Rieter creates value for customers by system competence, innovative solutions, excellent aftersales service and global presence. For the key issues related to competitiveness of spinning mills, the company will be offering value-adding innovations at ITMA 2015. Internet usage for optimising the entire system, new machine generations for preparatory and end spinning as well as corresponding spareparts, aftersales services and solutions for the optimal use of the spinning mill along the entire product life cycle will be shown in a big way.
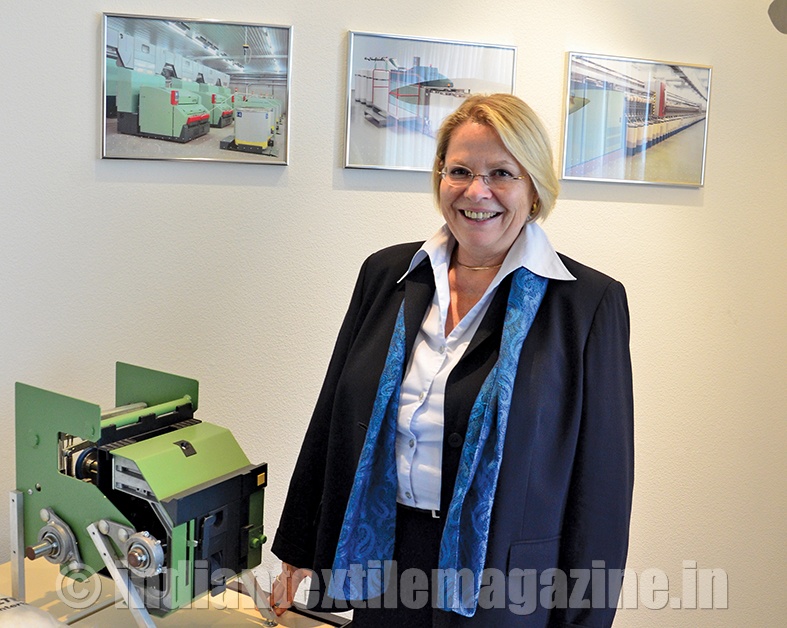
Investments in Rieter systems and machines are extremely attractive. The complete range offered by Rieter enables production of a consistent yarn quality with optimal cost effectiveness. Rieter systems and machines are durable and, with Rieter retrofits, remain competitive for a long time. However, Rieter offers even more.
Comprehensive know-how from fibre through yarn to the finished textile is the basis for innovation and ongoing optimisation in a spinning mill. Rieter supports customers from the initial investment discussions to the successful operation of their spinning mills and over the whole product life cycle. Alongside valuable systems and convincing technology, the company also offers the customer a supportive partnership.
Rieter’s innovations at ITMA 2015 offer high and, above all, consistent yarn quality, reduction in the manufacturing costs, increase in the raw material yield, decrease in energy consumption, and increased flexibility to respond to market changes.
All the three business groups are showing their product and service innovations for complete systems, spinning preparation and end spinning process under their trademarks Rieter, Bräcker, Graf, Novibra and Süssen. Highlights are the extended SPIDERweb Mill Control System, an important step applying the “Internet of Things” for optimising the spinning mill, the new E 36 / E 86 combing set, the new R 66 rotor spinning machine and the J 26 air-jet spinning machine with the Polyester option P 26.
The Business Group After Sales is presenting innovative spareparts and conversions packages as well as aftersales service offerings which maintain the competitiveness of Rieter systems, reaching from technology support over maintenance audits and repair services to customer training. In addition, Rieter After Sales offers end-to-end mill solutions leveraging on the group system supplier expertise.
Bräcker, Graf, Novibra and Süssen are presenting components for the manufacture of high quality yarns. These are for example represented by the STARLETplus traveller and the FlexComb circular comb.
SPIDERweb Mill Control System
The Rieter SPIDERweb Mill Control System is the only system on the market which uniformly covers the entire spinning mill from fibre to yarn and for all four spinning technologies, not only for new machines but also for older generations. SPIDERweb serves economic decisions in the spinning mill. The system is configurable for individual requirements. It stores and monitors the quality and production of all Rieter spinning systems. Subsequent enhancements can be upgraded. This safeguards the investment in a modern spinning mill.
For the first time, Rieter is showing a mobile solution that not only provides an overview of the data of the spinning mill, but also offers a configurable alarm function.
SPIDERweb opens the door to an Internet-based, intelligent spinning mill control. The system offers following advantages like permanently monitored sliver and yarn quality, incorporated expertise, optimal allocation of operating personnel, support for systematic preventative maintenance, fact-based and quick reaction to deviations, and increase in plant availability and productivity.
SPIDERweb will give visitors to the exhibition stand at ITMA an insight into the spinning mill of the future.
Since the beginning of this year, Rieter has strengthened its aftersales service offering by a third dedicated Business Group. The objective is to support customers over the entire product life cycle and to improve their long-term competitiveness. Rieter is presenting new aftersales service products at ITMA.
The expert teams from the group offer spinning mill audits which identify feasible short-term opportunities for improvements and create measurable results for customers. Globally located repair and maintenance centres enable customers to optimally maintain their machines. Thanks to the continuous training of personnel, Rieter offers the best possible support for the customers.
Rieter demonstrates know-how with thousands of various fabric samples which the teams from After Sales use to discuss the plans and objectives with the customers and seek solutions, always focusing on their needs, markets and opportunities.
Spinning preparation innovations
The C 70 high-performance card achieves excellent yarn quality at highest production rates for all yarn applications. Rieter controls the carding gap by means of precise flats guidance and with the working width of 1.5 m achieves the largest active carding area on the market.
Innovations in the pre- and post-carding zone facilitate a very specific waste selection and thus an excellent raw material yield and sliver quality.
