Demand for the Autoconer X6’s new open prism technology is accelerating across markets globally. The open prism OZ2 covers a wider application range and is a gamechanger for spinning mills. This new technology can process standard, elastic and multi-core yarns based on improved splice quality and splice process.
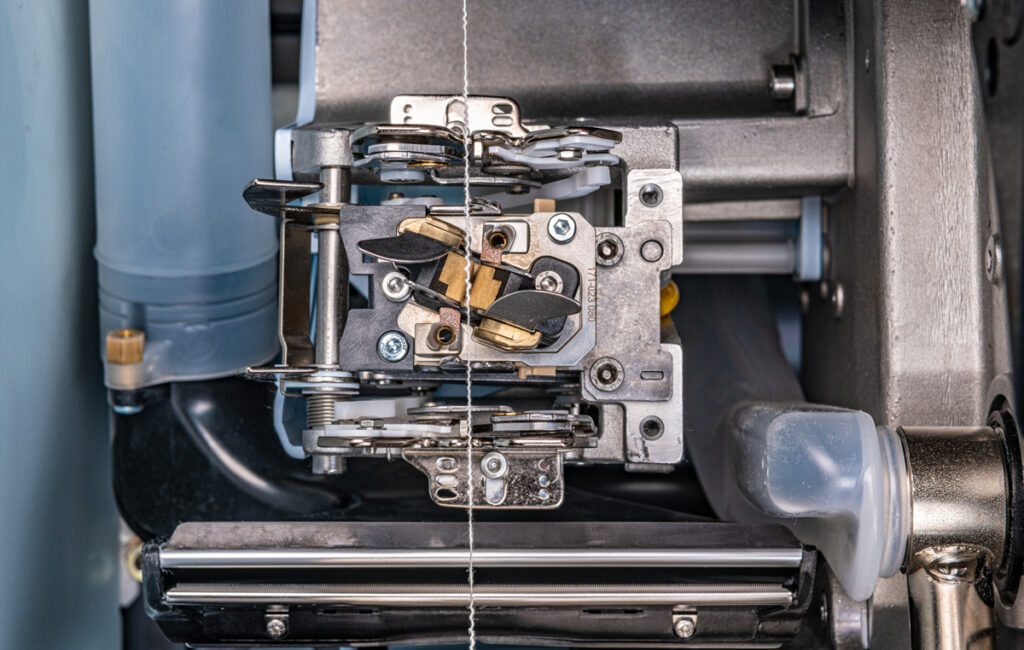
The open prism splice technology is designed to cover nearly the complete material and yarn spectrum with a minimum number of prisms. Having started with applications limited to single yarns made of 100% cotton and blends with more than 30% cotton, the material range was rapidly expanded in the last two years due to intensive technological testing.
Now spinning mills can cover the entire spectrum of cotton yarns and cotton blends with the open prism technology. In addition, elastic yarns in a wide variety of material combinations consisting of cotton, polyester, viscose, and blends as single, duo or multi-core yarns are possible.
The prism OZ1 is recommended for yarn count Ne 30 to Ne 120 and finer. With the all-new OZ2 prism, customers can widen the application range down to Ne 4. Because of its versatile application in coarser yarn count ranges, the prism OZ2 is particularly well-suited and recommended as an all-rounder for duo or multi-core yarns.
Rieter customers can take an application-oriented decision: spinning mills which focus on a yarn count range finer than Ne 30 and process cotton yarns, cotton blends or cotton-elastane blends select the standard version OZ1. For spinning mills with the widest application ranges and with different yarn structures and material combinations (cotton, polyester, elastane, viscose), Rieter recommends the optional prism OZ2 (Fig. 1).
Special advantages in the denim yarn spectrum
The production of modern denim fabrics requires both coarse single yarns and highelastic core yarns, such as single, duo-core or multi-core yarns, with very different material combinations. This is where the open prism technology is unique and unbeatable: all types of yarns can be processed with one splicing system. Customers can easily switch between elastic and standard yarn processing. The splicing parameters are almost the same. This is a big advantage compared to competitor splicing systems which have limitations in terms of universal applicability.
