More and more TCO 12 combers are now operating in India – and that success had to be earned. Customers in the Indian spinning industry want to experience real-world results from innovations on the shop floor. The rising popularity of the Truetzschler comber TCO 12 is a powerful indication of how our machines meet these expectations by providing outstanding quality and productivity.
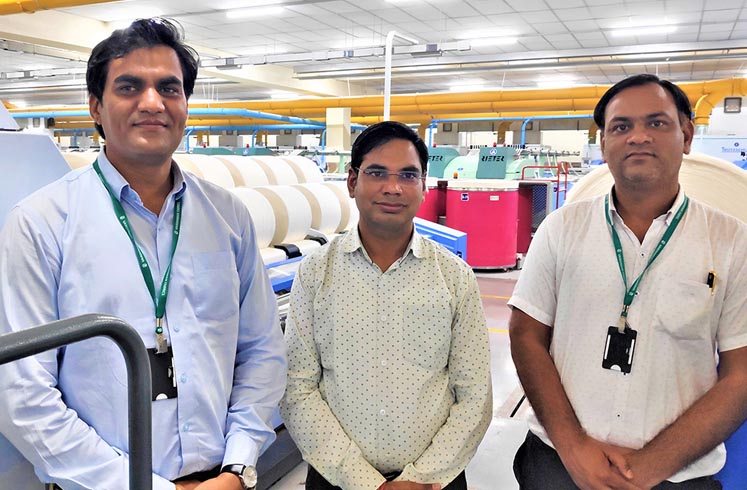
When Truetzschler launched its first comber TCO 12 in India in 2017, it faced some major challenges. Local and international competitors were fighting hard to win market share, while spinners in the Indian market wanted to get real-world and first-hand experience of the Truetzschler technology before they believed in the value of Truetzschler combing innovations like servo drive, twin drive or auto-leveler.
Vardhman Group – one of the biggest textile conglomerate in India is significant addition to a growing group of Indian companies that are using combing machines from Truetzschler. Vardhman has always been keen and proactive in trying the latest technological innovations. In this spirit, Vardhman decided to buy its first Truetzschler comber in 2017.
The customer tested the machine for two years at its site in Madhya Pradesh, comparing the quality and productivity against machines from other providers. Based on this trial, Vardhman was confident about the technology and performance of the TCO 12 – and ordered a complete combing set for its new spinning plant in at Vardhman Fabrics Unit, Budhni.
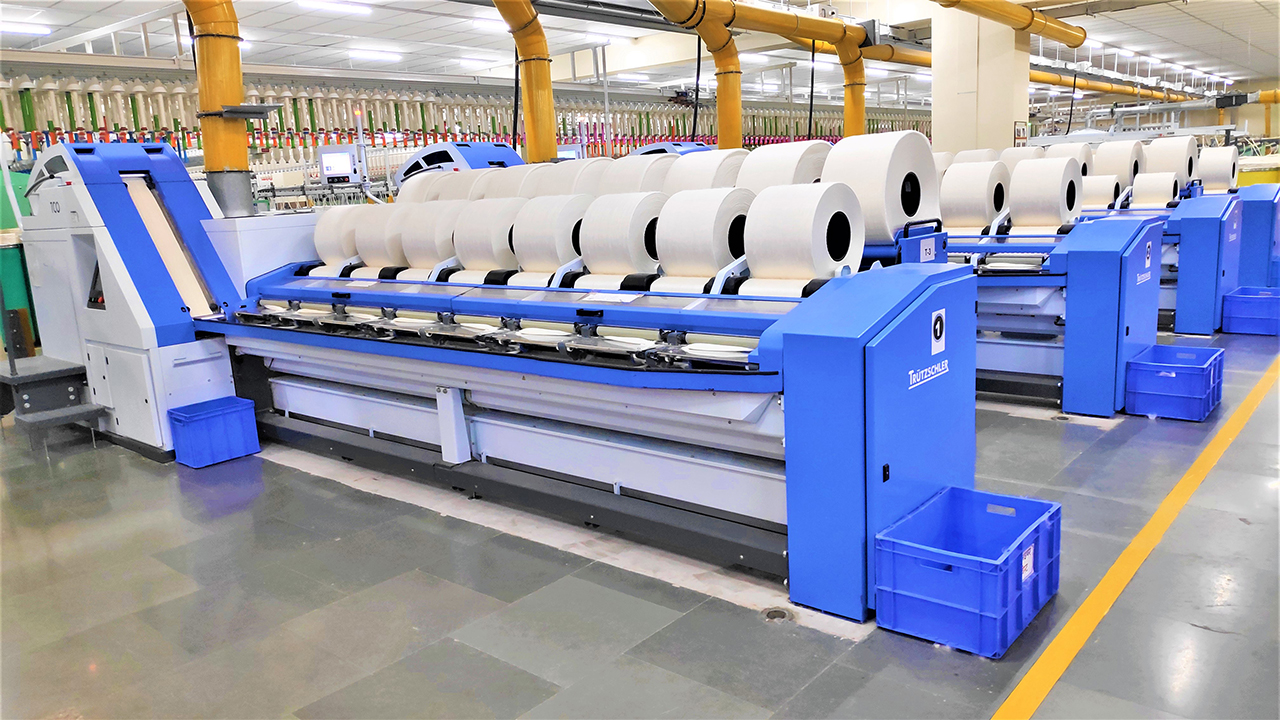
Another generation of innovative combing
In 2020, Truetzschler boosted its portfolio of combers by launching the next-generation “Type-2” machines. These new combers were developed in response to experience and insights from our customers’ sites. They offer a range of new features that improve on the “Type 1” machines launched in 2017. This includes:
• Simplified changing of the detaching distance, within just a few minutes.
