Following several years of development with partner Siemens, Oerlikon Barmag kicked off serial production of its new drive unit for POY systems at the beginning of the year. The new component makes stands out above all with regards to energy efficiency.
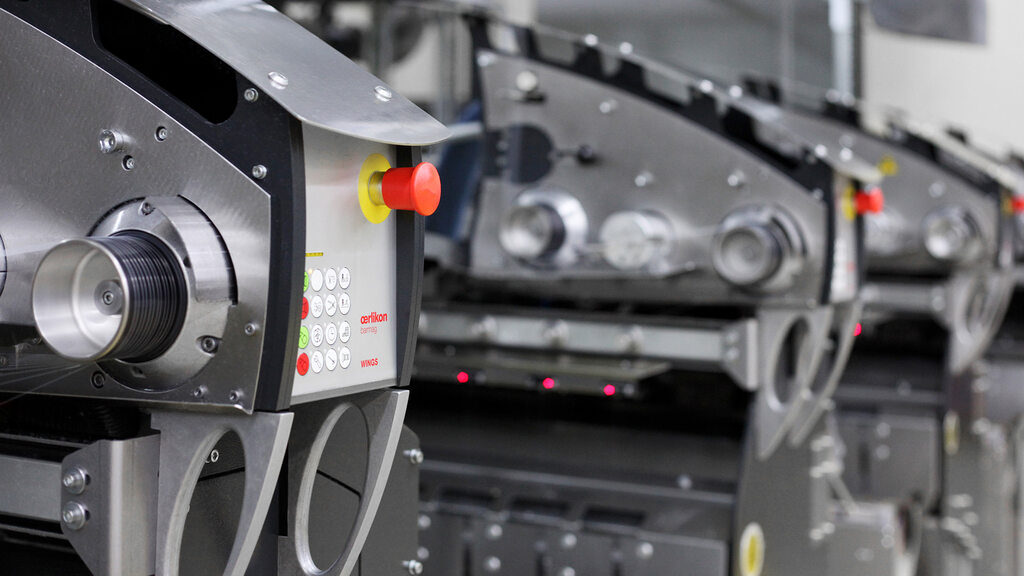
e-save: innovative technology helps save energy
The requirements-specific design of the compact inverter unit ensures functional optimization of the winder’s control functions. And the new component is used in conjunction with a performance-optimized chuck motor. This means that energy savings of up to 3% can be achieved for the take-up. “In the case of a 1,000-position system, this represents a saving of around 120,000 euros a year, depending on the relevant local energy costs. The many years of collaborating with our partner Siemens means that we are always state-of-the-art in terms of control technology. With our e-save-certified solutions, we are consistently able to offer our clientèle sustainable technology for the efficient manufacture of yarns”, states Arnulf Sauer, responsible for winder technology at Oerlikon Barmag.
Further customer benefits include a significant reduction in cables and cable trays. The reduced number of switching cabinets also saves space. Following intensive field tests at two well-known customers last year, the compact inverter unit was finally released for serial manufacture at the beginning of 2020. There are plans to deliver several thousand positions with the new component this year.