Fabric defects are a thing of the past, thanks to Pailung’s Fabric Defect Detection system, which uses computer vision to detect fabric defects inside the knitting machine, reducing waste fabric, and increasing customer satisfaction.
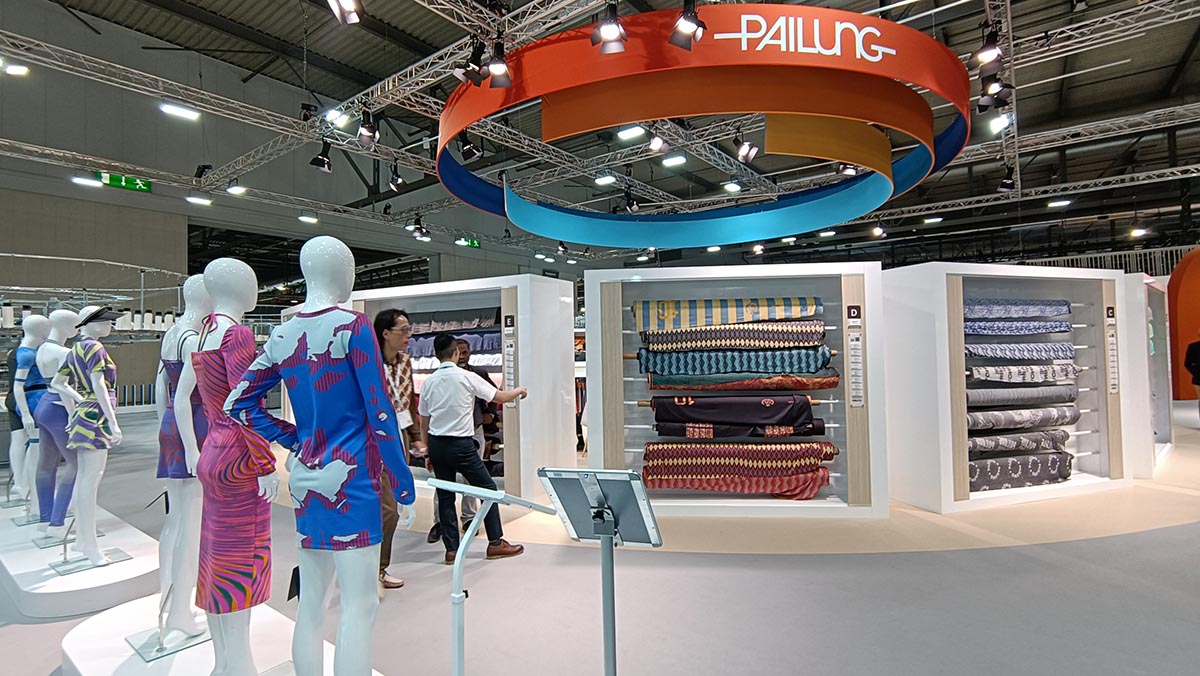
A study by the Waste and Resources Action Programme found that up to 15% of fabric goes to waste during production, due to defects such as snags and needle lines. This can result in significant financial losses for manufacturers, and negative impacts on the environment.
What’s even worse for manufacturers is when defective fabric reaches the customer, leading to quality complaints that can threaten future business. It’s all too easy for a human to miss a tiny defect in a long roll of fabric, and for that fabric to be delivered to the customer by mistake.
That’s why Pailung has been working hard to develop more advanced ways of detecting fabric defects. Their latest innovation utilizes cameras, fitted inside their knitting machinery, and equipped with computer vision to detect defects during production.