The new, very easily removable web bridge in a special package for the processing of synthetic fibres allows trouble-free cleaning and an immediate restart of the card. The second function of the package is the unique chute control with air pressure, which simplifies the processing of synthetic fibres. This enables the C 70 card to achieve high carding performance with synthetic fibres and, as a result, good running properties in spinning.
The innovative flat cleaning unit EVObrush of the latest card generation can also be retrofitted on older models. Its clothing can be replaced without the use of tools, reliably keeps the wire clothing clean and improves sliver quality.
New E 36 / E 86 combing set
The new combing set achieves the greatest productivity on the market. It consists of a new combing preparation machine, E 36 OMEGAlap, which is able to feed six new E 86 combers. With 540 kg/h and therefore the supply of almost 25,000 ring spindles, the set reaches the highest production volume on the market.
A new function simplifies setting and optimisation of the noil rate. This is made possible by the new FlexComb circular comb from Graf.
Rieter has the widest experience and range of solutions from simple to full automation in the combing sector. With automation, the customer can reduce the number of operators and simultaneously increase efficiency and yarn quality.
For older generations of combers, Rieter offers conversion kits that improve the productivity and yarn quality and make a reduction of the noil rate possible. At ITMA 2015 Rieter is demonstrating how quickly such a conversion can be realized and what economic advantages the customer gets.
All autoleveller draw frames from Rieter use the same dynamic autolevelling system for incomparable sliver uniformity, even at high delivery speeds of 1,100 m/min.
The ECOrized suction system on the new RSB-D 24 double-head autoleveller draw frame lowers the energy consumption. Older draw frame generations can also be retrofitted with this system.
A sliver sensor, patent pending, makes a high quality in sliver coiling already possible from the first metres following a can change. The practical setting of suction and delivery speed on the display, as well as the option of individual maintenance of the two heads, increases the level of convenience for setting and operating the machine. Together with the SB-D 22 double-head draw frame without levelling, a double-head line requires 50 per cent less space and therefore, compared with a line of single-head draw frames, also reduces costs.
End spinning process innovations
The success of the R 60 automated rotor spinning machine in recent years lies in the good yarn tenacity and low yarn manufacturing costs. Contributory factors are the low energy consumption and easy operation. At ITMA, Rieter is presenting the new R 66 rotor spinning machine which makes yarn production even more economical.
A higher yarn production per square metre is obtained with longer machines. Rieter now makes a length of up to 700 spinning positions possible. The new machine length reduces the costs for the entire rotor spinning system.
The S 66 spin box is the heart of the new R 66 rotor spinning machine. Compared with the S 60, the S 66 achieves higher speeds for improved economy and at the same yarn tenacity and yarn uniformity. The new replaceable CHANNELpass simplifies the optimisation for different raw materials.
The new electro-mechanical yarn traverse simplifies the setting of the winding angle for a wide range of applications, for reliable package flanks and good unwinding behaviour.
The existing rotor spinning systems are now modernised for synthetic fibres and higher speeds. With the ANTIstatic TWINdisc, the CHANNELpass, the clip-on opening roller or complete sets for box modernisation, Rieter offers solutions that allow a quick response to the changing market requirements. Time and energy savings as well as production increases lead to a better return.
J 26 Air-Jet Spinning Machine
With the J 26, Rieter extends the application range for air-jet technology and presents an additionally optimised machine.
With the processing of polyester, the challenge lies in the deposits of spinning finish and co-polymers. For this reason, Rieter now offers the option P 26 which significantly extends the time between the necessary cleaning operations.
A new option is the application of six robots on the machine. This allows applications which imply a higher rate of ends dow n or quality cuts to be processed.
A majority of air-jet yarns are later processed to knitted fabrics which require a softer touch. To this end, Rieter has developed technology components and setting parameters.
Rieter has for many years successfully used the Q 10 A yarn clearer in rotor spinning. Now it has been further developed for air-jet spinning. Based on an accurate monitoring of yarn structure, hairiness and yarn diameter, it interprets not only the standard functions but also the yarn tenacity.
K 46 Compact Spinning Machine
With 1,824 spinning positions, the K 46 Com4 compact spinning machine increases production per square meter in the spinning mill. The Rieter system range enables optimal machine layout and process workflows from the fibre to the finished yarn, even with these long compact machines.
Rieter now offers a quality package for the K 46 that leads to a significant improvement of the quality parameters CVm and IPI. It is an ideal supplement for spinning mills with high quality requirements.
Energy consumption per kilogram of spun yarn from the Rieter compacting system with suction drum today already lies far below that of apron systems. The new double-sided suction system ECOrized for long compact spinning machines now additionally reduces energy consumption.
G 32 Ring Spinning Machine
The G 32 ring spinning machine is, similar to the G 36 ring spinning machine, a guarantee for economically produced ring yarns. Now available is the revised G 32 ring spinning machine with a maximum length of 1,824 spindles and with the innovative suction tube ECOrized. In addition, a quality package for improvement of the yarn quality, a flexible change between S and Z twist and a special package for the processing of Polyester is available. The best fit for this package is the new traveller STARLETplus from Bräcker.
The G 32 ring spinning machine can now be retrofitted with the suction tube ECOrized. This also applies to the machines G 33, G 35 and G 36. Conversion with the suction tube ECOrized ensures sustainable energy and cost savings.
Rieter is the world’s leading supplier of systems for short-staple fibre spinning. Based in Winterthur (Switzerland), the company develops and manufactures machinery, systems and components used to convert natural and manmade fibres and their blends into yarns. The company is the only supplier worldwide to cover spinning preparation processes as well as all four end spinning technologies currently established on the market. With 18 manufacturing locations in 10 countries, it employs a global workforce of some 5,150, about 23 per cent of whom are based in Switzerland.