Pioneer Embroideries, a leading name in the textile industry, has embarked on significant projects aimed at enhancing its production capacity and sustainability.
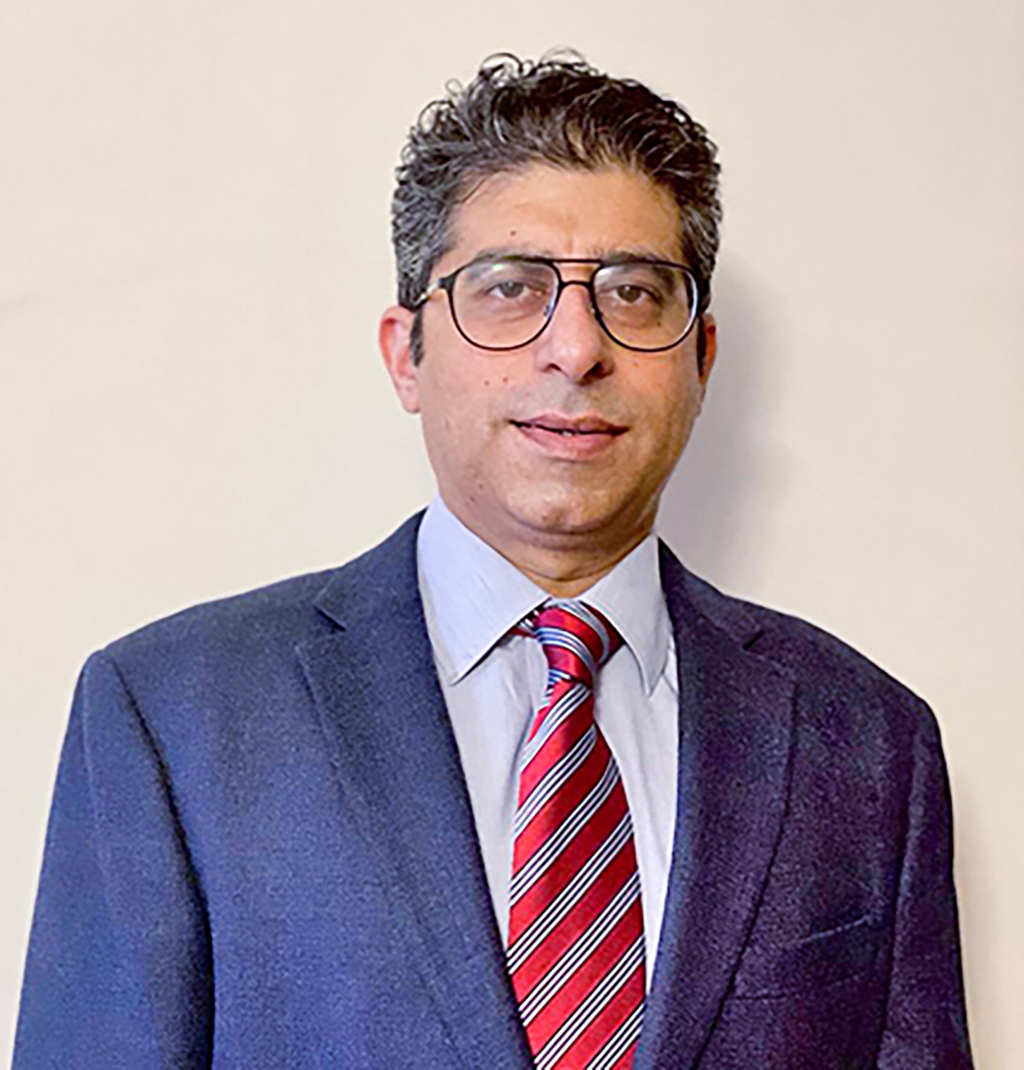
Under its Specialized Polyester Filament Yarn (SPFY) division, the company has successfully increased its spinning capacity from 18,000 MTA to 26,000 MTA, with production commencing in June 2023. Additionally, new value-added capacities in Partially Oriented Yarn (POY) and Draw Textured Yarn (DTY) are set to become operational by the end of September 2023. These initiatives represent a crucial step towards strengthening Pioneer Embroideries’ foothold in the industry.