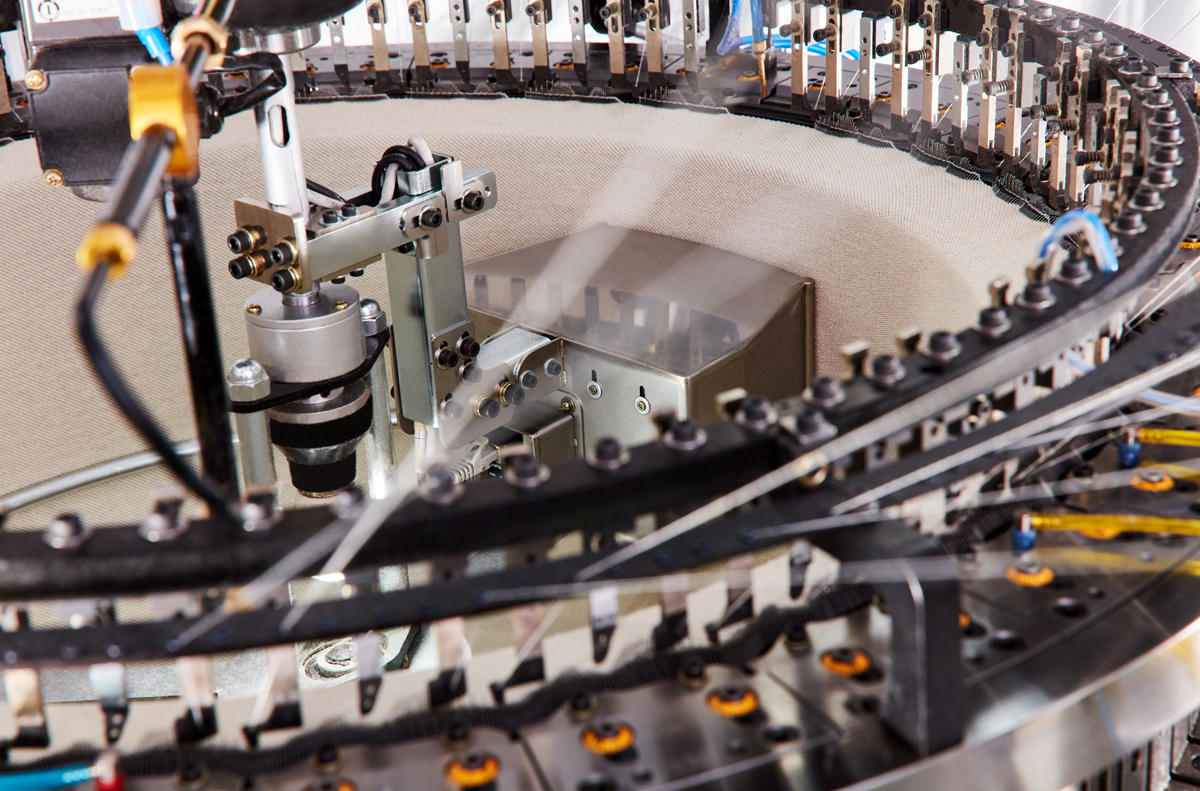
Real-time defect monitoring is game changer for textile manufacturers. When a defect gets detected, the knitting machine can be shutdown, immediately, pausing production until the problem has been solved, and reducing the manufacturer’s waste fabric losses.
But that’s just one of many benefits that textile manufacturers can expect from Pailung’s new, three-tier software suite. “We created this software to aid textile manufacturers in their digital transformation, and enable them to reap the benefits of textile industry 4.0,” says James C.C. Wang, Chairman and CEO of Pailung.
Transfer All Know-how from the Technician to the Factory
The Knitting Fabric Management System (KFMS) stores an archive of knitting detail resources. Every fabric that a Pailung knitting machine produces can be saved in this database, enabling any technician to produce all of those fabrics without prior knowledge of how they’re made.
Whereas, in the past, one technician might have all the know-how for producing a certain fabric, now any technician can produce that fabric. This effectively transfers all fabric production know-how from the individual technician to the factory as a whole.
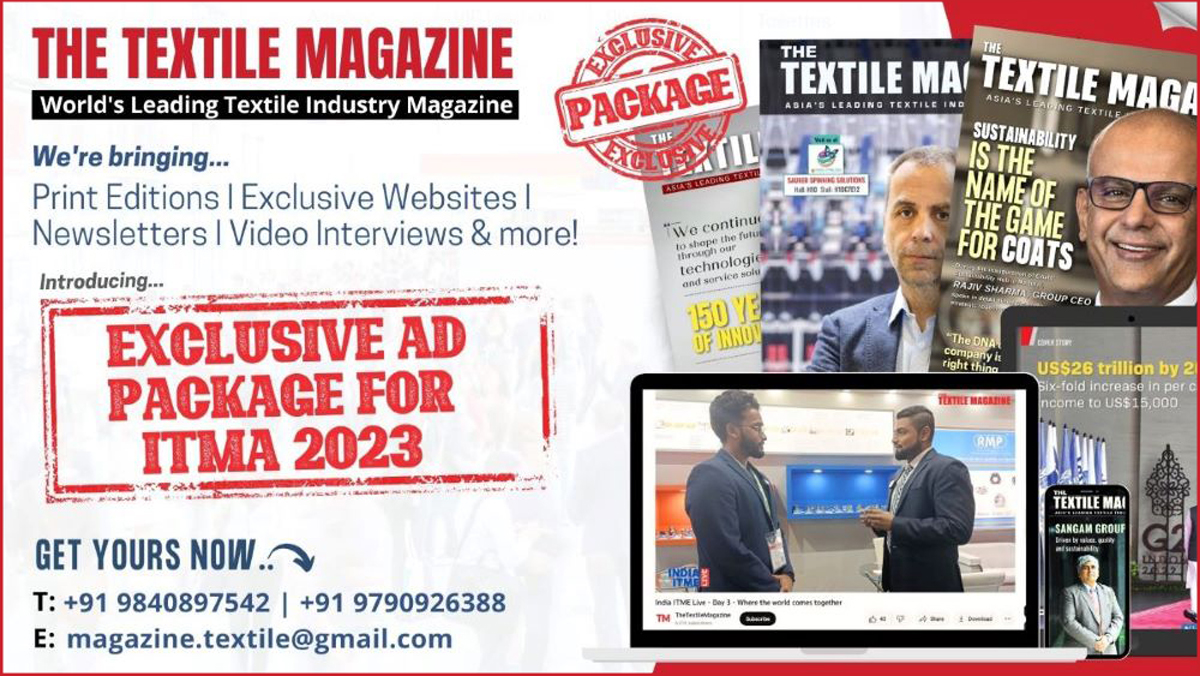
Detailed parameters can be saved for each fabric. Knitting parameters, including machine type, yarn type, specification, yarn length, and weight etc. And adjustment parameters, including knitting needle, tension, angle, and timing, etc.
