The R 66 rotor spinning machine with ECOrized makes a further energy saving about 10 per cent possible compared to the previous model R 60. The R 66 with ECOrized and a length of up to 700 positions offers further advantages with respect to the yarn quality, productivity and economy.
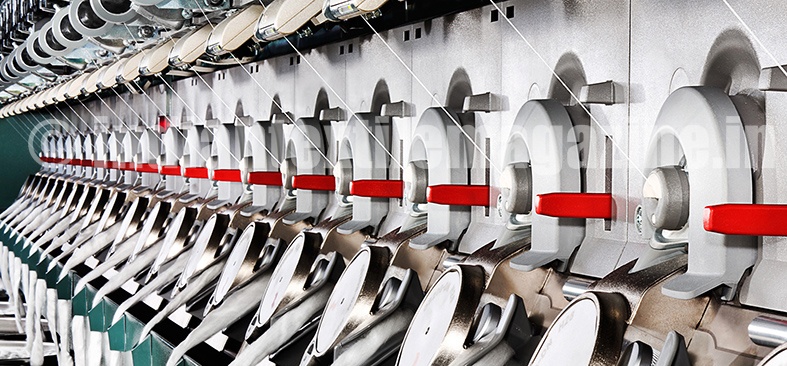
The R 66 was developed as a highly efficient machine, using the latest spinning technology for best spinning stability (Fig. 1). The high productivity and low energy consumption have now been supplemented by innovations for an additional, significant energy saving. The R 66 has proven itself not only by its very simple operation and maintenance, but also by its robustness and high reliability. Per machine, EUR 15000 and more can be saved. Up to 10 per cent energy savings for all applications also possible.
The savings with ECOrized are equally attainable for all applications. That has been shown by calculations and measurements with various applications: coarse Ne 12 yarns and fine Ne 30 yarns for knitting as well as for weaving yarns (Fig. 2).
Based on the individual energy costs, for each machine, EUR 15000 and more can be saved. The innovative equipment of the R 66 with ECOrized leads to a significant energy saving. It consists essentially of three components: Double sided suction, which has already proven itself over a long period of time on the Rieter compact spinning machines. Energy-efficient drives, developed in collaboration with a leading European motor manufacturer. Optimised software for machine control minimal energy losses by optimised air guidance.
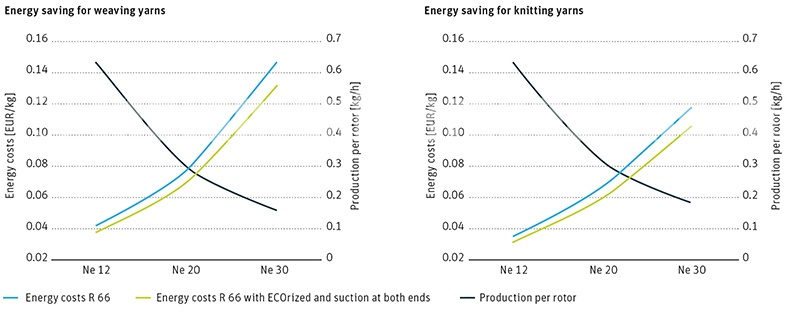
The longer the rotor spinning machine, the higher the influence of the spinning air on the energy consumption. With shorter machines, the aerodynamically designed suction duct of the R 66 with its optimised cross section ensures highest efficiency.
The ideal suction duct already represents a considerable advantage over other rotor spinning machines. Added to this is the advantage of unique automatic filter cleaning and the low spinning vacuum requirement for the spin box.
With longer machines, the R 66 is now available with the well-known, highly efficient suction from both machine ends. Consequently, flow losses are negligible also with this length and on all spinning positions – near to and far from the suction – equally good spinning conditions prevail.
Suction on both machine ends
The long model of the R 66 with ECOrized, independent sides and suction at both machine ends, offers further unique advantages along side the high energy efficiency:
Organization of the machine like two independent machines: independent operation of both machine sides, from the tube loader up to the package take-off; even maintenance and cleaning is possible on one side while the other side is in production.
Optimised logistics – the material allocation with one lot per machine side is clear and ideal for a reliable and automated package take-off. Each of the two tube loaders has sufficient capacity for its side and supplies the empty tubes to the robots in the quickest way.
Energy-efficient drives
The machine concept of the R 66 has advantages with the air-conditioning of the spinning mill. The heat that is generated by losses in the drives and electronic components can be far more easily led out of the spinning room, as with the R 66 its creation is concentrated at the head and foot sections of the machine. More efficient drives at this position also means less heat that must be discharged – even a double saving. Finally, the lower heat load with the R 66 also positively influences the lifetime long-term – in particular for the electronic components – and thus keeps the manufacturing costs low.
The most important influencing parameter is the spinning technology of the R 66. The potential for higher yarn tenacity with better yarn characteristics from the same raw material frequently permits a lesser yarn twist.
A five per cent lesser twist means a five per cent higher productivity, without higher energy consumption of the machine. That means five per cent lower energy consumption per kilogram of produced yarn.
By Stephan Weidner-Bohnenberger, Head Product Management Rotor Spinning Machines & Systems