Simultaneously, the company has undertaken a modernization project at its embroidery facility. This state-of-the-art greenfield project began commercial production recently. The combined cost of these two ventures totals approximately Rs. 110 crores. Upon reaching peak capacity utilization, these projects are expected to generate an incremental annual revenue of approximately Rs. 150 crores. Both initiatives are projected to achieve peak capacity utilization by Q3FY23-24.
Founded in 1991 by Mr. Raj Kumar Sekhani, Pioneer Embroideries Limited (PEL) has emerged as a prominent manufacturer and exporter of value-added Specialized Polyester Filament Yarn (SPFY) and Embroidery & Laces (EL) in India. The company operates a state-of-the-art SPFY manufacturing facility in Himachal Pradesh, along with two Embroidery & Laces manufacturing facilities in Gujarat, Dadra & Nagar Haveli. PEL has a robust marketing presence in all major markets.

PEL produces various types of SPFY, including Air Texturized Yarns, Carpet Yarns, Twisted Yarns, Fully Drawn Yarn, Draw Textured Yarns, and Partially Oriented Yarns. These find applications in technical textiles such as Flame Retardant yarns, Recycled yarns, Anti-Microbial yarns, UV Stabilized yarns, Easy Dyeable yarns, and other Fancy Yarns, capable of replacing natural fibers like Cotton, Viscose, and Wool.
Expansion & Modernisation