• A new and easy-to-use comb brush setting mechanism.
• A new top comb locking system.
• The option to select a detaching curve, for higher speeds.
• A special handle to lock and open the detaching unit with one hand.
• Modified doors and covers for better accessibility and aesthetics.
The machines have now been running at the Vardhman Fabrics site in Buddhi for more than a year. Technological reports for count Ne 20s to 30s showed that the machine comfortably achieved benchmarks for quality and productivity at high Nip rate of 500 and more.
Automatic greasing
The Truetzschler comber machines used by Vardhman Group also feature a special auto-greasing device. This automatically applies grease to all of the components that require it, which makes sure all necessary points on the combing head are always greased accurately and at the right time.
More innovations coming soon
The road to success, as the saying goes, is always under construction. In line with this saying, Truetzschler’s team is now working hard to develop even more features that add value for customers in this market. This includes the 1,200-milimeter Jumbo Can, as well as the Auto LAP transportation system and the flexibility to use different technological components. An automatic lap piecing system for the comber is now in development.
The planned new features are part of the company’s long story of responding to challenges by creating innovative solutions. And the next chapters in that story could be the most exciting ever…
—
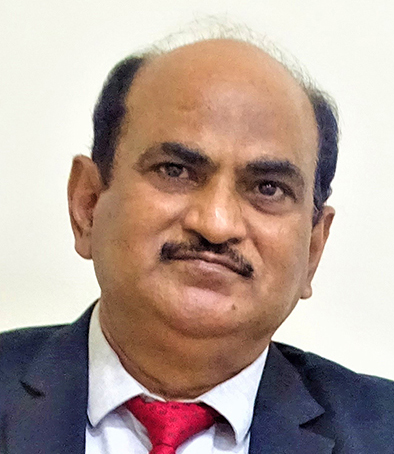
“The TCO12 is a futuristic design,” said T. C. Gupta, Chief General Manager of Vardhman Fabrics unit. “It presents special features where manual intervention is significantly reduced.”
—
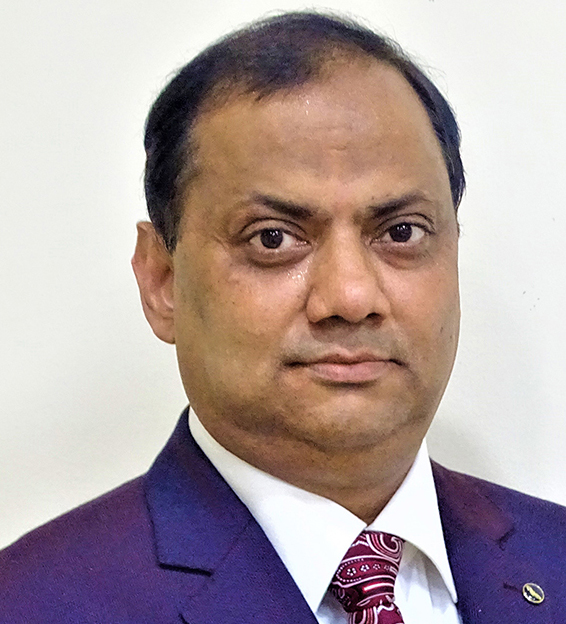
Harsh Mani Tripathi, Senior V.P., Vardhman Fabrics, added: “We supported all of these trials and shared our valuable input to make it a success. Vardhman Fabrics appreciates that the machine is good in terms of technology – and is also very stable, even in varying RH/Ambient conditions.”
—
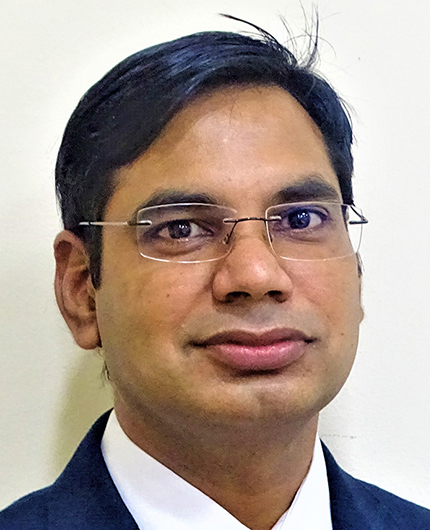
“At Vardhman, we appreciate this unique and innovative design feature,” said S. K. Nagar, Chief Manager. “Manual greasing means applying grease to 70 points within the machine. We always saved this time and effort”