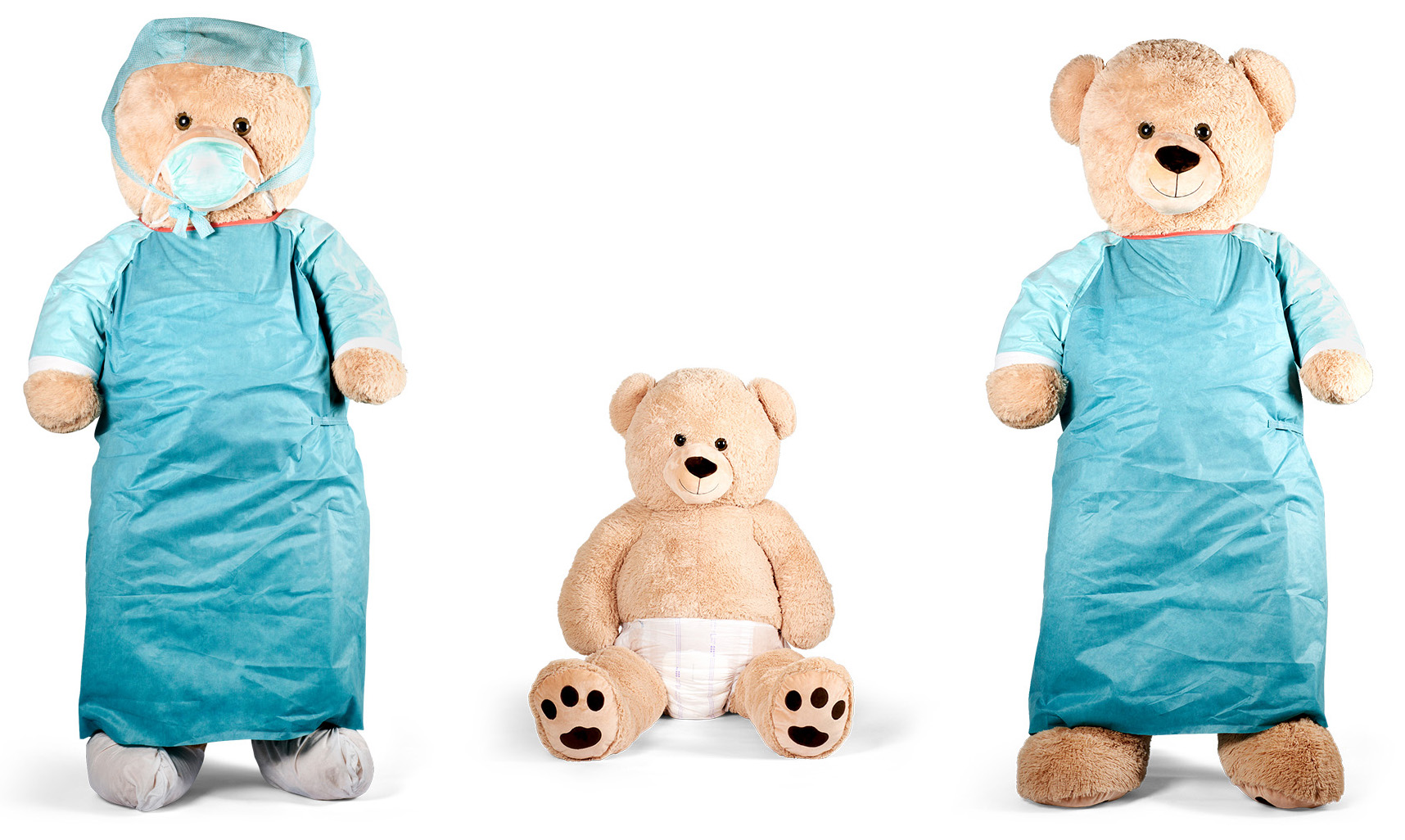
The leading manufacturer of nonwoven lines Reifenhäuser Reicofil – a business unit of the Reifenhäuser Group – is presenting its new RF5 XHL production platform for the first time at the leading international nonwovens trade fair INDEX 23 in Geneva (booth 1531) from April 18 to 21.
The suffix XHL stands for Extra High Loft. RF5 XHL is the evolution of the proven RF5 technology, targeted at super soft and drapeable nonwovens for the hygiene industry. “Thanks to highly crimped fibers with reduced fiber size, our XHL nonwovens offer a new level of quality with super soft touch for nonwoven products made from them – such as top sheet and back sheet,” explains Markus Müller, Vice President Sales & Marketing of the Reifenhäuser Group. “At the same time, we achieve a huge improvement in the carbon footprint of up to 30 percent thanks to reduced resource use.”