In its ongoing expansion and modernisation program, PEL is strategically replacing 32 existing embroidery machines across multiple locations with eight state-of-the-art machines in a centralized manufacturing unit. This move is aimed at boosting production capacity, improving quality, enhancing efficiency, and reducing costs. PEL has invested ₹33 crore in importing machinery from Lasser AG, Switzerland, and an additional ₹7 crore for ancillary machinery and utilities. The new facility is nearing completion and is poised to optimize PEL’s operations significantly.
PEL is also a leading promoter in the Shree Ganesh Integrated Textile Park (SGITPL), where it holds a 33.3% stake alongside two other lead promoters. This partnership has enabled PEL to establish a greenfield project and secure land for future growth. With government approval secured for SGITPL, PEL has invested approximately ₹12-13 crore in equity and infrastructure within the park. This new venture is expected to offer various advantages to the company, including support from state and central government initiatives.
SILKOLITE and Sustainable Innovations:
PEL has carved out a permanent niche for itself in the global SPFY business, thanks to its best-in-class quality under the SILKOLITE brand. PEL’s products primarily cater to the non-apparel segment, serving industries such as carpets, bath mats, upholstery fabrics, and curtains. PEL has become one of the first textile companies to establish a brand in a highly commoditized yarn business.
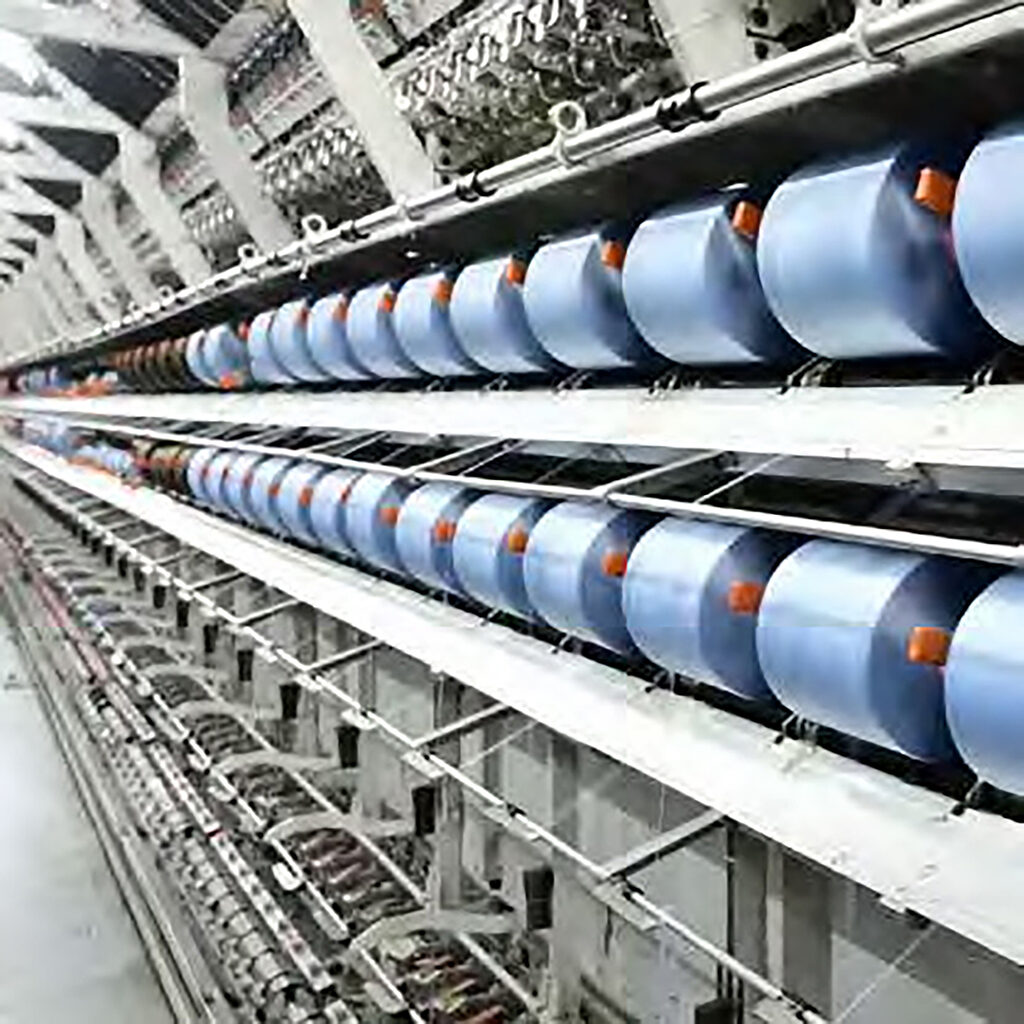
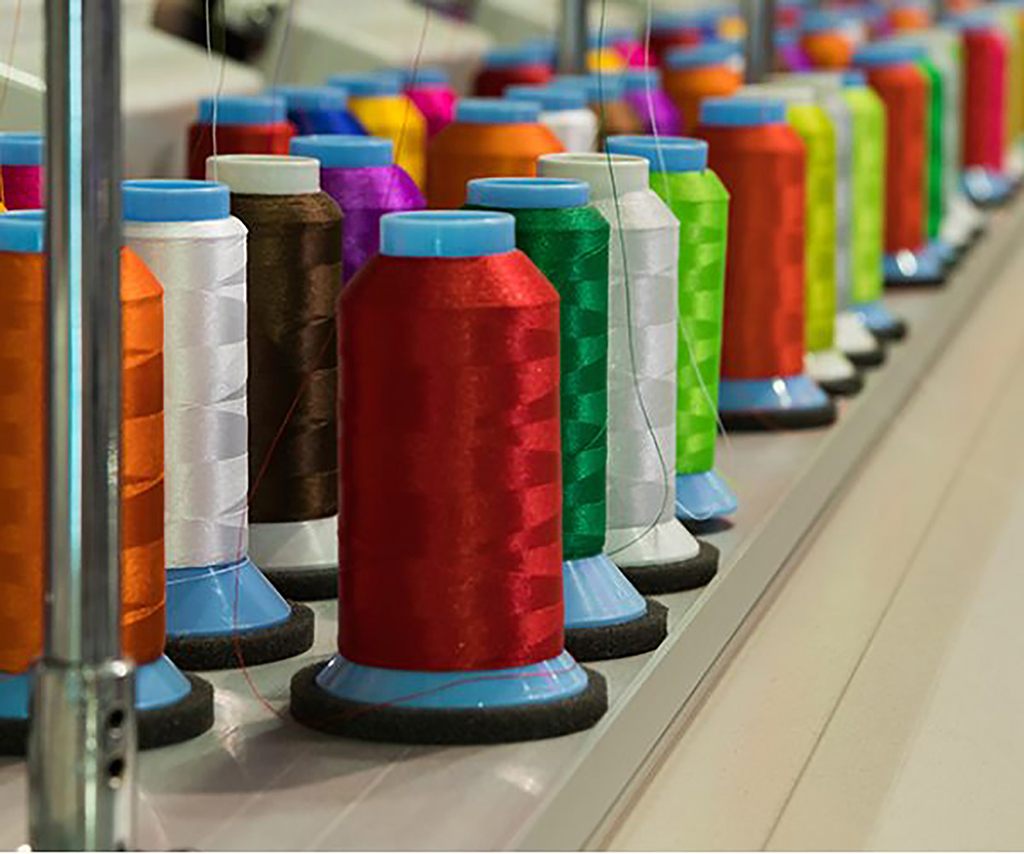
PEL boasts a capacity of approximately 14 million meters for braided laces and about 1,200 million stitches of embroidery. The company’s products command a premium in the marketplace due to their superior quality, design, and capacity.
