The group makes a meaningful contribution to the Indian industry ecosystem through its five businesses – recycling, packaging, textiles, master batches and hospitality. It continues to reinvent itself to maintain its leadership in quality product range and capacities coupled with affordability
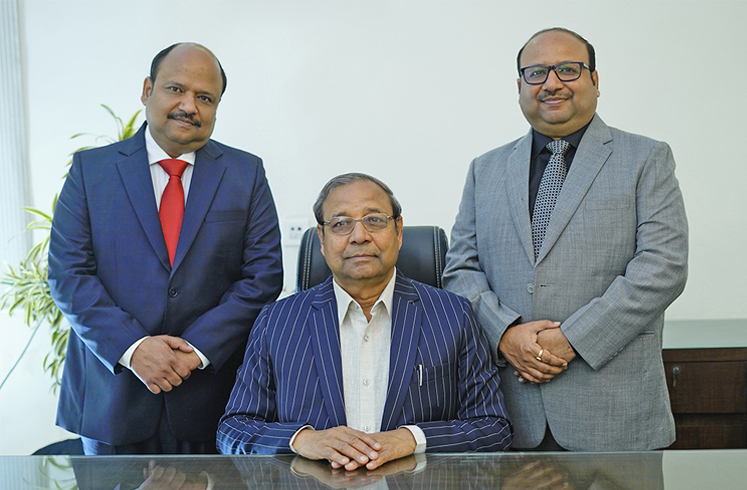
Pashupati Polytex is a multi-product textile manufacturer. The company, a part of the Pashupati Group, is all about quality, innovation and sustainability. It is engaged in manufacturing goods with proven quality such as woven fabrics (packaging goods) and filler additives, recycled polyester staple fibre (RPSF) with specialty fibre like P-Concrett™, reinforcement fibre, P-Anti Bacterial™, P-Acro Fill™ fibre, Fire Retardant™, etc., recycled PET flakes, recycled PET chips, polyolefin recyclates, colour master batches for PE, PP and PET and recycled synthetic yarns, with eight manufacturing plants across India at different locations.
“Besides manufacturing, we are also into waste management and assist brand owners in EPR compliance. By carrying out collection, segregation and recycling, Pashupati Polytex adheres to consistent quality, innovation and sustainability codes,” says Managing Director Bankey Bihari Goenka. Today, the group makes a meaningful contribution to the Indian industry ecosystem through its five businesses – recycling, packaging, textiles, master batches and hospitality. It continues to reinvent itself to maintain its leadership in quality product range and capacities coupled with affordability.
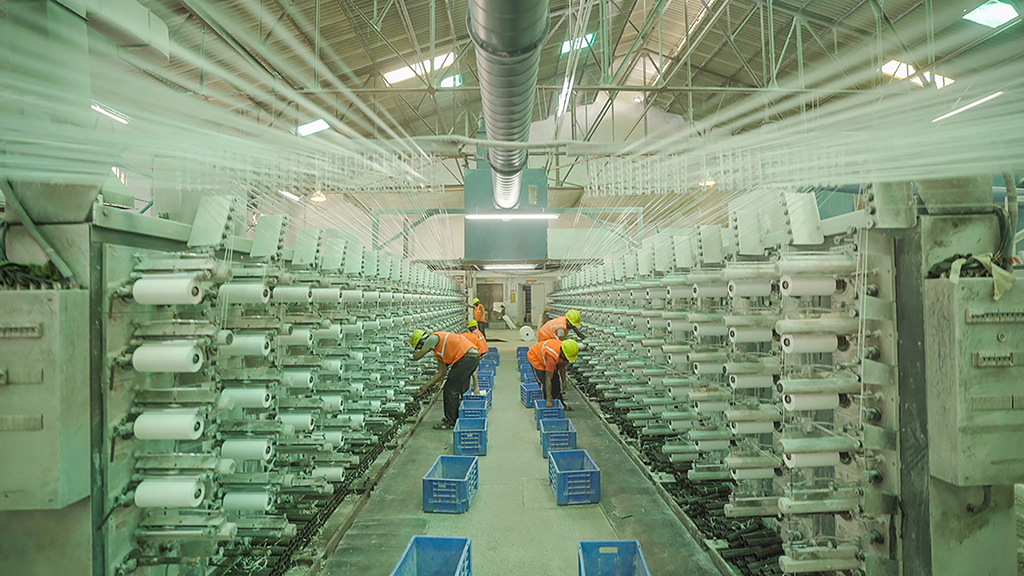
“We are recycling 11.5 million bottles per day with the capacity of 2,00,000 MT per year, saving up to 1.75 million cubic yards per year which is equivalent to 300, three BHK villas. Crude oil consumption is saved up to 0.87 million barrels per year which is equivalent to 1,95,500 MT of coal saved and 6.32 trillion British thermal units of heat energy conserved, reducing greenhouse gas emission of 4,20,000 MT of CO2 per year. We have been audited and certified by EUROPACERT for compliance of ISO 9001:2015, ISO 14001:2015, ISO 45001:2018, GRS Version 4.0, OEKO TEX Standard 100 Hohenstein (Germany), REACH compliance certificate CDG, RCS-100 by CU Certification, Commission Directive 2002|72|EC and Council Directive 94|62|EC, FDA compliance and IS 14887:2014 from BIS,” Goenka adds.
