Bullish on future growth prospects in India
Ruifang District, a bustling suburb of Taipei City, Taiwan is the headquarters of Pailung, a name synonymous with knitting machines. I was all excited during the drive down to meet Mr. James Wang, the company Chairman, through the busy traffic, so typical of Taiwan. After all it is not every day that you get a chance to pick the brains of the world’s largest manufacturer of circular knitting machines! And I must say that the one-on-one was one of the most interesting, engaging and informative interaction that I’ve had in recent years.
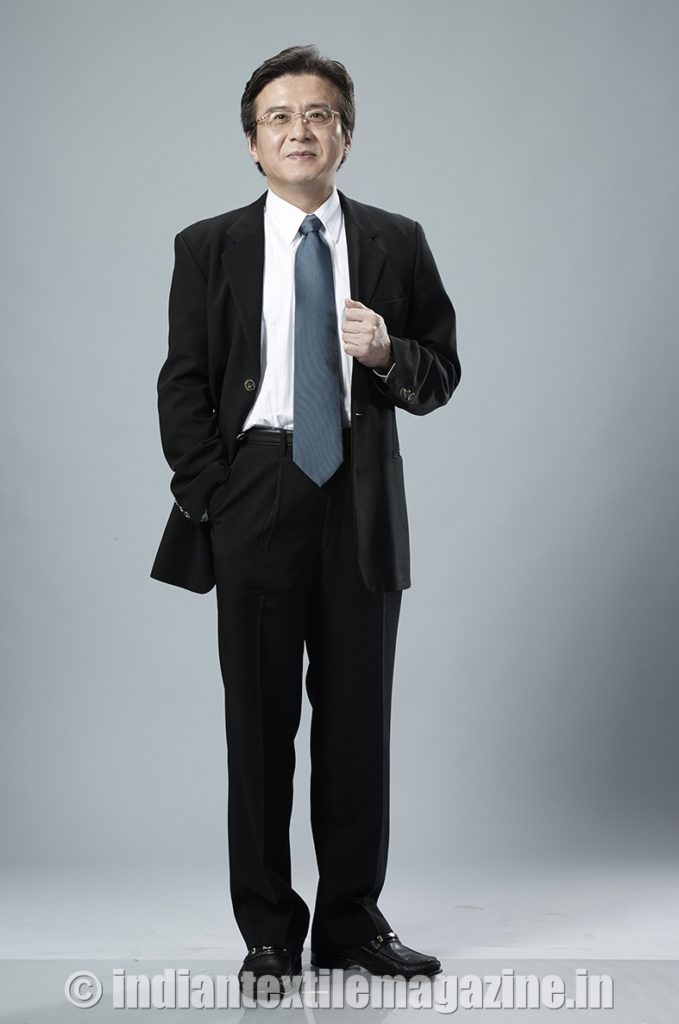
We spent more than 8 hours discussing a range of topics concerning the company, the global knitting industry, the Indian market and the emerging technologies and future plans. What impressed me the most is Mr. Wang’s futuristic vision, meticulous planning, in-depth knowledge and understanding of global markets and his keen interest to keep abreast of the developments that impact his business, including the current political uncertainty in Tamil Nadu, which could possibly have affect his business in the region.
Started in 1977, it’s a landmark year for Pailung as it completes 40 years of its presence in 2017. Mr. James Wang can be credited with much of the company’s success over the last three decades since he took over from his father in the 1980s. Pailung initially had its manufacturing facility in Taipei city and later on moved to Ruifang district in 1997.
Mr. Wang, who joined the business in 1985, recollected how knitting was hardly an option for big textile companies globally in the 1980s. “But today knitting as a manufacturing process has come a long way, thanks to all the innovation, research and development by knitting machinery manufacturers worldwide to make this a compelling option for textile manufacturing. Pailung has definitely been pioneer in this effort with more than 525 patents to its credit,” he said.
In the initial years, nearly 60 per cent of the Pailung’s sales came from the Taiwanese domestic market and the rest from export markets. Today, nearly 95 per cent of the sales come from export markets and only five per cent from the domestic market. Pailung has today become more global with a manufacturing facility in China and its big acquisition in the US, which is currently known as Vanguard Pailung.