As the owner of the heritage brand Hakoba, PEL has strengthened the brand’s reputation by continually expanding its library of embroidery designs, making Hakoba synonymous with high-quality embroidery worldwide.
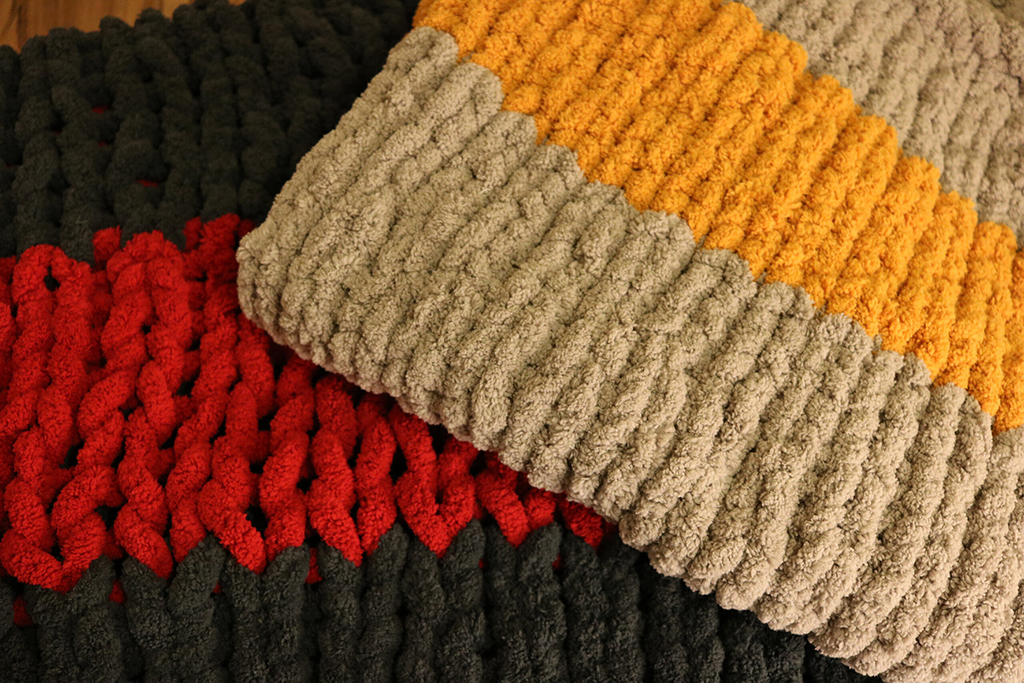
Sustainable Business and ECO-Friendly Production:
The Specialty Polyester Filament Yarn (SPFY) business has proven to be a profitable and diversifying venture for PEL. In the SPFY process, the yarn is dyed at the polymer stage, and the extruded yarns are colored with excellent color variations and fastness before the extrusion process. Notably, the dope-dyed process does not use water and generates zero effluents, making it an environmentally friendly method. PEL’s adoption of this process results in substantial water savings of approximately 1.9 million liters daily.
PEL’s achievements and investments underscore its dedication to staying at the forefront of the embroidery business, achieving operational excellence, and positioning itself for sustained growth and success.