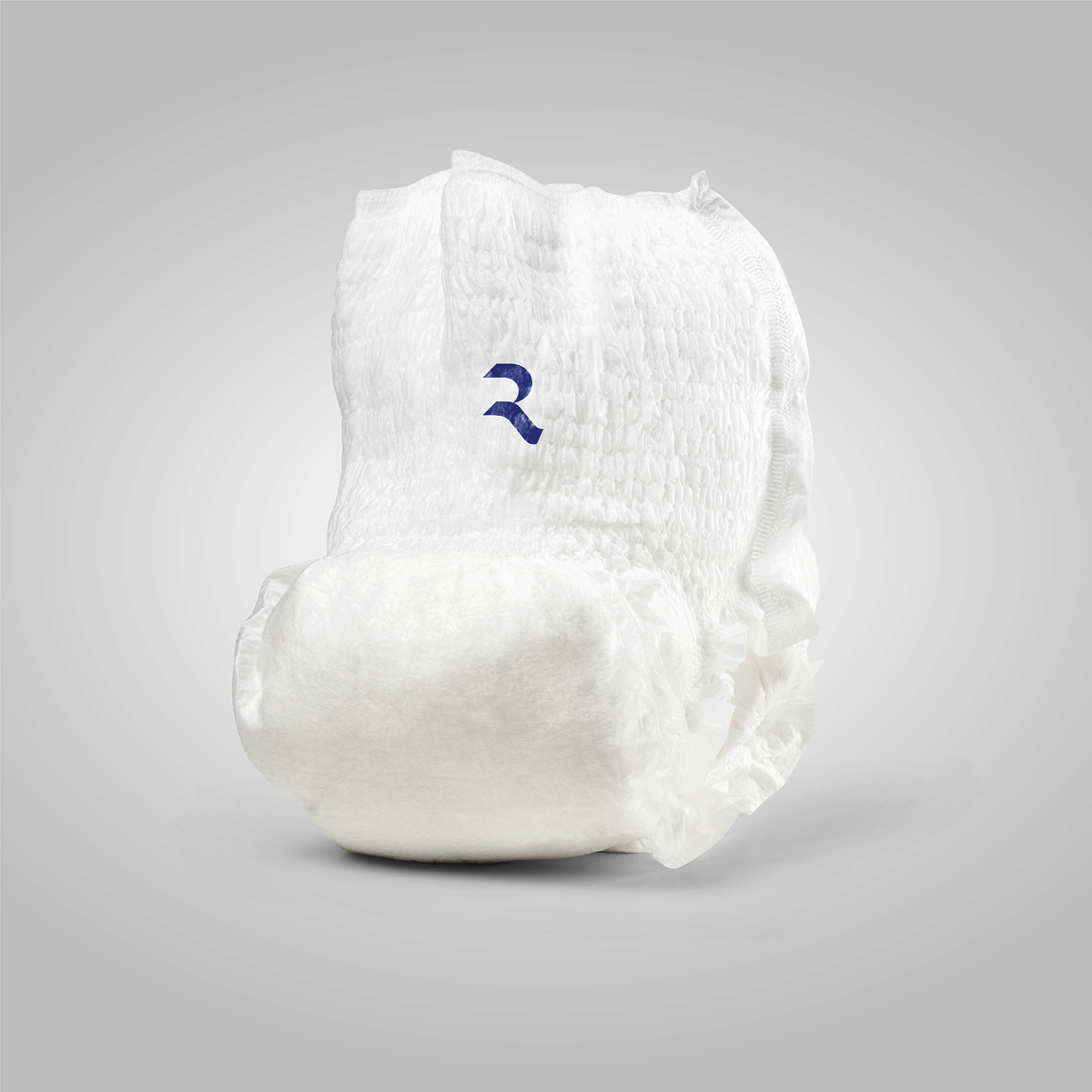
The RF5 XHL technology relies on the specially patented BiCo process. This combines two different raw materials in one fiber in the spunbond process, creating a bimetallic effect and optimally crimping the fiber. This results in a weight reduction of up to 25 percent for fiber sizes at 1.0 denier. At the same time, thickness increases by up to 30 percent compared to state-of-the-art material.
The new RF5 XHL lines are also equipped with particularly energy-efficient components, enabling resource-saving nonwoven production at high line speeds. To reduce production waste to a minimum, all raw materials are made of polypropylene (PP), for simple and efficient inline recycling. In contrast, common mixed-material fabrics made of PP/PE or PET/PE are very difficult to recycle. In addition, to meet the ongoing demand for more sustainable nonwoven products, RF5 lines also process bio-based raw materials on request.
