By Stephan Weidner-Bohnenberger, Head Product Management Rotor Spinning, Machines & Systems
The new software for the R 66 rotor spinning machine makes the daily work for the operators and the managers easier. They can retrieve and analyze important data directly on the machine display. Where necessary, productivity or quality-improving measures can be immediately implemented.
The new standard software of the R 66 simplifies data analysis and is very easy to use (Fig. 1). Reports on the condition of the machine are structured so that irregular data are quickly recognized. The reports retrievable are the production report for the entire machine, the individual spinning units and the messages from the yarn clearer, and recorded events and interventions for the entire machine and the individual spinning units.
Should a spinning unit not reach the previously defined production, this is clearly visible in the shift report. In the spinning units overview, this spinning unit is identified in color (Fig. 2). Definition of the limits is freely selectable, depending on the circumstances. Problematic spinning units, the so-called “off standard positions”, can be precisely localized and optimized, as they mostly cause quality problems or losses in production. That makes possible an efficient deployment of maintenance staff and ensures constantly high productivity and quality.
All events, interventions are retrievable
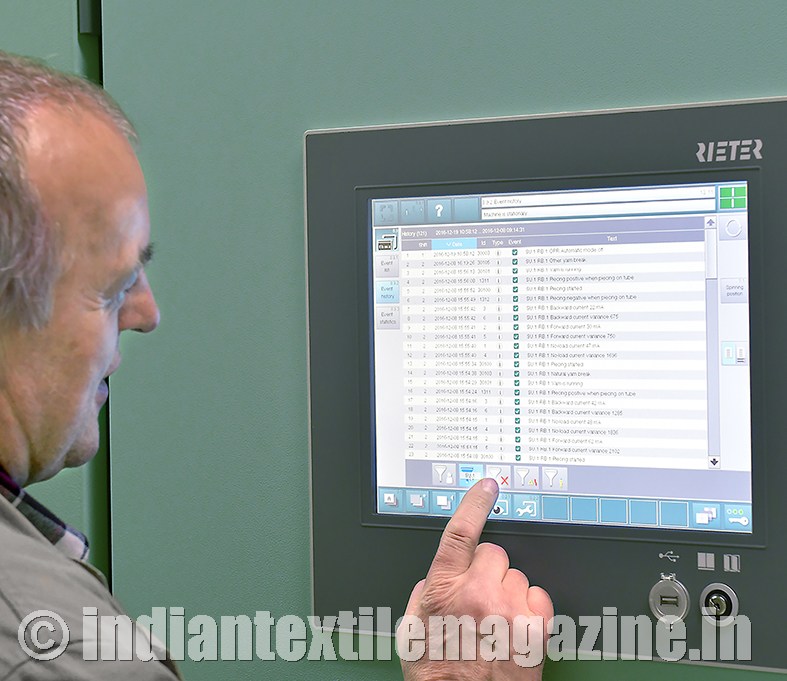
The machine records all events and interventions, including alerts, in a machine event report. This information is shown with a numerical code and a brief text. Via filter functions, component-specific information can be selectively retrieved here. This very quickly gives the maintenance staff an overview of the machine condition and they can systematically intervene, carry out maintenance work or, where possible, even quickly correct the faults.
Interesting is the linking of both items of information directly on the machine display. From the machine event report for a spinning unit, a direct switch to the production report for the spinning unit can be made. This allows a quick, precise and effective fault analysis.
The new software allows two procedures: the familiar work on the machine display and alternatively the temporary storage of all data on a USB stick. The data can subsequently be evaluated on the PC. For the machine report, the units demanding special attention can be selected in both ways. Rieter machines, preferably Rieter’s SPIDERweb mill control system, can be used to evaluate the data.
In the same way, data on error diagnostics can be downloaded. Where necessary, the list of events and interventions on the machine can be sent by email to the Rieter specialists together with a log file. Experts can localize faults rapidly and specifically and propose solutions.
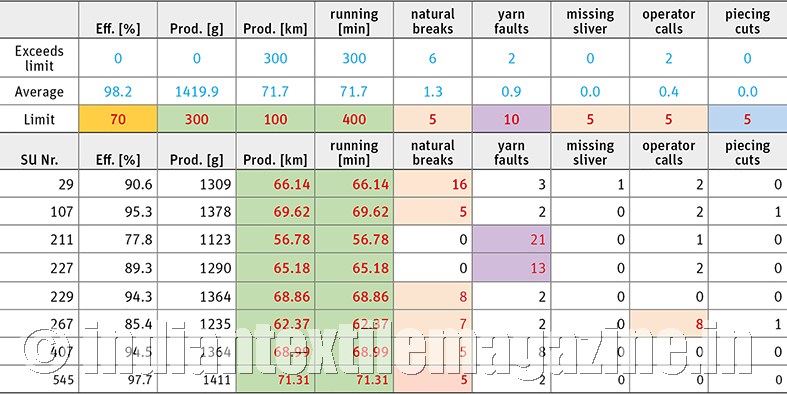
Users of VARIOspin, who design effect yarns with the E-Profi program from Amsler, profit with the new software from an extended scope for design creativity. Compared to the very expensive, classical mechanical systems for creating effect yarns, now up to 360 slubs per minute, can be produced on an R 60 or R 66. For certain applications, effects are possible with peaks look like being very short in the finished product. The fabric appearance in knits or wovens is thus in some cases close to that of a fancy ring yarn.
Customers who have tested the software confirm its easy handling. The clearly structured display and the feasible evaluations have proved to be valuable for every day work.
The rapid situation analysis, including the support of the Rieter experts, allows a precise maintenance assignment and fast correction of incidents. That ensures a high level of productivity and a consistent quality.