The year 2016 has been a landmark for the company. It broke all its earlier records by selling over 1940 machines, which is the best-ever performance by the company since inception, according to Mr. Wang. This number does not include Pailung’s sales from its facility in China and the sales out of the US from Vanguard Pailung. “If these numbers are also added, then Pailung Group sales is close to 2300 units in 2016,” said Mr. Wang. “With these numbers Pailung clearly leads the global market in circular knitting machine sales. We are currently the largest manufacturer in the world of circular knitting machines not just in terms of the number of units but also in terms of revenues.”
Pailung had a very successful ITMA at Milan, with the company receiving repeat orders from several major customers and also through some of the new projects initiated by its customers from Vietnam, Thailand, Indonesia and India. For the last few years, Pailung’s top 10 global markets which includes Taiwan, Vietnam, China, India, Indonesia, Thailand, Bangladesh, Pakistan, Turkey, Egypt and Honduras have been contributing 65-70 per cent of the company’s revenues. Pailung has till date sold more than 50,000 machines globally. In recent years, the company has been consistently shipping over 1,500 machines every year.
Vanguard Pailung
Pailung acquired the US-based circular knitting machine manufacturer Vanguard in 2009. Pailung has 67 per cent stake in Vanguard. Incidentally in 2016 Vanguard completed 100 years of its existence. Vanguard Pailung primarily caters to the American continent. Vanguard’s strength lies in its extremely high-speed, cost-effective knitting machines. Pailung is now taking Vanguard to other global markets. Mr. James Wang added that Pailung will continue to build on Vanguard products, utilizing its strength.
Wide product range
With 86 different models with specifications ranging from 3 inches to 64 inches’ diameter and 3 to 60 gauges, the company offers the widest range of machines in the circular knitting segment. Effectively, including all variants, the company offers 200,000 different types of machines based on customer requirements.
“It’s very rare for a machinery manufacturer to have such a wide range of machines to offer to the market. Compared to our global competitors we are much younger and smaller. But we have the flexibility to offer a very wide range of custom-built machines meeting the specific requirements of customers, which is our biggest strength,” he pointed out.
The company’s first major success came in late 1980s with its rib and interlock machines, followed by the launch of its single jersey and stripper machines in early 1990s and the ‘X’ and ‘K’ series of machines in 2004. In 1995, Pailung launched the Jacquard machine.
Asked why a customer should consider buying a Pailung machine out of the many other options available, Mr. James Wang observed: “Customers prefer Pailung machines because of its quality, flexibility, productivity, functionality and, more importantly, reliability. We offer more functionality and versatility even in our basic machines. With the acquisition of Vanguard, which is known for high productivity and higher speeds, we are now able to offer the customer increased efficiency on our machines”.
It is not surprising then to find that Pailung machines command a very strong preference even in the used machine market which shows the reliability and long lasting nature of the machines. “We have a Pailung machine running for the last 37 years in a customer location”, he added.
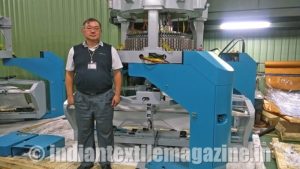
OIL
Pailung machines offer the versatility to run different types of material as per customer requirements, including cotton, polyester, viscose, nylon, wool, Kevlar, nomax and many more. It is with this requirement in mind that Pailung has set up ‘OIL’, acronym for ‘Open Innovation Lab’, almost 25 years ago. Initially started as FAE (Field Application Engineering), Mr. Wang was proud to say that today OIL has over 6,000 different types of fabric which are samples made through in-house research and development.
Complete solution provider
Thanks to its in-house knowledge, experience and data accumulation, Pailung has more than 6,000 different types of fabric, their knitting properties, raw material to knitting parameters up to dyeing and finishing. “We are not just a machine builder, we are a solution provider. Customers who want to make these fabrics and keep in tune with evolving fashion trends will definitely come to us as we can provide them the machine and also the knowledge of the new fashion trends”, Mr. Wang said.