Dry splicing or splicing with minimum water
For a very large variety of elastic yarns dry splicing is possible and will lead to yarnlike splice results (Fig. 2). For applications which need highest yarn strength and thus splice strength as well (average splice strength > 90-95%), the use of a very small amount of water is recommended to be on the safe side. Due to a minimized amount of water, drastically less cleaning is required. The splice process itself is more stable, while the fault rate and number of splice cuts are reduced to a minimum.
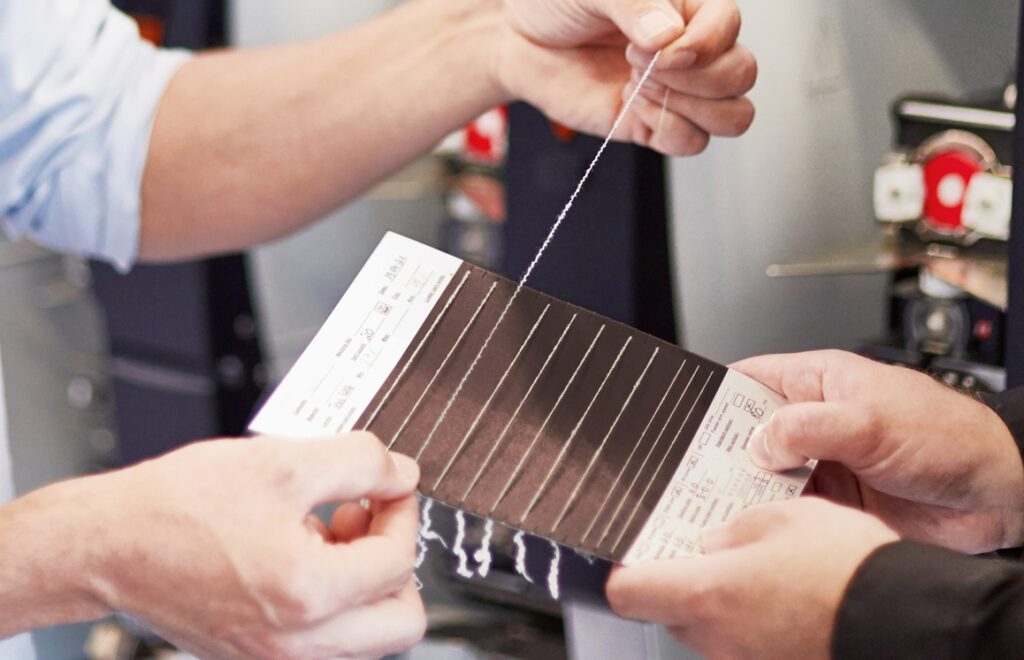
Open prism technology guarantees elasticity of the splice zone right through to the finished fabric including dyeable splice joints for uniform dyeing process and embedded elastic filament ends. This results in reduced splice failure rates in weaving and knitting by approx. 50-70% and, thus a higher quality of the finished products.
The universality of the Autoconer splice technology makes the use of the innovative open prism splice technology not only possible for new machines but it can also be retrofitted on all machine generations down to the Autoconer 338. In future the application range of the open prism splice technology will be expanded to S-twisted yarns with the prism OS.
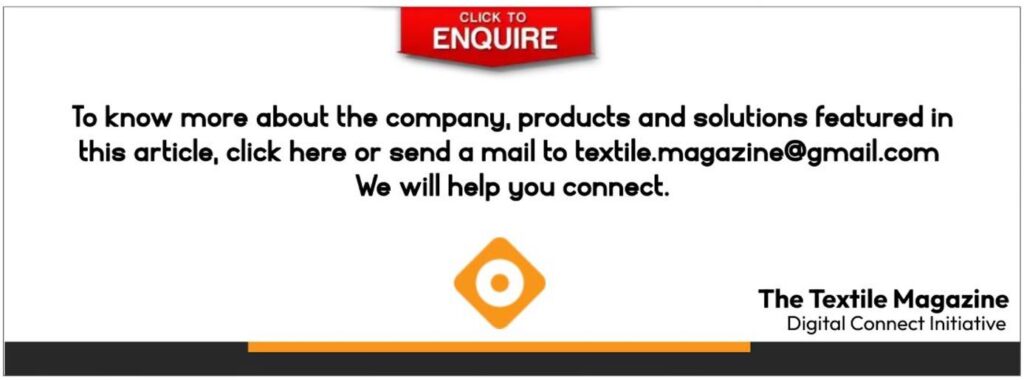