Wide Product Range
Throwing light on the products and solutions offered, Goenka mentions that the company’s business is based on manufacturing quality recycled products from plastic waste. “We started with recycling of post-consumer PET waste and expanded our PET recycling capacities continually. We understood the adverse impact of post-industrial PET waste on the environment and started handling post-industrial PET waste through partial chemical recycling. We manufacture all our products under one umbrella and use glycolysis technology to recycle burnt or degraded and difficult to recycle PI and PC wastes. Thus, we convert non-usable PET waste and up-cycle it to value-added products to bring it to the mainstream, thus enhancing its lifecycle. We are the first Indian company to get FDA approval for PET flakes,” Goenka elaborates.
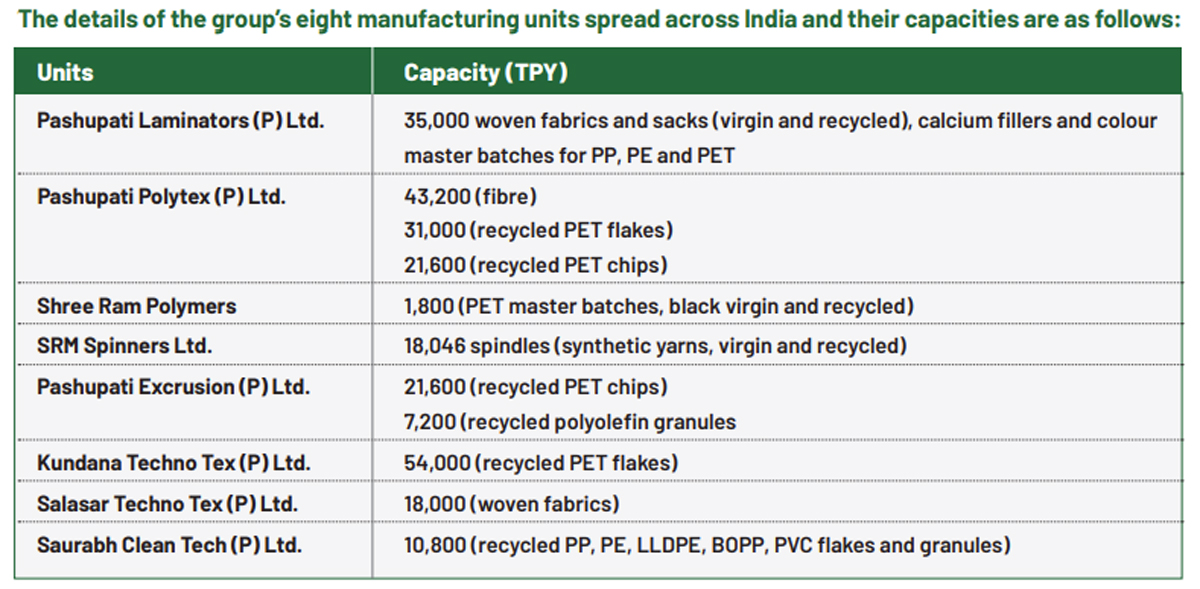
Some of the ongoing investments and expansion of capacities are as follows:
• Commence commercial production at new facilities – Kundana Techno Tex, Salasar Techno Tex and Saurabh Clean Tech in 2022.
• Building capacities in renewable energy (solar, wind and biomass) at the Jaipur and Kashipur facilities.
• Enhancing manufacturing capacity of PP and HDPE woven sacks (bags) by installing additional printing machines and block bottom bag-making machines.
• Installing new sorting machines for polyolefin waste, colour and polymer segregation.
• Installing food grade polyolefin granules-making technology.