Control Every Knitting Machine from One Dashboard
The Pailung Online Management System (POMS) allows the technician to control multiple knitting machines from a single computer. All workflows, from production to order scheduling and machine monitoring, can be performed remotely using this central system.
All fabrics that are saved in the KFMS, along with their corresponding parameters, can be accessed through the POMS. From there, the technician can select a fabric, schedule production, and monitor each knitting machine’s progress — all via the dashboard on their computer.
Boost Functionality of Textile Factory ERP System
The KFMS and POMS can be further integrated with the Manufacturing Execution System (MES). Together, these three systems are able to send data directly to the factory’s ERP system, which can use that data to account for knitting machine resources.
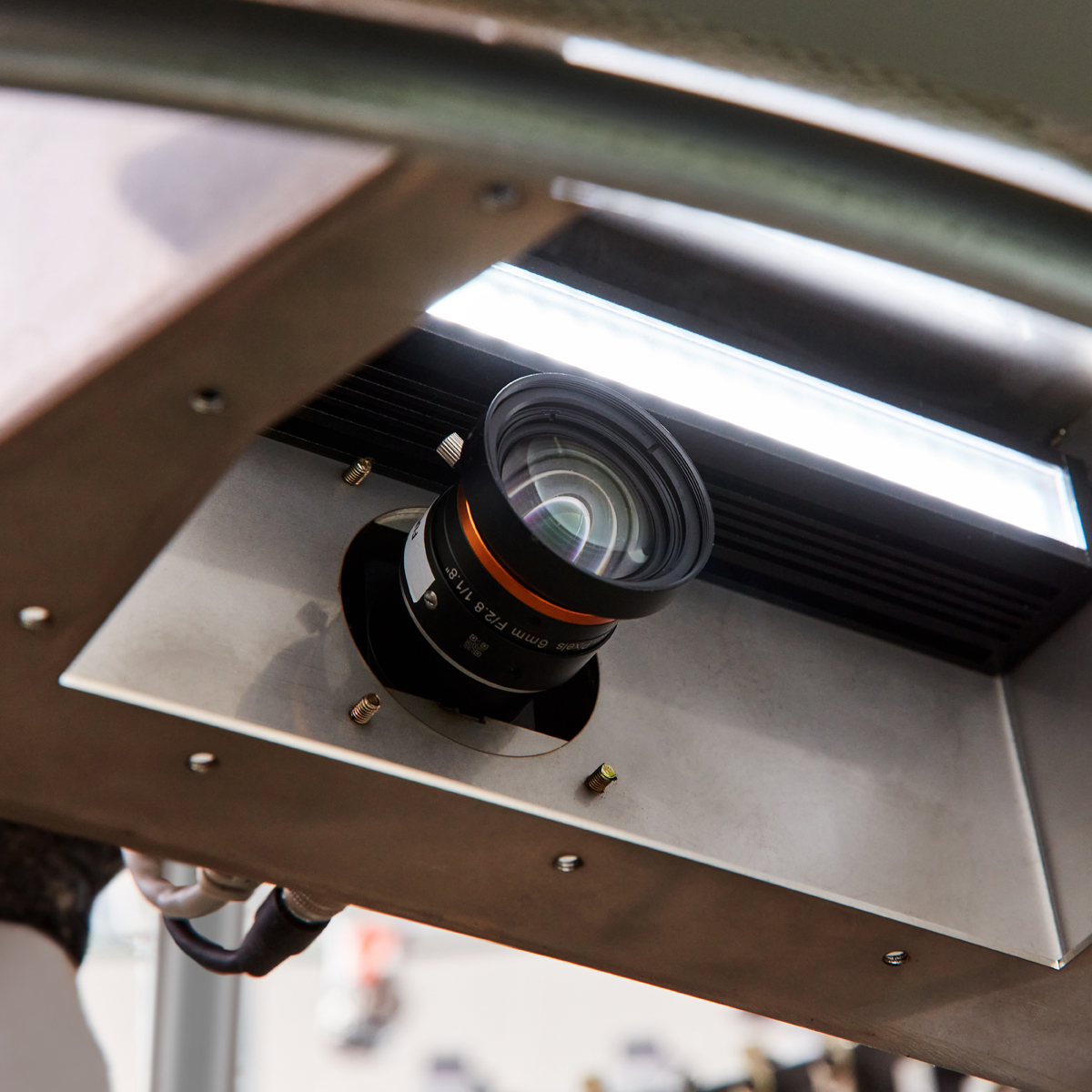
They can account for the difference between production volume and expected delivery volume, the ratio of knitting machine running time and downtime, as well as the type and frequency of knitting machine errors, etc.
Automate Knitting Machine Setup and Maintenance
Data from the KFMS and POMS informs the MES, which uses the fabric parameters to automatically set up each knitting machine. This saves the time that it would take for a technician to manually set them up, one by one.