Pailung offers machines for a variety of applications which it has classified into five different segments – lingerie, casual wear, sportswear, outdoor and dresser. Traditionally very strong in the casual wear and dress wear, the company has in recent years strengthened its presence in the sportswear, outdoor and intimate wear segments as well. “Sportswear, in particular all major suppliers to brands like Nike and Adidas use Pailung machines. In fact, Nike has nine global partners, of which six of them are our major partners. This means that more than 50 per cent of their machines are from Pailung. In the last 10 years, we set up our internal mission to focus on this segment and we co-operate with some of the biggest yarn makers in Taiwan”, Mr. Wang revealed.
Strong infrastructure focus
Pailung’s modern manufacturing facility has been constructed with its future requirements in mind. The company had installed the Flexible Manufacturing System (FMS) which is completely robotic controlled.
Elaborating further on the infrastructure, Mr. Wang said: “All key components are manufactured in-house, such as the main frame, the cambox holder, transmission, gears and cylinder. Pailung has a completely automated machine shop. We have complete control over the quality of the components manufactured. Our quality assurance department and material research department ensure that all incoming material like alloy steel and casting material are tested to ensure the right quality and consistency. The company has also invested on a furnace to produce alloy steel and castings.”
Pailung also works very closely with global suppliers like Groz-Beckert. “The company has co-operated with Groz-Beckert for more than 28 years. We are their single largest customer. We also work closely with Memminger, our strategic partner for more than 30 years”, said Mr. Wang.
Pioneering control systems
Pailung has always attempted to make machines more intelligent and web enabled. The web-enabled machine helps in sending data to the central computer. Mr. Wang further explained: “The Pailung ‘Online Monitoring System’ was developed not just for monitoring but also for controlling the machine. One of our major customers who has recently set up a plant in Vietnam wanted MES (Manufacturing Executive System) that requires sharing of information through our machine and through our POMS to their ERP system. The ERP system sends the work order, the machine is then instructed on the fabric or product to be manufactured on a given schedule. This requires very high level of integration with the IT system and availability of information for the customer. Pailung’s second generation controllers help in faster communication and data transfer for MES requirement. This is an optional system that we are offering for customers but we are increasingly seeing more customers opting for this. With the industry worldwide opting for Industry 4.0, we see this as a trend in the coming years.”
India success story
Pailung’s initial foray into the Indian market in 1987 when its first Indian customer approached it for buying its machines makes for interesting reading. It later turned out that the same Indian customer also became Pailung’s agent in India which is YuvrajMerch-X. Mr. Wang has been personally responsible for forging this Indian partnership which has now lasted well over 30 years. Pailung today has its agents in all markets across India.
Recollecting his 30-odd year association with the Indian market, Mr. Wang said that today India has transformed and is all set to play a bigger role in the textile field. In its initial years, Pailung sold on an average 50 to 100 machines a year in the Indian market. This has now gone up to 500 machines. Currently more than 7500 Pailung machines are running across over 1,000 customer locations in India. According to Mr. Wang the growth rate has significantly increased over the last 10 years.
When queried if India would emerge a leading global market for the knitwear segment, Mr. James Wang said: “For sure, India is among the top 3 countries worldwide for cotton cultivation. With Reliance, India has the largest global polyester manufacturer, and Birla, one of the world’s largest manufacturers of viscose. From the raw material availability point of view, India already plays a very important role globally. This is a very important consideration for future growth in textile manufacturing. India is the second largest populated country in the world and hence offers a huge domestic market for consumption, which is a major factor contributing to future growth.”
However, in the same breath Mr. Wang also said that India still lacks specialized knowledge of the knitting segment. “This is where we help by sharing our knowledge and experience for the benefit of our customers in India. We provide specialized training for our customer’s technicians. We also participate in the Knitwear Technology Mission (KTM) initiated by the Government of India,” he continued.
