installations successfully. The ‘Ventil Aqua’ waste water treatment plants are meant for all types of printing and not only for textile printing. The company has plans to expand the product range.
Highlighting the specialty of the plant, Mr. Ganduri further said: “This compact machine works on the chemical coagulation concept. It is a fully automated machine, easy to install and operate. Only minimal labour is required to operate this machine. These are factors that make it ideal for the entire printing industry.”
Throwing light on another machine that Spoorthi Technologies has launched recently, Mr. Ganduri observed: “We have also launched an automatic dispenser for printing. We have already successfully completed our first installation in Tirupur. We are importing the machine from Golden Colors, a Taiwan-based company.”
Further, a software for the printing industry is in the preliminary stage of development.
He is also confident about the continued growth of the Tirupur market when he said: “The resilience of the Tirupur market is amazing. In the last 6 years I have been here the entrepreneurs have faced a lot of problems such as power cut, growing pollution, etc. Surprisingly the industry here has never slipped even one bit. Year-on-year exports have only been growing. It is a tribute to the hardworking nature of the entrepreneurs here. People here have realized the importance of latest technologies. They are investing into modernizing their units. Earlier, people were hesitant. We convinced them, supported them and offered them training. The results are there for all to see. There have been instances when after 6 months to 1 year of installation; people have come back to us wanting more machines. I know of units where 6 to even 10 machines have been installed.”