It can quickly reset each knitting machine, according to the fabric scheduled for production, switching all parameters automatically. In this way, it can replace a large number of manual adjustments, and work order scheduling, which saves significant manpower and time.
Predictive maintenance is an added benefit of using the MES. It constantly monitors each knitting machine’s performance, and reports any abnormality back to the POMS. Big data can be used to optimize this function as more performance data gets recorded from the knitting machines.
Greater Accuracy and Efficiency in Quality Control
The MES can deliver even more benefits when combined with the Fabric Defect Detection (FDD) system. Installed close to the top of cylinder, the FDD system uses computer vision to inspect the fabric for defects, and has the ability to immediately detect any defect.
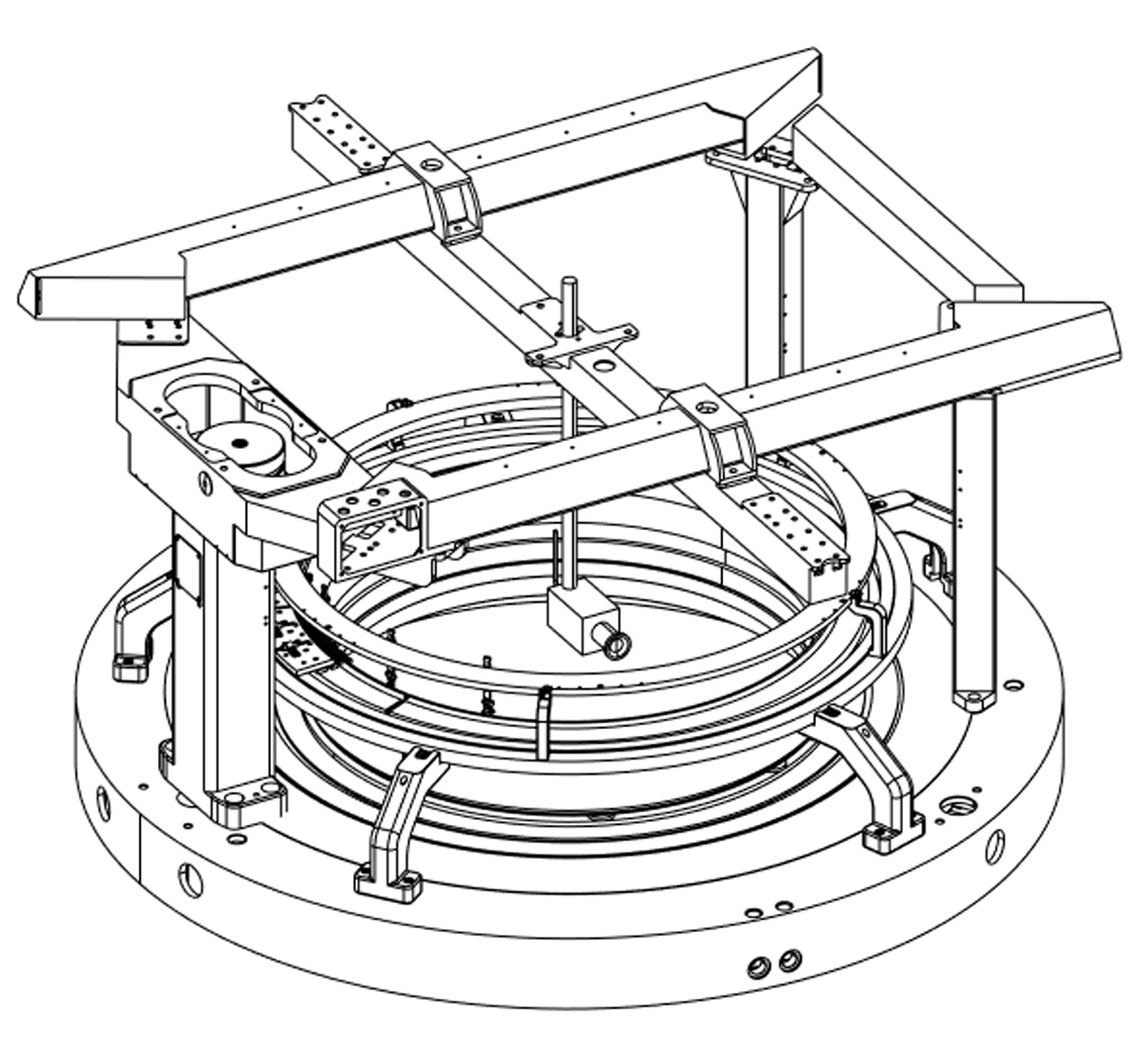
Knitting machines can be shut down immediately, whenever a fabric defect gets detected. This minimizes the amount of defective fabric that goes to waste, reducing the manufacturer’s losses, and the environmental impact of textile manufacturing.