India’s share of knitwear globally is still a very small percentage and even that is primarily in the cotton-based knitwear and apparel product. In the last 10 years Pailung has been working very closely with Indian customers to diversify into synthetic and man-made fiber based knitwear and apparel products. “We are pushing Indian customers to look at products beyond cotton knitwear segment. We can share our knowledge and experience for the benefit of customers. We can also bring experts from Taiwan to engage with Indian customers and share their knowledge and expertise”, assured Mr. Wang, before adding, “particularly with increasing awareness on sports and fitness, sportswear can be an interesting and potential segment for Indian textile companies to consider.”
Considering that large knitwear capacities have already been established in markets like Taiwan, Vietnam and China for outdoor and sportswear segment, does India stand a chance? Mr. Wang said: “In the peak of exports China was doing $270 billion and China’s domestic market was four times its exports. India’s textile & apparel market is $105 billion, out of which the domestic market is $65 billion and exports $40 billion.”
Mr. Wang further observed: “I am personally very convinced that the next big growth is going to come from the Indian domestic market. Over the next 10 to 15 years the GDP would triple to $6 trillion from the current $2.1 trillion. This will also mean the domestic market for T&A will grow by 8 times from the current levels.”
Training, service and spares
Pailung’s major customers in India include Sri Shanmugavel Mills (SSM), KPR Mills Ltd., Bannari Amman, SP Apparel, Eastman, TeeJay India, Alok Industries Ltd., Madhusudhan Rayon, SVG Fashions Ltd., Bombay Rayon, Vaibhavlaxmi Filaments, Cubatic, Shivalik and Oriental.
YuvrajMerch-X has a showroom-cum-demo centre in Tirupur where customers can try out samples. Most of the technical training is done at Pailung’s facility in Taiwan. The company has a schedule throughout the year for training its customers and their technicians and operators.
“I always believe that the success of any machinery manufacturer depends on the service and spares support provided to its customers. Every small machine downtime results in loss of productivity and revenue for the customers. Pailung is well aware of this and insists on a very strong service team to support its customers 24/7. The first criteria for becoming our agent is they should have technical knowledge and qualified technicians. Our agents keep sending technicians periodically for training and knowledge updation. Our warrior in the front line should be ready to service the requirement of all our clients. Periodically even our technicians from Taiwan visit India to meet customers at their respective units”, said Mr. Wang, highlighting an important point.
Pailung, through its agents, has around 15 service engineers to cater to all the service requirements of customers across India. Spares are stocked by the agents based on their understanding of customer requirements.
Speaking about the company’s initiative for energy savings, Mr. Wang mentioned: “Pailung has been continuously working on improving the quality, performance and efficiency of its machines. The company has worked hard in reducing mechanical friction and vibration in the machines, which has resulted in significant savings in energy cost. Pailung has also introduced ‘E3’ motors which are highly energy efficient.”
Spinit, a game changer
In recent years, there has been a lot of buzz on the ‘Spinit’ technology, i.e., circular knitting machines that can also spin. From just a concept a few years back, today these machines are going through final testing in many customer locations across India and other markets.
On Pailung’s initiative on the front, Mr. Wang said: “We have spent 6 years developing our Spinit machines and are quite optimistic about the future of this technology. Spinit is mainly suitable for single knit and the advantage is there will be no twisting. Hence it will offer the fabric the natural shine and softness. The other major advantage is you can run different yarn count and different varieties of yarn giving scope for a completely new type of fabric.”
Optimistic about the growth of this particular market segment, Mr. Wang said: “We showcased our Spinit machines at ITMA and many customers from India, Turkey, Vietnam, Thailand, Mexico, the US have evinced keen interest.”
Flat knitting
Pailung is still a new entrant in the flat knitting machinery business. It launched collar machines in 2007 and sweater machines in 2011. On the company’s foray into this segment, Mr. Wang stated: “Although we started late, we are trying to offer a differentiated product in the market. We have developed inverse plating in flat knitting machines. This is a non-intarsia framework but plating work with Pailung’s unique yarn separation system. Pailung’s inverse plating can produce two-tone jacquard, cable, mesh pattern or more design in single jersey knitwear. This has been well received by the market. Pailung is targeting specific industrial application as the shoe upper industry.”