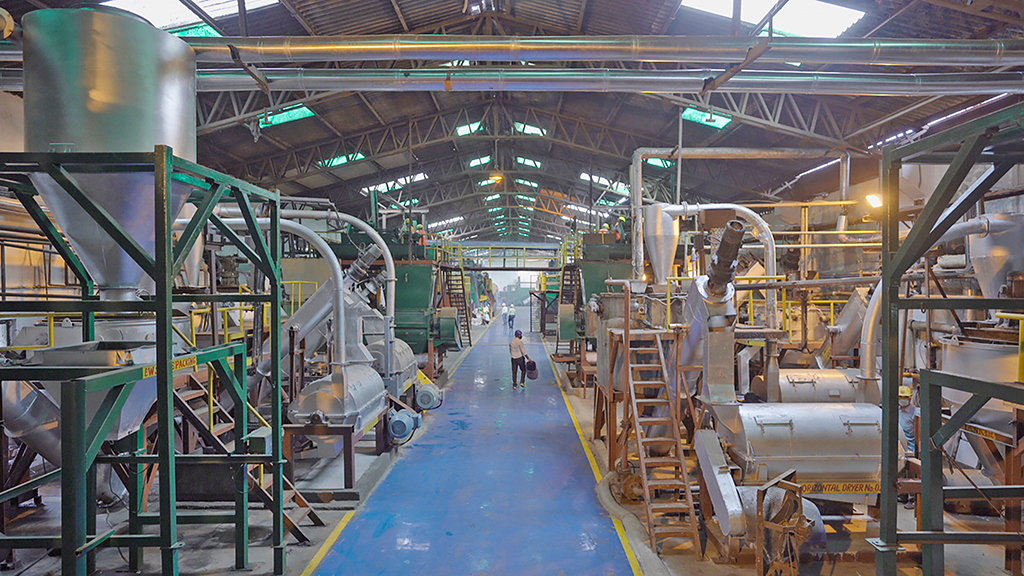
The new products, innovations and technology advantages offered by the company include:
• Expanding the base in waste (PET, HDPE, LDPE, SUP, MLP and PP) collection across India.
• Forwarding integration to PET recycling. The company manufactures recycled polyester staple fibre (solid, hollow and dyed) and specialty fibres. The plan is to make synthetic yarns.
• Recycled polyolefin granules, recycled PET flakes (food grade – first Indian company to get FDA approval), and recycled PET chips, recycled colour master batches.
• PP fibre for technical textiles applications.
• Apart from manufacturing, to maintain sustainability the company is also into waste collection, providing EPR facilities to brands by doing collection, segregation and recycling.
• Making recycled PET chips from waste which does not remain recyclable and can be burnt or used for landfill only.
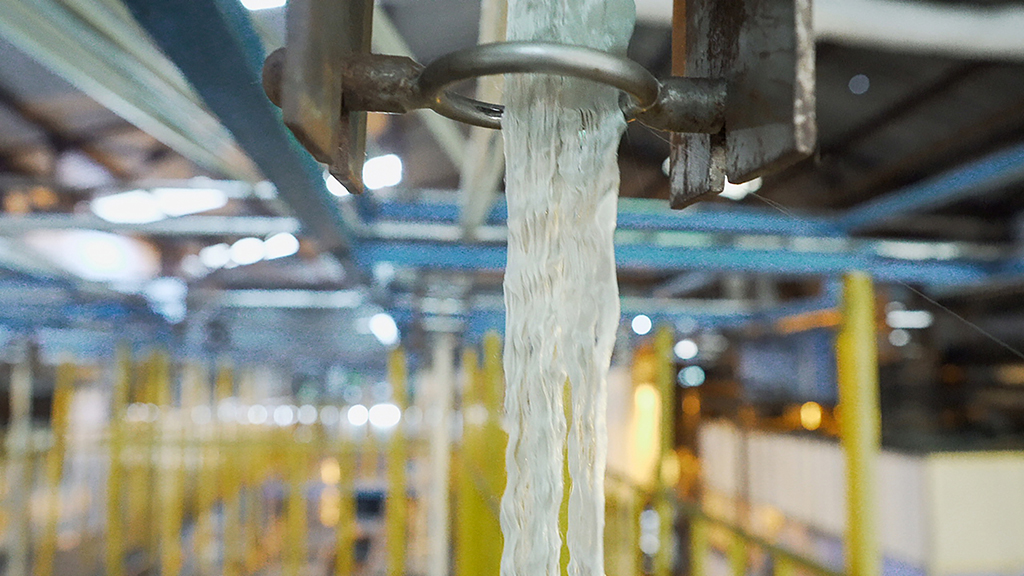
As regards the company’s share of domestic business and exports, Goenka states: “Our maximum sales are in the domestic market across India. We are very less into export because we have a great demand of sustainable products in the domestic market and are supplying our material to India’s leading manufacturers of textile sheet, film, strap, fibre, packaging, etc.”