Fabric defects can be very difficult to see with the human eye, especially when so much fabric is being produced by multiple knitting machines. Because of this, human quality control normally requires a lot of manpower and time. AI fabric inspection not only saves all that manpower and time; it even guarantees a higher level of accuracy. For example, the difference between the MES setting value of the yarn length and the actual measurement is ±0.5% FS.
Another advantage of the FDD system is that it can be used in both tubular and open-width devices, allowing the factory space to be utilized in more flexible ways.
Elevate the Quality of Knitted Fabrics
What’s the greatest benefit of Pailung’s software suite? It’s not just about detecting defects and eliminating poor quality fabric; it’s actually about elevating the quality of knitted fabrics to the next level. All of the data, collected throughout today’s production, can be used to improve tomorrow’s production, and so on.
In the near future, textile manufacturers that have not adapted to industry 4.0 will be left behind. Those that have adapted will reap the benefits, and succeed against their competitors. Now is the time for textile manufacturers to embrace digital transformation, and look to the future.
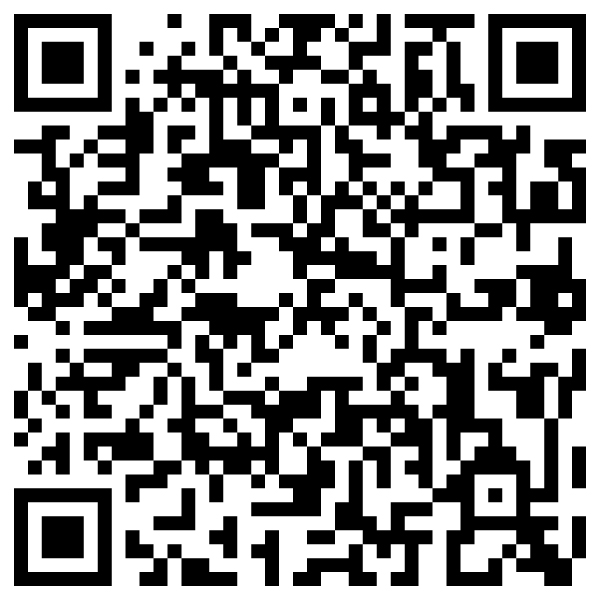
ITMA 2023
Heading to Milan this June? Pailung will demo its software suite at ITMA, the textile and garment technology exhibition. Scan the QR Code to register for a seminar, and visit Pailung’s booth in Hall 2, C101.