Future targets and outlook
Pailung expects to double its growth and revenues by 2020. The company is targeting sales of 3,000 machines by 2020, and by 2025 the target is to sell 4,500 machines, which will be a mix of circular, flat knit and Spinit machines.
With the acquisition of Vanguard, Mr. James Wang has expressed his interest for inorganic growth. He said: “In Europe, we see a lot of consolidation happening in major machinery and component groups. We expect this to happen in Asia as well, and we will be open for such opportunities. We are looking for opportunities which can complement our existing business.”
On a parting note expressing positive sentiments about the continued growth of the knitting industry, Mr. Wang said: “The circular knitting industry is a relatively newer technology compared to spinning and weaving. From the global trade for garment and apparel, knitting has bypassed weaving almost a decade back. With lesser investment, lower power consumption, better flexibility and lesser preparation, knitting is more economical to produce. We see that the trend is clearly moving towards knitting.”
A few decades back, knitting was only for very specific application, but over the years with all the innovation, knitting has now become more versatile. Apart from apparel, today knitting has its presence in home textiles, denims, show uppers, industrial and even in some of the technical textile applications. “We clearly see a lot of opportunities emerging in the knitting segment in the coming years, and Pailung will continue to play an important role as a global innovation leader in the knitting segment.”
SSM Group’s trust in Pailung machines for knitting project
Sri Shanmugavel Group of Mills (SSM) consists of 10 spinning units with a capacity of around five lakh spindles, two open-end spinning units, one woven fabric unit and one knitted fabric unit at Dindigul in Tamil Nadu.
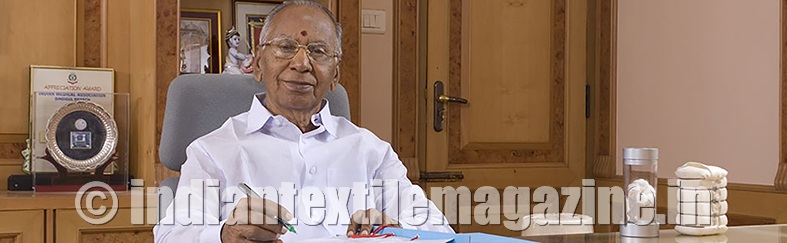
Employing nearly 10,000 associates with a daily production of around 2,50,000 kg of combed and carded yarn. The SSM Group markets its yarn manufactured across all its units under the brand Sudhan. The reason is the company is using the same set of machineries, same cotton, unique technology and trained labour force with a uniform work culture in all its units.
The SSM Group has been exporting to all major global markets, of which 80 per cent is combed knitting yarn. The company’s main count range is from Ne 20s to Ne 40s in ring spun quality and 4s to 20s in Oe quality both for weaving and knitting end use.
Referring to the company’s foray into knitting, Mr. P.S. Velusamy, Founder & Chairman, said: “Traditionally, we have been catering to the Tirupur market in a big way by supplying yarn. Some of our end-users preferred knitted fabric instead of sourcing yarn, and hence we decided to set up a manufacturing facility for knitted fabric”.
It was a big step forward for the SSM Group to invest in the knitting project. It did extensive groundwork to identify the right solution and finally decided on the Pailung machines for this project. “We have been working closely with the Pailung Group from 2005, right from the inception of our knitting project. We have invested in 261 knitting machines, including 165 single jersey machines, 50 interlock machines and 46 rib machines”, revealed Mr. Velusamy.
SSM has been manufacturing Single Jersey, rib and Interlock fabrics produced cent per cent out of Pailung machines. Asked about the experience of using Pailung machines so far, he said: “We are very happy with the fabric quality made out of Pailung machines and highly satisfied with the productivity, reliability and aftersales service provided by the company and their local agent. As we are loyal to ‘Pailung’ we receive prompt attention always”.
Investing on over 250 machines in one brand, Pailung was a big decision for SSM. “No doubt it was a big risk, but looking back we are not disappointed at all. We don’t have any immediate plans for expansion. But whenever we plan to expand, it goes without saying that our choice would be Pailung only. SSM currently has production capacity in knitted fabric of around 70,000 kg per day”, Mr. Velusamy added.
