If any part of a vehicle needs to meet highest standards of functionality and reliability, it’s the seat belt – the real lifesaver in a crash. Seat belts are among the typical and most critical applications of narrow fabric weaving, a sector in which technology from Swiss manufacturer CREALET is trusted by producers worldwide. Its warp feed systems help to create narrow fabrics with minimum faults and the ultimate performance required for their lifesaving protection.
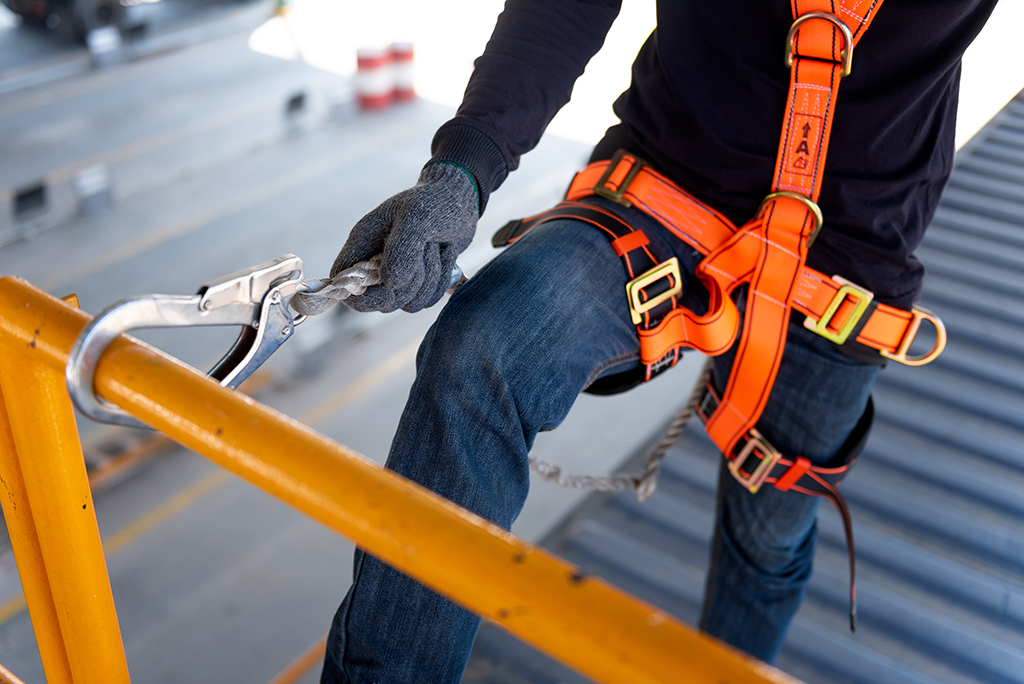
CREALET specializes in highly-reliable electronic warp thread feed systems for various types of narrow weaving machines. The fabrics are narrow, but the application range is wide: it includes feeding systems for shuttle looms for fabrics with seamless selvedges, needle looms for tapes and belts, as well as specially-designed weaving systems for making very heavy-duty fabrics.
Among CREALET’s long-standing customers is Stahl, a leading German weaver of straps and narrow fabrics. Many of these products serve applications with a high security aspect, so absolute and 100% reliable functioning of the belts must be guaranteed over several years of use – even 20 years or longer. “Our customers trust us and we invest in the best machinery to prove that trustworthiness every single day,” says Bernd Ledl, Managing Director at Carl Stahl GmbH.
Stahl weaves 300 threads per belt together at high speed to produce a 46 to 48 millimeter wide and 1.2 millimeter thick seat belt webbing. Each thread consists of more than 100 ultra-thin synthetic yarn threads, made of polyester. Around 30,000 meters of filaments are processed per meter of webbing. Ideal warp feeding is essential to make the process both smooth and perfect in terms of consistent quality. That’s where CREALET comes in, for secure production values and profitability.
Future-minded
Markets are more dynamic than ever, with new products and variations appearing faster and faster. At the same time, customers’ expectations of constant fabric quality are increasing. The competition is growing, and getting tougher.
