By Yvan Schwartz, Head Product Management Combing
The new Rieter combing set consisting of the E 36 OMEGAlap and the E 86 combing machine is the result of continuing development of the thousandfold-proven predecessor model.
The delivery speed of the OMEGAlap of 230 m/min, the quality-enhancing components of the E 86 comber as well as the set-production of 540 kg/h combed sliver are the outstanding performance features which Rieter presented at ITMA 2015 in Milan (Fig. 1).
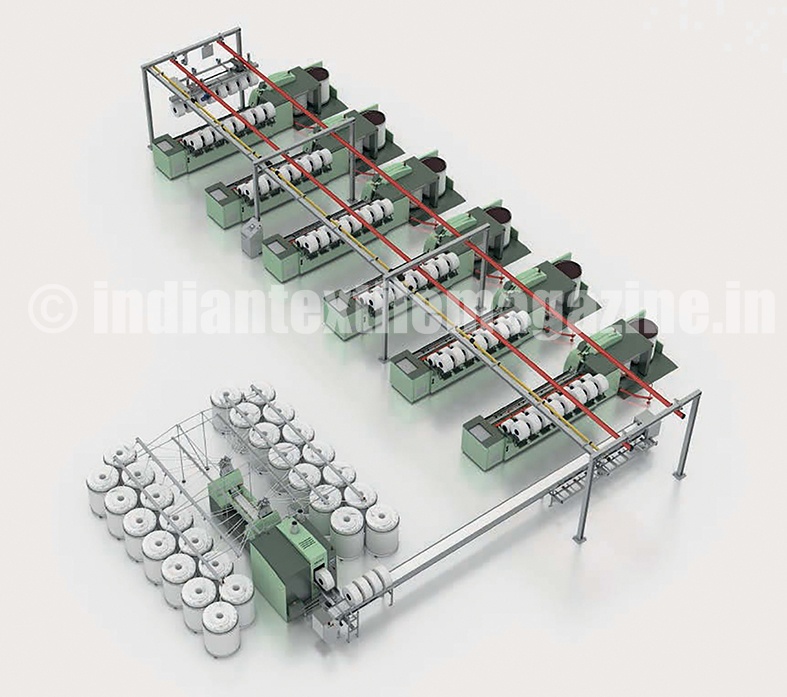
Since its introduction 12 years ago the OMEGAlap has maintained the highest production rate unchallenged in combing preparation. The E 36 OMEGAlap is the consistent development of this innovative product. The proven belt winding technology guarantees a gentle and uniform contact pressure over the largest possible lap circumference (270°). This system has been perfected over many years, so that a lap of the highest quality can be manufactured.
The OMEGAlap combing preparation supplies uniformly built-up laps with low hairiness and high lap weight combined with maximum production. The doffing time has been shortened and a delivery speed of up to 230 m/min is possible. That corresponds to a production of over 600 kg/h and a 50 per cent production increase compared to conventional combing preparation systems.
The E 36 OMEGAlap is the ideal combing preparation for maximum output and economy. At maximum comber production, an E 36 can supply the laps for 6 E 86 combers. For smaller sets, the E 34 OMEGAlap continues to be available.
With the latest E 86 comber from Rieter, well-known features have been retained and profitable features added (Fig. 2).
The customer therefore receives a combing machine that allows the best quality or the highest productivity on the market depending on the objectives.
The maximum output of the E 86 comber is 90 kg/h combed sliver (up to 540 kg/h set-production). The production of two tons per day is therefore significantly exceeded. The largest active circular combing area with an expansion of 45 per cent compared to the E 76 generation permits highest fibre purity and improved fibre parallelism. Optimally co-ordinated movement sequences lead to high nip rates with simultaneously gentle and controlled fibre treatment. The setting options on the E 86 comber allow the spinning mill to pursue either highest quality, maximum productivity or greatest raw material utilisation targets.
By using a 1,000 mm can diameter at the delivery of the E 86 comber, the manpower requirements can be reduced by 10 per cent as the cans have 75 per cent more storage capacity than the 600 mm cans. Consequently, also the efficiency of the comber and the draw frame increases because the number of can changes is halved. The drafting arrangement of the E 86 comber is improved by the addition of fibre-guiding components which reduces the number of clearer cuts in the yarn by up to 50 per cent. Furthermore, the calender module has been further developed, which ensures an optimal and compact combed sliver.
Full automation of a complete combing section allows a smooth 24-hour operation in the spinning mill and moreover reduces manpower to a minimum. For more than 20 years, Rieter has been the only successful supplier of a fully-automated combing section and has, over the years, perfected this.
Lap changing and piecing system ROBOlap
The ROBOlap removes the empty tubes, positions the 8 full laps and prepares the lap ends for the subsequent pneumatic piecing. With the fully-automated lap changing system ROBOlap, the efficiency of the E 86 comber is increased by about two per cent.
The quality of the automatic lap piecing device achieves a consistently high level over all 8 heads and is therefore better than manual piecing. Furthermore, the ROBOlap reduces personnel effort in the combing section, and production becomes less reliant on the operator. The ROBOlap is already being successfully used in more than 3,000 Rieter combers.
The lap and tube transport system E 26 SERVOlap transports full laps from a combing preparation system to the comber and returns the empty tubes from the comber. The laps are transported gently and prepared for the further process so that continuous high quality can be guaranteed. The worldwide use of the transport system in more than 20 countries has generated valuable experience by which the system could be steadily improved.
The manpower requirement of the fully-automated Rieter combing section with E 26 SERVOlap and ROBOlap is lower by a considerable 60 per cent than the manpower requirement of a combing section without automation (Fig. 3).
With the new combing set E 36 OMEGAlap and E 86 comber, Rieter supplies the highest set-production (up to 540 kg/h). Together with the over 20-year experience in combing automation, a completely autonomous combing unit has been created with either maximum production, highest quality or greatest raw material savings.