Teejay India’s preference for Pailung machines
Teejay India Private Ltd. is a weft knitted manufacturer and exporter of single jersey, rib and interlock fabrics that are dyed / printed. Located in the Brandix India Apparel City, a Special Economic Zone with export-oriented units involved in the integrated apparel supply chain in Visakhapatnam, the company is a fully-owned subsidiary of Teejay Lanka PLC, which is listed on the Colombo Stock Exchange.
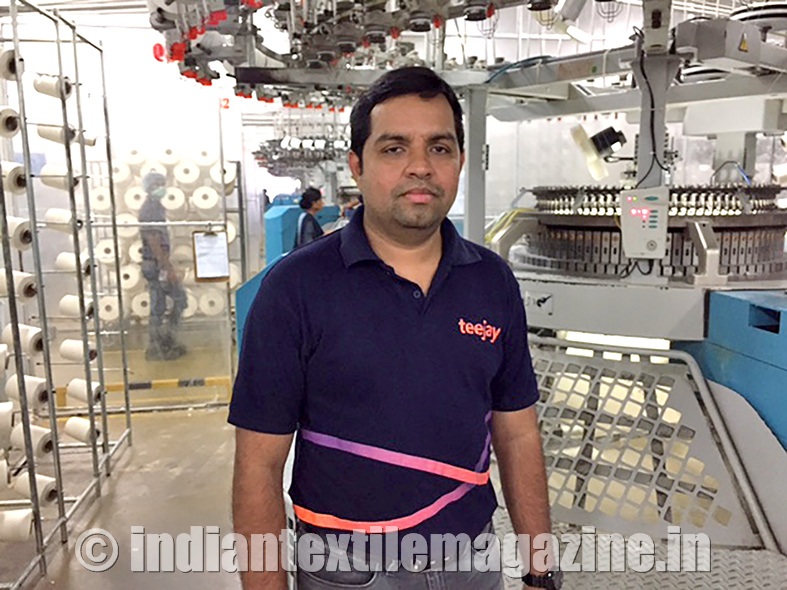
Brandix Lanka, Sri Lanka’s leading apparel exporter, and Pacific Textiles, the Hong Kong-based company with one of the world’s largest textile manufacturing facilities in China, are the major shareholders of Teejay Lanka.
Commenting on the company’s investment in India, Mr. Upul Nallaperuma, General Manager, Teejay India, said: “When Brandix entered India and set up the Brandix India Apparel City in Vizag with units involved in the apparel supply chain, it was decided to have a fabric mill to provide speed, quality and competitive cost to buyers. Teejay Lanka was looking at regional expansion and investing in India was a suitable opportunity. Considering the potential, Teejay decided to invest more in the expansion.”
Teejay first invested in a Pailung machine in 2008 and has been working with Pailung since last nine years. The company currently has 76 knitting machines from Pailung (55 Single Jersey & 20 Double Jersey). Teejay primarily offers weft knitted fabrics that are dyed / printed in knitting / fabric structures, including single jersey, rib, interlock, Pique / Lacoste, fleece, French Terry and Jacquard Jersey. The company uses Pailung machines for its entire knitting manufacturing process.
Asked about the company’s experience of working with Pailung machines, Mr. Upul Nallaperuma said: “Pailung machines have a unique combination of offering consistent quality with high productivity. The machines are reliable with good aftersales support”.
Teejay India initially invested in 25 SJ & 20 DJ knitting machines in 2008 and added another 20 SJ knitting machines in 2009. Based on the positive experience with Pailung the company added another 10 machines in 2013. “Based on the positive experience we have with Pailung knitting machines, we decided to expand with the same brand for our recent expansion, as it offers good performance, value for money, better return on investment, reliable, easy to operate and less breakdowns”, says Mr. Upul Nallaperuma.
Currently Teejay India has knitting production capacity of 20 + tons per day and the company is in the process of adding 10 + tons capacity per day by June 2017. “We are currently in the process our expanding our knitting capacity and ordered 30 Pailung machines for the same. This is the first set of Pai Lung 150 kg roll open width machines in India. We will consider Pailung for our future expansion as well”, he adds.