On its exhibition stand at the ITME 2012, Rieter will be demonstrating its competence across the entire spinning process and presenting all 4 end spinning systems. Large 1 000 mm cans can now be utilized in the Rieter fiber and spinning preparation from the card to the comber, ensuring higher efficiency and convenience in the spinning plant. Showcased on the stand will be the new air-jet spinning machine J 20, the new Rieter comber E 80 and the new draw frame SB-D 22.
The know-how relating to financing, spinning mill planning, use of the right technological elements, selection of the correct spinning process as well as many other factors is necessary to achieve success in the operation of a spinning plant. Rieter will be presenting all this expertise at ITME.
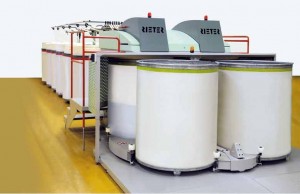
What the benefits and characteristics of the 4 spinning systems mean for downstream processing can be experienced by visitors in the technology showcase. Here end products and fabric samples of the 4 Rieter yarns are available.
The main company exhibits are:
E 80 Comber: This comber meets the highest standards in terms of productivity, quality and economy together with a high degree of flexibility. The effective production performance of the E 80 comber, in combination with the fully automated ROBOlap piecing system, is 2 tonnes/day. The lead in combing technology has been extended further through C•A•P•DQ (Computer Aided Process Development). With outstanding fiber selection and optimal machine running behavior, the comber achieves superior quality values with maximum economy. The mill-proven ROBOlap fully automated lap changing and piecing system is a unique feature and still sets the standard for modern combing operations.
SB-D 22 Double-Head Draw Frame: The SB-D 22 double-head draw frame without autoleveling guarantees maximum machine efficiency with a unique can changer up to 1 000 mm. The machine concept is labor- and space-saving. At delivery speeds of up to 1 100 m/min the mill-proven Rieter 4-over-3 drafting system ensures outstanding yarn quality.
Unique centralized drafting system setting and easy modification of the delivery speed on the display panel also enhance customer benefits. Energy consumption is some 20 per cent lower than for other manufacturers’ machines.
1 000 mm Cans from the Card to the Comber: Large 1 000 mm cans can now be utilized in the Rieter fiber and spinning preparation from the card to the comber. The number of different cans in the spinning mill can thereby be reduced, which keeps the investment costs low. Thanks to larger can sizes, the operator time is reduced and the yarn quality improved as a result of the lower number of sliver piecings. The impressive size of these large cans can be seen at the E 80 comber and SB-D 22 draw frame – both will be equipped with a 1 000 mm can changer.
J 20 air-jet spinning machine: The J 20 air-jet spinning machine features up to 120 high-production spinning units. The J 20 can be equipped for separate production on both machine sides, i.e., two different yarn qualities can be spun simultaneously on one machine. In conjunction with the newly developed spinning unit, the J 20 offers maximum yarn quality, productivity and flexibility. The unique quality characteristics of the air-jet spun yarn are reflected in the benefits for spinning mills, downstream processors and end users.
SPIDERweb mill monitoring system: Rieter has developed an innovative information and data collection system in the shape of SPIDERweb. Machines and the data system come from a single source and are ideally coordinated with each other. Due to the modular structure of SPIDERweb any number of machines can be connected, from blowroom to spinning installation. The open-ended network enables additional machines or SPIDERweb workstations to be connected at any time. SPIDERweb collects comprehensive data that provide an ongoing basis for increasing output and enhancing quality.
Rieter supports customers in the choice of the right spinning process by its comprehensive technological expertise in all four spinning processes through to the textile end product. At the exhibition, Rieter provides information on the benefits of the 4 Rieter Com4 yarns by means of various end products and fabric samples.
A reliable partner supplying a complete range of wearing, technology and standard parts. Original spare parts from Rieter ensure optimal working behaviour, smooth operation and additional security. Innovative developments plus high-quality products subjected to rigorous controls and checks enable Rieter to meet customers’ most stringent safety and production requirements. Furthermore, Rieter’s local warehouse facility will enable customers to plan their requirements and ensures quicker delivery.