Powerful USPs
According to Goenka, to be noticeable in the marketplace a company should have a powerful USP. He adds that for Pashupati Polytex, the USP is its customer-centric line of attack depending on certain principles such as:
• Assurance: This goes way beyond the product quality.
• Sustainability: The company believes in working in an environmentally, socially and hygienically suitable way. Therefore, it bestows all of its efforts towards manufacturing quality product range with sustainable approach.
• Reliability: The highly skilled team at Pashupati Polytex is committed to offering supreme support to its clients at each step.
In addition, it manufactures several sustainable products under one roof and does not compromise on quality. The company is equipped with all the necessary certificates, ensuring that it fulfils all the statutory compliances.
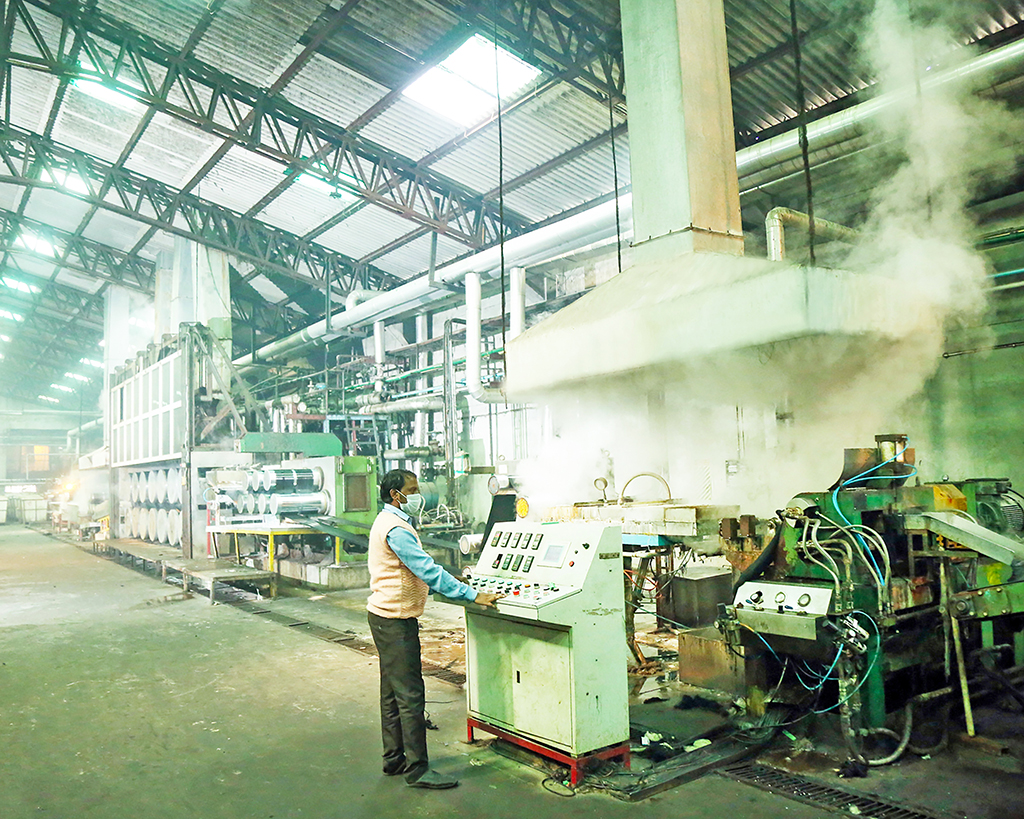
Growth Curve
Going into details regarding the company’s growth over the years, Goenka states: “The journey started about 45 years ago with deep-rooted values from which was absorbed the desire to work today for a better tomorrow. This line defined the product, processes, journey and destination for the group, and thus formed a framework of its operations. Today, the group makes a meaningful contribution to the Indian industry ecosystem through its five businesses and continues to reinvent itself. Our turnover is Rs 9,000 million.” Its team strength includes over 500 employees and 1,500 contracted labour and the group has nurtured the skill of producing significant volumes of finished products with low conversion costs.