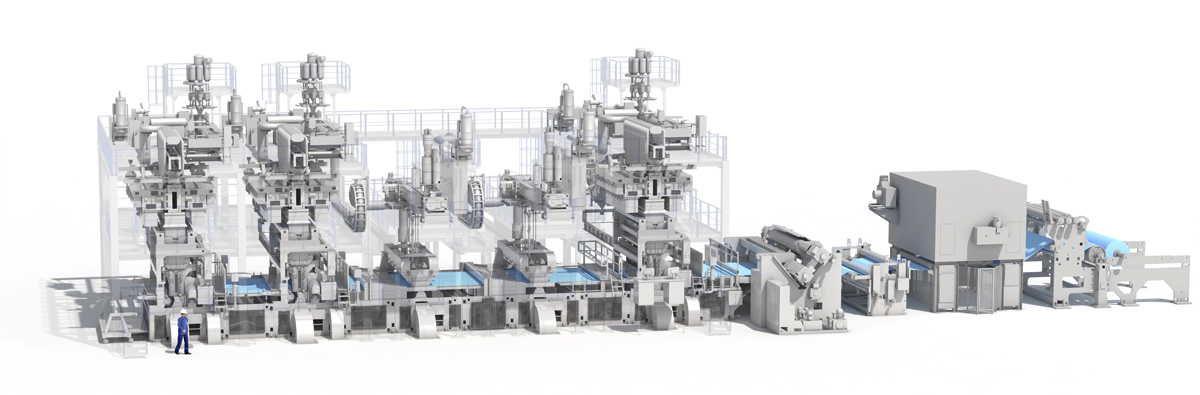
Smart digitalization increases production efficiency
With c.Hub, the new data connection platform of the Reifenhäuser Group, Reicofil offers its customers a digitalization solution that is consistently tailored to the requirements of nonwovens production. Customers have the possibility to securely network the data of their Reicofil lines, peripherals as well as ERP and MES systems via the c.Hub middleware, to store it centrally for easy analysis. Line operators can thus monitor and document their production and increase production efficiency based on data. Coming with various software bundles, c.Hub is offered as an on-premise solution, i.e. it can be operated locally and remains under the full data sovereignty of the user.
Enka Tecnica presents wide range of replacement components for spunbond, meltblown and composite lines
The Reifenhäuser Group business unit Enka Tecnica, specializing in spinnerets and high-end micro-components, is presenting its wide range of replacement components for spunbond, meltblown and composite lines at INDEX 23 in Geneva (Booth 1531). The highly specialized custom manufacturer offers economical high-end technology “made in Germany” that is 100 percent compatible with all globally installed lines, regardless of manufacturer.
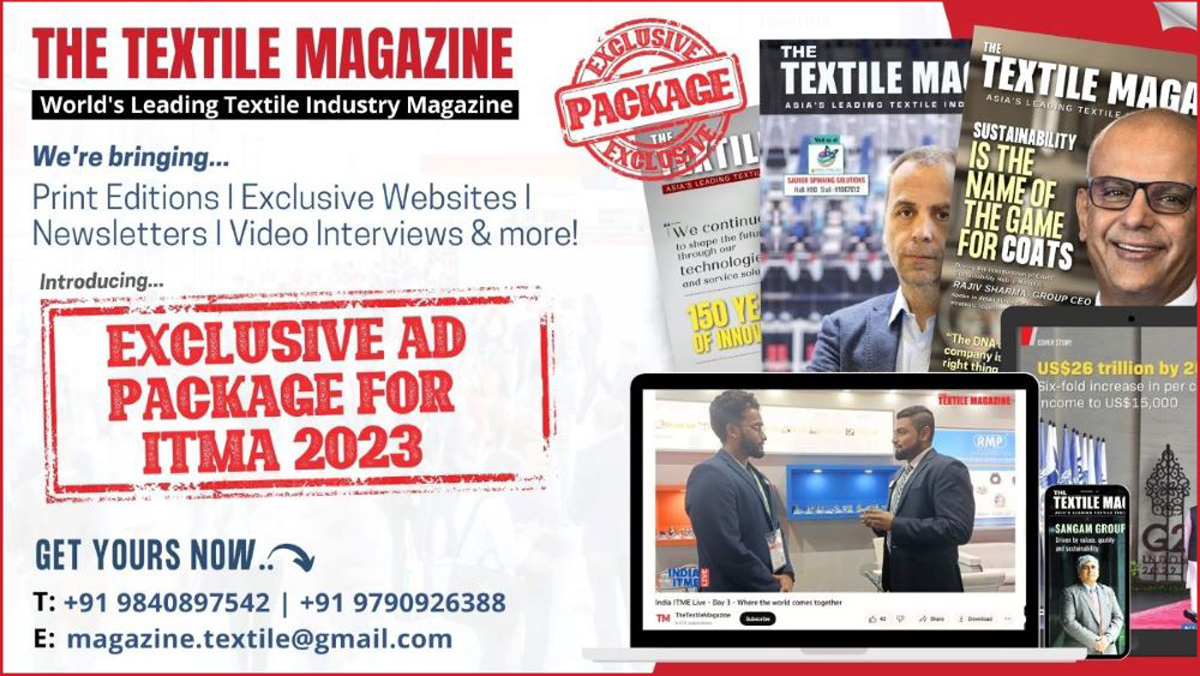
Producers of nonwovens worldwide rely on Enka Tecnica components to manufacture products for complex applications in hygiene, medical or filtration to provide them with access to new profitable markets. Trade-show visitors will gain a detailed insight into the entire range of products, from meltblown and spunbond spinnerets to meltblown cassettes and complete meltblown spinning beams designed with an energy concept optimized for sustainability. The outstanding quality of die tips and capillaries assures consistent product quality and precision, allowing producers to meet their tolerance specifications reliably and avoid scrap at the same time.