A reliable partner makes a big difference in these times, as a key assets for business success, especially with a vital function such as warp feeding. CREALET has the sophisticated technologies to optimize processes, preparing weavers for the era of IOT and Industry 4.0. Backed by decades of experience in the construction of warp feeding systems, the company is constantly developing the most modern solutions, dedicated to making the warp thread feed reproducible, traceable and most of all reliable.
Yarn tension is a major factor in warp feeding, and CREALET has devised effective solutions which quickly and precisely synchronize the tension of different warp beams and which connect to an integrated network. “It’s our goal to enable customers to realize their creative ideas now and in future,” says CREALET Sales Manager Andreas Wirz.
In-depth understanding
Fabric producers often face challenges in taking standard products beyond the limits of existing capabilities. Here, CREALET has the detailed knowledge of warp feeding to devise specific solutions, which then become as individual as each customer, offering original and effective competitive advantages. “We are the ideal partner for the many different requirements in warp feeding. We have all the know-how and experience to optimize machine efficiency and fabric quality,” says Wirz.
CREALET customers understand the importance of warp tension. It must be kept constant, from full to empty beam – and the same applies to weaving from creels. In both cases, warp tension that is too high or too low can cause thread breaks, damaging weaving behavior and efficiency. Electronic warp feeding systems solve the problem, keeping tension balanced at the right levels. This reduces machine load and increases both performance and fabric quality.
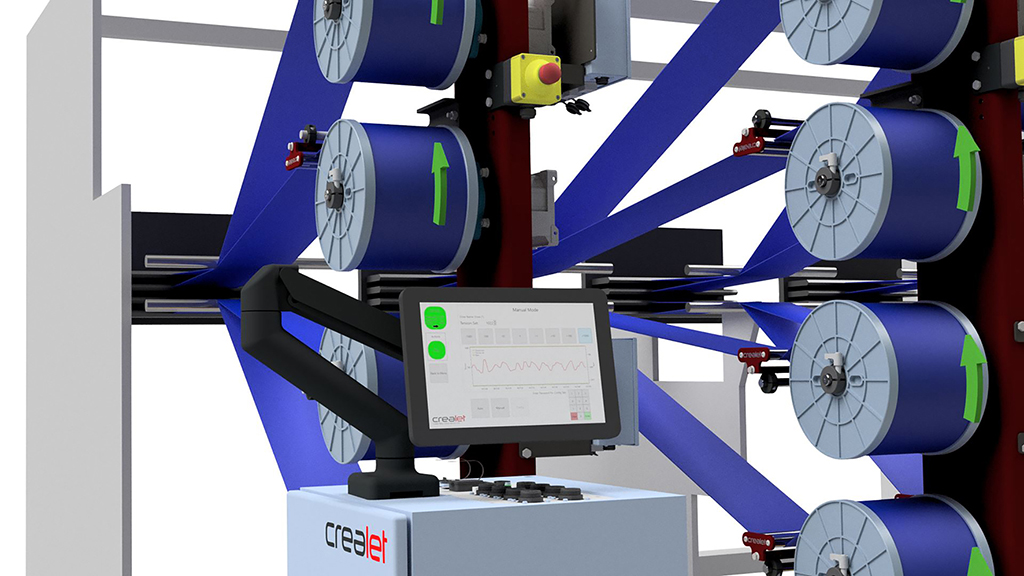
Targeted technology
When weaving safety belts, lifting belts, binding tapes or other narrow fabrics, the warp material must be fed from the creel or warp beams to the weaving machine under constant tension. When weaving from creels, delivery mechanisms are used that pull the warp ends off the creel with a coated take-off roller and feed it with the required tension to the loom. For weaving from several warp beams, an IPC-based control can be the right solution. All warp beams can be conveniently programmed and configured from the human interface.
In both creel and warp beam applications, thread tension is measured by load cells and the warp tension values are shown on the display. The desired warp thread tension is set at the control panel, eliminating the need for adjustment by springs.
Customer satisfaction
CREALET customers can optimize thread tension during the weaving process. Specially-designed creels and sectional warp beam frames can be supplied to complement perfectly the warp thread feed units. Comprehensive solutions also include warp beam stands, delivery units, warp let-offs and take-up, control units, gateways and software.
Good news for all narrow weavers! CREALET know-how also makes it possible to convert installed warp beam frames to electronic warp feed. “We are never satisfied, until our customers are satisfied,” says Wirz.