Neuenhauser Maschinenbau GmbH is an automation leader. For just a few weeks now, 169,728 spindles have been doing its duty under one roof at the largest ring spinning plant in the world. The Welspun manufacturing facility in Anjar, India is an enterprise of superlatives and active VDMA member the Neuenhauser Group has been instrumental in its development. 55 kilometres of track with 944 switches were installed just to transport the roving bobbins. 872 bobbin trolley trains travel on the tracks, guided and monitored by more than 1,000 sensors. Over 15 kilometres of cable and 2 kilometres of optical waveguides have been installed so that the enormous plant can be controlled through a single command centre. The site offers a tantalising glimpse of how Project Industry 4.0, the fusion of information technology and machine building, will affect industrial production in the future. Mr. Wilhelm Langius, Head of Textile Industry Automation, explains why automation is the only possible way of the future.
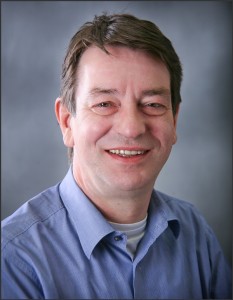
After China, India is the second largest textile manufacture in the world, and an enormously important market for Neuenhauser…
… Yes indeed. In the last few years, the Indian market has embraced automation in spinning plants very successfully. We have already completed more than 20 projects for various Indian customers in this segment. Last year, Neuenhauser succeeded in winning its largest order to date for roving bobbin and package transport systems with palletisation, from Welspun. This is one of the largest, most modern ring spinning mills in the world. The customer wanted a completely automated, “contactless” material transport system. Final acceptance was completed just a very few weeks ago.
Please would you outline briefly the path transport automation in spinning mills took to reach its present state.
As automation became increasingly widespread in natural and chemical fibre spinning mills, it gave rise to an enormous leap in productivity. It was then a logical progression to build apparatuses and systems that used technology to enable them to handle the heavy, delicate bobbins for natural, chemical and carbon fibres. Accordingly, Neuenhauser developed the world’s first fully automated handling system, called “AutoFlow”, as early as 1985. AutoFlow was designed with a device for removing the bobbins from production machines that is now well known in the textile industry, called the “lifter-doffer”. But this was just the first step on the road to full automation. Over time, our group of companies developed other automated handling systems for the textile industry, including not only devices for removing BCF bobbins from the spinning or winding machines, but also for overhead transport, intermediate storage and automatic packaging of the bobbins. So we now support and monitor the entire manufacturing operation, all the way up to loading and shipping.
Why was automation inevitable? Surely, customer countries such as China or India do not lack manpower?
Corporations like Welspun build gigantic production facilities, whose very manufacturing capacity on a daily basis poses problems: In terms of product quality as well as the greater need for human resources. This is further complicated by high turnover in personnel. Over the years, Neuenhauser has developed many automation projects for customers such as these, which have enabled them to prevail in a highly competitive environment.
What advantages does the automation powered by Neuenhauser also offer with regard to Industry 4.0?
In our vision, automation has a far more complex role than is generally thought. Its purpose is not just to lower payroll costs, although this is also a decision making criterion as well. In fact, our chief consideration in this undertaking is to reduce the need for manual handling of bobbins and the problems arising therefrom to the barest minimum. In this way, we help our users to improve the quality of their products. But automated handling systems, called AHS for short, also provide them with other advantages, such as a safe, high-performance product flow through the entire plant configuration, or better use of factory space through compact machines and systems. They also help to maintain a clean, tidy and efficient manufacturing environment and a safe, ergonomically less burdensome workflow. Neuenhauser is already considering Industry 4.0 for its future developments. But we have only just started. I believe that the economy will only become fully digitised in a series of many, many small steps.
What are the specific stages of robot-assisted transport in a spinning mill like this?
We have implemented CanTrac, a floor-based track system on which the cans containing the loose fibre strip are transported by means of a reciprocating “walking floor” mechanism from the combing the machines to the drawframes and then the roving frames. In the Welspun factory, overhead transport of roving bobbins is assured by TEXTRA. The system consists of closed profile rails, curves and switches which guide the trolley rollers. The trolley trains are driven directly by friction drive motors. An automatic bobbin doffer on the roving frame, that is to say a pre-spinning machine, transfers the bobbins to a trolley train, which then travels to a storage area or the spinning machine. When they arrive at the spinning machine, the full bobbins are inserted in the roving frame creel, replacing the empty tubes. The flexible link system makes it possible to transport different roving yarn qualities produced at the roving frames to any given spinning frame. Throughout the process, the control system ensures that the trolley train delivers the roving yarn to the right spinning frame.
And what happens after that? Would this result in the packages as the final product?
Finally, AutoFlow picks up the packages of finished yarn: The system at Welspun can manage over 1,000 packages per hour with more than 20 different articles simultaneously and transport them to their respective destinations with total reliability. For shipping, the packages are then either transferred to a palletizer or a carton packing system. The result for the customer is better bobbin quality due to the contactless material transport system; extremely short clearance times enhance the beneficial effects on the spinning and winding machines, and it is practically impossible for yarns to be misdirected.
So with Industry 4.0 we can expect nothing less than a fourth industrial revolution.
Digitisation of our plant equipment is already very advanced; workflow is completely computer-controlled. The relevant data can be retrieved via the human machine interface synchronously with production. We can already track the product back to the beginning of the manufacturing process. And all system components have been integrated in a higher-level plant management system.
We certainly still have a long way to go for Industry 4.0. Because as internet technologies are also introduced, the data will have to leave the factory. On this point, highest priority must be given to security. The networked products, machinery and systems will be able to interact with each other directly, and will render production considerably more efficient and more flexible. Customers and business partners will be involved even more closely in the ongoing processes. Industry 4.0 will also pave the way for many new developments, which we cannot even conceive of today.
What innovations will Neuenhauser present at the ITMA?
In Milan, we will exhibit new automation solutions for the automatic collection of packages from spinning machines and for palletizing and packaging.