Sustainability Initiatives
Commenting on the company’s sustainability focus and initiatives, Goenka says, “We complete the entire manufacturing process from waste collection to manufacturing of fibre and yarn for technical textiles and this is very important. Our focus is on full traceability from origin to finished product with special consideration of the sustainability aspect of our operations. The recycled PSF so made is supplied to home furnishing, clothing, upholstery, cushioning and technical textile industries. We have recently diversified into specialty fibres like anti-bacterial, fire-retardant, hydrophilic, reinforcement, easy dyeable, easy dyeable cationic (acrylic feel), low melt, biodegradable, PP fibre and Nylon 66|6.”

The company is also able to provide EPR (extended producer responsibility) compliance support to major FMCG brands. “We divert the burnt or degraded and discarded post-industrial and post-consumer waste from dumping sites and energy recovery sites to our partial chemical recycling, glycolysis plant to make recycled PET granules which are also used for all textile applications. Further, we manufacture recycled coloured master batches also from these chips to provide circular solutions to the plastic industry,” Goenka states.
The contribution of the company to sustainability is as follows:
- Planet
• Landfill space saved – 1.03 million cubic yards per year.
• 0.51 million barrels of oil saved per year.
• Energy conserved to the tune of 3.72 trillion BTUs per year.
• Significant GHG emission reduction.
• Zero liquid discharge norms maintained.
• All emission norms followed. - People
• Direct and indirect employment to over 3,000 people, including rag-pickers.
• Primary education to nearly 500 students of the local community children.
• CSR investments in helping the needy and poor.
• Policies to support gender equality and justice for all.
• Focus on transparency in waste.
“Our main efforts are for complete atomic segregation of waste (polymer and colour-wise), which we have almost achieved to a great extent. We have also implemented automation wherever possible in further processes like grinding, washing and manufacturing of sustainable products with reference to quality and products,” Goenka says.
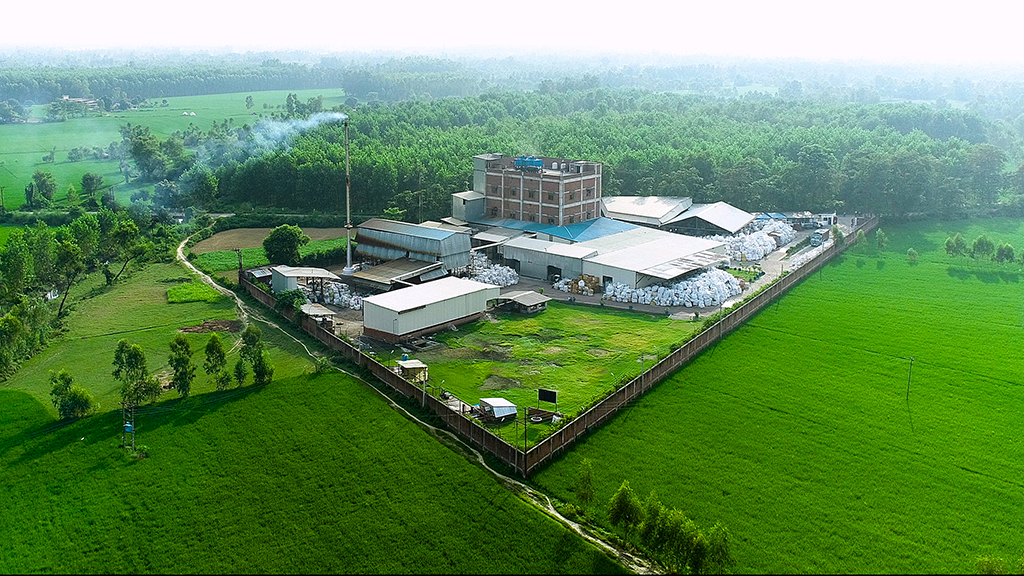
Growth Plans
According to Goenka, the group’s future plans and vision for 2025 and beyond are as follows:
• Expand waste collection capacity across India to collect PET, HDPE, LDPE, SUP, MLP and PP and ensure their recycling.
• Evaluate technologies in chemical recycling to treat complex mixed plastic waste to produce virgin grade polymer.
• Evaluate technologies to treat garbage and discarded waste and convert into oil, gas and electricity.
• Production of food grade flakes and chips from post-consumer PET bottle waste.
• Diversification into nonwoven and technical textile segment for further value-addition of recycled fibre.
• Develop capacities in renewable energy including solar power plant installation in manufacturing facilities.
• Forward integration to PTY and DTY in existing facilities.
The vision for 2025 and beyond includes foray into geo-textiles for packaging, besides specialty fibres and specialty polymers as well as setting up of manufacturing facility for chemical recycling of mixed complex plastic waste.