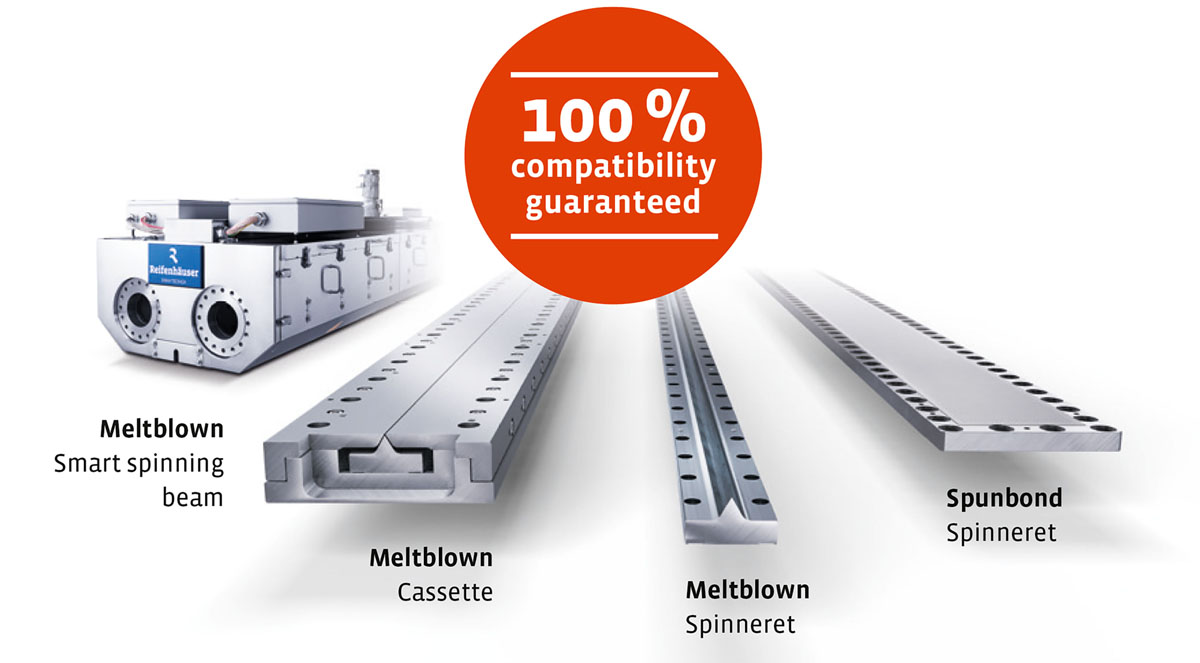
“Enka Tecnica’s unique selling point is its multi-vendor approach. All our components are custom-made providing hundred percent compatibility with the respective line,” explains Wilfried Schiffer, Managing Director of Reifenhäuser Enka Tecnica.
With its refurbishment service for used components, Enka Tecnica not only offers a cost-efficient alternative to new parts, but also extremely fast delivery times, a factor that is often decisive to maintain daily production targets. Visitors to Geneva will be able to see the quality of refurbished components displayed at the booth – a meltblown and a spunbond spinneret, half of which has been refurbished. They will be able to see the condition of the capillary holes before and after the refurbishment through a microscope.